Boosting Pavement Performance with Aggregate Imaging
BETTER ROADS SEPTEMBER 2008
A Federal Highway Administration (FHWA) grant will help move a prototype system that analyzes the properties of aggregates used in pavement closer to market, making specification of paving materials that enhance roadway durability and skid resistance more reliable.
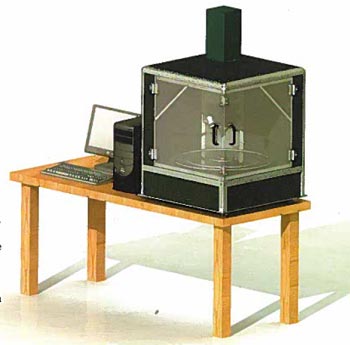
The commercial AIMS, shown in this conceptualized rendering, will be an integrated hardware/software system.
The grant was one of five awarded under the agency’s Technology Partnerships Program, which encourages industry to develop technologies now at the prototype stage in partnership with transportation agencies. The goal is to test promising innovations designed to improve highway quality and safety or reduce congestion in real-world settings and help make them commercially viable.
"Through the Technology Partnerships Program, we’re working to accelerate private sector engagement in addressing the challenges of building and maintaining the nation’s highway system," said FHWA Associate Administrator King W. Gee. "Industry innovation is essential to meeting the demands of roadway users for quality and safety."
Boosting Pavement Performance
Research has shown that the characteristics of aggregates used in hot–mix asphalt, hydraulic cement concrete and unbound aggregate pavement layers influence the structural integrity and durability of pavement systems. They also affect the skid resistance of pavement surfaces.
Key aggregate characteristics include shape, such as round, elliptical or flat; angularity, the sharpness of the corners of the aggregate particles; and texture, the smoothness or roughness of the particle surfaces. Accurate characterization of these properties—which vary with the type and source of aggregates and processing techniques—can improve specifications for projects and ultimately boost pavement performance and driver safety.
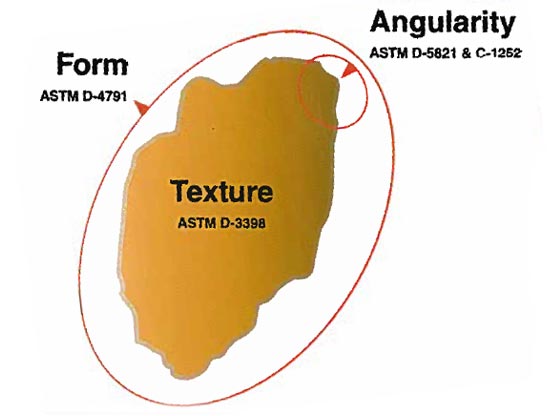
AIMS characterizes aggregate shape properties, which influence pavement performance.
The number of flat and elongated particles, for example, characterizes coarse aggregate shape. The angularity of gravel is determined by counting the number of particles with one or two crushed faces. Measuring the void percentage of an aggregate sample as it flows through a funnel assesses fine aggregate angularity.
A National Cooperative Highway Research Program study, described in Test Methods for Characterizing Aggregate Shape, Texture and Angularity (NCHRP Report 555), evaluated emerging test methods for measuring aggregate characteristics. The analysis looked at factors such as accuracy, cost, ease of use and readiness for implementation.
"AIMS allows the comparison of aggregates with a scientifically based system," said Meininger. "It measures aggregates in a nonbiased way."
Researchers tested an AIMS prototype at the Texas Department of Transportation and FHWA’s mobile asphalt materials testing laboratory. The mobile lab demonstrated how AIMS can be used to classify aggregate stockpiles for form, angularity and texture and its potential to replace aggregate consensus property test procedures for Superpave asphalt mix design with an automated, repeatable method that provides similar data, said Matthew Corrigan, mobile lab project manager.
The mobile lab has an ongoing project to collect AIMS data on a variety of aggregate sources used in asphalt pavements throughout the United States, Corrigan said. Future plans call for linking AIMS aggregate data with asphalt pavement performance in the field and recommending which aggregate properties are the best indicators for long–life asphalt pavements.
Refining AIMS
The AIMS system works by capturing digital images of the particles in an aggregate sample, analyzing the sample, and providing a graphical output of characteristics. The system’s software uses a series of analysis algorithms that objectively quantify aggregate properties on both the macro scale, such as shape and angularity, and the micro scale, such as surface texture.
The system uses computer digital images to measure the shape and angularity of individual particles from their silhouette outline and focal depth, and the texture of coarse aggregates from the gray–scale images of aggregate surfaces. The system’s software allows characterization of the distribution of shape and angularity for correlation with performance in pavement layers.
With the help of FHWA’s grant, Pine Instrument is now turning the prototype into a user–friendly, industry–ready product. In phase one of the project, the company is converting the collection of components that make up the research prototype to an integrated hardware system. It also is enhancing the analysis software to make results easier for AIMS users to interpret.
The combined hardware/software system will undergo a standard ruggedness study at Texas A&M University, a partner in the project, to determine how a variety of variables impact results, said Roger Pyle, Pine Instrument’s director of product technology.
The project’s second phase will involve tests at university, commercial and highway agency laboratories to establish the repeatability and reproducibility of AIMS results in a multi–laboratory environment. Texas A&M will analyze the data from those tests.
"It’s important to have an understanding of how reproducible the output from the system is," Pyle said. "We want to determine how closely the results will match when one aggregate supplier evaluates a product with one AIMS system and another lab uses a different system."
The planned outcome is an industry tool capable of accurately and rapidly measuring aggregate shape characteristics. Such a tool would offer an automated method of qualifying aggregate shape properties and surface texture to meet specifications, ensure good pavement performance and enhance roadway safety. The ultimate goal of this whole process is to develop a commercially available product.
A Future Look
In addition to AIMS, research is under way on other methods for measuring aggregate characteristics. One uses X–ray tomography, an imaging method widely used for medical applications, to obtain detailed, three–dimensional information on aggregates. Both the National Institute of Standards and Technology’s Virtual Cement and Concrete Testing Laboratory and FHWA’s Turner–Fairbank Highway Research Center are conducting studies using this method.
Another method uses high–resolution laser detection and ranging (LADAR) technology to provide three–dimensional measurements of aggregates from which quantitative characteristics can be calculated. LADAR consists of a photon source, a photon detection system, a timing circuit, and optics for the source and receiver. An NCHRP project is developing a LADAR system capable of precisely measuring aggregate characteristics such as shape, volume, angularity and surface texture.
Eventually, research efforts to better characterize aggregate properties may lead to more precise specifications for aggregate use on highway construction projects and better quality control tools for aggregate producers. "Once we have good aggregate measures that people can have confidence in, we can come up with more classes of materials and be more specific about what’s needed for a particular application," said Meininger.
Better measurement techniques may also increase the use of local aggregates on construction projects. Aggregates for U.S. projects are now transported from as far away as Canada and Mexico, which increases costs and has environmental consequences. "If local materials can be better characterized in shape, texture and angularity and qualified in terms of durability, they can be used instead," Meininger said.
Improving aggregate measurement and characterization techniques is just part of the equation, though. More research is also needed on how aggregate shape characteristics relate to pavement performance, said Meininger. "Once we have a better understanding of that, we can develop better specifications," he said.
To Learn More
The Technology Partnerships awards are the first grants FHWA has ever provided directly to general industry. Other companies received grants to refine and test an asphalt binder cracking device, an intelligent asphalt compaction analyzer, an all–weather pavement marking system for work zones and an automated pavement marker placement system.
FHWA is considering a second Technology Partnerships Request for Applications in June 2008. For more information on the Technology Partnerships Program or on participating in tests of the technologies, contact Julie Zirlin, Technology Partnerships Program coordinator, at (202) 366–9105 or julie.zirlin@dot.gov.
For more information on Pine Instrument’s aggregate imaging system, contact Dave Savage at (724) 458–6391 or dsavage@pineinst.com.
For more information on FHWA’s mobile asphalt materials testing laboratory, visit www.fhwa.dot.gov/pavement/asphalt/asmixlab.cfm or contact Matthew Corrigan at matthew.corrigan@dot.gov.