Innovative Field-Cast Uhpc Joints For Precast Bridge Decks
Innovative Field-cast UHPC Joints for Precast Bridge Decks (Side-by-Side Deck Bulb-Tees), Village of Lyons, New York: Design, Prototyping, Testing and Construction
3rd fib International Congress - 2010
Vic H. Perry, FCSCE, MASc., P.Eng, Lafarge North America, Calgary, AB, Canada
Mathew Royce, P.E., New York State Department of Transportation, Albany, NY, USA
- Abstract
- Introduction
- Investigating and implementing the use of UHPC for joint fill in precast bridge decks
- Concept and design parameters for panels and joints
- Characteristics of UHPC jointing material technology
- Strength durability
- Phase I: prototype and test panels with UHPC joint fill in a laboratory
- Phase II: use of UHPC joint fill in side-by-side deck bulb-tees
- Conclusions
- References
Abstract
Critical bridge components are often replaced during limited or overnight road closures. This paper presents the development, testing and installation of precast, high performance concrete bridge elements with field-cast ultra-high performance concrete (UHPC) Joint Fill for projects in New York State. Fundamentals of the technology, material properties, design, manufacturing, prototyping, load testing, erection and a project overview are included. By utilizing UHPC's combination of superior properties with precast bridge deck panels, deck performance is advanced and improved. Benefits include reduced joint size and complexity, improved durability and continuity, speed of construction, elimination of post-tensioning and extended usage life. This innovative joint design eliminates problems associated with joints in precast bridge decks and is now the strongest link in the precast bridge deck system.
Keywords: Composite, Ductile, Durability, Joint Fill, Precast, UHPC.
Introduction
Every day, bridge engineers face the challenge of ever increasing traffic volume and loadings on aging bridge infrastructure with reducing budgets and users demanding less inconvenience during maintenance or repairs. The result is demonstrated by the USA Federal HighWay Administration (FHWA) data which rates over 150,000 bridges categorized as structurally deficient and functionally obsolete1. Transportation authorities are faced with replacing or repairing these critical bridge components during strictly limited or overnight road closures. This paper presents a solution that will help bridge engineers, owners and users.
One of the largest and specific challenges facing bridge authorities is the long-term durability of bridge decks which receive continuous impact loading from trucks and changing environmental conditions. The years of continuous flexural and thermal stresses and exposure to corrosive elements create long-term deterioration and maintenance issues for bridge decks. While Cast-In-Place (CIP) concrete decks with High-Performance Concrete (HPC) and corrosion resistant reinforcement can significantly extend the deck life, it creates high user inconvenience and is problematic for bridge deck replacement in high traffic areas. The use of HPC precast deck panels is a common method to speed construction and reduce the user inconvenience; however the jointing of the precast system is a source of potential maintenance or even failure.
The use of Post-Tensioning (P/T) across the joints has been used as a method to ensure the deck effectively remains structurally monolithic while performing under the constant pounding of truck wheel loads and seasonal conditions, more specifically; to ensure the joint does not deteriorate or leak. While post-tensioning can resolve most of the performance issues, it is not without potential problems. It is expensive, requires specific expertise and equipment for installation; it has potential for corrosion and is not practical for slabs with a cross slope. Furthermore, the analysis is complex in terms of the correct post-tensioning forces (# of strands and forces longitudinal vs transverse), creep losses, grout properties, potential long-term corrosion of the strands, sequencing of P/T vs anchoring of the panels to the superstructure girders and introduction of post tensioning forces into the girders.
The introduction of new methodologies and innovative material technologies facilitates the implementation of new solutions. One new technology helping to solve the problem with deteriorating bridges is an ultra-high performance, fiber reinforced cement composite material which offers superior technical characteristics including ductility, strength and durability while providing highly moldable products, with a high quality surface aspect and a short bond development length.2,3 Ultra-high performance concrete (UHPC), when used as a jointing material in conjunction with reinforced high performance concrete (HPC) panels, provides a synergistic, new approach for reconstruction of bridge superstructures.
In 2008, the New York State Department of Transportation (NYSDOT) decided to investigate the use of UHPC joint fill with full-depth precast deck panels a new solution for replacement of deteriorating highway bridge decks. The solution was to use a precast
concrete deck panels with field-cast UHPC joints to develop the continuity in the deck panels. While this type of solution had been tried on an experimental basis in 2005 by the Ontario Ministry of Transportation (MTO), the NYSDOT decided to investigate the use of this solution for rapid replacement of bridge decks in high traffic areas4.
Utilizing the superior characteristics of the material technology enables the simplification of the precast panel fabrication and installation processes. This simplified design provides the owner with improved tolerances, reduced risk, increased speed of construction, an overall cost savings in construction and a more durable, longer lasting bridge deck solution.
Investigating and Implementing the Use of UHPC for Joint Fill in Precast Bridge Decks
The use of precast bridge deck systems by NYSDOT is not new. The issues with joints as well as the advantages of a precast deck system manufactured in a plant controlled environment compared to field-cast decks are well understood.
NYSDOT recognized that the properties of UHPC as a joint-fill material combined with precast decks holds great potential to address many concerns that bridge engineers have with respect to precast deck systems, such as the maintenance of joints in the precast system due to constant impact and flexing from truck traffic.
In 2008, the NYSDOT undertook an investigation to evaluate UHPC joint fill with precast bridge deck panels. While UHPC has been used on a limited basis in North America over the past ten years, its first use as a joint fill material in bridges was in 2006 at Rainy Lake, Ontario, Canada4. Therefore, the NYSDOT created a development program in order to investigate, prototype and test UHPC in bridge decks for the NY state highway system. The program has 4 phases:
Phase I: Prototype and test panels with UHPC joint fill in a laboratory.
Phase II: The use of UHPC joint fill in side-by-side Deck Bulb-Tees.
Phase III: The use of UHPC joint fill in full-depth precast deck panels on a single span, two-lane rural bridge.
Phase IV: The use of UHPC joint fill in full-depth precast deck panels on a large scale bridge.
This paper covers the preliminary results of Phase I and II only. Subsequent papers will cover final reporting of Phases I and II, plus Phases III and IV.
Concept and Design Parameters for Panels and Joints
The concept to be implemented by NYSDOT was full-depth precast panels with UHPC joint fill in order to provide continuity (Figures 1 & 2). The precast deck panels are supported on steel or precast beams with grouted shear pockets for composite action through shear transfer between the beams and deck (Figure 3).
The challenge facing designers and owners when utilizing full-depth precast bridge deck panels is durability of the joints due to the constant flexing from truck loadings, thermal movements and corrosion from salt of the rebar crossing the joints. The design of the joints focused on balancing a joint detail that provided deck continuity for loads, minimized traffic disruption during installation, speed of construction and long-term performance5,6.
Precast deck panels are manufactured in a controlled environment, which facilitates the consistent batching vs time of placement, curing, temperature, release of forms and handling; all which help to provide a product that is of consistent strength, durability and geometry, with dimensional stability.
The precast production method enhances controlled handling to eliminate accidental cracking due to early or improper loading. Additionally, precast deck panels are cured and demoulded to reduce the potential for cracking from moisture loss or external restraint. Precast deck panels not only have improved quality, low permeable concrete materials and mixes, they have reduced cracking due to the elimination of field shrinkage coupled with the restraint from supporting girders.
The full-depth precast panels specified by NYSDOT are designed with HPC and use epoxy coated or galvanized rebar to provide a panel with extended usage life. The NYSDOT standard specification for this type of panel is a minimum of 35 MPa (compressive strength) and maximum water-cement ratio of 0.40, for durability. The panel reinforcement design was based on continuity through the joints. The top surface of the concrete panels is sealed with a penetrating type sealer for additional corrosion resistance.
The UHPC joint material was assumed to provide sufficient bond development to allow full continuity of the rebar, as if it were continuous through the joint. Previous testing has shown that the bond development length of a 13 mm bar in UHPC is less than 75 mm4.
The UHPC joint fill material has excellent bond development length, superior freeze/thaw resistance, extremely low porosity, high flexural strength and superior toughness, which provides improved resistance to climatic conditions and continuous flexing from truck loadings across the joints. With previous projects, field-casting of monolithic UHPC joints in excess of 25 m showed no signs of shrinkage, cracking or leaking4. For more information on the material properties, see page 6 ("Characteristics of UHPC Jointing Material Technology").
Even though autogenous shrinkage of UHPC is significant by keeping the joint width small (152 mm), the total shrinkage across the joint is 0.09 mm. Experience on the New York projects show that the total shrinkage is distributed throughout the system and the UHPC/ HPC deck interface is bonded with no potential for leaking.
To minimize this corrosion potential, a non-corrosive rebar (epoxy coated or galvanized) was used. Additionally, the joint size is minimized to provide the least possible total shrinkage across the joint. Minimizing the joint size also reduced the quantity of jointing material to be cast on-site and simplified the precast panel manufacturing. Additionally, to enhance the bond between the precast panel and the joint fill, the surface of each HPC precast panel was soaked to saturated surface-dry (SSD), prior to casting the joint fill. A 40 mm concrete overlay could be provided to assure durability and provide a smooth riding surface. Diamond grinding the top surface is also possible to obtain a good riding surface.
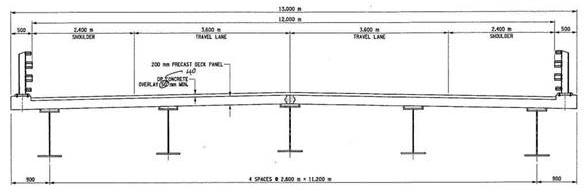
Fig. 1 Transverse Bridge Section of Precast Panels and Centerline UHPC Joint Fill5
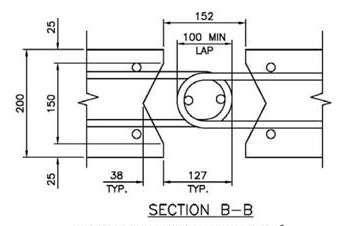
Fig. 2 Detail of Centerline Joint6
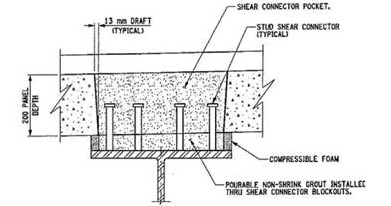
Fig. 3: Detail of Shear Pockets5
Characteristics of UHPC Jointing Material Technology
Ultra-High Performance Concrete (UHPC) is defined as a Portland Cement fiber composite, having minimum characteristic design values of 140 MPa compressive strength, 3 MPa direct tensile strength, in order to achieve a ductile behavior (non-brittle failure) under compression and tension, thereby dispensing with passive (non-prestressed) reinforcement.
The UHPC technology utilized for the joints in this project is an ultra-high-strength, ductile material formulation made with constituent ingredients such as: Portland cement, silica fume, quartz flour, fine silica sand, high-range water reducer, water and steel fibers. Compressive strengths for bridge applications can range from 120 to 200 MPa and flexural strengths range from 15 to 40 MPa.
The material's high mechanical properties are a result of proportioning the constituent ingredients to produce a modified compact grading with a nominal maximum coarse aggregate size of 400 µm, and a high tensile strength steel fiber with a geometry of 12 mm X 0.2 mm. The ratio of maximum coarse aggregate size to fiber is important to facilitate random orientation of fibers and a ductile behavior. These performance characteristics result in improved micro-structural properties of the mineral matrix, especially toughness and control of the bond between the matrix and fiber.
With a carbonation depth penetration of 0.5 mm, there is almost no carbonation or penetration of chlorides or sulphides and a high resistance to acid attack. The superior durability characteristics are due to low porosity from a combination of fine powders, selected for their relative grain size (maximum 0.5 mm) and chemical reactivity. The net effect is a maximum compactness and a small, disconnected pore structure.
The material's ultra-high strength properties and low permeability also provide excellent protection of the rebar against corrosion and improved bond with the rebar, thereby providing short bond development lengths.
The following is an example of the range of material characteristics for UHPC Joint Fill7:
Strength Durability
Compressive (28 days) 140 MPa Freeze/thaw (after 300 cycles) 100% Compressive (48 hours) 100 MPa Salt-scaling (loss of residue) <0.10 g/m2 Flexural 30 MPa Carbonation depth <0.5 mm Young's Modulus (E) 50 GPa
The materials are supplied to the site in a three-component premix (pre-blended powders in 35 kg bags plus superplasticizer and fibers), along with a mixer and technical on-site support from the supplier.
Phase I: Prototype and Test Panels with UHPC Joint Fill in a Laboratory
In 2008, the owner, material supplier and precaster agreed to undertake a prototyping and testing program to validate the full-depth precast panel and UHPC joint design. The prototypes to be cast and tested were pairs of precast panels with joint fill and small samples of UHPC with rebars for direct pullout tests (Figure 4 and 5)8.
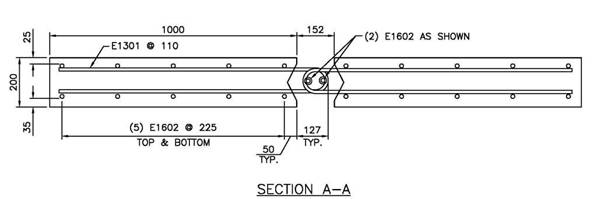
Fig. 4 Prototype Panel (Pairs) for Testing Joint Fill Performance6
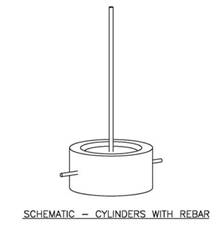
Fig. 5: UHPC Specimen with Rebar for Pullout Test6
The precast panel pairs were manufactured with three rebar joint configurations (straight bars, hairpins, and stud head) and three types of rebar (epoxy coated, galvanized and black) and for a total of nine configurations. Note: Figure 4 shows only the hairpin joint configuration.
Pullout test specimens (Figure 5) were manufactured with 13mm, 16mm and 19mm bar sizes in epoxy coated and black steel bars. Embedment lengths were 75mm for the 13mm Ø bar; 100mm for the 16mm Ø bar; and 125mm for the 19mm Ø bar. Failure behavior of the pullout tests conducted on all samples was rebar failure (Figure 6).
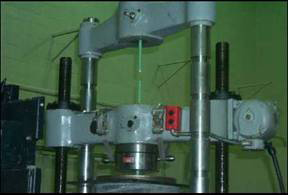
Fig. 6 Pullout Test Set-up showing Failure Behavior
To validate the joint's ability to remain water tight during the life of the bridge, the precast panel pairs are loaded with a simulated wheel impact loading while water is ponded on the joint (Figure 7). Test panels manufactured at Fort Miller Company, NY were shipped to the FHWA Turner-Fairbanks laboratory for fatigue testing in a field simulated, wet condition.
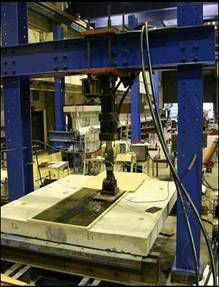
Fig. 7 Bridge deck panels with water ponding under fatigue loading (courtesy of FHWA)
The HPC precast deck panels (Figure 7) with the UHPC joint fill showed no signs of leakage or degradation at 9 million cycles of a simulated wheel loading (cycling from 1 ton to 8 tons).
Phase II: Use of UHPC Joint Fill in Side-by-Side Deck Bulb-Tees
The first demonstration project selected for UHPC joint fill was a 25.9 m single span Deck Bulb-Tee girder bridge in the Village of Lyons, NY, located in Wayne County in the north east corner of NY State on Route 31 (Figures 8 and 9). NYSDOT selected this project in order to validate the field casting process for UHPC joint fill.
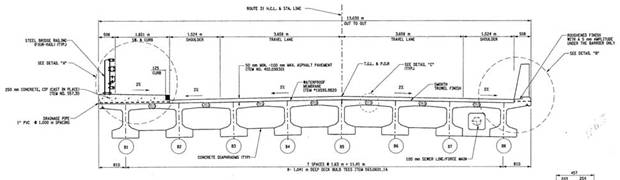
Fig. 8 Bridge Cross Section for Village of Lyons Bridge8
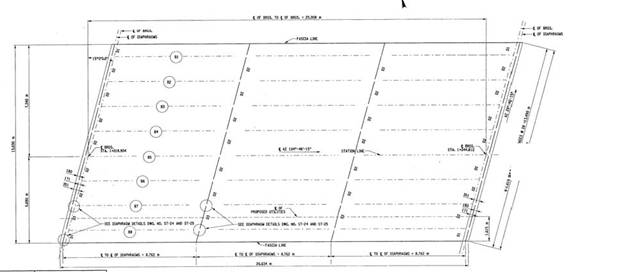
Fig. 9 Layout of Beams Plan8
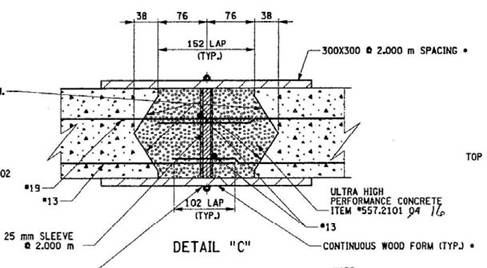
Fig. 10 Cross-Section of the UHPC Joint Fill between the Deck Bulb-Tees8.
NYSDOT called tenders for the project in the Fall of 2008 and awarded the contract to Ramsey Construction. Ramsey's construction team for the project attended the casting of the UHPC Joint Fill for the prototype UHPC joints at Fort Miller in January 2009 as part of their training and orientation for working with UHPC.
During the spring of 2009, Ramsey removed the existing bridge, prepared the new abutments and installed the new deck bulb-tees (Figure 11). In May 2009, the UHPC joint fill was installed to connect the side-by-side deck bulb-tees.
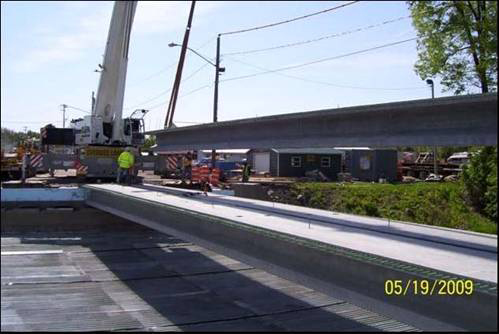
Fig. 11 Installing the side-by-side Deck Bulb-Tees
Following installation of the girders, the differential camber was adjusted with a temporary mid-span transverse beam and jacks (Figure 12).
The UHPC joint fill materials and portable mixers were delivered to the site by the material supplier and set up for batching (Figure 13). The superplasticizer, fibers and water are weighed out on-site. The mixers are set up in pairs to provide a continuous supply of material for the joint filling operation. (Mixers are normally set up at the end of the bridge to provide direct access to the bridge deck.) The batching crew is trained and supervised by the supplier's technical on-site support.
The IMER Mortarman 750 mixers are capable of batching 0.23 m3 per 20 minute batch cycle time for a volume of 1.36 m3/hour per pair of mixers. The number of mixers delivered to the site is determined based on the contractor's schedule.
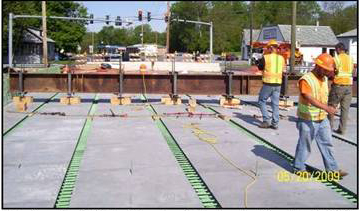
Fig. 12 Adjusting the Girder Camber Prior to Casting the UHPC Joint Fill
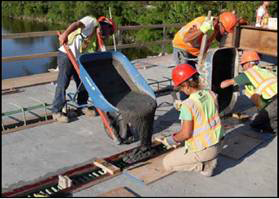
Fig. 13 UHPC Portable Mixers
The UHPC joint material is transported to the joints by power buggy or wheel barrow and then dumped directly into the joints (Figure 14). The UHPC material was batched with a mini-slump flow of 200 mm to 225 mm (self-consolidating and self-leveling). The consistency and quality of each batch is controlled, monitored and ensured by the on-site technical support. The rheology of material permitted the UHPC to be poured directly into the joints without any vibration.
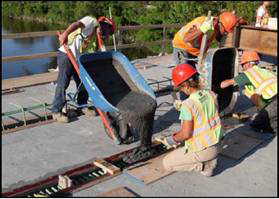
Fig. 14 Filling the joints with UHPC.
The joints are covered with form grade plywood strips, and then allowed to cure until reaching 100 MPa, before opening to traffic. The time to reach 100 MPa will vary. At ambient temperatures (20°C) without any accelerators, this would be approximately 3 days. This can be reduced with accelerator and heat. For the Village of Lyons project, NYSDOT required an asphalt overlay with a waterproofing membrane. Prior to placing the overlay, the UHPC joints were surface ground (Figures 15, 16).
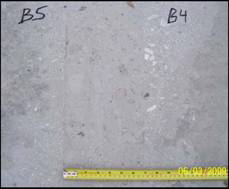
Figure 15 Close-up of a ground Joint Fill and side-by-side Deck Bulb Tees
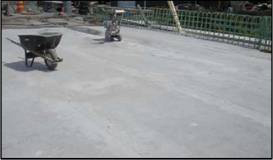
Fig. 16 Top view of bridge deck before applying asphalt overlay. Showing UHPC Joint Fill and side-by-side Deck Bulb-Tees.
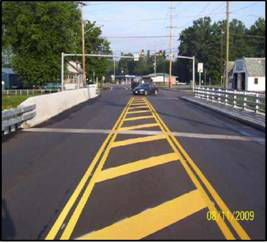
Fig. 17 Completed Bridge
Conclusions
The UHPC material's combination of superior properties (strength, durability, fluidity and increased bond capacity), in conjunction with reinforced precast panels, provides the ability to create new, optimized solutions for bridge construction. By utilizing its combined material properties, precast bridge deck panel design is advanced. Direct benefits may include: improved bridge deck performance through reduction of joint size and complexity; improved continuity and speed of construction and; elimination of field post-tensioning. Indirect benefits include: improved durability; lower maintenance and; extended usage life.
The project highlights and testing presented are preliminary findings of the NYSDOT precast bridge decks with UHPC program; Phase I and II. Early testing to date indicates that rebar in UHPC has a much shorter bond development length. This provides opportunities for bridge engineers to design narrower joint widths for precast deck systems without post-tensioning.
The field batching of UHPC joint fill for the Village of Lyons project indicates that this material can be successfully batched on site and provide adequate strengths during typical field curing conditions. This experience also shows that local contractors can easily adapt to using the material in bridge projects.
While there are still challenges when implementing this solution on a wide scale basis, the real challenge ahead is to identify the optimized shapes for precast deck panels and joints for various deck arrangements such as box girders. When optimized configurations are determined, precasters, manufacturers and contractors can invest in the formwork and equipment to economically produce these solutions. The true economics of these systems will eventually bring value to highway users through standard mass production of optimized shapes and systems and ultimately, years of low maintenance usage.
References
- Bhide, S., "Material Usage and Condition of Existing Bridges in the US", PCA, Skokie, Illinois, USA, 2008.
- Graybeal, B.A., "Fabrication of an Optimized UHPC Bridge", PCI National Bridge Conference, Atlanta, GA, USA, 2004.
- Bierwagen, D., Moore, B., and Perry, V., "Revolutionary Concrete Solutions", Construction Specifier, USA, 2006.
- Perry, V., Scalzo, P., Weiss, G., "Innovative Field-Cast UHPC Joints for Precast Deck Panel Bridge Superstructures – CN Overhead Bridge at Rainy Lake, Ontario", PCI-FHWA National Bridge Conference, USA, 2007.
- Drawings, "Precast Panel Reinforcing", NYSDOT, May 2008.
- Drawings, "The Fort Miller Company Shop Drawings for Ductal® UHPC Joint Test", Fort Miller Company, December 2008.
- Lafarge, Product Data Sheet: Ductal® JS1000, www.imagineductal.com, 2009.
- Drawings "Bridge Rehabilitation – Route 31 Over Canadaigua Outlet, SH 8028, Route 31", NYSDOT, June 2008.