Appendix A—Proposed Revisions To The AASHTO Standard Specifications For Transportation Materials And Methods Of Sampling And Testing, Part I Specifications
PROPOSED CHANGE TO AASHTO Standard Specifications for Transportation Materials |
(X) Revision or ( ) Addition M 6 |
M 6 Standard Specification for Fine Aggregate for Portland Cement Concrete
Revise title to read as follows:
Standard Specification for Fine Aggregate for Hydraulic Cement Concrete |
Other Affected Specifications or Sections |
Referenced Documents section in other AASHTO specifications or test methods will need to be changed. |
Background |
Most HPC contains pozzolans or slag; therefore, the word "hydraulic" is more appropriate. |
Anticipated Effect on Bridges |
Introduce correct terminology.
|
References |
None
(Submitted by: ) |
PROPOSED CHANGE TO AASHTO Standard Specifications for Transportation Materials |
(X) Revision or ( ) Addition M 80 |
M 80 Standard Specification for Coarse Aggregate for Portland Cement Concrete
Revise title to read as follows:
Standard Specification for Coarse Aggregate for Hydraulic Cement Concrete
|
Other Affected Specifications or Sections |
Referenced Documents section in other AASHTO specifications or test methods will need to be changed. |
Background |
Most HPC contains pozzolans or slag; therefore, the word "hydraulic" is more appropriate. |
Anticipated Effect on Bridges |
Introduce correct terminology.
|
References |
None
(Submitted by: ) |
PROPOSED CHANGE TO AASHTO Standard Specifications for Transportation Materials |
(X) Revision or (X) Addition M 6 and M 80 |
M 6 Standard Specification for Fine Aggregate for Portland Cement Concrete
M 80 Standard Specification for Coarse Aggregate for Portland Cement Concrete
Item No. 1
Add the following to Section 6.2 of M 80:
Coarse aggregate for use in concrete that will be subject to wetting, extended exposure to humid atmosphere, or contact with moist ground shall not contain any materials that are deleteriously reactive with the alkalies in the cement in an amount sufficient to cause excessive expansion of mortar or concrete, except that if such materials are present in injurious amounts, the coarse aggregate may be used with a cement containing less than 0.6 percent alkalies calculated as sodium oxide equivalent or with the addition of a material that has been shown to prevent harmful expansion due to the alkali-aggregate reaction (Note X). (See Appendix A1 and Supplementary Requirement S1).
Note X—In some areas with highly reactive aggregates, the 0.6 percent limit on alkalies may not be sufficient and a lower alkali content may be needed.
Item No. 2
Replace the Supplementary Requirement S1 of M 6 and add a new Supplementary Requirement to M 80 as follows:
S1 Reactive Aggregate
S1.1 Potential reactivity of siliceous aggregates: Alkali-silica reactions shall be mitigated either by a performance specification as given in S1.1.1 or a prescriptive specification as given in S1.1.2:
S1.1.1 Performance Type:
One of the following options shall be used:
- Obtain a service record of the aggregate with similar cementitious materials having similar alkali content. If satisfactory, no mitigation is necessary.
- Test the aggregate in accordance with AASHTO T 303 or ASTM C 1293. If the expansion is less than 0.10 percent at 14 days after initial reading when tested in accordance with AASHTO T 303 or less than 0.04 percent at one year with ASTM C 1293, no mitigation is necessary.
- If reactive aggregates are used, use pozzolan or slag, and test in accordance with ASTM C 441 to determine if the amount of pozzolan or slag is effective in mitigating deleterious reactions. For acceptance, the maximum expansion at 14 days shall not exceed 0.02 percent and at 56 days shall not exceed 0.10 percent.1 If specified, AASHTO T 303 test shall be used with the pozzolan or slag or blended cements to detect the potential for deleterious expansion. The test shall be performed by using 440 grams of the proposed blended cementitious materials, in the proportion to be used on the project, and 990 grams of the combined aggregates, in the proportions to be used on the project.
For acceptance using AASHTO T 303, the expansion shall not exceed 0.10 percent at 14 days.
S1.1.2 Prescriptive Type:
One of the following options shall be used:
- Limit the alkali content of cement to a maximum of 0.6 percent or limit the alkali content in portland cement concrete to 2.37 kg per cubic meter (4 lb per cubic yard).2,3
- Select aggregates with proven field performance when similar cementitious materials having similar alkali content are used.
- Use varying percentage of pozzolan or slag for different levels of alkali content of cement (Note Y).1
Note Y—Virginia Department of Transportation accepts the following combinations of cementitious materials for different alkali contents:
Combination of Cementitious Materials* |
Max. Cement Alkali, percent |
Cement only
Cement with minimum 15% Class F fly ash
Cement with minimum 20% Class F fly ash
Cement with minimum 25% Class F fly ash
Cement with minimum 30% Class F fly ash
Cement with minimum 25% slag
Cement with minimum 35% slag
Cement with minimum 50% slag
Cement with minimum 3% silica fume
Cement with minimum 7% silica fume
Cement with minimum 10% silica fume |
0.45
0.60
0.68
0.75
0.83
0.60
0.90
1.00
0.60
0.90
1.00 |
* Percentages of Class F fly ash, slag, and silica fume are based on the total amount of cementitious materials.
- lithium salts at a dosage rate of 1:1 LiOH.H2O : equivalent Na2O in the portland cement.3
____________________
1 Lane, D. S. and Ozyildirim, C., "Preventive Measures for Alkali-Silica Reactions (Binary and Ternary Systems)," Cement and Concrete Research, Vol. 29, 1999, pp. 1281-1288.
2 Guide Specification for Concrete Subject to Alkali-Silica Reactions, IS415, Portland Cement Association, September 1998, 8 pp.
3 Stark, D., "Alkali-Silica Reactions in Concrete," Significance of Tests and Properties of Concrete and Concrete-Making Materials, ASTM STP 169C, 1994, pp. 365-371.
Item No. 3
Add to Section 2. Referenced Documents in M 6 and M 80 as follows:
2.1 AASHTO Standards:
T 303 Accelerated Detection of Potentially Deleterious Expansion of Mortar Bars Due to Alkali-Silica Reaction
2.2 ASTM Standards:
C 441 Effectiveness of Mineral Admixtures or Ground Blast-Furnace Slag in Preventing Excessive Expansion of Concrete Due to Alkali-Silica Reaction
C 1293 Determination of Length Change of Concrete Due to Alkali-Silica Reaction |
Other Affected Specifications or Sections |
M 6 and M 80 |
Background |
Item Nos. 1 and 2
Supplementary requirement S1.1 of M 6 and Section 6.2 of M 80 indicate that cements with an upper limit of 0.6 percent alkalies can be used to inhibit alkali-silica reaction (ASR) when reactive aggregate is used. Generally, ASR can be controlled by using low alkali cement (less than 0.6 percent), a sufficient amount of an effective pozzolan, slag, blended cement, or lithium salts.(1,2,3) Tests can indicate the potentially deleterious aggregates and a lower alkali content than 0.6 percent may be needed in some areas. However, even if test results indicate potential expansions, an aggregate with a satisfactory service record with similar cementitious materials and conditions can be used.
Item No. 3
Updating referenced documents. |
Anticipated Effect on Bridges |
More durable structures when reactive aggregates are used. |
References |
- Lane, D. S. and Ozyildirim, H. C., "Evaluation of the Effect of Portland Cement Alkali Content, Fly Ash, Ground Slag, and Silica Fume on Alkali-Silica Reactivity," Cement, Concrete, and Aggregates, Vol. 21, No. 2, December 1999, pp. 22-36.
- ACI Committee 221, "State-of-the-Art Report on Alkali-Aggregate Reactivity (ACI 221.1R)," American Concrete Institute, Farmington Hills, MI, 1998.
- Standard Practice to Identify Degree of Alkali-Reactivity of Aggregates and to Identify Measures to Avoid Deleterious Expansion in Concrete, A23.2-27A, Canadian Standards Association, Rexdale, ONT, September 2001.
(Submitted by: ) |
PROPOSED CHANGE TO AASHTO Standard Specifications for Transportation Materials |
(X) Revision or (X) Addition M 85 |
M 85 Standard Specification for Portland Cement
Add the following to footnote d of Table 2—Optional Chemical Requirements:
In some areas with highly reactive aggregates, the 0.6 percent limit on alkalies may not be sufficient and a lower alkali content may be needed. |
Other Affected Specifications or Sections |
None |
Background |
Alkali content may need to be lower in some areas to mitigate ASR.(1) M6 or M80 provide other options as well. |
Anticipated Effect on Bridges |
More durable structures when reactive aggregates are used. |
References |
- Stark, D., "Alkali-Silica Reactions in Concrete," Significance of Tests and Properties of Concrete and Concrete-Making Materials, ASTM STP 169C, 1994, pp. 365-371.
(Submitted by: ) |
PROPOSED CHANGE TO AASHTO Standard Specifications for Transportation Materials |
(X) Revision or (X) Addition M 154 |
M 154 Standard Specification for Air-Entraining Admixtures for Concrete
Item No. 1
Revise Section 8. Test Methods as follows:
8.1 Determine the properties enumerated in Section 6 in accordance with Test Method C 233.
It is recommended that, whenever practicable, tests be made in accordance with the section on Materials for Tests for Specific Uses in Test Method C 233, using the cementitious materials proposed for the specific work.
Item No. 2
Add to Table—1 Physical Requirements as follows:
Compressive strength, min, % of control: |
1 day |
90 |
3 days |
90 |
7 days |
90 |
28 days |
90 |
56 daysB |
90 |
Flexural strength, min, % of control: |
|
3 days |
90 |
7 days |
90 |
28 days |
90 |
56 daysB |
90 |
B Applicable only when required by the purchaser |
Other Affected Specifications or Sections |
None |
Background |
Item No. 1
Most HPC contains pozzolans or slag. The effectiveness of air-entraining admixtures is affected by the use of pozzolans or slag. Consequently, all cementitious materials proposed for the specific work should be included.
Item No. 2
56 days is a common test age and is used in the FHWA definition of HPC.(1) |
Anticipated Effect on Bridges |
Item No. 1
Makes the test more representative of the field conditions.
Item No. 2
More economical concrete with improved properties and more realistic test age for HPC. |
References |
- Goodspeed, C. H., Vanikar, S., and Cook, R., "High Performance Concrete Defined for Highway Structures," Concrete International, Vol. 18, No. 2, February 1996, pp. 62-67.
(Submitted by: ) |
PROPOSED CHANGE TO AASHTO Standard Specifications for Transportation Materials |
(X) Revision or (X) Addition M 157 |
M 157 Standard Specification for Ready-Mixed Concrete
Item No. 1
Add to Section 2. Referenced Documents as follows:
2.1 AASHTO Standards:
M 302, Ground Granulated Blast-Furnace Slag for Use in Concrete and Mortars
M 307, Microsilica for Use in Concrete and Mortar
M XX1, Combined Aggregates for Hydraulic Cement Concrete
2.2 ASTM Standards:
C 1157 Hydraulic Cement
Item No. 2
Revise Section 3.1 as follows:
3.1 For the purpose of this specification, ready-mixed concrete is hydraulic cement concrete manufactured for delivery to a purchaser in a plastic state and delivered as hereinafter specified.
Item No. 3
Add ASTM C 1157 to Section 4.1.1 as follows :
4.1.1 Cement—Cement shall conform to Specification M 85 for Portland Cement or M 240 for Blended Hydraulic Cement, or ASTM C 1157 for Hydraulic Cement.
Item No. 4
4.1.2 Other Cementitious Materials—Cementitious materials other than cement shall meet the requirements of the following specifications unless specified otherwise by the purchaser:
Fly Ash—M 295
Ground Granulated Blast-Furnace Slag—M 302
Silica Fume—M 307
Item No. 5
Add the following at the end of Section 4.1.3 Aggregates:
Combined aggregate grading, if used, shall conform to Specification M XX1.
Item No. 6
Revise Section 5.1 as follows:
The mix design may be specified by the engineer or submitted to the engineer by the Contractor for approval or a performance-based specification may be used. When specified by the engineer, it shall include the following:
Item No. 7
Add new Section 5.3 as follows:
5.3 Performance-based Specification—Mix design shall be prepared and specified by those familiar with the material. The engineer shall specify the desired hardened concrete properties and permit the Contractor to design the mixture. Contractor will demonstrate through trial mixtures that the mix designs will provide the specified fresh and hardened properties. Selection of slump for placement shall be the responsibility of the Contractor. The Contractor shall make trial placements to demonstrate that concrete can be placed without any segregation, and without any difficulty in consolidating and finishing.
Item No. 8
Revise Sections 5.1.1 and 5.1.3 as follows:
5.1.1 Cementitious materials content in kg/m3 (lb/yd3) of concrete.
5.1.3 Maximum water-cementitious materials ratio, where water includes surface moisture, but excludes water of absorption of the aggregates.
Item No. 9
Revise Section 7.2 as follows:
7.2 The air-content of air-entrained concrete when sampled from the transportation unit at the point of placement shall be within the purchaser specified tolerances. Where it is not practical to test at this point, comparison of values measured at the point of placement and the nearest practical location shall be established.
Item No. 10
Add a note to Section 11.3.1 as follows:
Note X—HPC mixtures especially those with stiff consistency having high cementitious materials content, low water-cementitious materials ratio, and several admixtures may need longer mixing times and higher number of revolutions for thorough mixing.
Item No. 11
Revise Section 15.2 as follows:
15.2 If the measured slump, air content, or unit weight falls outside the specified limits, a check test shall be made immediately on another portion of the same sample. In the event of a second failure, the concrete shall be considered to have failed the requirements of the specification. Unit weight shall be required for lightweight concretes, and is recommended for normal weight concretes.
|
Other Affected Specifications or Sections |
None |
Background |
Item No. 1
Additional documents need to be added as described below.
Item No. 2
Pozzolans and slag are widely used in HPC.(1) The specification needs to encompass all hydraulic cements.
Item No. 3
ASTM C 1157 is a standard performance specification for hydraulic cement. Performance specifications are desirable to promote innovation and encourage more economical construction.
Item No. 4
Slag and silica fume are widely used in concrete and need to be included.(1)
Item No. 5
Combined aggregate grading is a proposed specification and should be included.
Item Nos. 6 and 7
Performance-based specifications permit innovation and utilization of new products.
Use of admixtures has a large effect on the slump of concrete. The Contractor should be responsible for the selection of slump. With the use of admixtures, slump can be easily adjusted to meet the needs of the project without affecting the water content.
Item No. 8
Cement is replaced by cementitious materials since pozzolans and slag are widely used in HPC. Bags or sacks are not the proper measures.
Item No. 9
Concrete in place is of interest. Delivery equipment such as a pump may alter the air-void system making the concrete less resistant to cycles of freezing and thawing.
Item No. 10
HPC may contain different cementitious materials, high cementitious materials content, and more than one admixture. The mixture may be very cohesive. Longer mixing times may be appropriate to produce a uniform and consistent product.
Item No. 11
Unit weight is a very useful test to check the air-content of the mixture. In lightweight concrete, unit weight is an important design criterion. |
Anticipated Effect on Bridges |
Improved concrete in bridge structures.
|
References |
- High Performance Concrete, Compact Disc, Federal Highway Administration, Version 3.0, February 2003.
(Submitted by: ) |
PROPOSED CHANGE TO AASHTO Standard Specifications for Transportation Materials |
(X) Revision or (X) Addition M 182 |
M 182 Standard Specification for Burlap Cloth Made from Jute or Kenaf
Item No. 1
Revise the title as follows:
M 182 Standard Specification for Burlap Cloth Made from Jute or Kenaf, and Cotton Mats
Item No. 2
Revise Section 1.1 as follows:
1.1 Scope—This specification covers requirements for burlap made from jute or kenaf, and cotton mats for use in curing concrete.
Item No. 3
Add a new Section 1.4 as follows:
1.4 Cotton—Cotton is a vegetable fiber harvested from the cotton plant. The cotton plant belongs to the genus Gossypium of the family Malvaceae.
Renumber existing Section 1.4 as 1.5.
Item No. 4
Add a new Section 2.4 as follows:
2.4 Cotton mats shall consist of a filling material of cotton "bat" or "bats" of at least 400 g/m2 (12 oz. per sq. yd.); covered with unsized cloth at a minimum of 200 g/m2 (six (6) oz. per sq. yd); tufted or stitched to maintain stability.
Item No. 5
Revise the first sentences in Sections 3.1 and 3.2 as follows:
3.1 The burlap and cotton mats shall be clean, evenly woven, and shall conform to the quality and product requirements established by this specification.
3.2 The burlap and cotton mats shall be examined visually for defects which would impair its their suitability for use.
Item No. 6
Revise Sections 4.1 and 4.2 as follows:
4.1 Lot —Unless otherwise specified, cloth and cotton mats of the same class presented at one time shall be considered a lot for purposes of inspection and tests.
4.2 Sampling for Test—Unless otherwise specified, random samples of cloth and cotton mats shall be taken from each inspection lot in accordance with the following table.
Item No. 7
Revise Sections 6.1 and 6.2 as follows:
6.1 The burlap cloth and cotton mats shall be packed in a manner acceptable to common carriers for safe transportation to point of destination specified in shipping instructions at the lowest transportation rate for such supplies.
6.2 Each roll or cotton mat shall have a ticket attached to the selvage at the inner end of the cloth or cotton mat giving the length and width, and name and address of the manufacturer.
|
Other Affected Specifications or Sections |
None |
Background |
Cotton mats are used successfully in some states such as Texas and New Hampshire and are very effective for curing HPC bridge decks.(1) |
Anticipated Effect on Bridges |
Improved curing practices that will result in more durable concrete decks with less cracking.
|
References |
- Texas DOT specifications for curing materials for concrete.
(Submitted by: ) |
PROPOSED CHANGE TO AASHTO Standard Specifications for Transportation Materials |
(X) Revision or (X) Addition M 194 |
M 194 Standard Specification for Chemical Admixtures for Concrete
Item No. 1
Revise Section 1.1 as follows:
This specification covers materials for use as chemical admixtures to be added to hydraulic cement concrete mixtures in the field for the purpose or purposes indicated for the seven types as follows:
Item No. 2
In Table 1 Physical Requirements, for compressive strength and flexural strength, add a new line for 56 days with the same requirements as listed currently for 28 days.
|
Other Affected Specifications or Sections |
None |
Background |
Item No. 1
It is very common to use other cementitious materials with portland cements.(1) Consequently, the term hydraulic cement concrete should be used.
Item No. 2
Test age of 56 days is common for HPC and is used in the FHWA definition of HPC.(1) |
Anticipated Effect on Bridges |
More economical concrete with improved properties.
|
References |
- Goodspeed, C. H., Vanikar, S., and Cook R. A. "High Performance Concrete Defined for Highway Structures," Concrete International, Vol. 18, No. 2, February 1996, pp. 62-67.
(Submitted by: ) |
PROPOSED CHANGE TO AASHTO Standard Specifications for Transportation Materials |
(X) Revision or (X) Addition M 195 |
M 195 Standard Specification for Lightweight Aggregates for Structural Concrete
Item No. 1
Add to Section 2. Referenced Documents as follows:
2.1 AASHTO Standards:
M XX1 Combined Aggregates for Hydraulic Cement Concrete
Item No. 2
Revise Section 5.1.2 to read as follows:
5.1.2 Grading—The grading shall conform to the requirements shown in Table 1 or the requirements of M XX1.
|
Other Affected Specifications or Sections |
M XX1 |
Background |
Item No. 1
A new Standard Specification for Combined Aggregates for Hydraulic Cement Concrete has been proposed and is identified as M XX1.
Item No. 2
The new specification needs to be referenced in M 195. |
Anticipated Effect on Bridges |
Improved workability and hardened concrete properties.
|
References |
None
(Submitted by: ) |
PROPOSED CHANGE TO AASHTO Standard Specifications for Transportation Materials |
(X) Revision or (X) Addition M 205 |
M 205 Standard Specification for Molds for Forming Concrete Test Cylinders Vertically
Item No. 1
Revise Section 5.1 as follows:
5.1 Single-use molds may be made of sheet metal, plastic, or other materials and must conform to the requirements of this specification. Paper molds shall not be used.
Item No. 2
Renumber existing Section 5.5.3 as 5.5.4 and add a new Section 5.5.3 as follows:
5.5.3 Top Cap—Sheet metal or plastic molds for use with concrete having a specified compressive strength greater than 6000 psi (40 MPa) shall be provided with tightly fitting domed metal or domed plastic caps to maintain the circular shape at the top of the cylinder and to provide a clearance above the finished concrete surface.
|
Other Affected Specifications or Sections |
None |
Background |
Item No. 1
High-quality paper molds have been shown to result in measured concrete compressive strengths about 13 percent lower than when steel molds are used.(1)
Item No. 2
Sheet metal and plastic molds with thin walls have a tendency to become out of round. Consequently, it is recommended that caps be required to retain the roundness. Dome caps ensure that the concrete surface is not deformed.(2) |
Anticipated Effect on Bridges |
Improved quality control.
|
References |
- Blick, R. L., "Some Factors Influencing High-Strength Concrete," Modern Concrete, Vol. 36, No. 12, April 1973, pp. 38-41.
- ACI Committee 363, "Guide to Quality Control and Testing of High-Strength Concrete, (ACI 363.2R-98)" American Concrete Institute, Farmington Hills, MI, 1998.
(Submitted by: ) |
PROPOSED CHANGE TO AASHTO Standard Specifications for Transportation Materials |
(X) Revision or (X) Addition M 240 |
M 240 Standard Specification for Blended Hydraulic Cement
Item No. 1
Add to Table 2—Physical Requirements as follows:
Compressive strength, min, MPa (psi)
28 or 56a days
Heat of Hydration
28 or 56 a days
a Only applicable when testing at 56 days is specified.
Item No. 2
Revise Table 3—Requirements for Pozzolan for Use in Blended Cements and for Slag for Use in Slag-Modified Portland Cements as follows:
Slag or pozzolan activity index: with portland cement, at 28 or 56a days, min. percent.
a Only applicable when testing at 56 days is specified.
|
Other Affected Specifications or Sections |
None |
Background |
Item Nos. 1 and 2
Test age of 56 days is common and used in the FHWA definition of HPC.(1) |
Anticipated Effect on Bridges |
Item Nos. 1 and 2
More economical construction. |
References |
- Goodspeed, C. H., Vanikar, S., and Cook, R., "High Performance Concrete Defined for Highway Structures," Concrete International, Vol. 18, No. 2, February 1996, pp. 62-67.
(Submitted by: ) |
PROPOSED CHANGE TO AASHTO Standard Specifications for Transportation Materials |
(X) Revision or (X) Addition M 241 |
M 241 Standard Specification for Concrete Made By Volumetric Batching and Continuous Mixing
Item No. 1
In Section 2. Referenced Documents, correct the titles of 211.1 and 211.2 and add M 307, C 1157, and 211.4R as follows:
211.1 Standard Practice for Selecting Proportions for Normal, Heavyweight, and Mass Concrete
211.2 Standard Practice for Selecting Proportions for Structural Lightweight Concrete
M 307 Microsilica for Use in Concrete and Mortar
C 1157 Blended Hydraulic Cement
211.4R Guide for Selecting Proportions for High-Strength Concrete with Portland Cement and Fly Ash
Item No. 2
Revise first sentence of Section 5.1.1 as follows:
5.1.1 Cement—Cement shall conform to Specification C 150, Specification C 595, or Specification C 1157 (Note 2).
Item No. 3
Renumber Sections 5.1.6 and 5.1.7 as 5.1.7 and 5.1.8, respectively.
Add new Section 5.1.6 as follows:
5.1.6 Silica Fume—Silica fume shall conform to Specification M 307.
Item No. 4
Add to Section 6.1.3 the definition of point of discharge as follows:
6.1.3 When air-entrained concrete is specified, the air content of samples taken at the point of placement from the transportation unit (see Section 10 and Table 3 for the total air content and tolerances) (Note 5). Point of placement is at the final location of the concrete. Where it is not practical to test at this point, comparison of values measured at the point of placement and the nearest practical location shall be established.
Item No. 5
Add the following to Section 6.1.5 about ordering:
6.1.5 Which of Options A, B, or C shall be used as a basis for determining the proportions of the concrete to produce the required quality (see 6.2, 6.3, or 6.4). Option B shall not be used with performance-based specifications.
Item No. 6
Revise the second sentence of Note 7 as follows:
Note 7—The purchaser, in selecting requirements for which he assumes responsibility should give consideration to requirements for workability, placeability, durability, surface texture, and density, in addition to those for structural design. The purchaser is referred to ACI Standard Practice 211.1 for normal weight concrete, ACI Standard Practice 211.2 for lightweight concrete, and ACI Guide 211.4R for high-strength concrete with fly ash, for the selection of proportions that will result in concrete suitable for various types of structures and conditions of exposure. The water-cement ratio of most structural lightweight concretes cannot be determined with sufficient accuracy for use as a specification basis.
Item No. 7
Revise the last sentence of Note 8 as follows:
Attention is directed to ACI Publications 211.1, 211.2, and 211.4R for additional information on mixture proportions.
Item No 8
Add to Note 15 and revise title and footnote C of Table 4 Overdesign Necessary to Meet Strength Requirements as follows:
Note 15—Due to variations in materials, operations, and testing the average strength necessary to meet these requirements will be substantially higher than the specified strength. The amount higher depends upon the standard deviation of the test results and the accuracy with which that value can be estimated from prior data as explained in ACI 318 and ACI 301. Pertinent data is given in Table 4 for specified strengths up to 5000 psi (35 MPa) and Table 5 for specified strengths greater than 5000 psi (35 MPa).
C If less than 15 prior tests are available, the overdesign should be 1000 psi (7.0 MPa) for specified strength less than 3000 psi (20 MPa) and 1200 psi (8.5 MPa) for specified strengths from 3000 to 5000 psi (20 to 35 MPa).
Table 5 Required Average Strength to Meet Strength Requirements for fc' > 5000 psi (35 MPa)
Number of TestsA |
Required Average Compressive Strength |
Less than 15 |
1.10 fc' + 700 in psi
(1.10 fc' + 5.0 in MPa) |
15 or more |
Use the larger value computed by
M(fc' +1.34s)
M(0.90 fc' + 2.33s) |
where
fc' = specified compressive strength
M = modification factor given in Table 6
A Number of tests of a concrete mixture used to estimate the standard deviation of a concrete production facility. The mixture used must have a strength within 1000 psi (7 MPa) of that specified and be made with similar materials. See ACI 318.
Table 6 Modification Factors
Number of Tests |
M |
15
20
25
30 or more |
1.16
1.08
1.03
1.00 |
For intermediate number of tests, use linear interpolation.
Revise title of Table 4 as follows:
Table 4 Overdesign Necessary to Meet Strength Requirements for fc' £ 5000 psi (35 MPa) A
Item No 9
Revise Section 11.2 as follows:
11.2 One strength test set of at least two or at least three cylinders as described in Section 11.3 and the accompanying slump, temperature, and air content tests shall be made for each 25 yd3 (19 m3) of concrete or fraction thereof, or whenever significant changes have been made in the proportioning controls. There shall be at least one strength test made for each class of concrete placed in 1 day.
Item No. 10
Revise Section 11.3 as follows:
11.3 For each strength test, at least two standard 6x12-in. (150x300-mm) cylinders or at least three 4x8-in. (100x200-mm) cylinders shall be made (see 14.2.2). A minimum of three cylinders shall be used for each strength when the specified strength exceeds 5000 psi (35 MPa). The test result shall be the average strength of the test cylinders, except that, if any specimen shows definite evidence other than low strength, of improper sampling, molding, handling, curing, or testing, it shall be discarded and the strength of the remaining cylinder(s) shall then be considered the test result.
Item No. 11
Revise Section 11.5.2 as follows:
11.5.2 No individual strength test shall be more than 500 psi (3.4 MPa) below the specified strength fc' when fc' is less than or equal to 5000 psi (35 MPa); or by more than 0.10 fc' when fc' is greater than 5000 psi (35 MPa). |
Other Affected Specifications or Sections |
None |
Background |
Item No. 1
Existing documents need to be revised and new documents added.
Item No. 2
ASTM C 1157 is a performance specification for blended hydraulic cement. Since performance-based specifications are encouraged for HPC, it needs to be added.
Item No. 3
Silica fume is widely used in transportation facilities and needs to be included.
Item No. 4
Delivery equipment may affect the air-void system. For example, air content of the concrete may change as a result of pumping.(1)
Item No. 5
In the performance-based specifications, the producer and the contractor should take the responsibility for proportioning the mixtures. Purchaser should state the required properties.
Item No. 6
ACI now has a document for proportioning high-strength concrete with fly ash.
Item No. 7
ACI has changed the titles of its documents.
Item No. 8
ACI 318 has proposed revisions that are more applicable to high-strength concrete.(2) The proposed changes are consistent with those proposed for ACI 318.
Item No. 9
Research has shown that the smaller size cylinders have greater variability. Hence, three 100x200‑mm (4x8-in) cylinders are needed for the same precision.
Item No. 10
4x8-in cylinders are commonly used and may exhibit higher variability.(3) For HSC, strength is more critical, and at least three cylinders are recommended for any size.
Item No. 11
Proposed changes are more applicable to high-strength concrete and are needed to be consistent with proposed revisions for overdesign.(2) |
Anticipated Effect on Bridges |
Improved quality of concrete.
|
References |
- ACI Committee 304, Placing Concrete by Pumping Methods, American Concrete Institute, Farmington Hills, MI, 1996.
- Cagley, J. R., "Changing from ACI-318-99 to ACI 318-02 What's New?" Concrete International, Vol. 23, No. 6, June 2001, pp. 69-184.
- Ozyildirim, C., "4 x 8 inch Concrete Cylinders versus 6 x 12 inch Cylinders," VHTRC 84‑R44, Virginia Transportation Research Council, Charlottesville, VA, May 1984, 25 pp.
(Submitted by: ) |
PROPOSED CHANGE TO AASHTO Standard Specifications for Transportation Materials |
(X) Revision or (X) Addition M 295 |
M 295 Standard Specification for Coal Fly Ash and Raw or Calcined Natural Pozzolan for Use as a Mineral Admixture in Concrete
Item No. 1
Delete Table 2—Supplementary Optional Chemical Requirement and renumber subsequent tables.
Item No. 2
Revise Table 3—Physical Requirements as follows:
Strength activity index:
With portland cement, at 28 or 56 days, min, percent of control 75 75 75
|
Other Affected Specifications or Sections |
None |
Background |
Item No. 1
Performance based approach is preferred. Also, the available alkali limit of 1.5 percent in table 2 does not provide protection in all cases.(1)
Item No. 2
Test age of 56 days is commonly used and is used in the FHWA definition of HPC.(2) |
Anticipated Effect on Bridges |
Item No. 1
More durable concrete.
Item No. 2
More cost effective. |
References |
- Snow, P. G., "Effect of Fly Ash on Alkali-Silica Reactivity in Concrete," Transportation Research Record 1301, Transportation Research Board, 1991, pp. 149-154.
- Goodspeed, C. H., Vanikar, S., and Cook, R., "High Performance Concrete Defined for Highway Structures," Concrete International, Vol. 18, No. 2, February 1996, pp. 62-67.
(Submitted by: ) |
PROPOSED CHANGE TO AASHTO Standard Specifications for Transportation Materials |
(X) Revision or (X) Addition M 302 |
M 302 Standard Specification for Ground Granulated Blast-Furnace Slag for Use in Concrete and Mortars
Item No. 1
Revise Table—Physical Requirements as follows:
28- or 56-day Index.
Item No. 2
Add the following sentence to Section A3.2:
Further information on preventing excessive expansion due to alkali-silica reaction is given in M 6 and M 80.
Item No. 3
Add the following to Appendix A:
A4. Shrinkage
When slag is added, the increase in shrinkage of mortar bars over control shall not exceed 0.03 percent.
Item No. 4
Add the following footnote to Section 2 Reference Documents:
M 6, Fine Aggregate for Portland Cement Concrete
M 80, Coarse Aggregate for Portland Cement Concrete
|
Other Affected Specifications or Sections |
None |
Background |
Item No. 1
56 days is a common age for HPC and is used in the FHWA definition of HPC.(1)
Item No. 2
See proposed revisions to M 6 and M 80.
Item No. 3
Shrinkage is important information and is included in M 295 for fly ash specification. For consistency, it should be included in this specification too. The value 0.03 percent used in AASHTO M 295 may need to be changed considering the low shrinkage and variability in HPC.
Item No. 4
Additional documents need to be added as described above. |
Anticipated Effect on Bridges |
Item No. 1
More economical.
Item Nos. 2 and 3
More durable concrete with less cracking.
Item No. 4
None. |
References |
- Goodspeed, C. H., Vanikar, S., and Cook, R., "High Performance Concrete Defined for Highway Structures," Concrete International, Vol. 18, No. 2, February 1996, pp. 62-67.
(Submitted by: ) |
PROPOSED CHANGE TO AASHTO Standard Specifications for Transportation Materials |
(X) Revision or (X) Addition M 307 |
M 307 Standard Specification for Microsilica for Use in Concrete and Mortar
Item No. 1
Replace "microsilica" with "silica fume" in the title and throughout the document.
Item No. 2
In Section 1.1, delete the third sentence that reads
Item No. 3
Delete Sections 3.2 Microsilica and 3.2.1 Silica Fume and replace with:
3.2 Silica Fume—very fine pozzolanic material, composed mostly of amorphous silica, produced by electric arc furnaces as a byproduct of the production of elemental silicon or ferro-silicon alloys (also known as condensed silica fume and microsilica).
Item No. 4
Delete the available alkalies requirement in Table 2—Optional Chemical Requirements.
Item No. 5
Revise Table 3—Physical Requirements as follows:
Strength Activity Index:
With portland cement, determine at 7, 28, and 56 days, min, percent of control 100
Oversize:
Percent retained on No. 325 sieve (45 m m), max, percent 10
Specific surface, min, m2/g 15
Item No. 6
Delete the drying shrinkage requirement from Table 4—Optional Physical Requirements.
Item No. 7
Add to Table 4 the following:
Bulk density, max, kg/m3 7 20
Item No. 8
Revise Section 8.2.4 as follows:
8.2.4 Strength Activity Index with Portland Cement, ASTM C 311, except use 225g of portland cement, 25 g of silica fume, and 687.5 g of graded Ottawa sand in the test mixture. The water-cementitious materials ratio shall be the same in the test and control mixtures. Also, a set of samples shall be evaluated at both 7 days and 28 days, and at 56 days if specified.
|
Other Affected Specifications or Sections |
None |
Background |
Item No. 1
Silica fume is the common terminology used by ASTM, ACI, and the industry. The association for the manufacturers is known as the Silica Fume Association.
Item No. 2
In transportation structures, silica fume is mainly used in the dry densified form.
Item No 3
Use standard definition for silica fume per ASTM 1240.(1)
Item No. 4
Table 4 has a performance requirement on reactivity with cement alkalies. Performance-based requirements are desired.
Item No. 5
56 days is common and is used in the FHWA definition of HPC.(2)
The density uniformity is deleted since it is not a meaningful test for silica fume. Silica fume density has very little variation.
Oversize material should be limited since it may contain contaminating material such as wood, quartz, and coal.
Specific surface limit ensures that very fine particles of silica fume are present.
Item No. 6
Drying shrinkage requirement is not applicable to silica fume, which is so fine and requires a large amount of water unless it is compensated with the use of high-range water-reducing admixtures.
Item No. 7
Bulk density indicates the extent of densification. The large agglomerates in densified silica fume may cause difficulty in obtaining good dispersion of the silica fume particles. If they do not disperse well, the desired properties are not achieved and in some cases agglomerates may act as highly reactive siliceous particles leading to disruptive ASR.(3)
Item No. 8
ASTM C 311 requires the addition of water for a constant flow in the test and control mixtures. Addition of silica fume increases the water demand; however, normal practice is to add a high-range water-reducing admixture to compensate for the demand and to better disperse the silica fume particles.
56 days is a common test age and is used in the FHWA definition of HPC.(2) |
Anticipated Effect on Bridges |
Item No. 1
More consistent terminology.
Item No. 2
Deletes an incorrect statement.
Item No. 3
More consistent definition.
Item No. 4
Avoids the prescriptive approach.
Item No. 5
More consistent concrete.
Item No. 6
Avoids an incorrect procedure.
Item No. 7
Improved quality of concrete.
Item No. 8
More consistent test procedure. |
References |
- ASTM 1240 Use of Silica Fume as a Mineral Admixture in Hydraulic Cement Concrete, Mortar, and Grout.
- Goodspeed, C. H., Vanikar, S., and Cook, R., "High Performance Concrete Defined for Highway Structures," Concrete International, Vol. 18, No. 2, February 1996, pp. 62-67.
- Marusin, S. L. and Shotwell, L. B., "Alkali-Silica Reaction in Concrete Caused by Densified Silica Fume Lumps," Cement, Concrete, and Aggregates, Vol. 22, Number 2, December 2000, pp. 90-94.
(Submitted by: ) |
PROPOSED CHANGE TO AASHTO Standard Specifications For Transportation Materials |
( ) Revision or (X) Addition M XX1 (Combined Aggregate) |
M XX1 Standard Specifications for Combined Aggregates for Hydraulic Cement Concrete
A new specification for combined aggregates is proposed and attached. |
Other Affected Specifications or Sections |
None |
Background |
In concrete, especially HPC, the combined grading of the aggregates is important. The goal of a combined aggregate grading is to improve the workability of concrete at given water and paste contents or to minimize the water and paste contents for a given workability or to improve both the workability and hardened properties of the concrete.
Concrete is a two-component system made of aggregates and paste. For improved durability, concrete with the least amount water and of paste is needed. This is possible with the use of well-graded aggregates composed of fine and coarse particles.
One of the SHRP products is the Packing Handbook (SHRP Product #2005). In the related SHRP report SHRP-C-334, the importance of combined grading is emphasized.(1) This report presented tables based on computer models for the theoretical packing of spherical particles for optimal grading. However, a study by Purdue University concluded that mixtures designed using the packing handbook were harsh and would achieve little or no cost reductions or quality improvements if implemented for field use.(2) Even though the SHRP Packing Handbook has not received acceptance, other approaches to the optimal grading have been pursued and used as explained below.
Four approaches are included in the combined grading specification and are explained in detail in the appendix.
The first approach uses the fineness modulus that indicates the fineness or the coarseness of the combined materials.
The second approach uses the coarseness factor developed by Shilstone.(3)
The third approach for uniform grading is derived from the asphalt industry. Cumulative percent passing is plotted against the sieve size raised to the power of 0.45. In a semi-logarithmic scale, a straight-line relationship is required. Aggregate grading should follow this line as closely as possible except that the grading falls below the line for small sizes to compensate for the presence of cement particles.(4)
The fourth approach uses a combined grading to achieve uniform distribution of aggregate particle sizes as used in concrete floor slab construction.(5,6) Generally a range for the percentage retained on each sieve size is specified. The goal is to minimize large changes in the percentage retained on consecutive sieves. |
Anticipated Effect on Bridges |
Improved concrete properties and performance.
|
References |
- "A Guide to Determining the Optimal Gradation of Concrete Aggregates," SHRP-C-334 Strategic Highway Research Program, National Research Council, Washington, DC, 1993.
- Cox, K. P., Scholer, C. F., and Cohen, M. D., "An Evaluation of the Strategic Highway Research Project Packing Handbook," Project C-36-65H, Purdue University, West Lafayette, IN, May 1994.
- Shilstone, J. M., Sr., "Concrete Mixture Optimization," Concrete International, Vol. 12, No. 6, June 1990, pp. 33-39.
- Neville, A. M., Properties of Concrete, Fourth Edition, John Wiley and Sons Inc., 1996.
- ACI Committee 302, "Guide for Concrete Floor and Slab Construction, (ACI 302.1R)," American Concrete Institute, Farmington Hills, MI, 1996, 65 pp.
- Keith, F. R., Walker, W. W., and Holland, J. A., "Designing a Durable, Light-Reflective Floor," Concrete International, Vol. 23, No. 7, July 2001, pp. 39-45.
(Submitted by: ) |
Standard Specification for Combined Aggregates for Hydraulic Cement Concrete AASHTO Designation: M XX1
1. SCOPE
1.1. This specification covers the requirements for combined aggregates for hydraulic cement concrete having a nominal maximum aggregate size of 50 mm (2 in.) or less. Fine and coarse aggregate shall be blended to achieve the desired properties. Two approaches are given. One is based on performance and the other on method type.
1.2. The values stated in SI units are to be regarded as the standard.
2. REFERENCED DOCUMENTS
2.1. AASHTO Standards:
M 6 Fine Aggregate for Portland Cement Concrete
M 43 Sizes of Aggregate for Road and Bridge Construction
M 80 Coarse Aggregate for Portland Cement Concrete
M 195 Lightweight Aggregates for Structural Concrete
T 22 Compressive Strength of Cylindrical Concrete Specimens
T 23 Making and Curing Concrete Test Specimens in the Field
T 97 Flexural Strength of Concrete (Using Simple Beam with Third-Point Loading)
T 119 Slump of Hydraulic Cement Concrete
T 126 Making and Curing Concrete Test Specimens in the Laboratory
T 141 Sampling Freshly Mixed Concrete
T 160 Length Change of Hardened Hydraulic Cement Mortar and Concrete
T 198 Splitting Tensile Strength of Cylindrical Concrete Specimens
T 259 Resistance of Concrete to Chloride Ion Penetration
T 277 Electrical Indication of Concrete's Ability to Resist Chloride Ion Penetration
PP 34 Estimating the Crack Tendency of Concrete
2.2. America Concrete Institute:
211.1 Standard Practice for Selecting Proportions for Normal, Heavyweight, and Mass Concrete
211.2 Standard Practice for Selecting Proportions for Structural Lightweight Concrete
3. SIGNIFICANCE AND USE
3.1. The goal of a combined aggregate grading is to improve the workability of concrete at given water and paste contents or to improve the hardened properties by minimizing the amount of the water and paste for a given workability or to improve both the workability and hardened properties of concrete.
3.2. The shape and texture of the aggregate also have a large influence on the water and paste demand. Trial batches shall be made to ensure that desired concrete properties are achieved.
4. GENERAL REQUIREMENTS
4.1. Fine and coarse aggregates used shall comply with the relevant provisions of AASHTO specifications M 6, M 43, M 80, and M 195 for ordering information, grading (M 43 shall be used unless otherwise permitted) based on a nominal maximum size, uniformity of grading, deleterious substances, and, if specified, reactive aggregates.
4.2. Tests for performance characteristics of the concrete shall comply with the relevant specifications and specified AASHTO Test Methods for sampling (T 141), making test specimens (T 23, T 126), slump (T 119), strength (T 22, T 97, T 198), and penetrability (T 259, T 277), shrinkage (T 160), crack tendency (PP 34), or other test methods as specified.
4.3. Proportions of fine and coarse aggregate shall be selected using the performance-based approach of Section 5 or the method-type approach of Section 6.
5. PERFORMANCE-BASED APPROACH
5.1. Contractor shall select the combined aggregate grading and demonstrate with trial batches that the specified properties are achieved (Note 1). It shall be the Contractor's responsibility to ensure that the combined grading provides the specified properties for the project.
Note 1—For proportioning hydraulic cement concrete, the AASHTO Standard Specifications for Highway Bridges, Division II, Article 8.4.1.1 and the AASHTO LRFD Bridge Construction Specifications, Article 8.4.1.1 specify the use of the absolute volume method for normal weight concrete such as described in ACI publication 211.1 and the use of trial mixes for structural lightweight concrete using methods such as described in ACI publication 211.2.
6. METHOD TYPE APPROACH
6.1. One of the following procedures shall be used to determine combined aggregate grading:
6.1.1. Combined fineness modulus
6.1.2. Coarseness factor chart
6.1.3. Power chart
6.1.4. Percent retained on each sieve
Note 2—Details of the procedures in 6.1.1 though 6.1.4 are given in the Appendix.
6.2. The specific combined grading to which the aggregate is to be blended, along with the tolerances for quality control, shall be submitted for approval. Concrete characteristics shall be verified by trial batches to ensure that the specified properties are achieved.
APPENDIX
Nonmandatory Information
A1. METHOD TYPE APPROACH:
A1.1 Fineness Modulus
A1.1.1 The combined fineness modulus (FM) is obtained by adding the total percentages of material in the sample that are coarser than each of a set of sieves (cumulative percentages retained) and dividing the sum by 100 (see ACI 116).1 FM is an index of the fineness of the material. A higher FM means that the aggregate is coarser. Trial batches are necessary to establish target values.
A1.2. Coarseness Factor
A1.2.1. Workability factor and coarseness factor are determined for the combined aggregate. The factors are plotted on the chart shown in Figure 1. Zone II is the desired location.2
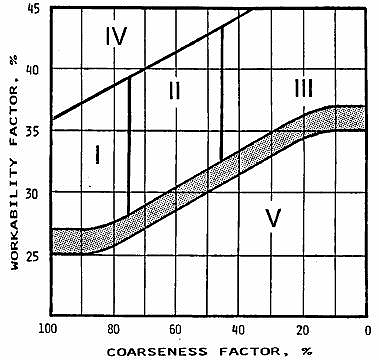
Figure 1—Coarseness Factor Chart
A1.2.2. The workability factor is the percent passing the No. 8 sieve adjusted for cementitious materials content of the proposed concrete mix. The measured percent passing the No. 8 sieve is increased or decreased by 1.0 percentage point for each 22 kg/cu m (38 lb/cu yd) that the cementitious materials content is above or below 334 kg/cu m (564 b/cu yd), respectively.
A1.2.3. The coarseness factor is the cumulative percent retained on the 9.5 mm (3/8-in.) sieve divided by the cumulative percent retained on the No. 8 sieve.
A1.2.4. The five zones in the chart represent the following types of concretes:
I "Gap-graded" and tends to segregate
II Well graded 38 to 13 mm (1-1/2 to 1/2 in.)
III 13 mm (1/2 in.) and finer
IV Sticky
V Rocky
A1.2.5. Example
Cement Content |
611 lb/cu yd |
Aggregate Data: As shown in Table A1.2.1 |
Aggregate ID |
Size 57 |
Sand |
SSD Weight, lbs |
1887 |
1108 |
Specific Gravity |
2.77 |
2.61 |
Aggregate, % by
weight |
63 |
37 |
Table A1.2.1—Sieve Analysis and Combined Grading
Sieve Size |
Size 57 |
Sand |
Combined |
% Passing |
% Mix |
% Passing |
% Mix |
% Passing |
Cum. % Retained |
% Retained |
2 in. |
100.0 |
63.0 |
100.0 |
37.0 |
100.0 |
0.0 |
0.0 |
1-1/2 in. |
100.0 |
63.0 |
100.0 |
37.0 |
100.0 |
0.0 |
0.0 |
1 in. |
100.00 |
63.0 |
100.0 |
37.0 |
100.0 |
0.0 |
0.0 |
3/4 in. |
85.0 |
53.6 |
100.0 |
37.0 |
90.6 |
9.4 |
9.4 |
1/2 in. |
60.0 |
37.8 |
100.0 |
37.0 |
74.8 |
25.2 |
15.8 |
3/8 in. |
35.0 |
22.1 |
100.0 |
37.0 |
59.1 |
40.9 |
15.7 |
No. 4 |
10.0 |
6.3 |
99.7 |
36.9 |
43.2 |
56.8 |
15.9 |
No. 8 |
0.0 |
0.0 |
87.8 |
32.5 |
32.5 |
67.5 |
10.7 |
No. 16 |
0.0 |
0.0 |
65.7 |
24.3 |
24.3 |
75.7 |
8.2 |
No. 30 |
0.0 |
0.0 |
33.6 |
12.4 |
12.4 |
87.6 |
11.9 |
No. 50 |
0.0 |
0.0 |
12.7 |
4.7 |
4.7 |
95.3 |
7.7 |
No. 100 |
0.0 |
0.0 |
3.4 |
1.3 |
1.3 |
98.7 |
3.4 |
No. 200 |
0.0 |
0.0 |
0.0 |
0.0 |
0.0 |
100.0 |
1.3 |
Q = Cumulative percent retained on 3/8 in. sieve = 40.9
R = Cumulative percent retained on No. 8 sieve = 67.5
W = Percent passing No. 8 sieve = 32.5
C = Cementitious materials content = 611 lb/cu yd
Workability Factor (WF) = W + (C-564)/38 = 32.5 + (611-564)/38 = 33.7%
Coarseness Factor (CF) = (Q/R)/100 = (40.9/67.5)100 = 60.6%
When the values of CF and WF are plotted on the Coarseness Factor Chart of Figure 1, they fall in Zone II.
A1.3. Power Chart:
A1.3.1. In this method, the percent passing each sieve size is plotted against the sieve size in microns raised to power of 0.45 on semi-log paper. A best fit straight line is then drawn through data points as shown by the broken line in Figure 2. The combined grading should follow the straight broken line within ± 7 percentage points deviation for percent passing. The dash lines in Figure 2 are 7 percentage points below and above the broken line indicating the acceptable variability. For aggregates passing the No. 30 sieve, the grading curve may fall below the power chart line to compensate for the presence of fine cementitious materials. 3
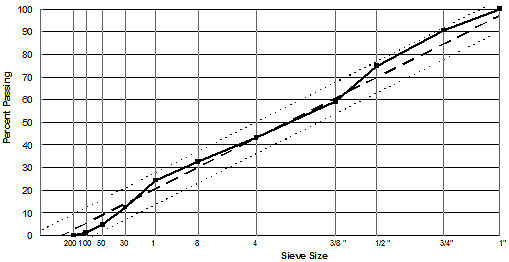
Figure 2— Power Chart
A1.4. Percent Retained on Each Sieve:
A1.4.1. In this method, the percent retained on each sieve size is kept to a limited range and the difference between percent retained on consecutive sieve sizes should be less than 10 percentage points.
A1.4.2. ACI 302 suggests limits for the material retained on each sieve for satisfactory reduction in water demand while providing good workability.4 If the largest size aggregate is 38.5 mm (1.5 in.), the percentage of material retained on each sieve size below the top size and above the number 100 sieve shall be between 8 and 18. If the largest size aggregate is 25 mm or 19 mm (1 in. or 3/4. in), the range shall be 8 to 22 percent. The ideal range for No. 30 (600 m m) and No. 50 (300 m m) sieves is 8 percent to 15 percent retained on each. These ranges are illustrated in Figure 3 together with the data from Table A1.2.1.
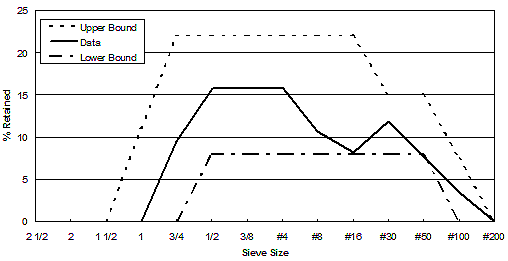
Figure 3— Percent Retained on Each Sieve
1 ACI Committee 116, "Cement and Concrete Terminology, (ACI 116-R)," American Concrete Institute, Farmington Hills, MI, 2000, 73 pp.
2 Shilstone, J. M., Sr., "Concrete Mixture Optimization," Concrete International, Vol. 12, No. 6, June 1990, pp. 33-39.
3 Neville, A. M., Properties of Concrete, Fourth Edition, John Wiley and Sons Inc., 1996.
4 ACI Committee 302, "Guide for Concrete Floor and Slab Construction, (ACI 302.1R," American Concrete Institute, Farmington Hills, MI, 1996, 65 pp.
Table of Contents | Next
FHWA-HRT-05-057
|