FHWA LTPP Guidelines For Measuring Bridge Approach Transitions Using Inertial Profilers
Chapter 2. Profile Measurements
Profile measurements should be performed with the LTPP inertial profilers survey units in accordance with the data collection and processing guidelines and procedures described in the draft LTPP Manual for Profile Measurements and Processing or any subsequent updates or replacements that occur for this manual.(5) The exception is that the setup options are modified for Long-Term Bridge Performance data collection as identified in these guidelines, which outline the procedure for profiling a bridge section and the number of acceptable runs that are required.
Inertial Profiler Setup
The FHWA LTPP profilers are set up for data collection for the LTPP Program as defined in the draft LTPP Manual for Profile Measurements and Process using the LTPP header format.(5) This header format has some limitation for use in collecting profiles for measuring bridge approach transitions. The main limitations are the ability to increment in both the positive and negative direction, input a start location other than zero, and add custom comments for all header information inputs. The long header format will accommodate the input information that is required for the bridge transition profile data collection with some interpretation of the header descriptions. This header format is compatible with the ProVAL software with output format in both the Engineering Research Division (ERD) and pavement profile format (PPF).
The profiler setup procedure for the bridge profile is as follows:
- Enter the Setup screen from the main menu and select the Analysis Options tab and make the following key changes:
- Select the Report Options tab and make the following key changes:
- Select the Profile Analysis tab and make the following key changes:
- Select the Texture Analysis tab and make the following key change:
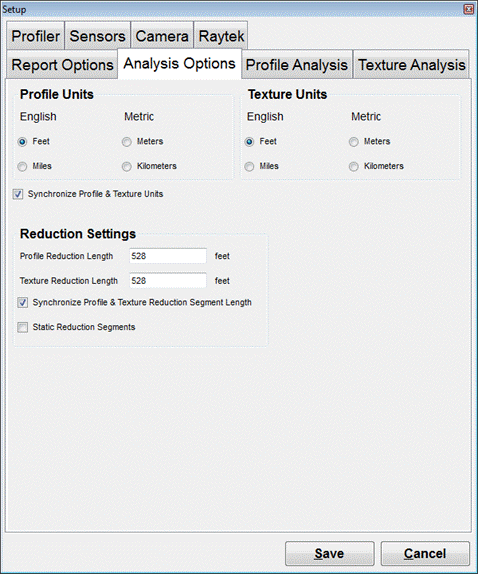
1 ft = 0.305 m.
Figure 8. Screen capture. Analysis options.
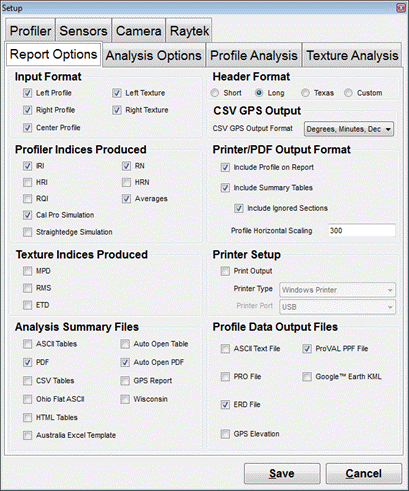
Figure 9. Screen capture. Report options.
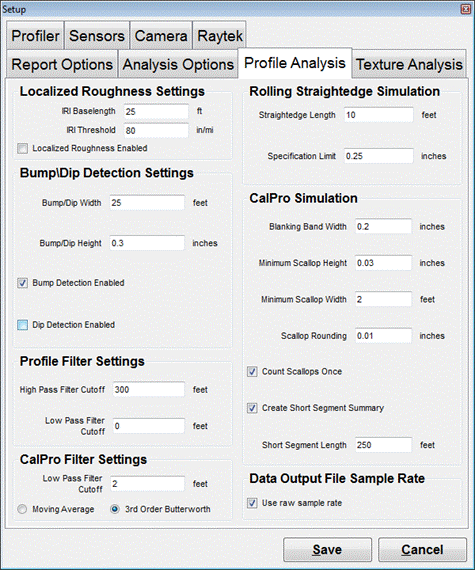
1 ft = 0.305 m.
1 inch = 25.4 mm.
1 inch/mi = 15.8 mm/km.
Figure 10. Screen capture. Profile analysis.
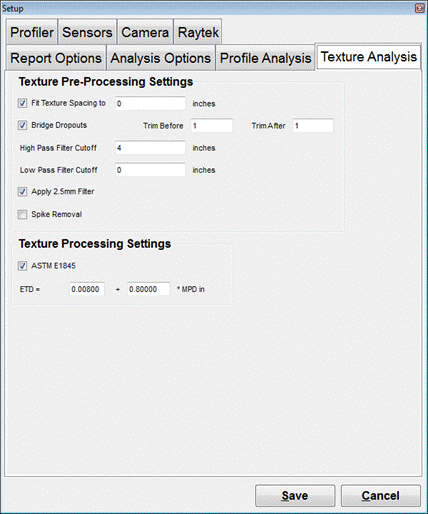
1 inch = 25.4 mm.
Figure 11. Screen capture. Texture analysis.
Profiler Survey Procedure
Profile surveys should be done in both directions using the following conventions:
- Positive direction from south to north or west to east.
- Negative direction from north to south and east to west.
- Distance should increase in the positive direction.
- Distance should decrease in the negative direction. The ending station for the positive direction will be the starting station for the negative direction and will end at zero.
The above instructions are based on general industry practice to increment stations from south to north and west to east. Site location and conditions may indicate that an alternative approach may be more practical, and this decision should be made at the discretion of the profiler crew. The road signage may not always be consistent with the direction of travel. For example, it is possible to be travelling in an easterly direction with the route signs indicating north. Because the profile data will be geo-tagged, it is not necessary to record the test direction information. The operator should indicate the direction from the route sign or general direction if there is no route signage. This information is included in the profile header and on the site information form.
Procedures for profiling a bridge section and the number of profile runs that are required at a bridge section are described in the next section.
Profiling Paths and File Naming Convention
The profile data should be collected with the profiler centered in the wheelpaths. If no defined wheelpath is visible, then the profiler will be centered between the centerline of the road and edge of the pavement. The operator should follow the same path when traversing the bridge.
The SSNNNDLV convention should be followed for naming files. The acronym is defined as follows:
- SS: State in which site is located. LTPP standard agency codes are used (e.g., 36 for
New York).
- NNN: Bridge identification (ID). This is a numeric character to identify the bridge as tested in sequence. This number can be tied to a specific bridge type (e.g., steel stringers or timber), type of approach (e.g., geosynthetic reinforced soil (GRS), approach slab or roadbase), or type of foundation (GRS, spread footing, piles, or drilled shafts).
- D: Letter code defining direction of travel (e.g., N for north, S for south, W for west, or E for east).
- L: Profile lane (i.e., lane 1, 3, 5, 7, 9, etc., in the positive direction and 2, 4, 6, 8, etc., in the negative direction taken from the median or centerline).
- V: Sequential visit identifier that indicates the visit code for the current profile data collection. This identifier indicates the number of times a set of profile runs has been collected at a site since the site was first profiled. An appropriate letter should be used for the current profiling (i.e., A used for the first visit, B for the second, etc.).
For example, the following data file names would be valid:
- 36001N1A: The profile data was collected in New York with this being the first bridge profiled in the northbound positive outer lane during the first visit.
- 36003W2B: The profile data was collected in New York with this being the third bridge profiled in the westbound negative outer lane during the second visit.
Information on the roadway for which the bridge is located, the bridge name, ID number, start location, and end length should be contained within the header discussed in the Inertial Profiler Setup subsection. An end of run comment should be completed by the operator for each run that will identify the run status or any conditions that could have an effect on the profile data. The operator comment field should be used for any additional comments regarding site conditions or pavement features. As previously noted, the information regarding the bridge is recorded on form 1A (see figure 4) or 1B (see figure 5) along with photos as recorded on form 2A (see figure 6).
Data Collection Procedure
Before collecting data at bridge sections, the operator should either perform or take steps to ensure the following conditions are met:
- Daily checks should be performed on the equipment (i.e., laser sensor check and bounce test).
- State transportation department procedures relating to safety issues should be strictly followed (i.e., light bar, directional warning light, strobe lights, use of turnarounds, etc.).
- Operating speed for collecting profile data should be 50 mi/h (80 km/h). If the maximum constant speed attainable is less than 50 mi/h (80 km/h) because of either traffic congestion or safety constraints, then a lower speed should be selected depending on the prevailing conditions. If the speed limit at the site is less than 50 mi/h (80 km/h), then the site should be profiled at the posted speed limit. If traffic traveling at high speeds is encountered at a test site, it is permissible to increase the profiling speed to 55 mi/h (89 km/h). Deviation from the expected speed should be noted. Hardware limitations, primarily as the result of the quality and configuration of the inertial profiler’s accelerometer, affects low-speed pavement longitudinal profile collection at less than 15 mi/h (25 km/h), causing the calculation of abnormally high and often invalid IRI data at these points.(7)
- The photocell should always be used to initiate data collection at the beginning of the test section.
- When entering header information into the software, the section number and direction of travel (four digits combined) assigned to the bridge should be entered as the site ID.
- The software’s stop distance should be established by taking a preliminary run using the start and end tapes to identify the beginning and end of the section. The horizontal test within the Calibration menu can be used to establish the distance between the two reflective stripes. Subsequent runs will use the photocell to start profiling and distance to end profiling.
- Digital forward-looking images should be collected in each direction following the procedures outlined in the draft LTPP Manual for Profile Measurements and Process.(5)
- The profile survey crew is responsible for working with FHWA and the relevant State transportation department to locate and correctly identify the bridge location for each project.
By selecting Start within the main menu, access to the header menu is obtained. Before starting the profile data collection, the header information needs to be entered or modified to represent the run data that will be collected. The following list outlines the required inputs for the header file:
- File name: The user enters the file name using the format as defined for the bridge profile data collection.
- Number: The user starts with run 1 and increases by increments of 1 in each direction.
- Start/stop method: The start method will always be photocell, and the stop method will always be distance. The distance input value is established from the trial run using the horizontal test from the Calibration menu.
- Units: The units will always be feet.
- Direction: The direction is positive or negative, which is updated with file name changes.
- Beginning station: The user enters “zero” in the positive direction and “length” as input for distance in the negative direction.
- Header fields: These fields describe the test location, lane, and direction. The bridge sequential number, bridge name and/or identifier, route, city/county, and State provided for locating the bridge should be input to the header file along with the lane designation and route direction.
- Comments: Comments that will explain or help with the interpretation of the profile data should be included here. If there are no comments, put “none” in the comment field.
Figure 12 shows an example of a screen capture of the header inputs. With the header information input, the user should initiate profile data using the procedures as outlined in the draft LTPP Manual for Profile Measurements and Processing.(5)
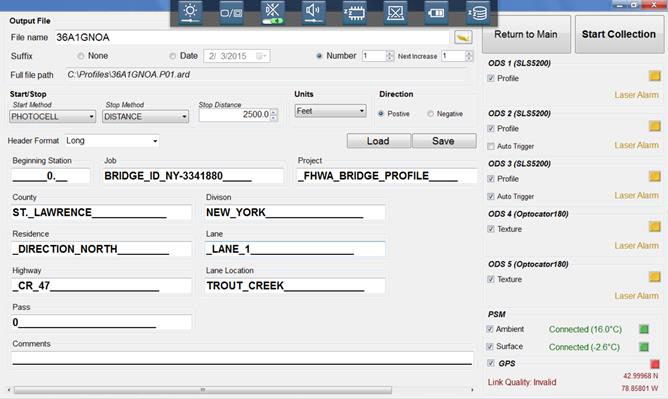
1 ft = 0.305 m.
Figure 12. Screen capture. Profiler system software header fields.
On completion of the previously mentioned steps, the following procedure should be followed to obtain an acceptable set of profile runs at bridge sections:
- Profile data should only be collected when traffic, weather, and pavement conditions (i.e., pavement surface is dry and clear of debris) will not hamper or affect the profile data. If conditions are not acceptable, the profile crew will be required to adjust or reschedule the profile data collection.
- The operator should ensure that the end of the bridge section length (i.e., 700 ft (213 m) from the end of the bridge interface) is passed before terminating profile data collection.
- The operator should obtain at least three runs by driving the profiler along the wheelpaths.
- After completing the data collection, the operator should review the profile runs that were collected. The operator should evaluate the profiles for equipment-related spikes by following the procedures described in section 2.9.4 of the draft LTPP Manual for Profile Measurements and Processing.(5) If the operator determines that at least three error-free runs along the wheelpaths have been obtained at the site, data collection should be terminated. Runs are considered error free if there are none of the following:
- Sensor issues.
- Distance-measuring instrument (DMI) issues, including DMI shift.
- Other equipment issues.
- Operator issues, including testing out of the wheelpath.
- Variability that is not pavement related.
- Unexplained run-to-run variability of profiles and/or IRI.
If the operator believes that three error-free runs along the wheelpaths have not been obtained, the operator should repeat the data collection and evaluate the profile data using the procedures described previously. A maximum of five runs along the wheelpaths can be performed. If the additional runs do not satisfy the criteria established for profile acceptance (defined in the LTPP manual), then the profile operator needs to provide an explanation for why the profile data is suspect. If the issue is equipment-related, then the operator should terminate the data collection and have the equipment serviced or repaired and calibrated before collecting any further profile data. The profile data can be retained or discarded at the discretion of the profile analyst.
- The profile sensors in the left wheel and right wheelpath and midlane along with two texture lasers located in the left and right wheelpath should be checked for operation and accuracy prior to profiling. The profile acceptance criteria are based on the profile sensors in the left and right wheelpath. The profile operator should perform a visual observation of the profiles in the midlane and those collected by the texture lasers by reviewing the profile graphs. In general, if the left and right profiles are of acceptable quality, then the texture lasers will also produce acceptable results.
Note that fewer than three runs can be accepted if conditions at the site result in excessive delay in the schedule. This may occur if it starts to rain during the data collection or if there are other local interruptions such as accidents or farm machinery using the roadway.
- The operator should generate ERD and PPF files from the .ARD data following the instructions in the user manual.(8)
- The operator is encouraged to use ProVAL cross-correlation analysis to determine run-to-run acceptability, time permitting. A correlation of 92 percent for three runs would be the target for acceptable repeatability between runs. It is possible that three error-free runs may not meet the criteria because of transverse variability within the section limits. In this instance, a comment on either form 1A or 1B would be sufficient to explain the variability.
- The operator should maintain a log of the runs on the daily progress report.
- The operator should back up the data before leaving the site following procedures described in section 2.9.6 of the draft LTPP Manual for Profile Measurements and Processing.(5)
An acceptable set of profile runs is three error-free runs in the wheelpaths.