Note: This document was superseded in March 2023 by: Manual for Heat Straightening, Heat Curving and Cold Bending of Bridge Components
Heat Straightening Repair for Damaged Steel Bridges
Superseded: Appendix, List of Revisions and Errata
Report No. FHWA-IF-99-004
Page | Item | Revision |
---|---|---|
6 | Fig. 1.2 (b), 2nd line of caption | Change "wind" to "ship mast impact" |
39 | Fig. 3.2 (a) | Dimensions "Lr-1" and "Lr" should read "L" |
39 | Fig. 3.3 | Next to last word is figure caption, "cord" should read "chord" |
42 | Fig. 3.5 | "R/ymax = 8.16" Should read "R/ymax = 8.15" |
44 | 1st column, 6th line from bottom | "Fig. 3.4" should read "Fig. 3.5" |
67 | 2nd column, line 29 | Line should read: "...different formulas are used, depending on ..." |
70 | 2nd column, line 22 | "(plate II)" should read "(P-11)" |
78 | Fig. 4.24 caption | Should read "residual stress distribution For damaged, Category W wide flange beams ..." |
80 | Fig 4.27 | Labels for the two curves should be interchanged and equations for E(T)/Eo should read
E(T)/Eo = 1.0 |
90 | Table 4.9 | Add footnote to table: "* indicates invalid data point" |
91 | 2nd column, 9th line from bottom | The word "full" should read "three-quarters" |
91 | 2nd column, 2nd line from bottom | The phrase "P-9 and P-11" should read "B-1 through B-4" |
94 | 1st column, 8th line from bottom | "depends of" should read "depends on" |
114 | 2nd column, line 15 | "form Fig. 4.26" should read "from Fig. 4.26" |
117 | 2nd column, line 15 | "Table 5.2" should read "Table 5.1" |
161 | Eq. 7.16 | "![]() ![]() |
173 | Table 8.2, Beam 5, 5th column | "-48.0/-6.23" should read "-48.0/6.97" |
179 | 2nd column, line 20 | Change "... strain over the 381 mm ..." to "... strain at the flange edge over the 381 mm ..." |
179 | 2nd column, line 21 | Change "table 1" to "table 9.1" |
181 | 2nd column, lines 9-13 | delete the phrase "The near side movements were inversely proportional to the size of the vees with ..." and modify the rest of the sentence to read "The most effective pattern was the one with line heats and no vee heats." |
181 | 2nd column, lines 13-20 | Delete the sentences from lines 13 through 20 beginning with "The use of two ..." |
187 | 2nd column, line before Eq. 9.3 | Change "... capacity along yield line ..."to "...capacity per unit length along a yield line' |
200-204 | Table 10.1, 4th column | The decimal point in all temperature entries should be replaced by a comma |
203 | Table 10.1, 10th column Line 21 | "9.94" should be replaced by "0.94" |
243 | Chapter 15. Bibliography | Add the additional references attached |
Interactive Guide to Heat Straightening, Volume 1: Management, Design and Technique (CD)
- Main menu to Techniques menu to External Restraints screen to 2nd screen: "Keys to Proper uses of Restraining Forces"
The 2nd bullet should read "Jacks should be placed in a direction tending to Straighten the member
- Main menu to Design menu to Number of Heats menu to 9th screen which shows a group of equations for Jacking Force factor, Shape factor and Stress factor
In the definition of ds, the word "aphex" should read "apex"
When clicking on the following terms: 1/
, d or tw, a pull-down graphic appears. The term "tw" shown in the graphic should be the thickness of the web rather than the thickness of the flange as shown
- Main menu to Techniques menu to Typical Heating Pattern Combinations menu to Damage Category menu to "Wide flange with weak axis flexural damage and a bulge on one flange" damage category
The graphic showing the heating pattern should contain a strip heat in the web equal in width to the flange vee heat at the web/flange juncture
Interactive Guide to Heat Straightening, Volume 2: Case Study, Lake Charles, Louisiana (CD)
- Main menu to Heating Patterns
The maximum strain ratios for web bulges are not shown . They are as follows:
At impact: 34 At diaphragm 2: 42 At diaphragm 3: 39 At diaphragm 4: 12
Additions to Bibliography
1. Avent, R. R., and Mukai, D., "Fundamental Concepts of Heat-Straightening Repair for Damaged Steel Bridges," Transportation Research Record, No. 1680, Transportation Research Board, Washington, DC, pp. 47-54, 1999.
2. Avent, R. R., and Mukai, D., "Planning, Designing, and Implementing Heat-Straightening Repair of Bridges," Transportation Research Record, No. 1680, Transportation Research Board, Washington, DC, pp. 55-62, 1999.
3. Avent, R. R., and Mukai, D., Heat-Straightening Repair for Damaged Steel Bridges, Vol. 1: Management, Design and Techniques, Pub. No. FHWA-HIF-00-008 (CD-ROM), Federal Highway Administration, Washington DC, 1999.
4. Avent, R. R., and Mukai, D., Heat-Straightening Repair for Damaged Steel Bridges, Vol. 2: Case Study, Lake Charles, La., Pub. No. FHWA-HIF-00-008 (CD-ROM), Federal Highway Administration, Washington DC, 1999.
5. Avent, R. R., Mukai, D. J., Robinson, P. F., and Boudreaux, R. J., "Heat Straightening Damaged Steel Plate Elements, Journal of Structural Engineering, ASCE, Vol. 126, No. 7, pp. 747-754, July, 2000.
6. Avent, R. R., Mukai, D. J., and Robinson, P. F. "Heat Straightening Rolled Shapes", Journal of Structural Engineering, ASCE, Vol. 126, No. 7, pp. 755-763, July, 2000.
7. Avent, R. R., Mukai, D. J., and Robinson, P. F., "Effect of Heat Straightening on Material Properties of Steel," Journal of Materials in Civil Engineering, ASCE, Vol. 12, No. 3, pp. 188-195, Aug. 2000.
8. Avent, R. R., Mukai, D. J, and Robinson, P. F., "Residual Stresses in Heat-straightened steel Members," Journal of Materials in Civil Engineering, ASCE, Vol. 13, No. 1, pp. 18-25, Jan/Feb. 2001.
9. Avent, R. R., and Mukai, D. J., "Engineered Heat-Straightening Repairs: A Case Study," Journal of Bridge Engineering, ASCE, Vol. 6, No. 2, pp. 95-102, Mar/Apr, 2001
10.Avent, R. R., and Mukai, D. J., "What you Should Know About Heat Straightening Repair of Damaged Steel", Engineering Journal, AISC, Vol. 38, No. 1, pp. 27-49, 1st Quarter, 2001
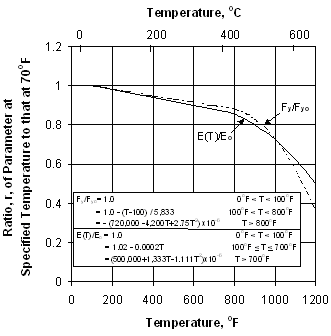
Revised Figure 4.27
Fy/Fyo= 1.0 | 0°F < T < 100°F | |
= 1.0 - (T-100) / 5,833 | 100°F ![]() ![]() | |
= - (720,000 -4,200T+2.75T2) x10-6 | T > 800°F | |
E(T)/Eo = 1.0 | 0°F < T < 100°F | |
= 1.02 - 0.0002T | 100°F ![]() ![]() | |
=(500,000+1,333T-1.111T2)x10-6 | T > 700°F |