Concrete Strength |
 |
 |
Acceptance
Method Used in the Prototype PRS
Concrete
strength is one of the four AQCs included in the prototype PRS developed
under the previous FHWA PRS study.(1,2,3)
The prototype required that flexural strength be measured directly from
beam specimens or indirectly from cylinder strength tests and used for
the acceptance of the as-constructed portland cement concrete (PCC) slab.
The prototype PRS recommended using core testing as an indirect measure
of the in situ flexural strength. With this method, cores are taken
at some reference maturity equivalent (for example, 3 days at 22 °C).
To provide rapid feedback to the contractor, the 28-day flexural strength
is then projected from the early age in situ strength data. The
inter-strength relationship between flexural and compressive strength
would be established for the approved mix design (prior to construction)
using project-approved aggregates, cement, and admixtures. The previous
PRS study concluded that there is no statistical difference between the
compressive strength of cores and cylinders cured under identical curing
conditions.(3)
The literature search focused on obtaining information related to these
processes, as well as the typical standard deviations associated with
the different strength sampling methods.
Variation
of Concrete Compressive Strength
A
discussion of the overall variation of in-place concrete core strengths
in structures was included in a draft report prepared by the American
Concrete Institute (ACI) Committee 214.(4)
This report referenced findings from a previous study which reported coefficients
of variation (COV) for structures as a function of one or many members,
and one or many batches of concrete.(5)
These findings are presented in table 1. Although these reported COVs
are specific to structures, the core COV expected in a PCC pavement is
most likely close to the 13.0-percent value associated with many members
and many cast-in-place batches.
Table
1. Coefficient of variation due to in-place strength variation within
the structure.(4)
Structure
Composed of:
|
One
Member
|
Many
Members
|
One
Batch of Concrete |
7%
|
8%
|
Many
Batches of Concrete
|
Cast-in-place
|
12%
|
13%
|
Precast
|
9%
|
10%
|
The ACI Committee 214 report also includes a section dealing with the
conversion of core strengths to equivalent in-place strengths (again,
focusing on structures).(4)
The report presents an equation that is used to calculate the equivalent
compressive strength (fC
(EQUIVALENT))
in terms of measured core compressive strength (fCORE)
and four correction factors. The correction factors account for
the effects of core length-to-diameter ratio (Fl/d),
core diameter (FDIAMETER),
moisture condition of the core (FMOISTURE),
and damage sustained during drilling (FDAMAGE).
The correcting equation is defined in equation 1.
fC
(EQUIVALENT) = Fl/d
* FDIAMETER
* FMOISTURE
* FDAMAGE
* fCORE
(1)
The report also contained
a table of guidelines for estimating the specific correction factors required
in the equation. These values are shown in table 2.
Table
2. Magnitude and precision of strength correction factors for converting
core strengths into equivalent in-place strengths.(4)
Factor
|
Mean
Value
|
COV,
%
|
Fl/d:
l/d ratio |
soaked
|
1
{0.117 4.3 * (104)
* fcore}(2 l/d)2
|
2.5
* (2 l/d)2
|
air
dried
|
1
{0.144 4.3 * (104)
* fcore}(2 l/d)2
|
2.5
* (2 l/d)2
|
Fdia:
core diameter |
50
mm
|
1.06
|
11.8
|
100
mm
|
1.00
|
0.0
|
150
mm
|
0.98
|
1.8
|
Fmc:
core moisture content
|
soaked
|
1.09
|
2.5
|
air
dried
|
0.96
|
2.5
|
Fd:
damage due to drilling
|
1.06
|
2.5
|
- Notes: 1
To obtain the equivalent in-place concrete strength, multiply the
observed core strength by the appropriate factor(s) in accordance
with equation 1.
- 2
fcore is expressed in terms of MPa.
- 3
Standard soaked and air dried conditions are specified
in American Society for Testing and Materials (ASTM) C 42.
Core
data for one pavement project in Indiana were presented in the 1996 Hughes
report titled Variability in Highway Pavement Construction.(6)
This 28-day core compressive strength data consisted of 63 cores taken
over a 6-week period. A statistical analysis of the data resulted
in a mean and standard deviation of 35.1 and 6.0 MPa, respectively. The
COV was then calculated to be 17.0 percent for this project.
A
1995 Illinois Department of Transportation (IDOT) report presented structural
and pavement strength data (contained in IDOTs MISTIC database).(7)
Both structural and pavement data were included in the report because
most of the mix designs were "indistinguishable." Each
calculated variability is specific to one mix design, one construction
year, and in some cases, one producer. Table 3 contains a summary
of the reported concrete cylinder compressive strength variability data.
Table
3. Concrete cylinder 28-day compressive strength variability data
from the Illinois Department of Transportation MISTIC database.(7)
Mix Number
|
Class
|
Year
|
n
|
Mean, MPa
|
Std Dev,
MPa
|
COV, %
|
1
|
pavement
|
1992
|
110
|
30.81
|
2.69
|
8.7
|
2
|
pavement
|
1992
|
38
|
28.31
|
3.87
|
13.7
|
3
|
pavement
|
1993
|
16
|
34.70
|
2.69
|
7.8
|
4
|
pavement
|
1992
|
82
|
33.47
|
5.51
|
16.5
|
5
|
pavement
|
1993
QA/QC
|
10
|
33.21
|
3.53
|
10.6
|
6
|
pavement
|
1993
Non-QA/QC
|
8
|
31.32
|
3.84
|
12.3
|
7
|
pavement
|
1992
Non-QA/QC
|
12
|
33.14
|
3.44
|
10.4
|
8
|
pavement
|
1991
Non-QA/QC
|
18
|
29.88
|
2.75
|
9.2
|
9
|
pavement
|
1993
QA/QC
|
31
|
35.23
|
6.27
|
17.6
|
10
|
pavement
|
1992
|
23
|
34.51
|
2.92
|
8.5
|
11
|
pavement
|
1993
|
15
|
35.11
|
1.69
|
4.8
|
12
|
pavement
|
1992
Non-QA/QC
|
28
|
35.88
|
5.58
|
15.5
|
13
|
structural
|
1992
|
29
|
33.07
|
4.63
|
14.0
|
14
|
structural
|
1993
|
23
|
35.20
|
4.01
|
11.4
|
15
|
structural
|
1992
|
94
|
32.76
|
4.61
|
14.0
|
16
|
structural
|
1993
|
30
|
33.27
|
5.73
|
17.2
|
17
|
structural
|
1992
|
110
|
30.81
|
2.69
|
8.7
|
18
|
structural
|
Unknown
|
40
|
35.80
|
6.34
|
17.7
|
19
|
structural
|
Unknown
|
11
|
34.58
|
9.16
|
23.9
|
20
|
structural
|
1993
QA/QC
|
34
|
29.61
|
4.72
|
16.0
|
Pavement
Data Only Averages
|
32.96
|
3.73
|
11.3
|
Structural
Data Only Averages
|
33.14
|
5.23
|
15.4
|
All
Data (Pavement and Structural) Averages
|
33.03
|
4.33
|
12.9
|
QA/QC
= Quality assurance/quality control.
An
analysis of the compressive strength data in table
3 shows little difference between the averages of the pavement and
structural 28-day cylinder compressive strength means (32.96 MPa for pavement
and 33.14 MPa for structural concrete). The data did show, however,
that greater variation (a higher standard deviation) was typically associated
with the structural data (average structural standard deviation of 5.23
MPa, compared to an average pavement standard deviation of 3.73 MPa).
A
1972 paper by Darter specifically discussed compressive strength variability.(8)
He presented results from a West Virginia study in which the variation
from materials, sampling, and testing was investigated for seven different
projects. Table 4 contains highlighted data from the West Virginia
study.
Table
4. Components of 28-day compressive strength variability for seven
West Virginia projects.(8)
Project
Number
|
Mean
|
Overall
|
Testing
|
Sampling
|
Materials
|
Std Dev,
MPa
|
COV, %
|
Std Dev,
MPa
|
COV, %
|
Std Dev,
MPa
|
COV, %
|
Std Dev,
MPa
|
COV, %
|
Paving
Concrete
|
1
|
32.23
|
3.76
|
11.7
|
2.60
|
8.1
|
0.63
|
0
|
2.73
|
8.3
|
2
|
25.89
|
2.90
|
11.2
|
2.22
|
8.5
|
0.29
|
0
|
1.86
|
7.1
|
3
|
25.65
|
3.96
|
15.5
|
2.19
|
8.5
|
|
|
3.41
|
13.3
|
4
|
32.82
|
3.22
|
9.8
|
1.38
|
4.2
|
0.23
|
0
|
2.90
|
8.8
|
5
|
32.32
|
5.05
|
16.5
|
4.03
|
12.5
|
|
|
3.76
|
11.7
|
Structural
Concrete
|
1
|
29.20
|
3.00
|
10.0
|
1.17
|
4.0
|
1.63
|
5.6
|
2.14
|
7.2
|
2
|
30.47
|
3.32
|
10.9
|
2.23
|
7.3
|
0.27
|
0
|
2.48
|
8.1
|
Paving
Data Only Averages
|
3.78
|
12.9
|
2.48
|
8.4
|
0.39
|
|
2.93
|
9.8
|
Structural
Data Only Averages
|
3.16
|
10.5
|
1.70
|
5.7
|
0.95
|
2.8
|
2.31
|
7.7
|
All
Data (Pavement and Structural) Averages
|
3.60
|
12.2
|
2.26
|
7.6
|
0.61
|
0.8
|
2.75
|
9.2
|
The data from these seven projects show an average overall project standard
deviation of 3.60 MPa and a corresponding overall project average COV
of 12.2 percent. Darter noted that the sampling and testing error
make up a significant portion of the overall variation, and the materials
COV is about three-fourths of the overall COV. Figure 1 illustrates
the relationships among the materials, sampling, and testing standard
deviations. It is important to note that the standard deviations
are not additive; therefore, the sum of the standard deviation shown does
not equal the overall standard deviation of the concrete strength.(9)
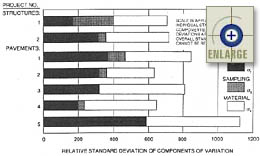 |
|
Figure
1. PCC relative standard deviation of components of variation
for compressive strength.(9) |
Similar
data was presented in a 1973 report by Di Cocco.(10)
He analyzed 28-day cylinder compressive test data from nine projects (the
data included concrete placed using three different mixer typescentral
mixer, paver, and truck mixer). The results showed an overall standard
deviation of 4.98 MPa for the nine projects.
Darter
also combined 28-day cylinder compressive strength data from 11 different
sourcesa total of 56 projects in all. It is important to note
that the data are comprised of test values in which one test represents
the average of three replicate cylinder tests. The data collected
for these 56 projects are presented in table 5. The data show an
average overall project standard deviation of 3.72 MPa (averages of three
cylinder tests) and an average overall project COV of 12.1 percent.
Table
5. Summary of 28-day cylinder compressive strength statistics of
various projects.(8)
Project
Number
|
Class
|
No.
of Tests
|
Mean,
MPa
|
Std.
Dev., MPa
|
COV,
%
|
1
|
pavement
|
536
|
31.19
|
2.73
|
8.8
|
2
|
pavement
|
292
|
33.65
|
3.72
|
11.1
|
3
|
pavement
|
96
|
39.20
|
3.75
|
9.6
|
4
|
pavement
|
192
|
38.11
|
3.90
|
10.2
|
5
|
pavement
|
196
|
35.15
|
3.98
|
11.3
|
6
|
pavement
|
112
|
33.27
|
4.19
|
12.6
|
7
|
pavement
|
258
|
37.71
|
4.60
|
12.2
|
8
|
pavement
|
320
|
36.16
|
4.65
|
12.9
|
9
|
pavement
|
232
|
36.47
|
4.90
|
13.4
|
10
|
pavement
|
176
|
33.97
|
5.00
|
14.7
|
11
|
pavement
|
126
|
34.94
|
5.05
|
14.4
|
12
|
pavement
|
46
|
24.13
|
3.19
|
13.2
|
13
|
pavement
|
12
|
28.90
|
3.52
|
12.2
|
14
|
pavement
|
12
|
28.10
|
2.18
|
7.8
|
15
|
pavement
|
15
|
29.65
|
1.92
|
6.5
|
16
|
pavement
|
14
|
37.48
|
4.38
|
11.7
|
17
|
pavement
|
22
|
28.33
|
3.79
|
13.4
|
18
|
pavement
|
27
|
36.41
|
3.30
|
9.0
|
19
|
pavement
|
31
|
30.34
|
2.89
|
9.5
|
20
|
pavement
|
24
|
30.45
|
2.75
|
9.0
|
21
|
pavement
|
14
|
27.53
|
6.74
|
24.5
|
22
|
pavement
|
25
|
28.46
|
1.99
|
7.0
|
23
|
pavement
|
10
|
26.82
|
3.56
|
13.3
|
24
|
pavement
|
15
|
31.76
|
3.31
|
10.4
|
25
|
pavement
|
13
|
26.73
|
2.68
|
10.0
|
26
|
pavement
|
93
|
29.75
|
3.56
|
12.0
|
27
|
pavement
|
82
|
33.74
|
3.01
|
9.0
|
28
|
pavement
|
845
|
33.45
|
5.12
|
15.3
|
29
|
pavement
|
5318
|
31.35
|
4.36
|
13.9
|
30
|
pavement
|
8468
|
29.35
|
4.29
|
14.6
|
31
|
pavement
|
146
|
33.17
|
4.58
|
13.8
|
32
|
pavement
|
39
|
29.79
|
5.01
|
16.8
|
33
|
pavement
|
68
|
15.58
|
2.10
|
13.5
|
34
|
pavement
|
208
|
36.19
|
3.38
|
9.3
|
35
|
pavement
|
861
|
35.71
|
3.72
|
10.4
|
36
|
pavement
|
296
|
40.33
|
10.62
|
25.6
|
37
|
pavement
|
51
|
19.51
|
2.79
|
14.3
|
38
|
pavement
|
44
|
20.13
|
3.19
|
15.8
|
39
|
pavement
|
153
|
26.06
|
2.81
|
10.8
|
40
|
pavement
|
87
|
23.37
|
3.80
|
16.2
|
41
|
pavement
|
81
|
25.30
|
3.09
|
12.2
|
42
|
pavement
|
89
|
24.13
|
2.50
|
10.4
|
43
|
pavement
|
61
|
22.61
|
3.30
|
14.6
|
44
|
pavement
|
19
|
32.41
|
2.09
|
6.4
|
45
|
pavement
|
23
|
41.09
|
2.39
|
5.8
|
46
|
pavement
|
33
|
25.17
|
2.16
|
8.6
|
47
|
pavement
|
74
|
36.34
|
4.62
|
12.7
|
48
|
pavement
|
44
|
30.27
|
4.01
|
13.3
|
49
|
pavement
|
14
|
35.85
|
2.94
|
8.2
|
50
|
pavement
|
28
|
34.68
|
4.41
|
12.7
|
51
|
pavement
|
47
|
17.75
|
2.28
|
12.8
|
52
|
pavement
|
63
|
22.25
|
2.96
|
13.3
|
53
|
pavement
|
63
|
29.18
|
3.40
|
11.6
|
54
|
pavement
|
187
|
35.64
|
4.23
|
11.9
|
55
|
pavement
|
65
|
33.25
|
3.67
|
11.1
|
56
|
pavement
|
90
|
40.55
|
5.12
|
12.6
|
Average
|
|
|
30.87
|
3.72
|
12.1
|
Note:
One test usually indicates the average of three replicate cylinders.
The
standards for 28-day cylinder compressive test COV (recommended by the
American Concrete Institute [ACI] in 1972) were also presented in the
1972 paper by Darter.(8)
These standards are summarized in table 6. A comparison of the summary
results from the 56 projects (COV of 12.1 percent) shows that the average
observed project quality falls in the "Good" range. In
the conclusions of his 1972 report, Darter recommends that a compressive
strength COV of 15 percent be used for design.
Table
6. ACI 1972 recommended standards for 28-day cylinder compressive
test COV.(8)
Class of
Operation
|
Coefficients
of Variation for Different Control Standards
|
Excellent
|
Good
|
Fair
|
Poor
|
Overall
variations: |
General
construction
|
Below
10.0
|
10.0
to 15.0
|
15.0
to 20.0
|
Above
20.0
|
Laboratory
control
|
Below
5.0
|
5.0
to 7.0
|
7.0
to 10.0
|
Above
10.0
|
Within-test
variations: |
Field
control
|
Below
4.0
|
4.0
to 5.0
|
5.0
to 6.0
|
Above
6.0
|
Laboratory
control
|
Below
3.0
|
3.0
to 4.0
|
4.0
to 5.0
|
Above
5.0
|
Neaman and Laguros presented 28-day cylinder compressive strength results
from a 12.9-km project in Oklahoma.(11)
Two-hundred pairs of cylinders (400 total cylinders) were tested for the
project, resulting in an overall 28-day cylinder compressive strength
mean and standard deviation of 26.22 and 4.97 MPa, respectively.
A histogram of this strength data is presented in figure 2.
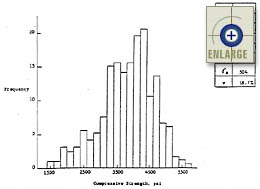 |
|
Figure
2. Histogram of 28-day cylinder compressive strength data for
a project constructed in Oklahoma (200 pairs of 2 cylinders).(11) |
1 psi = 6.9 kPa
In a 1992 report,
Wood presented tables of data showing normalized compressive strength
means and standard deviations for different ages.(12)
In addition to age, the report also looked at the influence of curing
condition and type of cement. Concrete compressive strength values
at 1, 3, and 7 days were normalized by dividing by the corresponding 28-day
compressive strength. These results, for the four different curing
conditions, are presented in tables 7 through 10.
Table
7. Variation of normalized concrete compressive strength with agemoist
curingportland cements.(12)
Age
at Test
|
Type
of Cement
|
I
|
II
|
III
|
IV
|
No.
|
Mean,
MPa
|
Std.
Dev., MPa
|
No.
|
Mean,
MPa
|
Std.
Dev., MPa
|
No.
|
Mean,
MPa
|
Std.
Dev., MPa
|
No.
|
Mean,
MPa
|
Std.
Dev., MPa
|
Moist
Curing
|
1
day
|
46
|
0.18
|
0.07
|
13
|
0.16
|
0.04
|
10
|
0.30
|
0.11
|
11
|
0.13
|
0.03
|
3
days
|
46
|
0.46
|
0.10
|
3
|
0.35
|
0.02
|
24
|
0.62
|
0.11
|
3
|
0.24
|
0.03
|
7
days
|
64
|
0.70
|
0.09
|
13
|
0.61
|
0.08
|
28
|
0.81
|
0.08
|
11
|
0.48
|
0.06
|
28
days
|
64
|
1.0
|
|
13
|
1.0
|
|
28
|
1.0
|
|
11
|
1.0
|
|
Note:
Data from 152-mm modified cubes and 152- x 305-mm cylinders are included.
Table
8. Variation of normalized concrete compressive strength with agemoist
curingblended cements.(12)
Age
at Test
|
Type
of Cement
|
IS
|
IP
|
IA
|
No.
|
Mean,
MPa
|
Std.
Dev., MPa
|
No.
|
Mean,
MPa
|
Std.
Dev., MPa
|
No.
|
Mean,
MPa
|
Std.
Dev., MPa
|
Moist
Curing
|
1
day
|
20
|
0.22
|
0.07
|
15
|
0.10
|
0.03
|
9
|
0.14
|
0.06
|
3
days
|
20
|
0.42
|
0.09
|
15
|
0.32
|
0.09
|
|
|
|
7
days
|
20
|
0.62
|
0.10
|
15
|
0.53
|
0.11
|
9
|
0.69
|
0.09
|
28
days
|
20
|
1.0
|
|
15
|
1.0
|
|
9
|
1.0
|
|
Note:
Data from 152-mm modified cubes and 152- x 305-mm cylinders are included.
Table
9. Variation of normalized concrete compressive strength with ageair
curing.(12)
Age
at Test
|
Type
of Cement
|
I
|
III
|
IS
|
IP
|
No.
|
Mean,
MPa
|
Std.
Dev., MPa
|
No.
|
Mean,
MPa
|
Std.
Dev., MPa
|
No.
|
Mean,
MPa
|
Std.
Dev., MPa
|
No.
|
Mean,
MPa
|
Std.
Dev., MPa
|
Air
Curing
|
1
day
|
10
|
0.16
|
0.08
|
6
|
0.24
|
0.08
|
20
|
0.21
|
0.06
|
15
|
0.10
|
0.03
|
3
days
|
19
|
0.44
|
0.10
|
15
|
0.56
|
0.13
|
20
|
0.40
|
0.08
|
15
|
0.33
|
0.08
|
7
days
|
19
|
0.67
|
0.09
|
15
|
0.78
|
0.10
|
20
|
0.59
|
0.08
|
15
|
0.54
|
0.10
|
28
days
|
19
|
1.0
|
|
15
|
1.0
|
|
20
|
1.0
|
|
15
|
1.0
|
|
Note:
Data from 152-mm modified cubes and 152- x 305-mm cylinders are included.
Table
10. Variation of normalized concrete compressive strength with ageoutdoor
exposure.(12)
Age
at Test
|
Type
of Cement
|
I
|
III
|
No.
|
Mean,
MPa
|
Std.
Dev., MPa
|
No.
|
Mean,
MPa
|
Std.
Dev., MPa
|
Outdoor
Exposure
|
1
day
|
|
|
|
|
|
|
3
days
|
21
|
0.53
|
0.10
|
21
|
0.69
|
0.15
|
7
days
|
21
|
0.78
|
0.09
|
21
|
0.88
|
0.12
|
28
days
|
21
|
1.0
|
|
21
|
1.0
|
|
Note:
Data from 152-mm modified cubes.
A
large amount of cylinder compressive strength data was collected at a
1993 paving project in Colorado.(13)
The project consisted of 25.7 km of paving on I-70 near the town of Vona.
A mean and standard deviation of 37.02 and 3.14 MPa, respectively, were
calculated for the 436 cylinders tested for 28-day compressive strength.
A histogram showing the testing results is presented in figure 3.
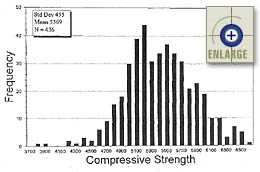 |
|
Figure
3. Histogram of 28-day cylinder compressive strength results1993
project on I-70 near Vona, Colorado.(13)
|
An article published
by the American Concrete Pavement Association (ACPA) in 1995 discussed
the typical 28-day compressive strength standard deviation expected from
ready-mix plants.(14)
It reported that historical records from past plant operations showed
that this standard deviation could be expected to be less than 2.76 MPa
for concrete coming from a well-controlled ready-mix operation.
In addition, it reported that ready-mix concrete historically has COVs
in the 7- to 13-percent range, whereas COVs for central-mix concrete
generally fall in the 5- to 12-percent range.
A
1990 report contained a reprint of an article by McMahon et al. that discussed
the quality assurance (QA) of PCC pavement.(9)
The authors reported the following information related to concrete
strength:
- Strength is not
always the most important characteristic of concrete quality, but it
is the one that is most often measured. It is assumed to be indicative
of the water-cement ratio and, accordingly, an indicator of durability.
The magnitude of the variability in strength, is, therefore, an indicator
of the magnitude of variability of the other characteristics.
- Variability in
concrete strengths can be attributed to two other types of variability:
(1) Inherent variability in the materials and processes that results
from chance causes, which cannot be controlled, and (2) variability
from assignable causes that can be controlled.
- The measurement
of variability from chance or inherent causes is complicated by the
inherent variability of each of the ingredients in the mix, which can
interact with the processes of blending, mixing, and placing, and result
in a much larger variability in the concrete itself.
- The assignable
causes of variability are more numerous and more difficult to isolate,
but the production of quality concrete is dependent on the reduction
of all variables. However, the isolation and restriction of variables
can be carried only as far as economic conditions warrant. Under
the present state of knowledge, the ultimate uniformity of concrete
production cannot be precisely stated. Extensive research will
be necessary to isolate variables and to determine the extent to which
variation can be reduced.
McMahon
et al. present variability data from many different published sources
in their article. Table 11 summarizes their results.
Table
11. Average deviation of 28-day concrete compressive strengths.(9)
Agency
|
Concrete
Type
|
Data Source
|
Average
Standard Deviation, MPa
|
Bureau
of Public Roads |
Paving
|
Research
|
4.03
|
Bureau
of Public Roads |
Paving
|
Historical
|
3.26
|
Bureau
of Public Roads |
Structural
|
Historical
|
3.97
|
Virginia
Dept of Highways |
Structural
|
Special
|
3.22
|
Virginia
Dept of Highways |
Paving
|
Cores
|
4.57
|
Ontario
Dept of Highways |
Paving
|
Routine
|
3.41
|
Note: The average
standard deviation is for all data presented.
Results
of an analysis of historical cylinder compressive strengths by the State
Road Department of Florida were also presented in the article by McMahon
et al.(9)
These results included data from two different concrete types (class A
and class NS). It was noted that "routine control is normally
exercised over class A concrete, whereas class NS concrete is spot checked
only occasionally." Tables 12 and 13 contain the results from
the Florida study (table 12 presents the results by project, and table
13 presents the results by concrete production source).
Table
12. Historical concrete compressive strength data published by the
State Road Department of Floridaproject comparison.(9)
Project
Number
|
Number
of Samples
|
Mean,
MPa
|
Overall
Std. Dev., MPa
|
COV,
%
|
Testing
Error, MPa
|
28-day
cylindersclass A concrete
|
1
1
|
536
|
31.19
|
2.73
|
8.8
|
1.21
|
2
|
292
|
33.65
|
3.72
|
11.1
|
1.43
|
3
|
96
|
39.20
|
3.75
|
9.6
|
1.28
|
4
|
192
|
38.11
|
3.90
|
10.2
|
1.07
|
5
|
196
|
35.15
|
3.98
|
11.3
|
0.332
|
6
|
112
|
33.27
|
4.19
|
12.6
|
1.35
|
7
|
258
|
37.71
|
4.60
|
12.2
|
1.03
|
8
|
320
|
36.16
|
4.65
|
12.9
|
1.09
|
9
|
232
|
36.47
|
4.90
|
13.4
|
1.32
|
10
|
176
|
33.97
|
5.00
|
14.7
|
1.45
|
11
|
126
|
34.94
|
5.05
|
14.4
|
1.12
|
Average
3
|
230
|
35.44
|
4.23
|
13.1
|
1.23
|
Range
|
224
|
5.93
|
1.32
|
5.1
|
0.41
|
28-day
cylindersNS concrete
|
1
1
|
50
|
27.72
|
2.741
|
9.9
|
115
|
2
|
340
|
24.51
|
3.79
|
15.5
|
93
|
3
|
240
|
27.62
|
4.00
|
14.5
|
134
|
4
|
200
|
23.95
|
4.17
|
17.4
|
122
|
5
|
240
|
26.07
|
4.62
|
17.7
|
96
|
6
|
196
|
28.90
|
5.03
|
17.4
|
160
|
7
|
148
|
29.05
|
5.05
|
17.4
|
92
|
8
|
94
|
29.23
|
5.34
|
18.3
|
87
|
9
|
108
|
25.21
|
5.34
|
21.2
|
116
|
10
|
182
|
25.33
|
5.35
|
21.1
|
113
|
11
|
156
|
28.34
|
5.35
|
18.9
|
70
|
12
|
224
|
28.81
|
5.69
|
19.8
|
127
|
13
|
138
|
27.17
|
6.09
|
22.4
|
161
|
Average
3
|
178
|
27.07
|
4.81
|
17.8
|
114
|
Range
|
246
|
5.27
|
2.30
|
7.9
|
91
|
- Notes: 1
Values are not included in range calculations.
- 2
Statistical outliernot included in calculation of range or average.
- 3
Averages are not weighted and include all values except the outlier.
Table
13. Historical concrete compressive strength data published by the
State Road Department of Floridaproduction source comparison.(9)
Source
|
Concrete
Class
|
Number
of Samples
|
Mean
Strength, MPa
|
Pooled
Std. Dev., MPa
|
COV,
%
|
1
|
A
|
480
|
33.09
|
4.09
|
12.4
|
NS
|
218
|
28.21
|
4.27
|
15.2
|
2
|
A
|
540
|
33.83
|
4.63
|
13.7
|
NS
|
360
|
29.03
|
4.55
|
15.7
|
3
|
A
|
440
|
34.85
|
4.03
|
11.6
|
NS
|
308
|
27.79
|
4.03
|
14.5
|
A 1966 paper by Steele et al. presented a summary of data collected for
two projects in West Virginia.(15)
A summary of the 28-day cylinder compressive strength results (reported
for both projects) is presented in table 14. The authors of this
report point out that although a typical project standard deviation
could be estimated to be around 3.17 MPa, it could range from 2.41 to
4.48 MPa. A calculated standard deviation for one lot may even
be higher.
Table
14. Strength parameters for Class A structural concretetwo
projects in West Virginia.(15)
Project
|
Number
of Tests
|
Avg 28-day
Compressive Strength, MPa
|
Standard
Deviation Individuals, MPa
|
West
VirginiaProject A |
190
|
29.20
|
3.00
|
West
VirginiaProject B |
200
|
30.47
|
3.32
|
Average |
|
29.84
|
3.17
|
A literature review conducted by ERES Consultants, Inc. for a report titled
Measurement and Specification of Construction Quality included
six different figures showing normal distributions of different types
of PCC strength data.(16)
These are presented in figures 4 through 9.
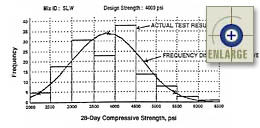 |
|
Figure
4. Histogram of 28-day concrete compressive strength.(16)
|
1 psi = 6.9 kPa
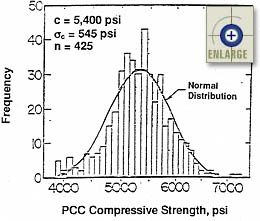 |
|
Figure
5. Distribution of PCC compressive strength.
(16)
|
1 psi = 6.9 kPa
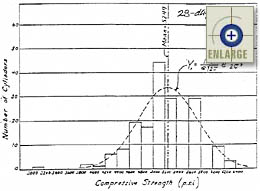 |
|
Figure
6. Histogram of 28-day cylinder concrete compressive strength.(16)
|
1 psi = 6.9 kPa
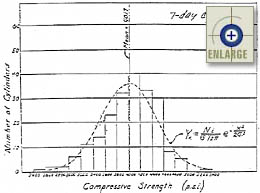 |
|
Figure
7. Histogram of 7-day cylinder concrete compressive strength.(16)
|
1 psi = 6.9 kPa
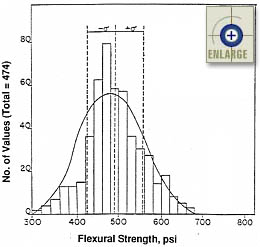 |
|
Figure
8. Histogram of concrete flexural strength.(16)
|
1 psi = 6.9 kPa
 |
|
Figure
9. Histogram of concrete flexural strength.(16)
|
1 psi = 6.9 kPa
Actual concrete strength
compressive strength data were also collected for the Federal Highway
Administration (FHWA)-sponsored project "Measurement and Specification
of Construction Quality."(17)
Both 28-day cylinder and core data were collected for three projects
(one each for Illinois, Minnesota, and Ohio) constructed during the 1995
construction season. The results of the statistical analysis for
both data sets are presented in table 15.
Table
15. 1995 28-day cylinder and core compressive strength data.(17)
Project
Location
|
Sample
Type
|
No. of
Samples
|
Mean, MPa
|
Std Dev,
MPa
|
COV, %
|
Rochelle,
IL |
Cylinder
|
106
|
37.40
|
5.16
|
13.8
|
Core
|
30
|
40.12
|
3.76
|
9.4
|
Mankato,
MN |
Cylinder
|
56
|
36.62
|
3.36
|
9.2
|
Core
|
30
|
41.26
|
7.38
|
17.9
|
Bellefontaine,
OH |
Cylinder
|
100
|
29.53
|
2.43
|
8.2
|
Core
|
31
|
41.45
|
5.32
|
12.8
|
Cylinder
Data OnlyAverages |
3.65
|
10.4
|
Core
Data OnlyAverages |
5.49
|
13.4
|
In
1996, Hughes compiled a table of typical 28-day PCC cylinder statistics
in a report titled Variability in Highway Pavement Construction.(6)
This table included data from two published State Highway Agency (SHA)
reports (from Arizona and Pennsylvania), as well as data from databases
and variability studies provided with a completed questionnaire.
These data are presented in table 16. Hughes also reported that the New
Jersey DOTs typical standard deviation associated with a lot is
approximately 2.07 MPa.
Table
16. Typical standard deviations for 28-day PCC cylinder strengths.(6)
Source
|
Year
|
Class
|
Mean, MPa
|
Std Dev,
MPa
|
COV, %
|
Georgia |
1993
|
Paving
|
32.89
|
3.35
|
10.2
|
New
York |
1993
|
Gen
Structural
|
30.43
|
5.21
|
17.3
|
New
York |
1993
|
Thin
Structural
|
33.27
|
5.36
|
16.3
|
New
York |
1993
|
Pumping
|
34.74
|
5.39
|
15.8
|
Maine |
1992
|
Gen
Structural
|
35.66
|
4.05
|
11.4
|
Maine |
1991
|
Gen
Structural
|
34.12
|
4.55
|
13.3
|
Virginia |
1988
|
Gen
Structural
|
33.40
|
4.55
|
13.6
|
Virginia |
1988
|
High
Strength
|
39.76
|
4.37
|
11.2
|
Arizona |
1974
|
Paving
|
30.16
|
4.15
|
13.8
|
Pennsylvania |
1972
|
Gen
Structural
|
32.06
|
4.83
|
15.1
|
Note: Standard
deviation based on single 28-day cylinders.
Variation
of Concrete Flexural Strength
Flexural
strength data from the Illinois Department of Transportation MISTIC database
were summarized and presented in a 1995 report.(7)
The results are shown in table 17. An analysis of the data shows
a typical average beam flexural strength standard deviation of 0.44 MPa
and an average COV of 8.1 percent.
Table
17. Concrete beam 28-day flexural strength variability data from
the Illinois Department of Transportation MISTIC Database.(7)
Mix Number
|
Class
|
Year
|
n
|
Mean, MPa
|
Std Dev,
MPa
|
COV, %
|
1
|
Structural
|
Unknown
|
18
|
5.63
|
0.60
|
10.7
|
2
|
Structural
|
Unknown
|
129
|
5.41
|
0.34
|
6.4
|
3
|
Structural
|
Unknown
|
13
|
5.35
|
0.39
|
7.3
|
Structural
Data Averages
|
5.46
|
0.44
|
8.1
|
Flexural
stength variability data were also presented by Darter in a 1972 report.(8)
This consisted of data from five Texas Highway Department projects, as
well as some data from the original American Association of State Highway
Officials (AASHO) Road Test. This information is summarized in table
18.
Table
18. Concrete beam 28-day flexural strength variability data from
the Texas Highway Department and the AASHO Road Test.(8)
Project
Number
|
Number
of Tests
|
Mean, MPa
|
Std Dev,
MPa
|
COV, %
|
Texas
Highway Department Data
|
1
|
135
|
4.78
|
0.57
|
11.8
|
2
|
305
|
4.56
|
0.39
|
8.4
|
3
|
474
|
3.38
|
0.46
|
13.7
|
4
|
258
|
2.82
|
0.14
|
4.9
|
5
|
270
|
4.67
|
0.45
|
9.6
|
AASHO
Road Test Data
|
1
|
11
|
4.55
|
0.35
|
7.7
|
2
|
11
|
4.90
|
0.37
|
7.5
|
Texas
Data OnlyAverages
|
4.04
|
0.40
|
9.7
|
AASHO
Data OnlyAverages
|
4.72
|
0.36
|
7.6
|
All
Project DataAverages
|
4.23
|
0.39
|
9.1
|
An
analysis of the flexural strength data in table 18 shows a typical average
beam flexural strength standard deviation of 0.39 MPa and an average COV
of 9.1 percent. Darter does point out that the AASHO data show less
variability than the Texas data (probably due to the stringent quality
control procedures at the Road Test). In this report, Darter recommends
that a flexural strength COV of 15 percent be used for design.(8)
In
a 1996 report, Hughes presented typical flexural strength data collected
from four different State studies.(6)
It is interesting to note that one of these States (Indiana) presented
contractor quality control data and State DOT acceptance data for the
same project. The collected data are presented in table 19.
Table
19. Typical flexural strength data for different State studies.(6)
Data Source
|
Test Type
|
Mean, MPa
|
Std. Dev.,
MPa
|
COV, %
|
Midwestern
State #1 |
mid-point
loading
|
5.63
|
0.72
|
12.7
|
Midwestern
State #2 |
third-point
loading
|
4.69
|
0.48
|
10.4
|
Pennsylvania |
not
reported
|
5.45
|
0.69
|
12.7
|
IndianaContractor
Quality Control Tests |
not
reported
|
4.52*
|
0.23*
|
5.0
|
IndianaState
Acceptance Tests |
not
reported
|
4.52*
|
0.26*
|
5.8
|
*
Each "sample value" included in the statistical analysis represents
the average of two beam breaks.
A
report by Greer contained information regarding the within- and between-batch
flexural strength variations in the laboratory and the field.(18)
The study analyzed published data from more than 200 mixes (more than
765,000 m3
of concrete) placed at the Atlanta International Airport. In the
laboratory, the within-test standard deviation represents the amount
of variation among flexural strength tests from the same batch of concrete
and is an indicator of the quality of the procedures performed by the
laboratory personnel. The laboratory between-batch variation,
however, "indicates the amount of variation between different batches
of the same concrete materials." In the field, the within-test
standard deviation is an indicator of the quality of the testing procedures
performed by the field testing personnel. The field between-batch
variability indicates the quality of the production and control procedures
used by the contractor and supplier. The results of the Greer study
are presented in table 20.
Table
20. Measured flexural strength variations at the Atlanta International
Airport.(18)
Variation
Type
|
Std
Dev Range, MPa
|
Average
Std. Dev., MPa
|
28-day
laboratory within-test |
Not
available
|
0.23
|
28-day
laboratory between-batch |
Not
available
|
0.19
|
28-day
field within-test |
0.22
0.28
|
0.24
|
28-day
field between-batch |
0.18
0.36
|
0.24
|
3-day
field within-test |
0.17
0.23
|
0.20
|
7-day
field between-batch |
0.17
0.33
|
0.29
|
Greer
noted that both the laboratory within-test and between-batch standard
deviations for both sources are independent of the measured flexural strength.(18)
Therefore, it can be concluded that the standard deviation is more appropriate
than the COV when evaluating flexural strength tests. Table 21 contains
proposed guidelines for assessing the level of quality associated with
flexural strength testing data.(18)
Table
21. Proposed guidelines for assessing the level of quality associated
with flexural strength testing data.(18)
Within-Test
Standard Deviation (Testing Agency)
|
Overall
Standard Deviation (Contractor)
|
Level
of Quality (Quality Control)
|
<
0.28 MPa
|
<
0.28 MPa
|
Excellent
to Good
|
0.28
0.45 MPa
|
0.28
0.45 MPa
|
Good
to Fair
|
>
0.45 MPa
|
>
0.45 MPa
|
Fair
to Poor
|
A
large amount of data was collected at a 1993 Colorado paving project.
The project consisted of 25.7 km of paving on I-70 near the town of Vona.
Flexural strength was measured from third-point load testing (modulus
of rupture) of 11 sets of 2 beams each. A mean and standard deviation
of 4.69 and 0.44 MPa, respectively, were observed from the testing.(13)
An
article published by ACPA in 1995 discussed the typical 28-day third-point
flexural strength standard deviation expected from ready-mix plants.(14)
It reported that historical records from past plant operations showed
that this standard deviation could be expected to be less than 0.48 MPa
for concrete coming from a well-controlled ready-mix operation.
Variation
of Concrete Split Tensile Strength
Split
tensile strength data were also collected at the 1993 Colorado paving
project.(13)
Split tensile strength tests were conducted on 39 sets of 2 cylinders
each, resulting in an overall mean and standard deviation of 3.10 and
0.26 MPa, respectively.
Within-Test
and Between-Batch Variability
A
report by Gray reported on a study that investigated both the between-
and within-laboratory variability.(19)
The study looked at testing results obtained in interlaboratory or comparative
testing programs that were operated in the three largest metropolitan
areas of British Columbia and Alberta, Canada. The study separately
analyzed laboratories that were and were not certified by the Canadian
Standards Association (CSA). Figure 10 shows linear trends of within-laboratory variability
versus average compressive strength for all programs. Figure
11 shows linear trends of average within-laboratory and between-laboratory
variability versus average compressive strength. Figure
12 shows linear trends of between-laboratory variability versus average
compressive strength for all programs. The following two conclusions were
drawn from the studys results:(19)
- The within-laboratory
precision of the standard test method for determining the compressive
strength of cylindrical portland cement concrete test specimens varies
linearly with the compressive strength of the test concrete. As
measured by the 95-percent repeatability limit (within a laboratory),
this variability approaches 10 percent of the compressive strength.
This implies that on the basis of test error alone, the difference in
absolute value of two test results obtained in the same laboratory on
the same material can be expected to exceed approximately 10 percent
of the average compressive strength of the test concrete about 5 percent
of the time, and there is reason to question one or both of the test
results only if such a difference is found to be larger than this value.
- The
between-laboratory precision of the standard test method also varies
linearly with the compressive strength of the test concrete. As
expressed by the 95-percent reproducibility limit (between laboratories),
this variability approaches 15 percent of the compressive strength.
This implies that on the basis of test error alone (including both the
within and between-laboratory components), the difference in absolute
value of two test results obtained in different laboratories on the
same material can be expected to exceed approximately 15 percent of
the average compressive strength of the test concrete about 5 percent
of the time, and there is reason to question one or both of the test
results only if such a difference is found to be larger than this value.
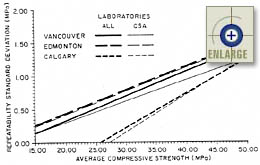 |
|
Figure
10. Repeatability (within a laboratory) standard deviation versus
average compressive strength for all programs.(19) |
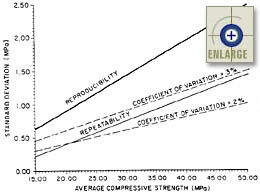 |
|
Figure
11. Average repeatability (within a laboratory) and reproducibility
(between laboratories) standard deviations versus average compressive
strength.(19)
|
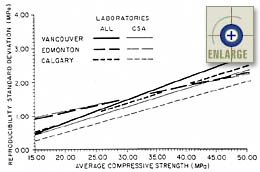 |
|
Figure
12. Reproducibility (between laboratories) standard deviation
versus average compressive strength for all programs.(19)
|
ACI
214-89 "Recommended Practice for Evaluation of Strength Test Results
of Concrete" was reviewed as part of a literature review conducted
by ERES Consultants, Inc. for a report titled Measurement and Specification
of Construction Quality.(16)
ACI Guidelines for determining the quality of a laboratory, based on observed
within-test COVs for compressive strength, are provided in table
22.
Table
22. Compressive strength within-test COV guidelines.(16)
Within-Test
COV*
|
Laboratory
Control
|
Below
3.0
|
Excellent
|
3.0
to 4.0
|
Very
Good
|
4.0
to 5.0
|
Good
|
5.0
to 6.0
|
Fair
|
Above
6.0
|
Poor
|
*
Variation in compressive strength between replicate samples tested
by the same operator.
Other information
included in the literature review stated that typical COV values for 7-day
flexural strength range from 2.8 to 17.6 percent, while COVs for
28-day flexural strength range from 3.5 to 9.6 percent.(16)
Accelerated
Testing Methods for Concrete Strength
Much
can be learned about nondestructive testing (NDT) methods for concrete
strength from the fast-track paving technology. Fast-track techniques
are generally used to move up the traffic open date of a newly constructed
or repaired PCC pavement. A number of different techniques have
been developed to provide quick and reliable assessments of the concrete
strength at early ages. One reviewed ACPA report describes the current
state of fast-track paving techniques, including six nondestructive strength
assessment methods that have been used.(20)
A table outlining the six methods is presented as table 23. Of these
six techniques, the most commonly used are the maturity and pulse-velocity
methods (both of which are described in more detail in the following sections).
Table
23. Non-destructive test methods for concrete.(20)
Test
Method
|
Standard
|
Basic
Description
|
Testing
Precision to Baseline Cylinder Strength2
|
Surface
Hardness (Swiss Hammer) |
ASTM
C 805 |
Rebound
of hammer correlates to surface hardness & compressive strength |
±
40 %
|
Penetration
Resistance (Windsor Probe) |
ASTM
C 803 |
Penetration
depth of gun-fired probe correlates to surface hardness &
compressive strength |
±
20 %
|
Pullout1 |
ASTM
C 900 |
Force
to remove cast-in metal probe correlates to surface compressive
strength |
±
15 %
|
Break-off |
ASTM
C 1150 |
Force
necessary to break a circular core cast or cut partially into
slab correlates to flexural strength |
±
15 %
|
Maturity |
ASTM
C 1074 |
Internal
temperature of concrete relates directly to concrete strength |
±
5 %
|
Pulse
Velocity |
ASTM
C 597 |
Velocity
of sound wave from transducer to receiver through concrete relates
to concrete strength |
±
10 %
|
- Notes: 1
Cap and pull-out (CAPO) variation of pull-out test not approved
by ASTM.
- 2
These are estimates of precision based on cylinder strength
tests made using recommended ASTM procedures. Inaccurate concrete
strength characterization by destructive cylinder testing is a common
problem.
Maturity Method
The
following is an excerpt from the above-mentioned ACPA report that describes
some of the maturity concepts.(20)
"Maturity
testing provides strength evaluation through monitoring of internal
concrete temperature in the field. The basis of maturity is that
each concrete mix has a unique strength-time relationship. Therefore,
a mix will have the same strength at a given maturity no matter what
conditions (time or temperature) occur before measurement."
Two methods of maturity
were introduced in the reportthe Nurse-Saul method and the
Arrhenius maturity equation. In the United States, the Nurse-Saul
method is the more commonly used of the two methods. The Nurse-Saul
method calculates maturity as a function of time and temperature using
equation 2.
M(t) =
S(TA
T0)
Dt
(2)
where
M(t) =
Temperature-time factor, degree-days or degree-hours.
Dt =
Time interval, days or hours.
TA
= Average concrete temperature during time interval, °C.
T0
= Datum temperature, °C (typically
10 °C).
No specific information
on the Arrhenius maturity method was provided; however, the report did
refer to ASTM C 1074 as a source for more information on the method.
Estimated
strength gain versus maturity is mix-specific. Therefore, laboratory
testing is required to accurately assess the as-constructed slab strength.
The following excerpt from the ACPA report describes the details of the
required laboratory and field maturity procedures.(20)
"Laboratory
testing requires preparation of trial batches using the actual field-mix
materials. Technicians must monitor the batch temperature and break
cylinders to develop a relationship between the strength criterion and
the temperature-time factor. This relationship becomes the calibration
curve for evaluating the field concrete strength.
Field maturity
evaluation begins with the embedment of thermocouples of temperature
probes in the concrete when practicable after finishing or curing. The
probes must connect to either commercially available maturity meters
or temperature recorders with an accuracy of 1 °C. Technicians take
readings at regular intervals then estimate strength using the temperature-time
relationship from the laboratory study."
Pulse-Velocity
Method
The
pulse-velocity method estimates concrete strength or stiffness by measuring
the time required for an ultrasonic wave to pass through the concrete
from one transducer to another. This method is also mix-specific;
therefore, laboratory testing is required to accurately assess the as-constructed
slab strength. The following excerpt from the ACPA report describes
the details of the required laboratory and field pulse-velocity procedures.(20)
"Pulse-velocity
testing requires laboratory calibration to produce meaningful field
information. Pulse-velocity readings are sensitive to aggregate,
water-cement-plus-pozzolan ratio, moisture content, and concrete consolidation.
Therefore, trial batches must contain the same mix materials
at similar proportions as the project mix. In the laboratory,
technicians take pulse-velocity measurements through a representative
number of cast specimens, test the specimens for strength, and plot
the results against the pulse-velocity readings to create a calibration
curve."
Finally, pulse-velocity
measurements are taken in the field following the manufacturers
recommendations for placement of the transducers. Early-age concrete
strengths are then estimated using the laboratory-developed calibration
curves.
Compressive
Versus Flexural Strength
Historically,
flexural strength testing has been used for acceptance and design; however,
today the trend is toward using compressive strength testing for not only
quality control, but acceptance as well.
Advantages of
Compressive Strength Over Flexural Strength for Acceptance
The
following list of the advantages of using compression test cylinders,
as opposed to flexural test beams, was compiled by Kosmatka:(21)
- Cylinders are
easier to make, handle, transport, and test.
- Construction and
inspection personnel are better acquainted with proper casting and testing
procedures for cylinders.
- Cylinders are
less sensitive to variations in testing procedures.
- Compression tests
have a lower coefficient of variation. For example, tests using
concretes made with 56 aggregate combinations and 2 different cement
contents had an average batch-to-batch COV of 5.73 percent for flexural
tests and 3.25 percent for compression tests.
- Some of the most
commonly used specifications and guidelines refer to concrete acceptance
criteria based on compressive strength.
- Statistical data
for ready-mix concrete design are usually available for compressive
strength, but not necessarily for flexural strength.
- Durability criteria
for mix design is usually based on compressive strength.
- Investigations
on low in-place concrete strengths are much easier to perform using
drilled cores than sawed beams.
Strength
Type Conversion Equations
In
the current PRS approach, flexural strength is used in the distress indicator
models that are dependent on strength. As many SHAs move toward
strength acceptance based on compressive or tensile strength testing,
it is becoming more important to understand the relationships between
different strength types.
Many
different strength-type relationships were discussed in Darters
1972 report.(8)
A relationship between modulus of elasticity and compressive strength
is presented as equation 3. (Note: Equation 3 was developed in English
units.)
Ec
= 33 w1.5
(fc)0.5
(3)
where
Ec
= Static modulus of elasticity of concrete, psi.
w =
Air dry weight of concrete at time of test, pcf.
fc
= Compressive strength of concrete at time of test, psi.
Flexural
strength is commonly estimated using an equation of the form shown in
equation 4.
S =
K (fc)0.5
(4)
where
S =
Flexural strength (modulus of rupture), MPa.
K =
Constant usually between 0.6 and 0.8 MPa.
fc
= Compressive strength of concrete at time of test, MPa.
As
stated, values for K typically range from 0.6 to 0.8 MPa, but can be as
low as 0.5 or as high as 0.9 for normal strength concrete. Because
of the possible wide range of values for K, estimated correlations are
not advised for the design of large projects. However, once established,
the correlation for a particular mix can be quite stable.(21)
Kosmatka
presented an example of a flexural strength versus compressive strength
relationship compiled by Walker, Stanton, and Bloem in 1956.(21)
This relationship is presented in figure 13. This chart (compiled
from data for various aggregate combinations) demonstrates the range associated
with making correlations from compressive to flexural strength.
(Note: Figure 13 is presented in both English and metric units.)
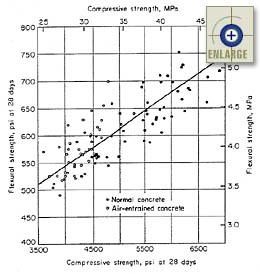 |
|
Figure
13. Relationship between flexural and compressive strength for
various aggregate combinations.(21)
|
Darter
presented the results of a 1962 study conducted by the Bureau of Public
Roads in which a relationship between flexural strength and modulus of
elasticity was developed.(8)
This relationship is presented as equation 5. (Note: Equation 5
was developed in English units.)
Ec
= 14.4 w1.5
S0.77
(5)
where
Ec
= Static modulus of elasticity of concrete, psi.
w =
Air dry weight of concrete at time of test, pcf.
S =
Flexural strength (modulus of rupture), psi.
The same Bureau of
Public Roads report also produced a relationship between indirect splitting
tensile strength and compressive strength. This relationship is
presented as equation 6. (Note: Equation 6 was developed in English
units.)
T =
1.37 (fc)0.69
(6)
where
T =
Indirect tensile strength, psi.
fc
= Compressive strength of concrete at time of test, psi.
A
1995 research work plan from Virginia was to focus on determining relationships
between compressive strength, tensile strength, flexural strength, and
wave propagation.(22)
The developed relationships were then to be verified by field testing
on construction projects using the same concrete mixtures evaluated in
the laboratory. This study was being conducted with the ultimate
goal of collecting enough data to develop a performance-related specification
for Virginia.
|