Precast Bent System for High Seismic Regions, Final Report
Publication No. FHWA-HIF-13-037
June 2013
Notice
This document is disseminated under the sponsorship of the U.S. Department of Transportation in the interest of information exchange. The U.S. Government assumes no liability for the use of the information contained in this document.
The U.S. Government does not endorse products or manufacturers. Trademarks or manufacturers' names appear in this report only because they are considered essential to the objective of the document.
Quality Assurance Statement
The Federal Highway Administration (FHWA) provides high-quality information to serve Government, industry, and the public in a manner that promotes public understanding. Standards and policies are used to ensure and maximize the quality, objectivity, utility, and integrity of its information. FHWA periodically reviews quality issues and adjusts its programs and processes to ensure continuous quality improvement.
1. Report No. FHWA-HIF-13-037 |
2. Government Accession No. N/A |
3. Recipient’s Catalog No. N/A |
||||
4. Title and Subtitle PRECAST BENT SYSTEM FOR HIGH SEISMIC REGIONS |
5. Report Date June 2013 |
|||||
6. Performing Organization Code |
||||||
7. Author(s) M. Lee Marsh1, Stuart J. Stringer1, John F. Stanton2, Marc O. Eberhard2, Olafur S. Haraldsson2, Hung Viet Tran2, Bijan Khaleghi3, Eric Schultz3, and Steve Seguirant4 |
8. Performing Organization Report No. |
|||||
9. Performing Organization Name and Address 1 BergerABAM, Inc. 33301 Ninth Ave South, Suite 300 Federal Way, WA 98003 2 University of Washington, Seattle, WA 3 Washington State Department of Transportation, Olympia, WA 4 Concrete Technology Corporation, Tacoma, WA |
10. Work Unit No. |
|||||
11. Contract or Grant No. DTFH61-09-G-00005 |
||||||
12. Sponsoring Agency Name and Address Federal Highway Administration Highways for LIFE Program Office 1200 New Jersey Avenue, SE Washington, DC 20590 |
13. Type of Report and Period Covered Final Report |
|||||
14. Sponsoring Agency Code |
||||||
15. Supplementary Notes |
||||||
16. Abstract This report is a technical resource that provides background information on the use of a precast bent system for use in high seismic regions. The system is designed for, and intended to be used with, prestressed girder bridges that are built integrally with the supporting intermediate piers. Such piers are built in two stages, with the lower stage placed first to provide support to the girders and the upper stage constructed later to integrate the pier and superstructure. The precast bent system uses precast columns with cast-in-place foundations, precast pier cap beams, and a cast-in-place upper stage pier cap beam. This report provides information on the system concept, as well as the background physical testing for the upper level grouted duct connections and the lower socket type connections. Additionally, the report provides design and construction specifications, describes a demonstration project constructed in Washington State, and discusses lessons learned from the demonstration project. Finally, two design examples are presented to illustrate the design process for the precast bent system for spread footings and drilled shaft foundations. This report includes three appendixes published as stand-alone documents:
In addition, two companion reports cover the detailed testing and modeling of the spread footing and drilled shaft foundation versions of the precast column-to-foundation connection:
|
||||||
17. Key Words Bridges, earthquakes, accelerated bridge construction, precast bent, connections, spread footing foundations, drilled shaft foundations, prefabricated bridge elements and systems |
18. Distribution Statement No restrictions. This document is available to the public through the National Technical Information Service, Springfield, VA 22161. |
|||||
19. Security Classif. (of this report) Unclassified |
20. Security Classif. (of this page) Unclassified |
21. No. of Pages 84 |
22. Price |
APPROXIMATE CONVERSIONS TO SI UNITS | APPROXIMATE CONVERSIONS FROM SI UNITS | ||||||||
---|---|---|---|---|---|---|---|---|---|
Symbol | When You Know | Multiply By | To Find | Symbol | Symbol | When You Know | Multiply By | To Find | Symbol |
LENGTH | LENGTH | ||||||||
in | inches | 25.4 | millimeters | mm | mm | millimeters | 0.039 | inches | in |
ft | feet | 0.305 | meters | m | m | meters | 3.28 | feet | ft |
yd | yards | 0.914 | meters | m | m | meters | 1.09 | yards | yd |
mi | miles | 1.61 | kilometers | km | km | kilometers | 0.621 | miles | mi |
AREA | AREA | ||||||||
in2 | square inches | 645.2 | square millimeters | mm2 | mm2 | square millimeters | 0.0016 | square inches | in2 |
ft2 | square feet | 0.093 | square meters | m2 | m2 | square meters | 10.764 | square feet | ft2 |
yd2 | square yards | 0.836 | square meters | m2 | m2 | square meters | 1.195 | square yards | yd2 |
ac | acres | 0.405 | hectares | ha | ha | hectares | 2.47 | acres | ac2 |
mi2 | square miles | 2.59 | square kilometers | km2 | km2 | square kilometers | 0.386 | square miles | mi2 |
VOLUME | VOLUME | ||||||||
fl oz | fluid ounces | 29.57 | milliliters | ml | mL | milliliters | 0.034 | fluid ounces | fl oz |
gal | gallons | 3.785 | liters | L | L | liters | 0.264 | gallons | gal |
ft3 | cubic feet | 0.028 | cubic meters | m3 | m3 | cubic meters | 35.314 | cubic feet | ft3 |
yd3 | cubic yards | 0.765 | cubic meters | m3 | m3 | cubic meters | 1.307 | cubic yard | yd3 |
NOTE: Volumes greater than 1000 l shall be shown in m3 | |||||||||
MASS | MASS | ||||||||
oz | ounces | 28.35 | grams | g | g | grams | 0.035 | ounces | oz |
lb | pounds | 0.454 | kilograms | kg | kg | kilograms | 2.202 | pounds | lb |
T | short tons (2000 lb) |
0.907 | megagrams | Mg | Mg (or "t") | megagrams (or "metric ton") |
1.103 | short tons (2000 lb) | T |
TEMPERATURE (exact degrees) | TEMPERATURE (exact degrees) | ||||||||
°F | Fahrenheit | 5(F–32)/9 or (F–32)/1.8 | Celcius | °C | °C | Celsius | 1.8C +32 | Fahrenheit | °F |
ILLUMINATION | ILLUMINATION | ||||||||
fc | foot–candles | 10.76 | lux | lx | lx | lux | 0.0929 | foot–candles | fc |
fl | foot–Lamberts | 3.426 | candela/m2 | cd/m2 | cd/m2 | candela/m2 | 0.2919 | foot–Lamberts | fl |
FORCE and PRESSURE or STRESS | FORCE and PRESSURE or STRESS | ||||||||
lbf | pounds | 4.45 | newtons | N | N | newtons | 0.225 | poundforce | lbf |
lbf/in2 | pound per square inch | 6.89 | kilopascals | kPa | kPa | kilopascals | 0.145 | poundforce per square inch | lbf/in2 |
*SI is the symbol for the International System of Units. Appropriate rounding should be made to comply with Section 4 of ASTM E380. (Revised March 2003)
Preface
Increasingly, construction methods that speed up bridge construction are being utilized to minimize traffic disruption and improve the safety of both construction workers and the traveling public. Often, prefabricated structural elements are used to speed up construction. Unfortunately, elements that speed up construction may not be appropriate when moderate to high seismic effects are expected.
This report summarizes a precast bent system that has been developed to both speed up construction and perform well under seismic loading. The system is configured to be used with precast girder superstructures that are supported on cap beams that are constructed in two phases. The first or lower-stage cap beam is constructed, the girders are then set on this beam, and finally the second or upper-stage cap is constructed using cast-in-place concrete to integrate the superstructure and substructure. This precast bent system is an adaptation of a common type of reinforced concrete bent or pier construction used throughout the United States.
Unique features of the precast bent system are a socket connection at the column-to-foundation connection and a grouted-duct arrangement at the column-to-cap beam connection. This system utilizes precast columns and precast lower-stage cap beams. The system also can include splices in the column to facilitate weight control for the columns, whereby splitting the column into multiple segments can limit the weight of precast elements that must be transported. Similarly, the precast cap beam can be split into segments for the same reason. Both of these internal connections are configured to be capacity protected for seismic forces. The lower column socket connection has also been configured to be used with spread footings, pile caps, and pile shafts (also known as drilled shafts).
Large-scale laboratory testing was completed and is reported in this report and in companion reports specifically covering each connection type. Design provisions have been crafted for use by designers with the AASHTO Guide Specifications for LRFD Seismic Bridge Design. Construction specifications are included in this report, as are design examples.
A demonstration project was constructed using this technology on a bridge in Washington State over Interstate 5. The details of the design for this project are included herein, as are construction photos and lessons learned that relate the construction contractor’s feedback following construction. The development and deployment of this technology has been a success, and the owner, Washington State Department of Transportation, continues to look for opportunities to apply the technology, along with other methods, to accelerate bridge construction in the State. The demonstration bridge is currently in service and is performing well, but has not been tested by an actual earthquake.
Table of Contents
CHAPTER 2. DESCRIPTION OF THE HFL PRECAST BENT SYSTEM
- Typical Precast Girder Bridge System
- Features of the HfL Fully Precast Bent System
- ABC-HfL Committee
- Summary
CHAPTER 3. SUPPORTING RESEARCH AND TESTING
- General Description of Testing Setup and Overall Approach
- Column-to-Cap Beam Connection Testing
- Large-Bar Anchorage Testing
- Column-to-Cap Beam Subassembly Testing
- Column-to-Spread Footing Connection Testing
- Test Specimen Design Details
- Experimental Results
- Experimental Results of the Column Splice
- Column-to-Oversized Pile Shaft Connection Testing
- Test Specimen Design Details
- Experimental Results
- Recommendations for Future Research
CHAPTER 4. DESIGN AND CONSTRUCTION SPECIFICATION PROVISIONS
CHAPTER 5. DEMONSTRATION PROJECT
- Structural Description of the Grand Mound Bridge
- Design Considerations
- Procurement
- Construction
- Lessons Learned and Contractor Feedback
- Footing
- Column Segments
- Grouted Column Joints
- Cap Beam
- Cap Beam Closure
- Girder End-Wall Diaphragms at Pier 2
- Precast Intermediate Diaphragms
CHAPTER 6. DESIGN EXAMPLE OVERVIEW
CHAPTER 7. CONCLUSIONS AND RECOMMENDATIONS
List of Figures
Figure 1. Diagram. Moment diagram of bridge pier with integral connections under transverse lateral loading
Figure 2. Photo. Typical prestressed girder bridge with longitudinal continuity
Figure 3. Diagram. Locations of connections relative to potential plastic hinge locations
Figure 4. Diagram. HfL precast bent concept, spread footing option – exploded view
Figure 5. Photo. Socket connection concept, as originally used
Figure 6. Photos. Precast bent cap under construction in Washington State
Figure 7. Diagram. Column-to-cap beam connection
Figure 8. Diagram. Cantilever subassembly testing setup for the column-to-cap beam tests
Figure 9. Photo. Test setup for large-bar anchorage testing
Figure 10. Graph. Grouted bar-duct pull-out test results
Figure 11. Equation. Development length for a bar grouted into a metal duct
Figure 12. Graphs. Column moment vs. drift plots
Figure 13. Graph. Specimen LB-FB milestones of damage
Figure 14. Photo. Condition of the base of column in LB-FB at end of testing
Figure 15. Photo. Construction of spread footing test specimen
Figure 16. Photo. Testing in progress for spread footing specimens
Figure 17. Diagrams. Strut and tie models for (a) bent out bars and (b) headed bars
Figure 18. Diagram. Details of test specimen SF-1
Figure 19. Diagram. Details of test specimen SF-2
Figure 20. Graph. Final criteria design space for specimen SF-3
Figure 21. Diagram. Specimen SF-3, section parallel to load direction
Figure 22. Graph. Specimen SF-1 base moment-drift response
Figure 23. Graph. Specimen SF-2 base moment-drift response
Figure 24. Graph. Specimen SF-3 base moment-drift response
Figure 25. Chart. Comparison of specimen drift ratios at major damage states
Figure 26. Photos. Comparison of test specimens after one cycle to drift of 4.3 percent
Figure 27. Photo. Specimen SF-2 after completion of cyclic testing
Figure 28. Photo. Specimen SF-3 footing failure
Figure 29. Diagram. Precast column elevation and splice location
Figure 30. Equation. Embedded length of the column into the shaft
Figure 31. Equation. Spacing of shaft transverse reinforcement
Figure 32. Diagram. Elevation and plan of strut-and-tie model for transmitting column forces to the drilled shaft in the splice region
Figure 33. Photos. Column reinforcement (left) and shaft-footing reinforcement (right)
Figure 34. Photos. Specimen construction (left) and specimen testing (right)
Figure 35. Graph. Specimen DS-1 base moment-drift response
Figure 36. Graph. Specimen DS-2 base moment-drift response
Figure 37. Chart. Comparison of specimen drift ratios at major damage states
Figure 38. Photo. Specimen DS-1 after testing
Figure 39. Photo. Specimen DS-2 after testing
Figure 40. Diagram. HfL demonstration project bridge layout
Figure 41. Diagram. HfL demonstration project plan and section at the center pier
Figure 42. Diagram. HfL demonstration project segmental column elevation
Figure 43. Diagram. HfL demonstration project segmental column sections
Figure 44. Photo. Mock-up of the grouted joint
Figure 45. Photos. Construction sequence for placement of first precast column segment
Figure 46. Photos. Construction sequence for placement of the column segments
Figure 47. Photo. Precast cap beam placement
Figure 48. Photo. Grouting the joints between column segments and between columns and cap beam
Figure 49. Photo. Placement of precast girders and preparation for deck slab topping concrete
Figure 50. Photo. Completed demonstration bridge (photo courtesy of the Precast/Prestressed Concrete Institute)
Figure 51. Photo. Single-piece column used on the 36th Street Bridge in Redmond
Figure 52. Photo. Difficulty with sealing the column segment joint during grouting
Figure 53. Photo. Lowering the second lower-stage cap beam into place
Figure 54. Photo. Lower-stage cap beam closure prior to concrete placement
Figure 55. Photo. Girder end wall diaphragms and girders on oak blocks
Figure 56. Photo. Precast end panel
List of Tables
Table 1. Test matrix for beam-to-column connection
Table 2. Spread footing test specimens
Table 3. Spread footing test specimen material properties and axial loading
Table 4. Column and shaft reinforcement
Table 5. Drilled shaft test specimen material properties and axial loading
AASHTO | American Association of State Highway and Transportation Officials |
ABC | Accelerated bridge construction |
ACI | American Concrete Institute |
ADT | Average daily traffic |
C-C-T | Compression-compression-tension |
CP | Capacity protected |
ED | Energy dissipating |
ERS | Earthquake resisting system |
FHWA | Federal Highway Administration |
HfL | Highways for LIFE |
HSS | Hollow structural section |
o.c. | On center |
P-M | Axial load-moment |
SDC | Seismic Design Criteria |
WSDOT | Washington State Department of Transportation |
CHAPTER 1. INTRODUCTION
Background
Bridge construction frequently leads to traffic delays, which incur costs that can be measured in terms of time, wasted fuel, and emotional distress. Transportation agencies are therefore seeking methods for accelerating bridge construction ABC. Use of precast concrete for bridge substructures offers potential time savings on site and represents promising technology for ABC. Furthermore, limiting the amount of on-site work improves safety for both the motoring public and highway workers, and it reduces environmental impacts. For these reasons, transportation agencies are gradually embracing the ABC philosophy for many of their urban construction projects.
Connections in precast substructures are typically made at the beam-column and column-foundation interfaces to facilitate fabrication and transportation. However, for structures in seismic regions, those interfaces represent locations of high moment and shear demands, as well as large inelastic cyclic strain reversals. Developing connections that are not only sufficiently robust to accommodate those inelastic cyclic deformations, but are also readily constructible, is the primary challenge for ABC in seismic regions.(1)
This report describes the development, experimental validation, and on-site implementation of a precast concrete bridge bent system that is intended to meet those challenges. The development was possible only because of the close cooperation among members of the team, which included the disciplines of design (BergerABAM, Washington State Department of Transportation), research (University of Washington), precast fabrication (Concrete Technology Corporation), and construction (Tri State Construction).
The work described in this report was partially supported by a grant from the Federal Highway Administration (FHWA) Highways for LIFE (HfL) Technology Partnerships Program. The purpose of Highways for LIFE (HfL) is to advance longer-lasting highway infrastructure using innovations to accomplish fast construction of efficient and safe highways and bridges. Furthermore, HfL seeks to improve safety during and after construction, reduce congestion caused by construction, and improve the quality of highway infrastructure. Accordingly, the HfL precast bent system improves safety during construction by reducing the time the contractor is on a congested job site, it improves safety after construction by using improved connections for seismic resistance, it reduces highway congestion in terms of reducing construction time, and overall, it should improve infrastructure by providing better and more durable construction.
Potential Benefits of ABC and Criteria for Selection
The primary benefits of ABC accrue from the savings of time on site. Conventional bridge construction typically generates traffic congestion and delays for an extended time period, which adversely affects individual travelers’ budgets and the region’s economy, impacts air quality due to increased vehicle emissions, and reduces quality of life due to personal time delays. Also, untimely service due to delays for workforce, supplier, and customers can result in significant costs to the traveling public and regional businesses.
Prefabrication of structural elements is the essence of accelerated construction. Although prefabrication can decrease total contract time, reduction of the time spent on site is the critical component. Khaleghi documented the details of ABC usage in Washington State and the Washington State Department of Transportation (WSDOT) strategic plan for ABC.(2)
Precast units are often constructed in specialized plants. There, repetitive construction permits investment in high-quality steel forms, which more easily allow for high-quality finishes and accurate dimensional control. Plant precasting also allows tight quality control of materials, rapid production, good schedule control, and the possibility of prestressing. Site precasting offers other advantages, such as allowing workers to work at ground level and removing the need for, and limitations of, long-distance transportation to the site. While precasting the substructure may impose a construction cost premium, it can often be offset by the economic benefits of the time saved through ABC.
Objectives
The objectives of this project were to bring a bent system to market that could be used with prestressed girder bridges that are used in the higher seismic regions of the country. The system needed to be conceived such that it was readily constructible, thereby satisfying the need for ABC, and it needed to be sufficiently rugged that it can accommodate the levels of seismic shaking expected in such regions of the country. The constructability would be demonstrated during the construction of an actual bridge using the technology developed for the bent system. And the required seismic ruggedness would be demonstrated by laboratory testing of large-scale components of the bent system. Additionally, design tools would be needed by the bridge engineering community, so design specifications, design examples, and construction specifications would also be developed.
Overview of Report
Chapter 2 of this report describes the HfL precast bent system by first reviewing the current preferred construction methods of bents or piers in Washington State, then comparing the HfL system to the standard bents. The western portion of Washington State is a high seismic area and, accordingly, bridges in that part of the State have been designed to withstand large earthquakes. The HfL system begins with the current system and introduces precast elements and improves connectivity in such bents at the same time. The goal of the construction is to emulate cast-in-place construction and provide equal or better performance, both seismically and from a durability standpoint.
Chapter 3 reviews the testing work that has been done by the University of Washington in support of the HfL precast bent system. This work includes testing of precast column-to-cap beam connections that predates the HfL grant and testing that was supported by the grant, which includes tests of both spread footing and oversized pile shaft column-to-foundation tests.
Chapter 4 provides an overview of the design and construction specifications that have been developed as part of this project. Full listings of the design specifications are included in appendix A (published under separate cover), and the design provisions have been formatted such that they could be adopted into the AASHTO Guide Specifications for LRFD Seismic Bridge Design, referred to herein in as the AASHTO Seismic Guide Specifications.(3)
Chapter 5 describes the demonstration project, which is a two-span bridge over Interstate 5 in Washington State. The chapter provides insight into the design considerations, the construction of the center bent, which was the focus of this HfL grant, and concludes with a debrief and lessons learned summary from the contractor and the design team.
Chapter 6 provides an overview of the design examples that have been developed to support deployment and training of engineers in how to design the HfL bent system, including background on how to use the AASHTO Seismic Guide Specifications document and approach for this system.
Chapter 7 provides concluding remarks and recommendations for future deployment and use of the system.
This report also has three appendixes, published as stand-alone documents:
- Appendix A provides a draft of the design specification language in the form of an appendix that could be included in the AASHTO Seismic Guide Specifications specifically for this precast bent system.
- Appendix B includes Design Example No. 1, which covers the seismic design of the demonstration project bridge with its spread footings.
- Appendix C includes Design Example No. 2, which covers the design of a column-to-drilled shaft connection.
CHAPTER 2. DESCRIPTION OF THE HFL PRECAST BENT SYSTEM
Typical Precast Girder Bridge System
For many years bridge engineers have used precast, prestressed concrete girder superstructures because they are quickly erected and have proven both durable and cost-effective. Girder technology has been continually improved upon so that spans in excess of 200 ft are now possible.
However, precast substructures, with the exception of piling, have seldom been used in high seismic regions. Lateral seismic forces cause the largest moments to occur at the connections, as shown in figure 1, due to frame action of the columns and cap beams. Those connections must be moment-resisting and robust under cyclic loading to maintain the integrity of the structure, and if the members are precast, the connections must also be easy to assemble on site. Achieving both characteristics simultaneously represents a significant design challenge.
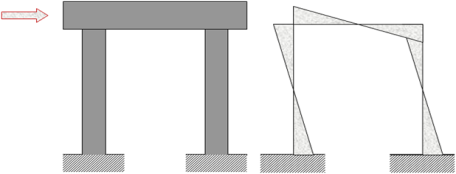
Figure 1. Diagram. Moment diagram of bridge pier with integral connections under transverse lateral loading.
Under longitudinal seismic loading, it is highly desirable that a moment connection exist between the girders and cap beam. This type of connection is used by WSDOT and is useful wherever longitudinal continuity is desired. Such a system is referred to as an integral bent cap and is commonly achieved with two-stage cap beam construction by casting an upper-stage cap beam around bars and prestressing strands that project from the girder ends, thereby connecting the girders rigidly to the completed cap beam. Figure 2 shows a typical prestressed concrete girder bridge with longitudinal continuity. In the absence of such a moment connection, the columns must act as cantilevers, resulting in a system that is not as efficient as one in which column fixity is developed at both the top and bottom of the columns.
It is essential that the location of precast element connections be coordinated with the locations of potential plastic hinging zones that are expected to develop during seismic loading. Many connections may be located away from plastic hinging zones, and those connections are not expected to see large inelastic cyclic strains. Such connections may be designed simply to be acceptably strong and to remain elastic under seismic loading. These connections are “capacity protected” (CP), as shown in figure 3, meaning that they should never see forces large enough to produce inelastic action because the plastic hinges, which are located elsewhere, act as fuses to limit the internal forces.
On the other hand, connections that are near or adjacent to plastic hinging regions do experience inelastic action and therefore participate in the dissipation of earthquake-induced vibration energy. These connections are called “energy dissipating” (ED) elements, as shown in figure 3. ED connections are being used in this precast bent system, and thus the connections’ ability to endure the expected inelastic seismic demands must be proven in laboratory experiments. These experiments are key elements of the process to demonstrate viability of the precast bent system for deployment in seismic regions.
Features of the HfL Fully Precast Bent System
The HfL precast bent system utilizes precast columns, either single piece or segmental, and precast lower cap beams. Figure 4 shows the configuration of the system that was developed. The construction sequence and the subsequent advantages of the bent (or pier) system are described here.
First, the foundations are prepared to accept the precast columns; either spread footings or oversized pile-shaft foundations may be used. The foundation-to-column connection is referred to as a socket connection. In the case of the spread footing foundation, the socket connection is made by placing the precast column in the excavation, placing the footing steel, then casting the footing concrete. Alternatively, the footing steel may be placed before the column is set. Similarly, for the oversized pile-shaft, the column is placed on top of the cast-in-place shaft and the transition or splice region of the shaft is cast around the column.
The precast column-to-foundation connection’s primary advantage is construction speed, because it allows a foundation and a column to be cast in little more time than is needed to cast a foundation alone. Furthermore, because the connection vertical strength is much greater than the weight of the cap beam, the foundation need not achieve full design strength before the cap beam can be placed. The time to the start of setting girders on the cap beam is a critical measure of the savings provided by the bent system.
Once the foundation reaches adequate strength, the lower-stage precast cap beam may be placed by passing the beam over reinforcing bars that extend upward from the precast column. The reinforcement extending from the column is arranged as “fewer, larger” bars to simplify the erection of the bent system. These bars may typically be No. 14 or No. 18 bars. Corrugated metal ducts are included in the cap beam to accept the column dowels. These ducts are of a relatively large diameter, such that the potential for interference with the column bars is minimized. The column bars are subsequently grouted into the ducts in the lower-stage cap beam. Owing to the superior confinement of the ducts, relatively short embedment lengths are possible and are sufficiently robust, as demonstrated in the laboratory, to resist the cyclic inelastic action expected during an earthquake.
After the lower-stage cap beam is grouted into place and the grout attains sufficient strength, the girders may be placed. The common practice of placing all girders for one span first, then moving the cranes to place the girders on the adjacent span, is still acceptable with this system. From this point on, the pier and bridge are completed as usual, with a small depth of concrete being placed above the lower stage to lock in the girders, then intermediate diaphragms may be placed. The deck slab is constructed, and finally the upper-stage cap is poured.
The foundation-to-column and column-to-cap beam connections are the critical elements that lead to the system’s viability, and the genesis of each is reviewed here.
The socket connection concept arose from discussions with Tri-State Construction regarding simple ways to precast a column and integrate it with the foundation. The socket concept had the advantages of having no projecting bars from the precast column sides, which makes handling the columns easy, and because the column is embedded the full depth of the footing, no concrete is required to be placed beneath the column, which helps ensure good consolidation of the concrete around the column. If soil conditions are not adequate to reliably support the precast column during erection, then a small unreinforced slab can be placed below the column to facilitate safe and accurate erection.
The socket concept for the footing-to-column connection was used previously in Washington State in a modified form, by the contractor on the HfL project team. In that case, the contract called for cast-in-place columns, but the contractor elected to precast them on site and to use a socket connection to save time. See figure 5. The footing was 6 feet thick, the columns were 4 feet square, and the connection between them was made by both roughening the column surface locally and by adding horizontal form-saver bars. Those bars screwed into threaded couplers embedded in the face of the column within the depth of the footing to provide shear friction resistance across the interface, and were inserted after the column had been placed. At the time, the confirmation testing of the HfL foundation connections had not been completed, so the form-saver bars were included for conservatism.
The concept for the column-to-cap beam connection has been used previously in the high seismic zone of western Washington State. Figure 6 shows fabrication and subsequent placement of that precast bent cap. The bridge site was in a congested urban area with high visibility from the traveling public and with high scrutiny from local municipalities. To open the bridge as quickly as possible, the contractor proposed precasting the cap beams for the intermediate piers instead of casting them in place, as shown on the contract plans. This change saved the owner and the contractor several weeks on the contract duration. The columns were reinforced with the same No. 14 column bars as on the original plans. They were grouted into 4-inch galvanized steel ducts that were placed in the precast bent cap using a template. The cap beams weighed approximately 100 tons each and were precast on the ground adjacent to the columns.
For the system described in this report, the grouted column bar-beam connection was modified by using the largest bars possible, up to and including No. 18 bars. That choice allows the ducts to be large in diameter and few in number; both features facilitate fit-up on site and reduce the probability of accidental misalignment. However, anchorage of such large bars within the depth of the cap beam is not possible if the development length equations of the American Association of State Highway and Transportation Officials (AASHTO) LRFD Bridge Design Specifications referred to herein as the AASHTO LRFD, must be satisfied.(4) Previous studies had indicated that bars grouted into ducts resulted in significantly shorter development lengths than predicted by the standard equations due to the confinement provided by the duct, but those studies examined smaller bars and tighter ducts than are proposed here.
Research was therefore undertaken to determine the development properties of large bars grouted into large-diameter ducts and the response of such connections to cyclic lateral loading.(5) That research is described in detail below.
The cap beam-to-column connection for the proposed system is shown in figure 7. A precast concrete column, with six No. 18 vertical column bars projecting from the top, is placed in the excavation, braced, and then the footing is cast around it. Later, the precast cap beam, which contains 8.5-inch-diameter corrugated metal ducts, is fitted over the column bars and grouted in place, completing the bent. The selection of six No. 18 vertical column bars reduces the congestion at the column-to-cap beam connection while providing generous assembly tolerances.
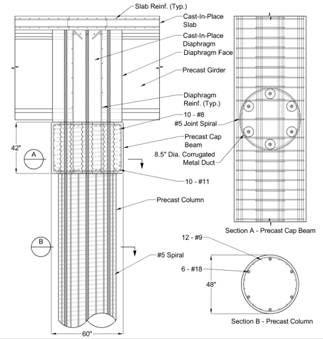
Figure 7. Diagram. Column-to-cap beam connection.
The top and bottom connections are different because, even though the seismic performance requirements are similar in both locations, the construction needs are not. A spread footing for a typical overpass is generally too heavy for precasting to be viable, so it is likely to be cast in place. The socket connection then provides generous tolerances and fast construction. However, using the socket concept at the top would mean casting the cap beam in place, and that would eliminate much of the time advantage of prefabrication. Thus, a socket connection at the base and a grouted-duct connection at the top were selected as practical solutions to this problem.
The connections may be compared with other alternatives, such as those given in Marsh et al.(1) For example, grouted sleeves have been adopted for the base connection by a number of agencies, such as the Utah DOT. The sleeves are typically cast into the column and fit over bars projecting upwards from the footing. The socket system proposed here has the advantages that the placement tolerances for the column are significantly greater than those available with a sleeve system, and the connection requires no special or proprietary hardware.
ABC-HfL Committee
To help guide the HfL demonstration project design and construction effort, the WSDOT Bridge and Structures Office convened a committee consisting of WSDOT engineers, University of Washington researchers, consultants, contractors, and precasters. This group met regularly during the design and construction phases. Because the overall concepts for the top and bottom of column connections had been established, the group primarily focused on small modifications that would improve the constructability, while either maintaining or improving seismic performance. Concurrent with the design effort, testing at the University of Washington was ongoing, and most of the modifications could be included or addressed in some manner during testing. This helped keep the experimental test specimens as nearly identical to the details deployed in the field demonstration as possible. The committee also assisted WSDOT with integration of the HfL bent system into the overall demonstration project bridge, and considerations such as the actual geometry of sections, skew, bent cap cross slope, and tolerances were addressed during the design phase. Ideas to facilitate the formwork used for the upper stage of the cap beam were developed and included. These resulted in “end walls” that were constructed on the prestressed girders to act as side forms for the upper cap beam. Additionally, other precast elements were considered and included in the demonstration project. These included the use of precast intermediate diaphragms on the prestressed precast girders.
Summary
The intention is that the HfL precast bent system may be used anywhere that high seismic ground motions are expected. Thus, the system should have wide applicability across the United States. The system shown herein is somewhat specific to WSDOT construction, but it can be easily adapted for use in other parts of the country. Because the critical energy dissipating connections are in the substructure, the system is compatible with a wide variety of precast prestressed girder types, including the AASHTO I-type sections, the popular State DOT-specific types, which have been optimized for efficiency, and the popular bulb and decked-bulb tee section types.
CHAPTER 3. SUPPORTING RESEARCH AND TESTING
General Description of Testing Setup and Overall Approach
To proof test the concepts developed for the HfL bent system, large-scale testing of subassemblies was conducted at the University of Washington, where the three major subassemblies (column-to-cap beam, column-to-spread footing, and column-to-oversized pile shaft connections) were tested individually. The subassemblies were each determinate cantilever test specimens; thus, the applied forces were known at all points during the testing. An example of the testing machine set-up is provided in figure 8, where the upper column-to-cap beam connection test specimen is shown. Note that the specimen was tested inverted. This same testing rig was used to test the spread footing and oversized pile shaft specimens.
Column-to-Cap Beam Connection Testing
The major questions about the precast bent system that required experimental investigation concerned the connections. At the cap beam, the dominant issues were anchorage of the large-diameter column bars into ducts and the inelastic cyclic performance of a moment connection made with large bars.
The bar anchorage demands can be divided into two categories; construction and seismic. For the first-stage precast cap beam, the length available for bar development is limited by the depth of the cap beam, and the loads consist of the weight of the girders and slab. (The second-stage cap beam is typically cast with or even after the last section of roadway slab, so most of the slab weight will be in place before the second stage is cast.) Because all the girders on one side of the cap beam may be placed before any are set on the other side, and the slab may be poured from one end of the bridge to the other, the cap beam will likely experience torsional loading. It is this torsional loading that leads to the potential for tensile stresses to develop in the bars under construction conditions. This loading controls the development demand in the first-stage precast cap beam. In the great majority of cases, anchorage sufficient to develop the yield strength of the bar would be sufficient to resist the construction loads, because the construction demands are kept below the yield stress of the bars.
However, seismic loading leads to higher bar stresses and inelastic strain demands, and therefore requires a more robust anchorage. For all but the largest and most critical bridges, seismic design is conducted only for the bridge in its finished form, in which case both stages of the cap beam are in place, and the total height of the cap beam is available for development of the column bars. Thus, during an earthquake, both the bond demand and the total bond capacity are larger. Because the grouted ducts exist only in the first-stage cap beam, the components of the total bond capacity in the two stages of the cap beam are likely to differ.
Additionally, the anchorage demands differ depending on whether the loading is in the transverse direction of the bent or in the longitudinal direction. Because the lower-stage of the cap beam is below the soffit of the girder superstructure, longitudinal load transfer between the substructure and the superstructure occurs entirely above the lower-stage cap beam (this can be seen in figure 3). In the transverse direction, frame action for this type of open-soffit superstructure system is developed with the columns and the full-depth cap beam. Therefore, the full depth of both stages of the cap beam is available for resistance of the column plastic hinging moments (see figure 1).
For testing of the column-to-cap beam connection, two series of tests were performed. Prior to testing of the column and cap beam subassembly as described in the introductory section above, individual bars grouted into corrugated steel ducts were tested to failure. This testing helped define the efficiency of the grouted-bar connections and thus helped establish the bar sizing and arrangement for the main subassembly tests. The testing of both the individual bars and the upper connection subassembly was completed before the HfL grant was awarded. The tests were funded by WSDOT and completed at the University of Washington. Full details of these tests may be found elsewhere. (See references 5, 6, 7, and 8.) However, for completeness an overview of these tests is provided in the sections below.
Large-Bar Anchorage Testing
To investigate the development of bars grouted in steel ducts, the University of Washington performed 17 monotonic pullout tests with bars as large as No. 18, which supplemented a previous test series at smaller scale.(9) The test setup for these experiments is shown in figure 9, where the corrugated metal duct is cast into the cylindrical anchor block. The large bars were then grouted into the ducts and tested until failure with a hydraulic ram. The applied load was recorded with a load cell above the ram. Bar strains, displacements, and anchor block surface deformations were also recorded throughout the tests.
The material characteristics in the tests included ASTM A706 Grade 60 deformed reinforcing bars, corrugated galvanized pipes (also called ducts in this report), and cementitious grout with a nominal compressive strength of 8.0 ksi. The corrugated pipes are available in diameters from 6 inches to 12 feet. The pipes have thicker walls, deeper corrugations, and potentially better bond and confinement properties than those of standard post-tensioning duct. Seventeen pull-out tests were conducted on No. 8, No. 10, No. 14, and No. 18 bars with embedments ranging from two bar diameters up to 14. Four specimens were tested with polypropylene fibers to determine whether such fibers when mixed in the grout had any beneficial effect.
Experimental Results
The results of the pull-out tests are summarized in figure 10, which shows the bar stress at failure plotted against embedment length. To permit comparison among different bar sizes, the embedment length is normalized with respect to bar diameter. In the nomenclature for the tests, 18N06 denotes a No. 18 bar, with no fiber in the grout (denoted by the letter N), embedded 6 bar diameters. Where applicable, the letter N is replaced by the letter F to signify fiber in the grout. The letter C indicates a bar embedded in concrete, which was used as a control specimen to verify the scaling of the ducts and bars was appropriate. One test used the letter S to indicate a splitting failure at the top surface of the surrounding concrete cylinder. This was caused in part by the spiral reinforcing of the cylindrical anchor block slipping, reducing the confining pressure of the concrete surrounding the grouted duct. The compression struts radiating from the anchored bar then caused the anchor block to split. This failure mode was suppressed in all other specimens and, as such, the data point is somewhat of an anomaly. A nonlinear numerical model was calibrated against the test results, and the model’s results are also shown.
Three outcomes can be seen from the tests. First, the bar stress at failure is essentially proportional to le/db, where le is the embedment length and db is the bar diameter. This implies that the bond stress is constant along the bar and the same in all specimens, and that failure was by plastic shear failure in the grout. Visual observations supported this finding. Second, the bar can be anchored to reach yield and fracture if the embedment lengths are at least 6 and 10 db, respectively. These are experimental results, and suitable safety factors, in the range of 50 percent, should be added for design, particularly for cyclic design conditions. These results show that even a No. 18 bar can easily be anchored to achieve fracture within the 3.5-ft depth of a typical cap beam.
Third, it appears that the presence of fibers in the grout actually reduced the bond strength, as well as the cube strength of the grout. This can be explained as follows. Longitudinal elastic and plastic elongation is accompanied by a reduction in bar diameter due to Poisson effects and necking, respectively, which causes the lugs to partially disengage from the surrounding grout, thereby reducing the bond capacity. In the post-peak region, the fibers had been expected to improve the behavior by bridging cracks in the grout, but the ducts appeared to fulfill that function. When the bond strengths were normalized by the square root of the grout compressive strength, the peak resistance of the specimens with and without fibers was similar. It was concluded that the duct provided adequate confinement to the grout, and that the fibers were not necessary.
Based on these experimental results, an expression for calculation of the embedment length, lac, was developed for the HfL precast bent project. This expression is given in figure 11.
In the equation, dbl is the bar diameter, fye is the expected yield strength of the bar, and f’g is the compressive strength of the grout (taken as the 28-day strength because expected value strengths are not typically quantified in the literature). This expression is based on developing an ultimate tensile strength of 95 ksi with a 10 dbl embedment. A 1.5 safety factor, as mentioned above for cyclic loading, is then applied, and the conversion between the expected yield and expected ultimate is 1.4 = 95/68 for A706 Grade 60 reinforcing steel. The stated coefficients produce a lac/dbl = 16.1 to develop 95 ksi tensile strength with 8 ksi grout. On the plot in figure 10, this would produce line from the origin to approximately 95 ksi at 16 le/db, which conservatively envelops (is beneath) all data points, including specimen 18N14.
Column-to-Cap Beam Subassembly Testing
Once the anchorage properties under monotonic tension loading had been established, column-to-cap beam connection tests were conducted under cyclic lateral loading.(7,8) The specimens were tested upside down for convenience, so the cap beam could be bolted to the base of the test rig. The specimens were 42 percent scale, so the 20-inch-diameter test column represented a 48-inch-diameter prototype. The goal was to investigate the behavior of complete grouted bar connections under cyclic lateral load.
Four subassemblage tests were performed to evaluate the seismic performance of the proposed connection. The primary study variable was the bonded anchorage length of the longitudinal bars into the cap beam. In two of the specimens, the reinforcing bars were debonded over 8db near the beam-column interface to reduce the strain concentrations at the cold joint at the soffit of the cap beam.
Table 1 shows the details of the scaled test specimens. Specimen REF is a scaled model of a typical WSDOT cast-in-place bridge column, with 16 No. 5 bars evenly distributed around the perimeter, giving a longitudinal reinforcement ratio, ρ, of 1.58 percent. The transverse reinforcement consists of a ¼-inch-diameter spiral spaced at 1¼ inches. This specimen provides a baseline for evaluating the performance of the proposed system, and hence its designation as REF, for “reference.”
The other three specimens, LB-FB, LB-D1, and LB-D2, represent possible variations of the proposed precast connection. The columns were reinforced longitudinally with six No. 8 bars that were grouted into 4-inch-diameter corrugated metal ducts in the cap beam and extended through the full depth of the stage 2 cast-in-place diaphragm. These bars represent larger prototype bars, hence the specimen names with LB, which stands for “large bar.” This reinforcement provided a longitudinal reinforcement ratio, ρ, of 1.51 percent. In specimen LB-FB, the bars were fully bonded into grouted ducts, whereas in specimens D1 and D2, two methods of local debonding were studied. The local debonding was intended to reduce the strain concentration at the beam-column interface that is caused by the short development lengths and the cold joint at the interface. The bars in LB-D1 and LB-D2 were debonded over a length of 8 bar diameters, 8db, into the cap beam using two different methods (D1 and D2). LB-D1 was debonded using a 1-inch-diameter schedule-40 PVC pipe, which was split longitudinally, fitted tightly around the No. 8 bar, taped together, and sealed with caulk at the ends. LB-D2 was debonded using a 1-inch-diameter schedule-30 PVC pipe that fit more loosely around the bar and was easier to construct, but provided no restraint against bar buckling. The detail was constructed by sliding the pipe over the bar and sealing it with caulk at the ends.
Additionally, 12 No. 3 bars were added around the perimeter of each precast column to satisfy AASHTO LRFD longitudinal bar spacing requirements. The additional bars stopped at the cap beam interface and therefore provided no additional flexural capacity. The spiral reinforcement in the columns was the same as in the reference specimen, and the spiral continued with the same spacing into the cap beam to confine the joint region. A thin grout pad was provided at the beam-column interface to simulate field erection of the precast pieces. Fluid, high-strength, non-shrink grout with an average compressive strength of 9 ksi at 5 days was used. Grade 60 bars were used for the mild steel reinforcement, while Grade 90 wire was used for the spirals. The design concrete strength was 6 ksi.
Specimen | Description | ρ (%) | Longitudinal Reinforcement | f’co (ksi) | Paxial (kips) | ![]() |
---|---|---|---|---|---|---|
REF | Reference cast-in-place reinforced column | 1.58 | 16 - No. 5 | 6.83 | 240 | 0.112 |
LB-FB | Precast column with bars fully grouted in corrugated ducts in beam | 1.51 | 6 - No. 8 (12 - No. 3 for spacing) |
8.34 | 212 | 0.081 |
LB-D1 | LB-FB with bars debonded 8 db in the grouted ducts using Method 1 | 1.51 | 6 - No. 8 (12 - No. 3 for spacing) |
7.69 | 260 | 0.108 |
LB-D2 | LB-FB with bars debonded 8 db in the grouted ducts using Method 2 | 1.51 | 6 - No. 8 (12 - No. 3 for spacing) |
6.20 | 240 | 0.123 |
Experimental Results
Each specimen was tested under constant axial load and a cyclic lateral displacement history. The selected lateral loading protocol consisted of three cycles at each of a series of increasing displacements. All four specimens demonstrated nearly identical force-displacement responses and levels of physical damage. Specimens REF, LB-FB, LB-D1, and LB-D2 maintained 80 percent of their peak lateral resistance up to drifts of 5.5 percent, 5.2 percent, 5.7 percent, and 5.8 percent, respectively.
Figure 12 shows the equivalent (base) moment versus drift ratio curves for each specimen.
The four curves are remarkably similar, despite the different specimen construction methods. The slightly different peak loads are mainly attributable to minor differences in the applied axial load and material strengths. There is a small amount of pinching seen in the curves just before the system crosses zero displacement, which occurs because the compressive force is resisted only by the reinforcing bars prior to closing of the cracks in the concrete. It can also be seen that there is little loss in flexural strength until the drift reaches at least 4 percent, despite the increasing amount of damage accumulating in the plastic hinge region.
The largest contributor to the total deformation for specimens LB-FB, LB-D1 and LB-D2 was the opening of a large localized crack at the column-to-cap beam interface. Rotations measured over the bottom 1.5 inches of the column accounted for more than 90 percent of the total column displacement. This phenomenon, in which the members behave as essentially rigid bodies, while the connections accommodate deformations, has been successfully used in precast building design and tested in the PRESSS program.(10) In contrast, in specimen REF, the curvature was more evenly distributed over the bottom 3.5 feet of the column, as is common in cast-in-place systems. In specimen REF, the crack width at the interface was roughly equal to the sum of the widths of the flexural cracks above, thus indicating approximately equal contributions to the specimen displacement.
The types and amount of physical damage observed were nearly identical for all specimens, including specimen REF. Damage consisted of moderate spalling of the concrete cover and crushing of the core concrete over a plastic hinge region about 12 inches long. Spalling initiated at drift levels of 2.0 percent, 2.0 percent, 2.4 percent, and 2.1 percent for specimens REF, LB-FB, LB-D1 and LB-D2, respectively.
At drift levels of 5.6 percent, 5.3 percent, 5.7 percent, and 5.8 percent, respectively, the extreme flexural bars began to buckle, pushing outward on the spiral. The spiral kinked and then fractured shortly after longitudinal bar buckling was first observed. When the buckled bars were next loaded in tension, they straightened and fractured. The finding that buckling in the column occurred at almost the same drift in each specimen was surprising, given that in two specimens the bars were debonded over a length of 8 inches in the cap beam. However, the great majority of the bar deformation occurred in the column, where the detailing was the same in all specimens.
Longitudinal bars in specimens LB-FB, LB-D1 and LB-D2 fractured at drift levels of 6.5 percent, 7.1 percent, and 7.4 percent, respectively. Bar fracture was brittle with no necking, and occurred approximately 6 inches along the column from the interface with the cap beam, at the apex of the buckled shape. One bar partially fractured during a load cycle and illustrated the failure process; the inside face of the buckled bar experiences extreme compression strain due to combined compression and bending. When the bar straightens on the next tensile cycle, the inner face undergoes a large strain increment that initiates fracture due to low cycle fatigue. This observation and the lack of necking indicate that bar fracture occurs as a consequence of bar buckling and not tensile strain concentration at the interface.
The points during loading at which various types of physical damage occur are shown for the fully bonded, LB-FB specimen in figure 13. This figure provides a visual reference between damage locations and the hysteresis loops for this specimen. This representation is also helpful in interpreting pushover analysis curves for such a specimen. Note that the designation of “cap-beam” spalling denotes the onset of shallow spalls on the top of the cap beam locally around the ducts. This spalling was minor in nature.
Despite their different capacities for inhibiting buckling, the two types of details, fully bonded and debonded, performed almost identically. This is confirmed by the similarity in their moment-drift curves. The primary reason for the similarity in behavior was that the debonding was located in the cap beam, whereas the buckling deformations occurred in the body of the column, where both specimens were identical. It is felt that debonding is unnecessary, because the grouted bar pulls out a conical wedge of grout from the duct and the cyclic loading progressively breaks down the bond between the bar and the grout allowing strain penetration to form. Thus, this region behaves similarly to an intentionally debonded bar permitting relief of strain concentrations. It should be noted, however, that for pulse or impact loading debonding may be beneficial as significant strain penetration has not been developed through cyclic loading.
All three variations of the proposed system performed satisfactorily to a drift ratio of 5.5 percent, before longitudinal bar buckling and fracture occurred. This value is approximately three times the demand expected in a major earthquake and is comparable to the value achieved with a cast-in-place system. In all cases the failure occurred in the plastic hinge region of the column. This finding suggests that the large-bar, large-duct precast system has sufficient ductility capacity for all foreseeable seismic demands, and system performance is similar to cast-in-place construction.
Figure 14 shows the condition of the plastic hinging zone of the column for specimen LB-FB at the end of testing (i.e., after longitudinal bar fracture). This damage was similar in all three of the grouted-duct specimens. It can be seen that, while the column is extensively damaged, the cap beam and joint region are in acceptable condition. Some minor cracking can be seen in the joint region on the right side of the cap beam in the photo. Additionally, the shallow spalls on the face of the cap beam near the ducts are likewise visible. Such damage is consistent with the capacity protection design approach, where only minor damage is permitted in the members adjacent to a plastic hinging member. The damage state for this specimen satisfies this constraint. Thus, the performance of the test specimens indicates that the response is similar to cast-in-place construction, and the cap beams can be adequately capacity protected for this type of connection.
Column-to-Spread Footing Connection Testing
As with the upper connection, proof testing of the socket concept was necessary to demonstrate viability of the connection to the footing. The goal of the laboratory tests was to evaluate the connection’s response to combined cyclic lateral load and constant vertical load. To be successful, the connection must provide adequate seismic resistance and simultaneously not lose its ability to support the bridge gravity load.
The specimens for the spread footing connection tests consisted of 20-inch-diameter precast concrete columns embedded in cast-in-place foundations. The columns were cantilevers and were loaded at a location that corresponded to the inflection point in the prototype column. The cantilever height was 60 inches, or three column diameters. Figure 15 illustrates the construction of the foundation. The lower column segment has been placed and the footing reinforcement has been tied. Note the block outs for the anchor rods, instrument rods projecting horizontally from the column, and the column longitudinal reinforcement ready to be grouted into the upper column segment.
The testing was conducted with axial load and lateral shear loading applied to the test specimen. Lateral restraint prevented sliding of the bottom of the footing, but no hold-downs were used. Figure 16 shows what appear to be uplift restraints as through bolts and yellow load cells. These were provided only to prevent overturning, if it occurred. The bolts were left loose, and they were never engaged during testing. This arrangement is one of the few tests known to exist of foundations where rocking was permitted, even though it never occurred. This verified the approach of utilizing the axial load to resist overturning even as the column developed its full plastic hinging moment.
The longitudinal reinforcement in the precast column is developed at the base by mechanical anchors or heads, rather than the traditional method of bending the bars outwards. Doing so offers the construction advantage that the precast column becomes a linear concrete element with no reinforcement protruding to the side, and it is therefore simpler and safer to both cast and transport. The headed anchorage method also offers a much more direct force transfer between the column and the footing than the bent-out bar configuration, as demonstrated by the strut-and tie models shown in figure 17. The bent-out arrangement requires extensive stirrup steel, as the hook on the main bar is ineffective in transferring column forces through the joint region and into the footing. This is because the compression strut within the joint must develop tangentially to the outside of the 90-degree bend in the column bar. This configuration also leaves an unreinforced section between the hooks and bottom bars that can split horizontally after the joint region has cracked, which can propagate into a complete joint failure.
The model proposed for use with the headed bars is simple, by contrast, and provides positive and robust development of the longitudinal column reinforcement through a well-defined compression-compression-tension (C-C-T) node. The headed bars thus offer advantages from both constructability and seismic performance viewpoints. This is unusual; more commonly, a change that benefits one imposes a disadvantage for the other.
The major questions associated with the connection’s seismic performance are related to the transfer of forces from the column to the footing, so the testing focuses on this transfer. The headed-bar detail helps address this performance, but other issues must also be addressed. The connection must be able to resist the cyclic column moments without significant damage to the footing and without the column punching through the footing under gravity load. tested socket columns for buildings and concluded that, unless special conditions were satisfied, the footing depth should be at least 1.5 times the column diameter.(11) However, the sockets they used were much smaller in plan than a typical spread footing for a bridge, so two of the HfL tests, which were based on a footing depth/column diameter ratio of 1.1, demonstrated that the connection is strong enough to induce a plastic hinge to form in the column, just above the footing. Achieving this behavior is important, not only because it is required by the AASHTO specifications, but also because post-earthquake inspection and repair are more expensive for footings than for columns.(3,4)
Test Specimen Design Details
The prototype spread footing was designed according to the specifications in force at the time of the experimental design. (See references 12, 13, 14, and 15.) The prototype structure included 48-inch-diameter precast concrete segmental columns embedded into a 54-inch-thick cast-in-place reinforced concrete spread footing. Stability against overturning and one-way shear determined the footing’s dimensions. The AASHTO Seismic Guide Specifications require that the resultant of the vertical reaction forces be located within the center two-thirds of the footing under dead loading; this resulted in an 18-foot square prototype footing.
Top and bottom flexural steel within the footing were controlled by minimum steel requirements and resulted in No. 8 bars at 12 inches on center (o.c.) and No. 11 bars at 12 inches o.c., respectively, in each principal direction. Twelve No. 10 diagonal bars were placed horizontally around the column, to provide confinement of the region around the column in order to develop a normal clamping force and the corresponding shear friction resistance across the precast–cast-in-place interface. The diagonal bars were concentrated into three sets at the bottom and one at the top. The diagonal reinforcing steel used was equal to the amount needed if the cohesive component of the shear friction force defined by the AASHTO LRFD was ignored completely. Four additional No. 8 diagonal bars were provided on the top mat to resist cracking on the diagonal around the column.
Minimum transverse reinforcement within the footing was provided using No. 5 bars at 12 inches o.c. within the effective width, as required by Caltrans. This requirement for transverse steel in footings was also adopted into the second edition of the AASHTO Seismic Guide Specifications and is now required. However, the purpose of this steel is in large part to preserve the strut-and-tie mechanism for column bars that are turned outward, as was shown in figure 17a.
All of the test specimens were scaled down to 42 percent scale of the prototype structure to fit within the testing equipment. In the first two spread footing specimens, SF-1 and SF-2, the footing depth was approximately equal to the column diameter. These proportions are typical of cast-in-place construction. Because these two specimens failed in the column with no damage at all to the footing, a third specimen was constructed with a footing depth that was only half of the column diameter. The goal was to force failure into the footing to gain a better understanding of the flow of forces within the joint region and the possible failure mechanisms.
The design of SF-1 was the most conservative of the first two specimens. SF-1 had slots under the column to allow some bars of the bottom mat (scaled to No. 5 bars at 5 inches o.c.) reinforcement to go through the base of the column, which ensured a direct engagement between the compressive strut from the column and the tension steel in the footing. The scaled down top mat consisted of No. 3 bars at 5 inches o.c. The diagonal shear friction bars placed around the column were 12 No. 4 bars in the bottom mat, and 4 No. 3 bars in the top mat. Caltrans’s requirement of transverse reinforcement was met with 3-gauge ties at 5-inch spacing within the effective width of the footing. The total number of stirrups was therefore 128 in specimen SF-1. Details of this specimen are shown in figure 18.
Specimen SF-2 was a simplified version of specimen SF-1. One difference was that the slots at the base of the columns were removed to simplify the column formwork, and this arrangement would simplify placement of the footing steel in the field. Consequently, the bars could not go underneath the column, and instead, they were bundled with existing bars on either side of the column. That placement frees the bottom mat of steel to be placed at any time, thereby improving constructability. Most of the diagonal shear friction steel was taken out, leaving only one set (four bars) in each of the bottom and top mats. Ties were reduced by half and kept in the locations where they would most effectively engage with 45-degree compressive struts developing within the footing. Details of specimen SF-2 are shown in figure 19.
The design of specimen SF-3 was based on the test results for specimens SF-1 and SF-2, in which nearly all of the damage was concentrated in the column, as opposed to the footing. The footing in SF-3 was designed to be much thinner to increase the likelihood of footing damage. Experimentally, the objective of SF-3 was to estimate how thin a footing could be used with the socket connection.
To estimate the capacity and failure mode of the footing, a design criteria space was created based on AASHTO code provisions. The demands were based on the column strength calculated using expected material properties (fy = 68 ksi and f’c = 5.2 ksi), while the footing and connection capacities were based on design strengths, calculated with ϕ-factors according to AASHTO LRFD and the Seismic Guide Specifications. The design space (figure 20) shows combinations of the normalized footing depth (hfooting/Dcolumn) and normalized footing length (Lfooting/Dcolumn) that would lead to failure. Each curve in the figure corresponds to a particular failure mode. Combined shear and moment transfer was also added to the design space, where it is designated “ACI moment transfer.” This mode of failure is not treated directly by the AASHTO criteria; thus, the American Concrete Institute (ACI) 318 criteria were used. Each curve is marked “above” or “below” to indicate whether the design point on the graph should lie above or below the curve. Arrows are also used on the plot to indicate on which side of the curve the design point should lay.
The Lfooting/Dcolumn ratio of the footing was determined by overturning considerations to be 4.5. Then, the design space showed that the critical failure modes were one-way shear, and the ACI combined shear and moment transfer mechanism (shown as the green line with “x” marks). Note that the design space also shows a potential shear friction failure and a column longitudinal bar development failure. These criteria are not relevant in the design of specimen SF-3 for the following reasons. First, the shear friction curve corresponds to shear friction resistance provided by the cohesive component alone and ignores the benefits of any shear friction steel, which was provided, thus mitigating this failure mechanism. Second, the longitudinal bar development curve does not account for the fact that the column bars were terminated with mechanical anchors.
To suppress the one-way beam shear but allow punching shear and moment transfer to occur, shear reinforcement needed to be placed in strategic locations. Transverse reinforcement was placed outside the nominal conical failure surface for punching shear (extending d of the footing away from the column faces in all directions) but within the beam shear failure planes (consisting of lines located d from the “compression” and “tension” faces of the column). Since the column portion embedded in the footing was octagonal, the failure plane was predicted to be closer in shape to that of an octagon. Placement of the shear reinforcement was also limited by the effective shear width defined in the AASHTO Seismic Guide Specifications.
The result of this design procedure was a footing depth that was half the column diameter. Unlike specimens SF-1 and SF-2, the bottom flexural reinforcement of specimen SF-3 was not controlled by minimum requirements. Strength considerations required No. 7 bars at 2.5 inches o.c. in which the first four lines of steel on either side of the column were bundled. Minimum steel was placed in the top mat, and instead of distributing those bars along the specimen’s width, fewer and larger bars were used and were placed near the column to hold up the ties. Since the tie steel was designed to suppress the one-way shear failure mechanism, it exceeded Caltrans’ minimum requirement of (psi) shear stress capacity on the cross section and resulted in a stress of about
(psi) (area of steel within the effective width, beff, 40 inches). The 2:1 ratio of column diameter to footing depth, along with suppression of beam shear, predicted that the footing would fail in combined punching shear and moment transfer. The reinforcement and geometry of specimen SF-3 are shown in figure 21.
Table 2 provides a summary of the design features of the three spread footing test specimens, and table 3 provides the day of test material properties and the applied axial loading.
Specimen | Column Slots | Bottom Reinforcement | Top Reinforcement | Shear Friction Reinforcement Sets | Ties |
---|---|---|---|---|---|
SF-1 | Yes | Minimum | Minimum | 3 Bottom 1 Top |
Full Caltrans |
SF-2 | No | Minimum | Minimum | 1 Bottom 1 Top |
Half Caltrans |
SF-3 | No | Strength | Minimum | 1 Top | 1-Way Shear |
Specimen | fy (ksi) | Column f’co(ksi) | Footing f’co(ksi) | Paxial (kips) | ![]() |
---|---|---|---|---|---|
SF-1 | 61.6 | 5.00 | 6.51 | 159.4 | 0.101 |
SF-2 | 61.6 | 5.50 | 6.76 | 159.2 | 0.092 |
SF-3 | 59.2 | 7.94 | 7.91 | 159.5 | 0.064 |
In specimens SF-1 and SF-2, the column contained a grouted lap splice 20 inches above the top of the footing in order to evaluate splice performance when constructability constraints necessitate the use of a segmental column. The splice detail is an optional feature of the precast bent system that allows long columns to utilize precast technology, when single piece columns are too heavy to transport and erect. The position of the splice may be seen in figure 15, at the top of the column in the photo. Note that the upper segment of the column has not yet been grouted onto the lower segment of the column.
In all three cases, the column surface was roughened where it was embedded into the footing. The roughening was achieved using small timber strips that represented, at laboratory scale, the “saw tooth” roughening used at the end of Washington State standard prestressed concrete girders. Use of timber strips necessitated flat surfaces, so the cross-section was changed from circular to octagonal in the lower portion of the column. Other methods of surface roughening, such as sandblasting or use of a surface retarder, may be possible and would allow the use of a circular section throughout as long as the resulting degree of roughness is verified.
Experimental Results
Figures 22 through 24 show the hysteretic responses of the three test specimens in terms of base moment versus drift ratio. The measured responses of the specimens indicate that all three specimens exhibited a stable hysteretic response with minimal strength degradation until high drift ratios are achieved. Similar to the column-to-cap beam connections discussed above, only minimal pinching was observed due to crack closure. The responses of both specimens SF-1 and SF-2 were stable to large drifts (at about 6 percent), at which point the lateral-load resistance dropped rapidly due to longitudinal bar buckling, loss of core confinement due to fractured transverse steel, and ultimately longitudinal bar fracture. By contrast, the strength of specimen SF-3 decayed more gradually, with a consistent rate of degradation starting at 2.5 percent drift, then rapid strength loss at roughly 10 percent drift when a combined shear and moment transfer failure occurred.
The maximum base moments were approximately 3,100 kip-in. for both specimens SF-1 and SF-2, while specimen SF-3 was approximately 10 percent stronger than the other two specimens (with a base moment capacity equal to roughly 3,350 kip-in.). Uniaxial tension tests on the column longitudinal reinforcing steel showed that all three specimens had virtually the same yield and ultimate strength. However, the concrete cylinder compression tests showed that the concrete compressive strength was about 50 percent higher for specimen SF-3 than for specimens SF-1 and SF-2 (see table 3); hence, the increase in flexural resistance.
The definition of failure is often taken as the state at which flexural resistance drops below 80 percent of the maximum resistance obtained in the test. In both specimens SF-1 and SF-2, that state occurred at approximately 7 percent drift and corresponded to the onset of buckling of the longitudinal bars (roughly 7 percent drift in both SF-1 and SF-2). Ultimately, the bars fractured in specimens SF-1 and SF-2 at 10.6 percent drift, at which point the lateral-load resistance of the columns decreased abruptly.
Specimen SF-3 maintained its strength above 80 percent of the maximum base moment resistance to a drift ratio 8.3 percent when being pushed to the north and 10.5 percent drift when pushed to the south. The column bars did not fracture in specimen SF-3. Instead, the column punched through the footing resulting from the development of a combined shear and moment transfer failure mechanism.
As shown in figure 25, the damage progression was similar for all specimens. Cracking of the column in all three specimens initiated during the first loading cycles with additional crack initiation and propagation throughout subsequent cycles. First yield in the column longitudinal bars was detected at the level of the column-to-footing interface and occurred at nearly the same drift for all three specimens: specimen SF-1 yielded at 0.55 percent drift, specimen SF-2 yielded at 0.47 percent drift, and the bar in specimen SF-3 yielded at a drift ratio of 0.51 percent drift.
The spalling pattern among the three specimens was similar but not identical. Minor spalling first appeared in specimens SF-1 and SF-2 at drift ratios of approximately 1.1 to 1.2 percent. Specimen SF-3 reached this level of damage slightly later, at a drift ratio of 1.4 percent. The specimens reached the level of significant spalling, which corresponds to a spalled height greater than 1/4 of column diameter, at about 2.2 to 2.6 percent drift for all three specimens. The fully spalled state (after which spalling no longer progressed) varied both in terms of drift ratio and the overall extent of spalling. This state was reached for specimens SF-1, SF-2 and SF-3 at drift ratios of 7 percent, 4 percent, and 6 percent, respectively. The spalling in SF-1 and SF-2 extended 10 inches and 12 inches above the top of the footing respectively, whereas in SF-3, the spalling extended up only to a height of 7 inches.
Figure 26 compares spalling of the three columns at a drift ratio of 4.3 percent drift. As spalling in the column increased, the longitudinal bars were exposed, which was eventually followed by longitudinal bar buckling at approximately 7 percent drift for all specimens. The spiral reinforcement fractured shortly after as a result of buckling of the longitudinal bars. In subsequent cycles, the longitudinal bars at extreme tension and compression locations underwent alternating buckling and straightening cycles, which induced large strain reversals, particularly along the inside face of the buckled bar.
a) Specimen SF-1 |
b) Specimen SF-2 |
c) Specimen SF-3 |
Figure 26. Photos. Comparison of test specimens after one cycle to drift of 4.3 percent.
Fracture due to low-cycle fatigue initiated at the locations of bar buckling for specimens SF-1 and SF-2 at roughly 10.6 percent drift. The final state of damage due to cyclic loading for specimen SF-2 can be seen in figure 27. The damage of specimen SF-1 was very similar. The damage observed is emulative of conventional well-detailed reinforced concrete construction for these two specimens, and this confirms the effectiveness of the socket-connection approach.
No bars fractured in specimen SF-3, as the column to footing connection failed due to the combined shear and moment transfer vertical shear stresses around the perimeter of the column segment within the footing. The final condition of specimen SF-3 from underneath the footing can be seen in figure 28. This failure condition was expected and provided useful information on the relative footing and column dimensions. The specimen also possessed a remarkable drift capacity (10 percent) considering the details of construction. However, it is not recommended that such unusual construction be utilized in practice (i.e., thin footing with relatively deep column). Further details of the testing can be found in Heraldsson et al.(16)
Experimental Results of the Column Splice
A construction splice was included in the column in the SF-1 and SF-2 test specimens. This arrangement is shown in figure 29, where the grouted splice began 20 inches above the top of the footing and extended upward away from the plastic hinge region. The purpose of this splice was to demonstrate that a grouted splice of the longitudinal bars could be adequately developed to transfer the column forces. This splice is closer to the plastic hinge region than the AASHTO Seismic Guide Specifications would permit. However, the splices suffered no damage or deterioration other than a crack within the grout bedding layer between column segments during the testing of the specimens. Steel strains within the column longitudinal reinforcement (bar mark C102 in figure 29) measured 2 inches below the grout layer (i.e., 18 inches above the top of the footing) indicated strains well in excess of five times the yield strain at roughly 5 percent drift. The strain gauges saturated at this strain level and were unable to record higher strains. This indicates that the splice region within the upper column segment was able to resist relatively high cyclic strain demands without any significant damage or deterioration.
The splices demonstrated acceptable performance in the laboratory testing, thus indicating that such splices can be designed within the column and still achieve capacity protected behavior of the column. In practice, the splices should be kept as far away from the plastic hinging as is reasonable to help ensure adequate performance.
Column-to-Oversized Pile Shaft Connection Testing
To make the fully precast bridge bent system applicable to multiple foundation types, a column-to-oversized pile shaft (drilled shaft) connection detail was proposed. It was adapted from the column-to-footing “socket” connection described previously and consists of embedding a precast column into the cast-in-place transition or splice region of the pile shaft.
Test Specimen Design Details
A shaft and column system prototype was designed according to the AASHTO LRFD, AASHTO Seismic Guide Specifications, and WSDOT Bridge Design Manual.(12,13,17) Two reduced-scale test specimens were developed from the prototype and then fabricated and tested at the University of Washington under combined cyclic and axial loading. The prototype precast column was designed to have a reinforcement ratio of approximately 1 percent, with the transverse reinforcement in the column defined by requirements for shear and confinement of the concrete core. The column longitudinal reinforcement was terminated with mechanical anchor heads to provide a short non-contact lap splice between the column and pile shaft longitudinal reinforcement within the splice region of the shaft. By minimizing the size of the splice region, a conservative (upper bound) estimate of the maximum prying forces generated by the embedded column segment can be developed.
The surface of the column was roughened where it was to be embedded in the pile shaft. The details of the roughening were the same as those used by the column-to-footing socket connection specimens. Load transfer at the interface was designed using the AASHTO LRFD shear-friction design procedure and strut-and-tie models. In the embedded region, the column section was reduced to an octagon to facilitate the forming of the roughened surface, which used wooden strips. This shape was chosen for constructability reasons, and it does not need to be octagonal from a force-transfer perspective.
The embedment length of the column in the pile shaft was defined by requirements for splicing the shaft and column bars. The splice is by definition a non-contact splice, for which the WSDOT Bridge Design Manual provides design requirements. Because the column bars were larger than the shaft bars they would normally control the splice length. However, the mechanical anchors on the column bars reduce the development length so that straight shaft bars controlled the splice length. The shaft was designed as a capacity-protected element to ensure that the plastic hinge would form in the column and the shaft would remain essentially elastic.
The shaft lateral confinement reinforcement was designed according to WSDOT Bridge Design Manual requirements for non-contact lap splices in conventional cast-in-place pile shafts. The spiral was terminated by three turns of spiral at the top of the shaft. This length calculation was proposed by McLean and Smith.(18) The embedded length was calculated according to the equation shown in figure 30.
In this equation, lns is the length of the non-contact lap splice, ls is the lap splice length between the longitudinal column and shaft bars, ls = 1.7 ld (for a Class C lap splice), where ld is the development length of the controlling bar, and e is the distance between the shaft and column longitudinal reinforcement.
The shaft spirals were designed as non-contact lap splices according to the WSDOT Bridge Design Manual. The spacing for spirals was determined according to the equation shown in figure 31.
In this equation, Asp is the area of the shaft transverse (spiral or hoop) reinforcing bar, Al is the total area of the column longitudinal reinforcement, fytr is the nominal yield strength of the shaft transverse spiral reinforcement, ful is the specified minimum tensile strength of the column longitudinal reinforcement, and k is a factor representing the ratio of column tensile reinforcement to total column reinforcement at the nominal resistance, which may be determined from moment-curvature analysis or taken as 0.5.
The spiral spacing requirements were also adapted from McLean and Smith, and the intent of the spiral in the splice region is to provide sufficient clamping force to preserve the integrity of the force transfer mechanism when the column bars reach their tensile strength.(18)
The scale of the system was chosen so that the ratio of shaft diameter to column diameter was as small as possible according to WSDOT Bridge Design Manual detailing requirements, so that test specimens represented the most critical conditions. This led to the prototype system consisting of a 6-foot-diameter column and a 9-foot-diameter shaft, which were represented at 28 percent scale in the laboratory specimens by a 20-inch-diameter column and a 30-inch-diameter shaft. The embedded length of the column in the pile shaft (28 inches) was based on the scaled-down non-contact lap splice length of the shaft prototype according to the WSDOT Bridge Design Manual.
The only difference between test specimens DS-1 and DS-2 was the amount of spiral within the column-to-shaft splice region. Specimen DS-1 included the lateral confinement reinforcement scaled from the prototype pile shaft, while specimen DS-2 included 50 percent of the scaled prototype lateral confinement reinforcement. The goal was to promote failure in the shaft splice region in specimen DS-2, to develop an understanding of the load transfer and failure mechanisms. Figure 32 illustrates a simplified strut-and-tie mechanism for the transfer of forces between the column and shaft. This mechanism is discussed in detail in Hung et al.(19) Table 4 summarizes the longitudinal and lateral pile shaft reinforcement for the prototype structure and the two test specimens. Table 5 summarizes the day of test material properties and the applied axial loading.
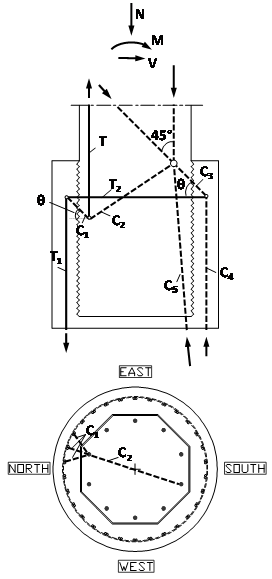
Figure 32. Diagram. Elevation and plan of strut-and-tie model for transmitting column forces to the drilled shaft in the splice region.
Item | DS-1 | DS-2 |
---|---|---|
Column Longitudinal Reinforcement | 10 No. 5 bars | 10 No. 5 bars |
Column Lateral Confinement Reinforcement | 3-gauge wire at 1.25-in. pitch | 3-gauge wire at 1.25-in. pitch |
Shaft Longitudinal Reinforcement | 2 No. 3s bundled, total 30 bundles | 2 No. 3s bundled, total 30 bundles |
Shaft Lateral Confinement Reinforcement | Two 9-gauge wire at 3-in. pitch | One 9-gauge wire at 3-in. pitch |
Specimen | fy(ksi) | Column f’co(ksi) | Shaft f’co(ksi) | Paxial (kips) | ![]() |
---|---|---|---|---|---|
DS-1 | 66 | 7.77 | 7.36 | 159 | 0.065 |
DS-2 | 66 | 7.17 | 6.45 | 159 | 0.071 |
In both specimens, the bottom of the shaft was fixed to a 74-inch by 48-inch by 24-inch cast-in-place footing so that the specimens could be attached to the testing rig. The test specimens were constructed in three stages, the column and the specimen footing were each cast separately, as seen in figure 33. Once these components had cured, the column was lifted and placed inside of the pile shaft reinforcement extending out of the specimen footing. This is shown on the left in figure 34. The shaft transition was then cast around the octagonal portion of the column integrating the column and the pile shaft. The specimens were then placed into the testing rig, as shown on the right in figure 34, where they were instrumented and finally tested.
Experimental Results
Quasi-static, cyclic lateral load tests were performed to evaluate the seismic performance of the two specimens. In each test, the specimen was subjected to a constant axial load of 159 kips, accompanied by a cyclic displacement-controlled lateral loading. The column base moment-drift responses for specimens DS-1 and DS-2 are shown in figure 35 and figure 36, respectively.
Overall, the response of each specimen was ductile with stable hysteretic loops and minimal pinching until large drift ratios were achieved. The maximum moments at the base of the column (top of pile shaft) were approximately 3,400 kip-in. in both specimens. In both specimens, the peak moment occurred at about 2.5 to 3.0 percent drift, and the moment first dropped below 80 percent of the peak value at about 8 percent drift for DS-1. Specimen DS-2 reached 20 percent strength loss at approximately 6.5 percent drift, when vertical and diagonal cracks had propagated throughout the entire splice region and the shaft lateral confinement reinforcement had begun to rupture.
The progression of damage is chronicled in figure 37, which shows the drift ratios at the initiation of significant damage states recorded for the column and the shaft of each test specimen. In the initial cycles, up to about 0.7 percent drift ratio, the cracks in both specimens were hairline and closed almost completely at zero displacement between cycles. At about 0.7 percent drift, the longitudinal steel in the column yielded; after this, the first significant horizontal cracks appeared. These cracks did not close completely after the horizontal load dropped to zero.
After the longitudinal column reinforcement yielded, each specimen behaved quite differently. In DS-1, damage was concentrated in the column directly adjacent to the top of the shaft, and the specimen eventually failed by fracture of the longitudinal steel in the plastic hinge region of the column, in what might be thought of as a typical column failure. The longitudinal bars buckled, causing a kink in the spiral steel, which initiated its fracture. After the spiral fractured, the longitudinal bars straightened and re-buckled with each load cycle and eventually fractured due to the low-cycle fatigue caused by the alternate bending and straightening. The longitudinal steel in the shaft never yielded, and the transverse steel in the shaft yielded but never fractured. This behavior, characterized by concentration of damage in the column, was similar to that of specimens SF-1 and SF-2.
In specimen DS-2, the amount of spiral steel in the shaft was only half that in specimen DS-1. It is therefore not surprising that the transverse reinforcement in the shaft yielded earlier than in DS-1 and subsequently fractured. The damage to the splice region was characterized by very large vertical and diagonal cracks opening up within the shaft. This inelastic action contributed significantly to the overall specimen displacements. Failure was initiated by fracture of the spiral steel in the shaft, starting at the top and progressing downwards. The damage to the shaft caused the load to drop with increasing drift. The longitudinal bars in the column did not buckle, and the lateral confinement reinforcement in the column never fractured.
Figure 38 shows specimen DS-1 after the test. The damage to the shaft exists mainly in the small region of top cover concrete above the ends of the vertical bars. In the remainder of the shaft, the column is still held firmly by friction. Figure 39 shows specimen DS-2 after testing, where the shaft has been pried open by the lateral prying forces generated by the embedment of the column so the column could be lifted freely out of the shaft without any resistance.
Recommendations for Future Research
The experimental work served as proof-of-concept testing for the system. Inasmuch as the localized column inelastic response was similar to that of conventional reinforced concrete, significant confidence resulted from the few large-scale tests completed. This is so largely because the plastic hinge regions themselves were, in fact, the same as conventional cast-in-place concrete. The significant difference between cast-in-place construction and the HfL bent system lies in the adjacent capacity protected elements. These comprise the spread footing joint region and surrounding concrete, the column-to-drilled shaft splice region, and the joint region in the cap beam just above the column.
While other researchers have completed tests of column-to-spread footings, the drilled shaft tests completed as part of this project are some of the only tests the authors are aware of for the splice region. Accordingly, the two tests reported herein are themselves useful, but additional tests to better isolate the force transfer mechanisms in the splice zone would be useful. One such test is currently underway at the University of Washington.
The dropped (two-stage) cap beam system with integral connection with the superstructure girders, whether part of this precast bent system or part of a conventional cast-in-place system, has not been sufficiently tested to fully understand the effectiveness of the longitudinal seismic force transfer mechanism. It is believed that conservative allocation of the distribution of those forces has been accounted for, but large-scale proof testing of the system is highly desirable. The open soffit nature of prestressed girder bridges puts more demand on the girder flange-to-cap connection than that of a box girder bridge, where the lower flange is continuous across the width of the bridge. Such testing could validate the ability to suppress damage in the superstructure and cap beam while simultaneously transferring sufficient forces to ensure plastic hinging in the column tops below the cap beam. The target force level would be the overstrength forces corresponding to plastic hinging.
A third area of research that would be desirable is the effect of including prestressing in the column itself. The use of unbonded prestressing has been shown effective in reducing damage and residual drifts in piers subjected to earthquakes. Historically, there has been concern over the durability of unbonded tendons in columns, but the use of precast columns for the HfL system creates an opportunity to potentially overcome that concern. It has been proposed, and testing is underway, to use pretensioned strand that is debonded in sealed ducts in the middle length of a precast column, but the strands would be developed with bonded construction at the ends of the precast column. This system is potentially an incremental improvement over the HfL precast bent system.
CHAPTER 4. DESIGN AND CONSTRUCTION SPECIFICATION PROVISIONS
Because of the specific requirements of a fully precast concrete bent system in high seismic regions, special design and construction specifications have been developed. The design specifications have been formatted to act as an appendix to the AASHTO Seismic Guide Specifications, and a full draft of these provisions is provided in appendix A of this report. These provisions supplement, and in some cases modify, the AASHTO Seismic Guide Specifications so that the precast components and the entire system are designed such that the system is consistent with the large-scale experimental validation testing. The design specifications include an overview of the HfL precast bent system, the Earthquake-Resisting System (ERS) classification of the HfL system, the local displacement capacity for Seismic Design Categories (SDCs) B and C, the analytical plastic hinge length, and the socket-type foundation connection for both spread footings and oversized drilled shafts.
Additionally, there are specific provisions detailing the design requirements for the following cases, where the bridge falls with SDCs C and D:
- Interface shear transfer between the precast column and cap beam or between segments of precast columns.
- Splicing of longitudinal reinforcement in columns subject to ductility demands.
- Minimum development length of reinforcing steel.
- Lateral reinforcement inside the plastic hinge region.
- Development length for column bars extended into oversized pile shafts.
- Lateral confinement for oversized pile shafts.
- Superstructure capacity design for integral bent caps loaded in the longitudinal direction.
- Cap beam joint proportioning for longitudinal and transverse seismic loading.
- Minimum joint shear reinforcement for both T and knee joints.
- Requirements for horizontally isolated flares.
Additionally, during the design of the demonstration project (described in the next chapter), WSDOT developed special construction specifications (special provisions) to supplement their standard specifications. The following is a list of the special provisions with references to the 2010 WSDOT Standard Specifications for Road, Bridge, and Municipal Construction, which is available for free download at http://www.wsdot.wa.gov/Publications/Manuals/M41-10.htm.
Note that the precast column and cap beam elements were covered under the standard specifications for precast concrete panels, and as such required fabrication by a certified precast concrete fabricator. This requirement had implications on tolerances, quality control, and inspection that were felt reasonable for the demonstration project.
Shop Drawings (Grouted Joint Mock-Up)
The third paragraph of Section 6-02.3(28)A is supplemented with the following:
The Contractor shall submit a grouting operation Plan to the Engineer for approval in accordance with Section 6-02.3(26)H except duct leak tightness testing will not be required.
The Contractor shall construct the grout test joint as shown in the Plans. The test joint shall use the same type and size of shims planned for use in the bridge. The Contractor shall, in the presence of the Engineer, perform the grouting of the test joint per the approved grouting operation Plan. The test joint shall be allowed to cure for a minimum of 3 days, after which the forms and duct plugs shall be removed. The grout coverage in the gap between the top and bottom form and the annular space between the PVC pipe and the metal duct shall be inspected. The test shall be considered successful if the joint and annular space are filled. Results from the test joint shall be used to modify the grouting operation Plan. These modifications may include, but are not limited to, added grout vents, modified grout consistency, change of grout type, and revised joint forms. The modified grout operation Plan shall be submitted for approval. The Contractor shall not proceed with grouting operations to the bridge until a successful test of the grout test joint is completed. The test shall be conducted at least 2 weeks prior to the Contractor’s scheduled bridge grouting.
Casting
Section 6-02.3(28)B is supplemented with the following:
- The precast columns shall be fabricated by the same fabricator as the precast cap beams.
- The precast column segments shall be match-marked.
- The precast cap beam end panels shall be cast using a template from the precast cap beams.
- Ducts shall be semi-rigid, corrugated, galvanized, ferrous metal. The minimum duct thickness shall be 31-gauge.
Erection
Section 6-02.3(28)I is supplemented with the following:
- Grout placed between column segments and column-to-cap beam connections shall be pumpable and conform to Section 9-20.3(2). The minimum compressive strength shall be 6,000 psi at 7 days and 8,000 psi at 28 days. These compressive strengths shall be lab-verified from the field-produced 2-inch cubes.
- The ducts between column segments shall be air flushed prior to grouting.
CHAPTER 5. DEMONSTRATION PROJECT
Following the testing of the spread footing connection, and based on the success of the column-to-cap beam connection, a demonstration project that uses the HfL precast bent system was planned and executed by WSDOT as part of the HfL project. The objective of the project was to demonstrate the constructability of the bent system on a bridge project that would be competitively bid.
The demonstration project is a replacement bridge for the existing US 12 bridge over Interstate 5, a major north-south freeway in Washington State, at Grand Mound. It was built on an alignment parallel to the existing bridge. Interstate 5 at this location had an average daily traffic (ADT) count of 59,000 in 2011, and US 12 had a count of 15,000. The new bridge is a two-span 88-foot-wide structure that has four 12-foot-wide traffic lanes, a 13-foot-wide turn lane, a 5-foot-wide bike lane, and two 6.5-foot-wide shoulders. Aside from the demonstration nature of the project, primary drivers for using ABC techniques for the replacement bridge were reduced traffic impacts, improved site constructability, improved work zone safety, improved material quality and durability, and reduced life-cycle costs. While reduced on-site construction time was also a goal, it was recognized that the unique and new details of construction would probably preclude achieving significant time savings.
Structural Description of the Grand Mound Bridge
The bridge is 176 feet long and crosses the interstate at approximately a 29-degree skew, which provided challenges with regard to the integration of the girders and cap beam. The details of the WSDOT HfL demonstration project are shown in figures 40 through 43, which illustrate the following pertinent bridge design features:
- Precast superstructure with cast-in-place closure at the intermediate pier.
- Precast end and intermediate diaphragms.
- Precast cap beam, made in two segments.
- Cast-in-place precast cap beam closure pour.
- Precast segmental columns, joined by bars grouted in ducts.
- Unique socket connection between the precast column and the footing.
The superstructure consists of fifteen 35-inch-deep decked-bulb tee prestressed girders that span 88 feet. These are supported by the intermediate pier comprised of spread footings, precast column segments, a precast dropped cap beam and a cast-in-place diaphragm. A 5-inch cast-in-place topping is placed over the decked-bulb tees, whose flanges act as stay-in-place forms. The girders are connected with two precast intermediate partial-depth diaphragms per span that were match cast to each girder at the precast facility. Full-depth cast-in-place diaphragms were included at each abutment and at the four-column center bent that is located in the median strip of Interstate 5. To reduce the amount of formwork for the cast-in-place diaphragm at the intermediate pier, each of the girders had precast end walls, which acted as stay-in-place forms.
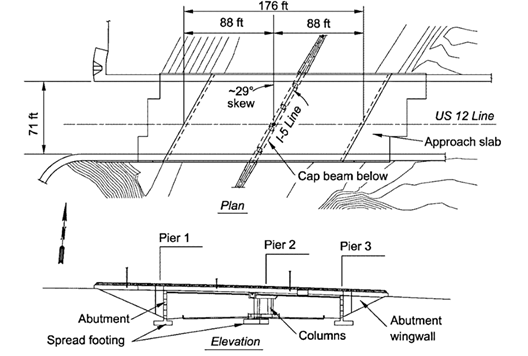
Figure 40. Diagram. HfL demonstration project bridge layout.
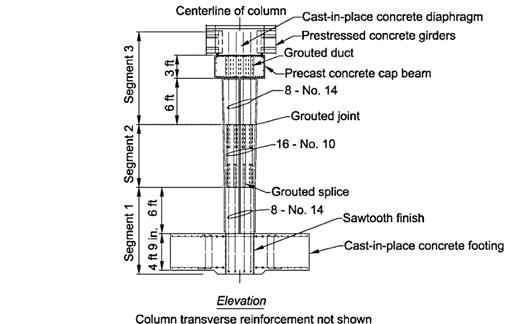
Figure 42. Diagram. HfL demonstration project segmental column elevation.
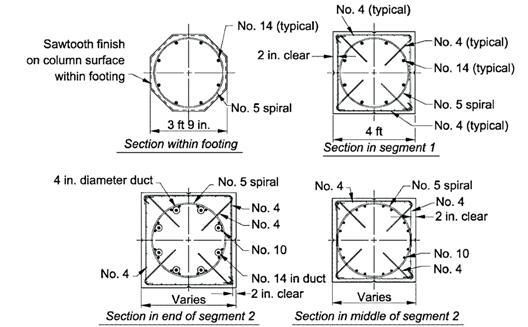
Figure 43. Diagram. HfL demonstration project segmental column sections.
The abutments at each end of the bridge consisted of cast-in-place tall abutment walls with overhanging end diaphragms and adjacent wingwalls on either side. The prestressed concrete girders were placed on top of elastomeric bearing pads that allowed for longitudinal movement of the bridge under seismic and thermal movements. Transverse movement of the superstructure was restricted at each abutment by including cast-in-place shear blocks between each girder.
The precast bent system used in the HfL project relied on the standard Washington State practice of integrating the prestressed girders with the cast-in-place second-stage cap beam. This system provides longitudinal moment transfer from the bent columns, through the cap beam, to the girders. The precast first-stage cap beam for the demonstration bridge was built in two pieces that were integrated with a closure pour at the crown point. This was required because the bridge is 84 feet wide, including sidewalks. Ideally, the precast first-stage cap would be built as a single piece to avoid the time required for splicing segments, but lifting and shipping weight restrictions led to the two-piece solution in this case. This decision could, of course, vary by project. The first-stage cap beam included straight prestressing steel to prevent cracking under shipping and construction loading.
The columns used in this project were spliced to permit erection in segments. While the columns of the demonstration project were small enough to be handled as a single piece, the segmental concept was used to demonstrate the technology for use on other projects where the columns are longer and cannot be transported or lifted as a single piece. The configuration of the spliced column and sections through each individual piece is shown in figures 42 and 43.
Also seen in figure 42 is the detail of the socket connection at the footing. Note that a slightly depressed center section of the footing was used to ensure that the reinforcement heads on the column bars extended below the bottom mat of reinforcement in the footing. This detail is important to ensure that a robust strut-and-tie mechanism can form as part of the column and footing joint shear force-transfer mechanism. The additional depth required in the center of the footing is not difficult to construct, as only a little extra soil is removed in this area of the footing excavation. The cover on the bottom mat of reinforcement then is just a little larger in this area.
Figure 43 shows the various cross-sections used along the length of the column. The full length of the column segment that was embedded into the cast-in-place footing used an octagonal section with saw-tooth roughening. This enhanced the constructability of the column roughening during precasting. The octagonal section extended 3 inches above the top of the footing, which allowed for the column plastic hinge to behave roughly as a circular section without any bidirectional bending effects present in a rectangular or square section. A similar detail was used at the top of the column, where the 3 inches of the column adjacent to the soffit of the cap beam was reduced to a 4-foot-diameter circular section.
Above the octagonal section the column was expanded to a 4-foot square section for architectural reasons. For the first 6 feet (i.e., the remaining length of column segment 1) the column sides were parallel, and then they changed to a 1:48 outward taper for segments 2 and 3. The reinforcement in segments 1 and 3 consisted of 8 No. 14 longitudinal bars and a No. 5 spiral with a 4-inch pitch, while segment 2 was reinforced with 16 No. 10 longitudinal bars with a No.5 spiral at 4-inch pitch. The grouted splice between the column segments was created by the extension of the No. 14 bars from segments 1 and 3 into corrugated metal ducts cast into the ends of segment 2. A non-contact lap splice was made, with the No. 10 bars in segment 2 being placed as close as possible to the metal ducts.
The details of the precast bent system connections used in the demonstration project were essentially identical, apart from scale, to those tested and proven effective in the laboratory.
Design Considerations
The design of a fully precast bent system for high seismic regions required special attention to a number of design components to ensure adequate performance and enhanced constructability. Special considerations were made in to following areas:
- Cap beam joint region detailing for both the longitudinal and transverse directions of loading.
- Prestressing of the stage one cap beam for transportation and construction handling stresses.
- Two-piece cap beam to limit transportation weights to those local precast trucking subcontractors could carry, and to render the lower cap beam determinate for its self-weight.
- Location of the closure within the cap beam to reduce flexural demands (i.e., locate near an inflection point), along with detailing of the closure region due to congestion issues.
- Stirrup placement in the cap beam due to the skew and the position of the prestressed girders.
- Orientation of ducts at the column splices so that they do not extend into the plastic hinge regions of the columns.
- Joints at the top and bottom of the columns where the section is transitioned from square to circular sections so that the column response is symmetric about all directions.
- Termination of additional reinforcement in the column (i.e., those provided based off of maximum longitudinal bar spacing requirements) at the plastic hinge zone to prevent increased column overstrength.
- Extending longitudinal column bars through the stage one cap beam into the stage two cast-in-place diaphragm to provide a complete and robust load path from the substructure to the superstructure.
- Continuity of girder prestressing strands across the stage two cap beam by means of mechanical strand anchors, overlap of the prestressing strands, and/or strand “dog-bones.”
- Anchorage of column bars below the bottom mat of the footing reinforcement to develop a robust load path from the column to the spread footing.
- Roughness of shear friction surface for the socket connection to provide adequate axial resistance and prevent the column punching through the footing.
- Additional shear friction reinforcement within the spread footing to provide the needed normal “clamping” force on the column to develop the previously mentioned shear friction resistance.
- Grout materials to allow sufficient flowabilty, pumpability, and strength.
- Tolerances.
- Precast/Prestressed Concrete Institute (PCI)-certified precaster.
Most of these special design considerations are explained in significant depth in appendix B, while the remaining items are discussed in either this report or appendix C.
Procurement
The demonstration project bridge was procured by traditional design-bid-build methods. There were no incentives or disincentives given to the contractor for the project. The contractor was required to build the structure as shown on the bid documents and was not permitted to initiate change proposals that eliminated the key demonstration elements of the project. For example, the segmental column was required even though single-piece columns could have been used for this application. There were 15 bidders for the project, indicating a competitive bidding climate at the time. The engineer’s estimate for the bridge portion of the project was $3.05 million, and the low bid for this portion was $2.46 million. The cost of the bridge in terms of square footage of deck was $160, including mobilization and approach slabs, compared to $211 per square foot of bridge deck for conventional construction in this region in 2011. The bid price for the precast beams was $1,500 per lineal foot and $1,200 per lineal foot for the columns. The costs were not analyzed in order to separate elements such as the competitive bid climate from potential cost impacts of the precast bent construction.
Construction
Because the primary benefit of the fully precast bent system is the reduced construction time, this section will outline the construction steps required to fully construct the HfL bridge system. Prior to beginning erection of precast elements on-site, several requirements were imposed on the contractor. First, to ensure the contractor’s capability to perform critical grouting operations, the contractor was required to create a mock-up of the grouted lap splice joint between column segments. This was to demonstrate that they were able to adequately pump the grout so that the bedding layer between the column segments and the annular space within the corrugated metal ducts were filled without voids according to the specifications. This was accomplished using a plywood dummy joint as shown in figure 44, where the square plywood base includes a 48-inch square 1-inch-thick bedding layer. Inside of the 4.5-inch-diameter corrugated metal tubes were 1.5-inch PVC pipes to represent No. 14 reinforcing steel. The grout was pumped into the joint using the lower tubes.
Secondly the construction specifications required that the same precaster builds all of the column segments, the stage one cap beam, and the prestressed concrete girders. This was to ensure that adjacent precast elements were compatible and coordination issues were easily resolved. Finally, at this stage of construction, it was decided that the end walls (which acted as stay-in-place forms for the stage-two cap beam at the intermediate pier) and the intermediate diaphragms were match cast onto the prestressed concrete girders at the precast facility. This was done in an effort to reduce the amount of formwork required on-site.
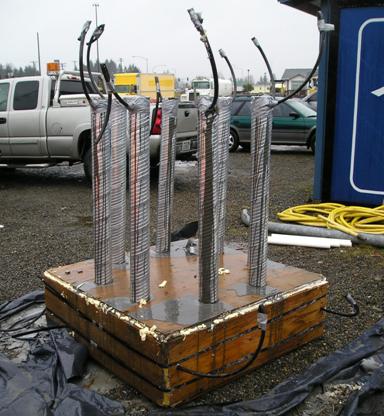
Figure 44. Photo. Mock-up of the grouted joint.
After the preconstruction items were taken care of, construction of the precast intermediate pier could begin with the construction of the spread footings and the socket connection from the column to the footing. The steps in the construction sequence for the column-to-footing connection are listed below:
- Excavate for footing and install forms.
- Place leveling pad and set first segment of column.
- Place footing reinforcing and cast footing concrete.
- Remove forms and backfill around the excavation.
Figure 45 illustrates this construction sequence. In the photo, an erection frame, which was built of hollow structural sections (HSS) and was developed by the contractor to assist in both positioning and bracing the column, can be seen.
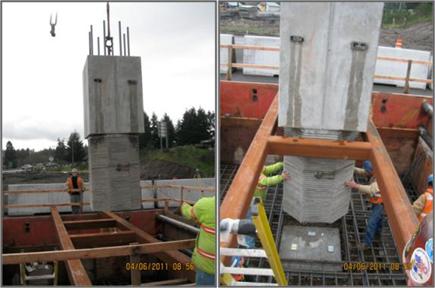
Figure 45. Photos. Construction sequence for placement of first precast column segment.
The next stage of construction was the erection of the columns and the precast stage one bent cap, the steps of which are listed below and are shown in figures 46 and 47:
- Place and shim middle column segments.
- Place and shim top column segments.
- Install column bracing.
- Place and shim precast bent cap segments.
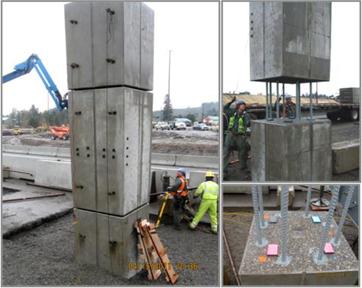
Figure 46. Photos. Construction sequence for placement of the column segments.
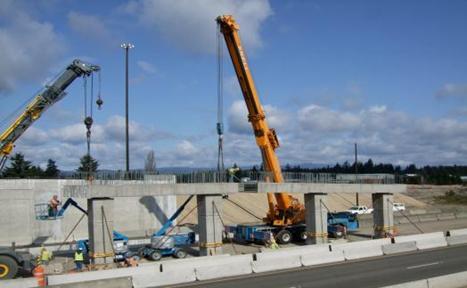
Figure 47. Photo. Precast cap beam placement.
The joints between column segments and the column to bent cap were all grouted at one time. The process included the following steps and is illustrated in figure 48:
- Install grout forms and seal.
- Pump grout and close grout tubes.
- Remove grout forms and inspect grout in joint and grout tubes.
- Repair unfilled grout tubes and patch back grout tubes.
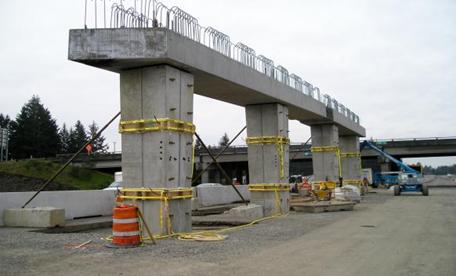
Figure 48. Photo. Grouting the joints between column segments and between columns and cap beam.
Due to the relatively small size of the column and precast cap beam segments, all pieces on this bent had to be stacked and braced before any joint grouting could be conducted to provide the necessary dead weight to offset the grouting pressures. This would not necessarily be the case if larger segments were required, such as when taller column segments are used. In those cases, intermediate grouting steps would be necessary to ensure structural stability during construction.
The construction sequence for placement of the precast superstructure at the intermediate pier is listed below and shown in figure 49:
- Place precast girders on oak blocks.
- Install girder bracing if necessary.
- Complete welded ties between girders.
- Grout intermediate diaphragms and join flange shear keys.
- Place slab reinforcement and cast concrete.
- Cast pier diaphragm concrete 10 days after slab casting. Note that each deck-bulb tee was fitted with a precast end wall, with the intent of reducing the amount of formwork needed.
- Cast traffic barrier and sidewalk.
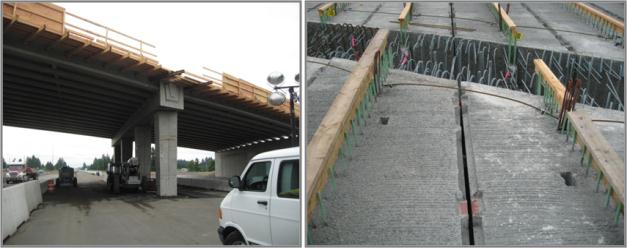
Figure 49. Photo. Placement of precast girders and preparation for deck slab topping concrete.
Figure 50 is a photo of the completed bridge.
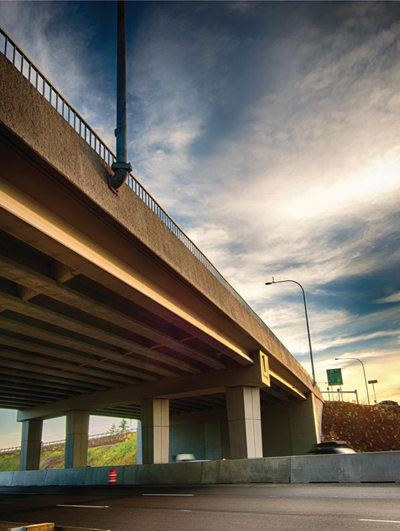
Figure 50. Photo. Completed demonstration bridge (photo courtesy of the Precast/Prestressed Concrete Institute).
Lessons Learned and Contractor Feedback
Eric Schultz, the WSDOT bridge designer, met with the contractor and the project office staff at the contractor’s job site office and discussed the constructability of each of the individual stages for the precast elements of pier 2. Schultz framed the conversation by saying that WSDOT intends to use these precast techniques where there is limited access and a limited construction time window. The contractor was asked to provide comments on each of the construction elements, starting with the footing.
Footing
The contractor’s staff (contractor) felt that this portion of the construction was straightforward. They indicated that they would use a shoring box again if they had the choice and that this worked well even though their shoring box was slightly undersized. They felt the use of the shoring box helped speed up the work. When specifically asked about placing the column and then footing reinforcing around the column, the contractor said they liked the configuration especially because no reinforcing bar needed to be threaded through or underneath the column. The contractor noted that they had concerns about controlling the elevation of the column. They said it was difficult to determine where to make an accurate measurement from. It is suggested that small metal tabs could be placed near the top of the column that could be used to make more accurate measurements. Some thought this might help, but not all were in agreement.
Column Segments
The contractor indicated that they would have preferred the columns to be cast-in-place; however, they could see the benefit to using a single precast column with the grout connection at the cap beam only. This would eliminate the cure time for the column concrete and require bracing for only 1 day. With the installation of all the segments and cap beam prior to grouting, the contractor needed to provide bracing for an extended amount of time. However, even with this bracing, the process was simpler than erecting individual segments and grouting them before moving on to the next segment. If taller columns were being built with this technique, intermediate grouting operations would be required.
It is essential to recognize that the segmental concept was used on the demonstration project solely to demonstrate feasibility of the concept. For columns of the size used here, single-piece columns would be the preferred method of for the precast bent concept. The same contractor proposed and used single-piece columns virtually identical to the HfL columns, as shown in figure 51, for the 36th Street Bridge in Redmond, Washington. There were 14 of these columns placed in the center pier of this bridge, which was in the median of a divided highway. The use of the precast columns saved approximately 1 month of time on the project.
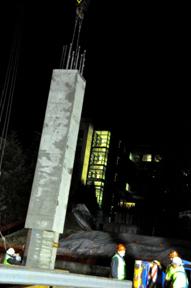
Figure 51. Photo. Single-piece column used on the 36th Street Bridge in Redmond.
Grouted Column Joints
The contractor preferred the joints that had the ducts in the lower section. They indicated that all the joints where the ducts were below the joint were grouted without any leaking. They believe that this configuration made it so there were lower grout pressures on the forms, since the forms did not have to resist the pressure head from the ducts. The superintendent suggested that the joint be sealed by having something like a compression seal that was sandwiched between the top and bottom segments and would be held in place by the weight of the segment on top. It should be noted that having the ducts within the lower column segment would only be feasible in locations where the entire splice was outside of the plastic hinge region as defined by the AASHTO Seismic Guide Specifications. Such a configuration would not have worked between column segments 1 and 2 for this demonstration project. If longer column segments were used, this may not be an issue.
The problem with sealing the column joints is largely one of not having the right concept. The grout forms, as constructed, were not stiff enough to maintain a good seal all the way around the column (see figure 52). A form that would produce an adequate seal could be designed fairly simply. This is an example of a problem that will disappear once the construction technique is applied several times.
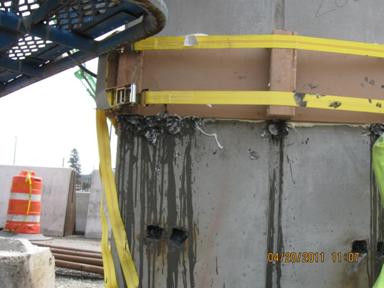
Figure 52. Photo. Difficulty with sealing the column segment joint during grouting.
The contractor was then asked if they thought tighter tolerances on the column segments would have helped in sealing the joints. They responded that this could cause delay in fabrication, and that they would suffer time delays for segments that had to be remade or repaired.
Finally, the contractor felt that the grouted joint between the column and the cap beam was the easiest to construct, although they would have preferred to have a deeper bedding layer for the joint. There are structural reasons to keep this joint as small as possible, since it was in the plastic hinging zone, and if the joint was too large, hoop reinforcing for confinement would need to be added to the joint. Regardless, the contractor preferred this joint to all others, as it was the easiest to construct.
Cap Beam
The contractor’s concern here was that the lap splice between the two cap beam segments would be difficult to align properly due to the congestion of the reinforcement, as shown in figure 53. WSDOT asked about the alignment of the ducts in the cap beam and whether the contractor had any explanation as to why the ducts did not center well around the longitudinal bars from the column. The contractor did not have a specific reason, other than to point out all the tolerances that could add to alignment error (column tolerances, bar placement in the columns, orientation of the columns, cross-slope of the cap beam, placement of the ducts in the cap, slope of the ducts in the cap, etc.).
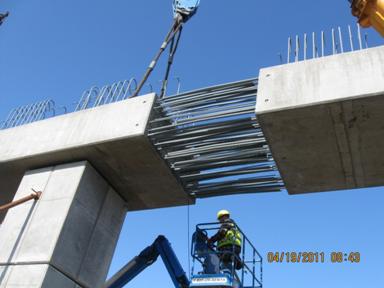
Figure 53. Photo. Lowering the second lower-stage cap beam into place.
Cap Beam Closure
It was apparent during the installation of the stirrups in the cap beam closure that the stirrups should have been detailed as ties. It was nearly impossible to install the stirrups as shown in the plans, so a modification to the stirrups was made. The stirrups should be detailed as three interlocking ties, instead of U-shaped stirrups, to facilitate placement. The contractor indicated that the closure was very congested (see figure 54) and would have preferred to use a pea gravel concrete mix design to make it easier to place and consolidate. They thought the hanging form work was simple and easy to construct.
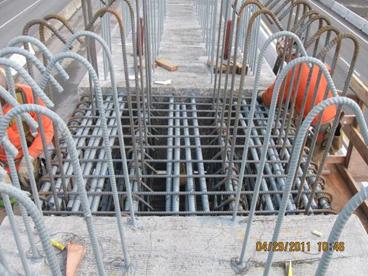
Figure 54. Photo. Lower-stage cap beam closure prior to concrete placement.
Girder End-Wall Diaphragms at Pier 2
The contractor felt that the 5-inch-thick precast walls at the pier 2 cap beam were not that useful. They indicated that they still needed to install formwork at the bottom of these walls to the top of the lower cap beam and around the oak blocks (see figure 55). The contractor felt that this diaphragm pour would be much simpler if it was cast-in-place, and it would take the same amount of time to construct with or without the end walls. They also suggested that the precast end panels were not helpful in speeding up the work and, similarly, they would prefer this to be cast-in-place, since they had to make forms anyway.
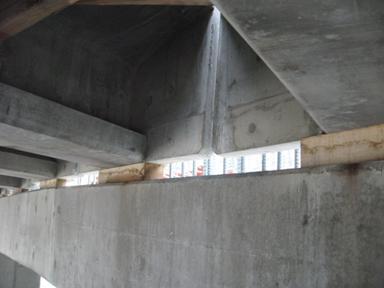
Figure 55. Photo. Girder end wall diaphragms and girders on oak blocks.
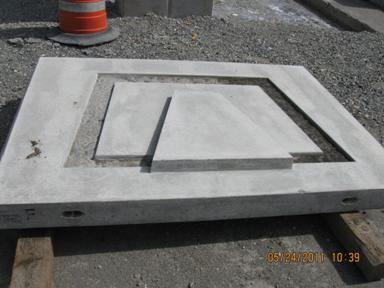
Figure 56. Photo. Precast end panel.
Precast Intermediate Diaphragms
The precast intermediate diaphragms were connected with a grouted joint. The horizontal reinforcement consisted of headed bars projecting from the ends of the diaphragms into the joint where a notched HSS section captured the heads and provided load transfer. During construction, the precaster mentioned that these bottom double-headed bars were supplied in one piece that ran horizontally through the girder and into the diaphragm joints at each end. The tolerances on the length of these bars were not very tight and, as a result, there was difficulty in providing the specified extension during match casting of the diaphragms. Additionally, because of the variable elevation of the top of the cap beam, the vertical alignment was difficult to control. Despite this, the horizontal alignment of the diaphragms was well controlled.
CHAPTER 6. DESIGN EXAMPLE OVERVIEW
As part of the final deliverable package for the HfL precast bent system for high seismic regions, two design examples were developed to illustrate the pertinent design considerations. The design examples show how to apply the provisions of the AASHTO Seismic Guide Specifications to a fully precast bridge in conjunction with the design provisions generated as a part of this project (discussed in chapter 4). Particular emphasis is given to the design and detailing of the connections between precast elements to ensure ductile energy dissipating behavior within the plastic hinge regions of the columns and capacity protection throughout the remainder of the structure.
The two design examples use actual bridges that have recently been designed by WSDOT. The first design example uses the US 12 bridge over Interstate 5 at Grand Mound (the demonstration project described in chapter 5), and the second design example uses the US 101 Bone River Bridge replacement near Raymond. Design example 1 is detailed in appendix B to this report, and design example 2 is detailed in appendix C.
The new Bone River Bridge is a replacement for the existing two-lane crossing, which was built in 1935 using timber trestles. The new bridge is a three-span structure, with the two-column intermediate bents and the short-stem seat abutments each supported by two oversized pile shaft foundations. The superstructure consists of four prestressed concrete wide flange girders, which was made continuous at the integral dropped cap beam at the intermediate piers. The precast concrete columns were connected to the pile shaft foundations using a socket connection similar to the large-scale laboratory tests described earlier in this report.
The first design example covers the following areas:
- General seismic design and analysis philosophy in the AASHTO Seismic Guide Specifications.
- Structural seismic demand analysis using an elastic centerline bridge model, a multimodal response spectrum analysis, and the coefficient method of predicting the nonlinear displacement demands.
- Structural capacity analysis (i.e., pushover analysis) including the development of nonlinear moment-curvature and axial load-moment (P-M) interaction relationships, plastic hinge definition, and the displacement capacity of the system.
- Plastic design forces.
- Displacement capacity to demand ratios.
- Individual member ductility demands.
- Column plastic hinge shear capacity to demand ratios.
- P-Δ effects.
- Required support lengths at the abutments.
- Capacity protection of the following members or components:
- Superstructure (precast prestressed concrete girders).
- Prestressed concrete girder strand development at the intermediate pier to provide continuity of the girders.
- Shear blocks at the abutments to resist transverse design forces.
- Precast cap beam for seismic as well as construction, transportation, and erection loading.
- Column to cap beam connection and joint design with an emphasis on the special considerations particular to an integral dropped cap beam.
- The splice between column segments.
- The column to cast-in-place spread footing socket connection.
- Constructability considerations such as shipment and crane pick weight restrictions, fit-up between precast elements, tolerances, and construction sequence.
The second design example focuses almost exclusively on the connection between a precast column and a cast-in-place oversized pile shaft. This example has a reduced scope compared to the first example, as all of the other design considerations are principally the same for the two bridges, and a full treatment in the second example would be redundant.
CHAPTER 7. CONCLUSIONS AND RECOMMENDATIONS
The goal of this project was to bring emerging technology for ABC connections in two-stage cap beam bent construction in seismic regions to a deployment-ready stage. Previous laboratory testing indicated that seismic ABC technologies were feasible for column-to-cap beam connections. This HfL project extended that work to connections at the bottom of the column. With successful proof testing of the lower connection, a demonstration project was selected, designed, and constructed using the precast bent system.
A working group of DOT personnel, contractors, precasters, academic researchers, and consultants was formed to guide the final development and design of the bent system. This group was highly effective in providing and vetting the details of the design and construction. The contractor constructed the final product without significant difficulty. Because this was the first such bent constructed, and because a proof-of-constructability spliced column was used, no significant data were developed on likely time savings. However, it is, clear that time savings are possible, mainly because the cap beam can be erected quickly.
The lessons learned and guidance that emerged from the working group will provide valuable guidance to subsequent projects that choose to utilize this system. Currently, such systems are bid as alternates to cast-in-place construction, and contractors used to building cast-in-place bents are not keen to use the new system. Based on what was learned in the demonstration project, it is expected that such reluctance will diminish as contractors become used to constructing the bent system. It may therefore be necessary for the owner to incentivize or even require the system be used when it makes sense within the overall ABC decision framework.
With the design tools developed and accompanying this report, designers have the necessary tools to design precast two-stage bents in moderate-to-high seismic zones. Inasmuch as owners must agree to use this system, the system would fall under the “Permissible Elements that Require Owner’s Approval” category of the AASHTO Seismic Guide Specifications.
The system provides seismic performance in terms of damage levels, energy dissipation, and overall behavior that is emulative of reinforced concrete bent construction. This was shown for the various connections in the proof tests reported herein. While the testing provides evidence of acceptable seismic performance, several additional tests have been proposed in this report. Some of those tests are underway currently, and these are an additional column-to-drilled shaft test and a pretensioned column test. However, a longitudinal test of a full bent and girder system would be highly desirable to confirm the behavior of the entire bridge system. Such tests would be relevant not only for this precast bent system, but also for cast-in-place bents with prestressed girder superstructures.
The project demonstrates that a focused, collaborative effort between an owner, researchers, designers, and constructors resulted in a viable system that can be deployed to resolve the seismic challenges and provide significant benefits to accelerate bridge construction. The resulting bent system is a valuable contribution to bridge engineering and construction, and the path taken, the team that traversed it, and the support provided by FHWA combine to illustrate an effective manner of bringing new technology to market.
REFERENCES
- Marsh, M., Wernli, M., B.E.Garrett, J.F.Stanton, M.O.Eberhard, and M.D.Weinert. (2011). NCHRP Report 698 Application of Accelerated Bridge Construction Connections in Moderate-to-High Seismic Regions. Washington, D.C.: National Cooperative Highway Research Program, Transportation Research Board.
- Khaleghi, B. (2010). Washington State Department of Transportation Plan for Accelerated Bridge Construction. Transportation Research Record No. 2200, Washington D.C.: Transportation Research Board of the National Academies, pp. 3-11.
- AASHTO. (2011). AASHTO Guide Specifications for LRFD Seismic Bridge Design (Second ed.). Washington, DC: American Association of State Highway and Transportation Officials.
- AASHTO. (2010). AASHTO LRFD Bridge Design Specifications (Fifth ed.). Washington, DC: American Association of State Highway and Transportation Officials.
- Steuck, K., Stanton, J., and Eberhard, M. (2009). Anchorage of Large-Diameter Reinforcing Bars in Ducts. ACI Structural Journal, Volume 106, No. 4, pp. 506-513.
- Eberhard, M., Pang, J., Stanton, J., and Steuck, K. (2009). WA-RD 684.1 Anchorage of Large-Diameter Reinforcing Bars Grouted Into Ducts. Olympia, WA: Washington Department of Transportation.
- Pang, J., K.P.Steuck, L.Cohagen, Stanton, J., and Eberhard, M. (2008). WA-RD 684.2 Rapidly Constructible Large-Bar Precast Bridge-Bent Seismic Connection. Olympia, WA: Washington State Department of Transportation.
- Pang, J., Eberhard, M., and Stanton, J. (2010). Large-Bar Connection for Precast Bridge Bents in Seismic Regions. ASCE Journal of Bridge Engineering, Volume 15,No. 3, pp. 231-239.
- Raynor, D., Lehman, D., and Stanton, J. (2002). Bond-Slip Response of Reinforcing Bars Grouted in Ducts. ACI Structural Journal, Volume 99,No. 5, pp. 568-576.
- Nakaki, S., Stanton, J., and Sritharan, S. (1999). Overview of the PRESSS Five Story Precast Test Building. PCI Journal, Volume 44,Number 5, pp. 26-39.
- Osanai, Y., Watanabe, F., and Okamoto, S. (1996). Stress Transfer Mechanism of Socket Base Connections with Precast Concrete Columns. ACI Structural Journal, Volume 93, No. 3, pp. 266-276.
- AASHTO. (2009). AASHTO LRFD Bridge Design Specifications (4th ed., 2009 Interim Revisions). Washington, DC: American Association of State Highway and Transportation Officials.
- AASHTO. (2009). AASHTO Guide Specifications for LRFD Seismic Bridge Design (First ed.). Washington, DC: American Association of State Highway and Transportation Officials.
- WSDOT. (2008). Bridge Design Manual (LRFD) M23-50.02. Olympia, WA: Washintgon State Department of Transportation.
- Caltrans. (2006). Seismic Design Criteria Version 1.4. Sacramento, CA: California Department of Transportation.
- Haraldsson, O., Janes, T., Eberhard, M., and Stanton, J. (2013). Precast Bent System for High Seismic Regions - Laboratory Tests of Column-to-Footing Socket Connections FHWA-HIF-13-039. Washington DC: Federal Highway Adnimistration.
- Hung, V., Stanton, J., and Eberhard, M. (2013). Precast Bent System for High Seismic Regions - Laboratory Tests of Column-to-Drilled Shaft Socket Connections FHWA-HIF-13-038. Washington DC: Federal Highway Adnimistration.
- WSDOT. (2012). Bridge Design Manual (LRFD) M23-50.12. Olympia, WA: Washintgon State Department of Transportation.
- McLean, D., and Smith, C. (1997). Noncontact Lap Splices in Bridge Column-Shaft Connections WA-RD 417.1. Olympia: Washington State Department of Transportation.