Long-Term Plan for Concrete Pavement Research and Technology - The Concrete Pavement Road Map: Volume II, Tracks
Track 1. Performance-Based Concrete Pavement Mix Design System (MD)
TRACK 1 (MD) OVERVIEW
This track will develop a practical yet innovative concrete mix design procedure with new equipment, consensus target values, common laboratory procedures, and full integration into both structural design and field quality control (QC). As opposed to mix proportioning, mix design engineers a concrete mixture to meet a variety of property or performance targets. The process begins by defining the end product, and then the various materials are selected, proportioned, simulated, and optimized to meet the end product goals. This track will develop mix design rather than mix proportioning.
This ambitious track also lays the groundwork for the concrete paving industry to assume more mix design responsibility as State highway agencies move from method specification to a more advanced acceptance tool. To do this, however, the concrete paving industry and the owner-agencies must be able to refer to a single document for state-of-the-art mix design.
The track provides a plan for research in the following areas:
- Integration of volumetrics-based, property-based, performance-based, and functionally based mix designs and recycled materials into the mix design system.
- Identification of new and upgraded equipment and test procedures.
- Development of an expert system that connects test results to each other.
- Improved models to predict slab performance.
- Field evaluation and implementation procedures that provide a mechanism for user feedback.
- Technology transfer activities.
The goal and objectives for this track and the gaps and challenges for its research program are summarized below. A phasing chart is included to show the approximate sequencing of the problem statements in the track. A table of estimated costs provides the projected cost range for each problem statement, depending on the research priorities and scope determined in implementation. The problem statements, grouped into subtracks, then follow.
Track Goal
Innovative concrete mix material selections and mix design procedures will produce economical, compatible, and optimized concrete mixes integrated into both structural concrete pavement design and construction control.
Track Objectives
1. Develop a concrete lab of the future that will give the user a sequence of mix design tests and procedures that integrate structural design and QC with material selection and proportioning.
2. Develop the tools necessary to predict the compatibility and effectiveness of concrete mixes under specific field conditions before paving begins.
3. Detect potential construction problems early and correct them automatically using innovative QC tools.
4. Detect potential long-term durability problems more effectively during both the mix design process and the construction QC program.
5. Improve the ability to predict concrete mix properties and their relationship to slab behavior and performance (e.g., shrinkage, joint opening, and curing) using the next generation of advanced modeling techniques.
6. Identify and use innovative, nontraditional materials that accelerate concrete pavement construction, maintenance, and rehabilitation and/or extend product life at a fair cost.
Research Gaps
- Insufficient understanding of the material factors that influence pavement performance.
- Insufficient understanding of the effects that material has on durability prediction.
- Lack of equipment and test procedures to accelerate durability testing.
- Lack of cost effective programs to accelerate training on new tests.
- Insufficient understanding of the impacts that materials have on pavement constructability.
- Insufficient understanding of the relationship between materials and surface characteristics.
- Insufficient understanding of the ways to use locally available materials more effectively.
- Insufficient understanding of the ways to advance higher order use of recycled concrete materials.
- Insufficient understanding of the future roles and responsibilities of the public and private sectors.
Research Challenges
- Tie the materials used to pavement performance indicators.
- Learn more about concrete pavement deterioration and reliably identify the materials or material combinations that cause deterioration.
- Identify equipment that can measure the most relevant identified properties.
- Quantify the cost of test equipment, training, and the materials themselves.
- Recognize a connection between the materials selected and the ease of constructing with them.
- Identify the user demands for smooth, quiet, safe, and long-lasting pavements and translate those demands into material selection and optimization.
- Identify a place for all grades of materials and identify ways of using locally available materials in less critical applications (e.g., county roads or stopgap pavements).
- Prepare the concrete pavement industry in the United States to meet sustainability goals that other countries have moved toward, specifically a 100 percent reuse policy.
- Identify who will establish performance standards for future concrete pavement mixes and material selection, proportioning, and compatibility factors.
Research Track 1 (MD) Phasing
The horizontal bar chart in figure 1 shows the approximate time phasing of the problem statements in this track grouped by subtrack across 10 years. The phasing information here is a summary of the approximate phasing included with the full written description of each problem statement in this track.
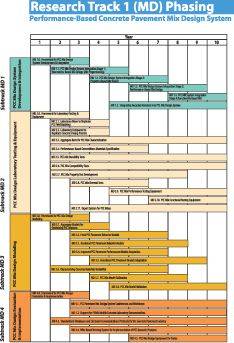
Click to enlarge or view alternative text
Figure 1. Track 1 (MD) subtrack and problem statement phasing chart.
Research Track 1 (MD) Estimated Costs
Table 1 shows the estimated costs for this research track.
Table 1. Research track 1 (MD) estimated costs.
Problem Statement |
Estimated Cost |
Subtrack MD 1. Portland Cement Concrete (PCC) Mix Design System Development and Integration |
|
MD 1.0. Framework for PCC Mix Design System Development and Integration (Subtrack MD 1) |
$300 k |
MD 1.1. PCC Pavement Mix Design System Integration Stage 1: Volumetrics-Based Mix Design (Mix Proportioning) |
$500 k–$1 M |
MD 1.2. PCC Pavement Mix Design System Integration Stage 2: Property-Based Mix Design |
$1 M–$2 M |
MD 1.3. PCC Pavement Mix Design System Integration Stage 3: Performance-Based Mix Design |
$1 M–$2 M |
MD 1.4. PCC Pavement Mix Design System Integration Stage 4: Functionally Based Mix Design |
$1 M–$2 M |
MD 1.5. Integrating Recycled Materials into PCC Mix Design System |
$500 k–$1 M |
Subtrack MD 2. PCC Mix Design Laboratory Testing and Equipment |
|
MD 2.0. Framework for PCC Mix Design Laboratory Testing and Equipment (Subtrack MD 2) |
$200 k |
MD 2.1. Laboratory Mixer to Replicate PCC Field Batching |
$1 M–$2 M |
MD 2.2. Laboratory Compactor to Replicate Concrete Paving Practice |
$1 M–$2 M |
MD 2.3. Aggregate Tests for PCC Mix Characterization |
$2 M–$5 M |
MD 2.4. Performance-Based Cementitious Materials Specifications |
$1 M–$2 M |
MD 2.5. PCC Mix Durability Tests |
$2 M–$5 M |
MD 2.6. PCC Mix Compatibility Tests |
$2 M–$5 M |
MD 2.7. PCC Mix Property Test Development |
$2 M–$5 M |
MD 2.8. PCC Mix Thermal Tests |
$500 k–$1 M |
MD 2.9. PCC Mix Performance Testing Equipment |
$2 M–$5 M |
MD 2.10. PCC Mix Functional Testing Equipment |
$2 M–$5 M |
MD 2.11. Expert System for PCC Mixes |
$1 M–$2 M |
Subtrack MD 3. PCC Mix Design Modeling |
|
MD 3.0. Framework for PCC Mix Design Modeling (Subtrack MD 3) |
$150k |
MD 3.1. Aggregate Models for Optimizing PCC Mixtures |
$250 k–$500 k |
MD 3.2. Fresh PCC Pavement Behavior Models |
$1 M–$2 M |
MD 3.3. Hardened PCC Pavement Behavior Models |
$250 k–$500 k |
MD 3.4. Improved PCC Pavement Performance Models Adaptation |
$250 k–$500 k |
MD 3.5. Functional PCC Pavement Models Adaptation |
$250 k–$500 k |
MD 3.6. Characterizing Concrete Materials Variability |
$250 k–$500 k |
MD 3.7. PCC Mix Model Calibration |
$1 M–$2 M |
MD 3.8. PCC Mix Model Validation |
$500 k–$1 M |
Subtrack MD 4. PCC Mix Design Evaluation and Implementation |
|
MD 4.0. Framework for PCC Mix Design Evaluation and Implementation (Subtrack MD 4) |
$150 k |
MD 4.1. PCC Pavement Mix Design System Conferences and Workshops |
$2 M–$5 M |
MD 4.2. Support for FHWA Mobile Concrete Laboratory Demonstrations |
$1 M–$2 M |
MD 4.3. Standardized Databases and Electronic Communications Protocols for the Concrete Pavement Industry |
$250 k–$500 k |
MD 4.4. Web-Based Training System for Implementation of PCC Research Products |
$500 k–$1 M |
MD 4.5. PCC Mix Design Equipment for States |
$1 M–$2 M |
Track 1 (MD) |
|
Total |
$29.8 M–$67.8 M |
Track Organization: Subtracks and Problem Statements
Track 1 (MD) problem statements are grouped into four subtracks:
- Subtrack MD 1. PCC Mix Design Development and Integration.
- Subtrack MD 2. PCC Mix Design Laboratory Testing and Equipment.
- Subtrack MD 3. PCC Mix Design Modeling.
- Subtrack MD 4. PCC Mix Design Evaluation and Implementation.
Each subtrack is introduced by a brief summary of the subtrack’s focus and a table listing the titles, estimated costs, products, and benefits of each problem statement in the subtrack. The problem statements then follow.
SUBTRACK MD 1. PCC MIX DESIGN SYSTEM DEVELOPMENT AND INTEGRATION
This subtrack develops the overall track structure and integrates all the output from the other four subtracks into a comprehensive, cohesive product. The problem statements in this track will integrate volumetrics-based, property-based, performance-based, and functionally based mix designs and recycled materials into the mix design system. Table 2 provides an overview of this subtrack.
Table 2. Subtrack MD 1 overview.
Problem Statement |
Estimated Cost |
Products |
Benefits |
MD 1.0. Framework for PCC Mix Design System Development and Integration (Subtrack MD 1) |
$300 k |
A validated, sequenced, and detailed research framework for this subtrack. |
An effective, coordinated, and productive research program. |
MD 1.1. PCC Pavement Mix Design System Integration Stage 1: Volumetrics-Based Mix Design (Mix Proportioning) |
$500 k–$1 M |
Software, guidelines, and supporting products for a new generation of concrete mix design that will optimize concrete mixtures for paving. |
A procedure to allow job-specific optimization of concrete paving mixtures based largely on currently available technology, rather than current mix proportioning methods based on either previous experience or procedural guidance developed for a broad range of concretes. |
MD 1.2. PCC Pavement Mix Design System Integration Stage 2: Property-Based Mix Design |
$1 M–$2 M |
Updates to the software, guidelines, and supporting products for concrete mix design and optimization. |
Building on the foundational work conducted under MD 1.1 (PCC Pavement Mix Design System Integration Stage 1: Volumetrics-Based Mix Design), a procedure capable of designing and optimizing a mix for more specific and pertinent concrete properties, possibly including strength, workability, permeability, stiffness, shrinkage, and coefficient of thermal expansion. |
MD 1.3. PCC Pavement Mix Design System Integration Stage 3: Performance-Based Mix Design |
$1 M–$2 M |
Updates to the software, guidelines, and supporting products for concrete mix design and optimization. |
A quantum improvement to the mix design process; newly developed tests and models for predicting pavement performance that allow the mix to be optimized to meet the service requirements of structural and material performance. |
MD 1.4. PCC Pavement Mix Design System Integration Stage 4: Functionally- Based Mix Design |
$1 M–$2 M |
Updates to the software, guidelines, and supporting products for concrete mix design and optimization. |
A sophisticated optimization system capable of selecting the most appropriate mixture to meet both performance requirements as well as functional requirements; a procedure based on new test procedures that identify the potential for concrete to provide a smooth, safe, and quiet pavement. |
MD 1.5. Integrating Recycled Materials into PCC Mix Design System |
$500 k–$1 M |
Guidance and possible modifications to the mix design products that allow a user to design a concrete mixture using recycled materials. |
Mix design procedures capable of economically and accurately characterizing recycled materials as concrete constituents; facing the challenge of moving to a 100 percent reuse policy, as many countries outside of the United States are doing, particularly in Europe. |
Problem Statement MD 1.0. Framework for PCC Mix Design System Development and Integration (Subtrack MD 1)
Track: |
1. Performance-Based Concrete Pavement Mix Design System (MD) |
Subtrack: |
MD 1. PCC Mix Design System Development and Integration |
Approximate Phasing: |
Years 1–3 |
Estimated Cost: |
$300 k |
Subtrack MD 1 (PCC Mix Design System Development and Integration) provides a set of research problem statements that will culminate in a significantly improved state of the art and practice. As the funding becomes available, an initial effort will be necessary to develop a framework for the research to be accomplished within this subtrack. |
Tasks: |
- Examine the problem statements in subtrack MD 1 (PCC Mix Design System Development and Integration), modify as appropriate, and divide them into specific, manageable contracts.
- Arrange the contracts in a carefully sequenced plan that reflects a logical progress of research and available funding.
- Expand each of the broad research problem statements included in the subtrack into a detailed research plan with specific objectives, tasks, and funding recommendations.
- Review and provide direction for the various research contracts underway to ensure that they fulfill their objectives and allow future contracts to use their results. Guide the additional work required if a contract fails to achieve its objectives and additional work is necessary.
|
Benefits: |
An effective, coordinated, and productive research program. |
Products: |
A validated, sequenced, and detailed research framework for this subtrack. |
Implementation: |
This research will provide the organization and validation essential for the success of this subtrack. Implementation of this problem statement will set the stage for the rest of the problem statements in subtrack MD 1 (PCC Mix Design System Development and Integration). |
Problem Statement MD 1.1. PCC Pavement Mix Design System Integration Stage 1: Volumetrics-Based Mix Design (Mix Proportioning)
Track: |
1. Performance-Based Concrete Pavement Mix Design System (MD) |
Subtrack: |
MD 1. PCC Mix Design System Development and Integration |
Approximate Phasing: |
Years 2–5 |
Estimated Cost: |
$500 k–$1 M |
Today’s mix design for concrete paving mixtures relies on experience, often in the form of recipe mixes. While this experience should not be ignored, the specific mixture used in a particular job should not be considered ideal for every job of that type. There can be a wide range of demands on paving jobs (e.g., required time of opening and use of admixtures and supplementary cementitious materials). Optimization techniques are necessary to select the most appropriate mixture that balances these job-specific conditions with long-term durability, while remaining cost effective.
The first step for successfully implementing a mix design system is to develop one that includes methods and parameters with which the industry is familiar. Volumetric-based design (proportioning) includes procedures that specify contents (e.g., minimum cement) and ratios (e.g., water-cement mix) for concrete-making constituents. The guidance given in American Concrete Institute (ACI) 211 committee documents might serve as a starting point for newer methods, supplemented with state-of-the-art proportioning guidance advanced by individuals such as J.M. Shilstone and K.C. Hover, and by agencies including the National Institute of Standards and Technology (NIST) and the U.S. Army Corps of Engineers (USACE), among others. This first stage of the mix design system will employ commonly used lab tests and will limit mix parameter modeling, relying instead on the empirical relationships between mix volumetrics and concrete properties of interest (e.g., strength, workability, and permeability). |
Tasks: |
- Identify and assemble available mix design and proportioning systems.
- Assess user needs for the mix design system and determine ways to incorporate the state of the practice to implement this first stage of the overall system quickly.
- Assemble the requisite models for the system.
- Identify the requisite laboratory test procedures and ensure standardized reporting for input to the mix design system.
- Develop a beta version of the system and solicit peer review.
- Develop a final version of the system and prepare it for training and implementation.
|
Benefits: |
A procedure to allow for job-specific optimization of concrete paving mixtures based largely on currently available technology, rather than current mix proportioning methods based on either previous experience or procedural guidance developed for a broad range of concretes. |
Products: |
Software, guidelines, and supporting products for a new generation of concrete mix design that will optimize concrete mixtures for paving. |
Implementation: |
This first stage of the mix design system will be implementable immediately, and will advance the industry. Further refinements will be made to this system in subsequent stages to capture mix properties and pavement performance more directly. |
Problem Statement MD 1.2. PCC Pavement Mix Design System Integration Stage 2: Property-Based Mix Design
Track: |
1. Performance-Based Concrete Pavement Mix Design System (MD) |
Subtrack: |
MD 1. PCC Mix Design System Development and Integration |
Approximate Phasing: |
Years 4–7 |
Estimated Cost: |
$1 M–$2 M |
While the first stage of the mix design system is based on volumetric ratios and limits, the second stage will offer a more fundamental approach to mix design by measuring and predicting mix properties relevant to pavement performance. The specific properties will be identified when the system itself is developed, and fresh properties such as rheology and hardened properties such as strength and permeability will be included as targets. The result of the second stage will be a mix design system built on the framework established in the first stage. By thus using a common interface and process, implementation of this and subsequent stages will be seamless. |
Tasks: |
- Assemble the requisite models for the system.
- Identify the requisite laboratory test procedures and ensure standardized reporting for input to the mix design system.
- Develop a beta version of the system and solicit peer review.
- Develop a final version of the system and prepare it for training and implementation.
|
Benefits: |
Building on the foundational work conducted under MD 1.1 (PCC Pavement Mix Design System Integration Stage 1: Volumetrics-Based Mix Design), a procedure capable of designing and optimizing a mix for more specific and pertinent concrete properties, possibly including strength, workability, permeability, stiffness, shrinkage, and coefficient of thermal expansion. |
Products: |
Updates to the software, guidelines, and supporting products for concrete mix design and optimization. |
Implementation: |
This second stage of the mix design system will be implementable immediately and will advance the industry. Further refinements will be made to this system in subsequent stages to capture pavement performance more directly. |
Problem Statement MD 1.3. PCC Pavement Mix Design System Integration Stage 3: Performance-Based Mix Design
Track: |
1. Performance-Based Concrete Pavement Mix Design System (MD) |
Subtrack: |
MD 1. PCC Mix Design System Development and Integration |
Approximate Phasing: |
Years 6–9 |
Estimated Cost: |
$1 M–$2 M |
Volumetric- and property-based mix design procedures cannot describe PCC paving mixtures accurately in terms of the mixtures’ impact on pavement performance. The result of these approaches, largely based on an empirical understanding of the effects of properties on performance, is poor design reliability. To offset this shortcoming, this third stage in developing a mix design system will integrate sophisticated pavement performance models. The result will be a seamless tool that can predict various performance measures of a concrete pavement as a function of the concrete mix. Optimization techniques then can be used to select the ideal materials and proportions for achieving the desired level of pavement performance, while maintaining desired levels of other concrete properties (e.g., strength and workability). |
Tasks: |
- Assemble the requisite models for the system.
- Identify the requisite laboratory test procedures and ensure standardized reporting for input to the mix design system.
- Develop a beta version of the system and solicit peer review.
- Develop a final version of the system and prepare it for training and implementation.
|
Benefits: |
A quantum improvement to the mix design process; newly developed tests and models for predicting pavement performance that allow the mix to be optimized to meet the service requirements of structural and material performance. |
Products: |
Updates to the software, guidelines, and supporting products for concrete mix design and optimization. |
Implementation: |
This third stage of the mix design system will be implementable immediately and will advance the industry. Further refinements will be made to this system in subsequent stages to capture the functional performance of the concrete pavement more directly. |
Problem Statement MD 1.4. PCC Pavement Mix Design System Integration Stage 4: Functionally Based Mix Design
Track: |
1. Performance-Based Concrete Pavement Mix Design System (MD) |
Subtrack: |
MD 1. PCC Mix Design System Development and Integration |
Approximate Phasing: |
Years 8–10 |
Estimated Cost: |
$1 M–$2 M |
Pavement and materials engineering decisions often are driven by functional requirements responding to a public need–for example, demands for quieter, smoother, and safer pavements. While concrete pavements can meet all of these functional demands, pavements must be designed appropriately to do so. As part of this fourth stage, a system will be developed to evaluate the effects of concrete materials and mixture on pavement function (e.g., noise, ride quality, texture). By better understanding these relationships, a more rational approach to meeting these functional requirements can be met with improved mix design techniques. Using these procedures, innovative solutions such as two-lift pavements can be designed optimally, with the top layer designed to meet a set of functional demands. |
Tasks: |
- Assemble the requisite models for the system.
- Identify the requisite laboratory test procedures and ensure standardized reporting for input to the mix design system.
- Develop a beta version of the system and solicit peer review.
- Develop a final version of the system and prepare it for training and implementation.
|
Benefits: |
A sophisticated optimization system capable of selecting the most appropriate mixture to meet both performance and functional requirements; a process based on new test procedures that identify the potential for concrete to provide a smooth, safe, and quiet pavement. |
Products: |
Updates to the software, guidelines, and supporting products for concrete mix design and optimization. |
Implementation: |
This final stage of the mix design system will be implementable immediately. It is the final product from this research track. |
Problem Statement MD 1.5. Integrating Recycled Materials into PCC Mix Design System
Track: |
1. Performance-Based Concrete Pavement Mix Design System (MD) |
Subtrack: |
MD 1. PCC Mix Design System Development and Integration |
Approximate Phasing: |
Years 5–10 |
Estimated Cost: |
$500 k–$1 M |
Previous studies have demonstrated that recycled concrete and other recycled materials can be used in new concrete mixtures successfully, as long as the effects of using recycled materials in the mixture are compared to the effects of using virgin materials. This study will build on that work, determining innovative ways to use recycled materials in PCC pavements. Because sustainability is being emphasized increasingly in the United States and abroad, identifying creative uses for recycled materials will sustain and likely extend their desirability. |
Tasks: |
- Investigate using recycled materials in mix designs for shorter performance life pavements, such as an 8-year pavement.
- Investigate using recycled materials for various portions of the product, for example, the fine or course fractions of the aggregate.
- Investigate the boundaries for using recycled materials in bases and two-lift construction.
- Combine the recommended guidance into supplements or adjustments to the new performance-based mix design system.
|
Benefits: |
Mix design procedures capable of economically and accurately characterizing recycled materials as concrete constituents; facing the challenge of moving to a 100 percent reuse policy, as many countries outside of the United States are doing, particularly in Europe. |
Products: |
Guidance and possible modifications to the mix design products that allow users to design a concrete mixture using recycled materials. |
Implementation: |
With pressure to use recycled materials expected to increase, having proper guidance available to users will ensure that the PCC pavement industry is prepared to meet these demands. |
SUBTRACK MD 2. PCC MIX DESIGN LABORATORY TESTING AND EQUIPMENT
This subtrack identifies all the new and upgraded equipment and test procedures needed for the concrete laboratory of the future. This subtrack also addresses a range of opportunities, from improved laboratory mixing to more accelerated durability testing. It concludes with an expert system that connects the test results. Table 3 provides an overview of this subtrack.
Table 3. Subtrack MD 2 overview.
Problem Statement |
Estimated Cost |
Products |
Benefits |
MD 2.0. Framework for PCC Mix Design Laboratory Testing and Equipment (Subtrack MD 2) |
$200 k |
A validated, sequenced, and detailed research framework for this subtrack. |
An effective, coordinated, and productive research program. |
MD 2.1. Laboratory Mixer to Replicate PCC Field Batching |
$1 M–$2 M |
AASHTO-formatted specifications for constructing and operating a laboratory mixer capable of replicating the full-scale batching and mixing process. |
Lab equipment capable of simulating the full-scale batching process, resulting in more representative concrete test specimens and thus a more reliable mix design. |
MD 2.2. Laboratory Compactor to Replicate Concrete Paving Practice |
$1 M–$2 M |
AASHTO-formatted specifications for constructing and operating a laboratory compactor capable of replicating the full-scale compacting (consolidating) effort induced by the vibration and extrusion process of a slipform paver. |
Lab equipment capable of simulating the compacting effort of a slipform paver, resulting in more representative concrete test specimens and thus providing a more reliable mix design. |
MD 2.3. Aggregate Tests for PCC Mix Characterization |
$2 M–$5 M |
Various AASHTO-formatted materials specifications and test procedures capable of evaluating aggregate properties most sensitive to the behavior, durability, performance, and function of both paving concrete and the concrete pavement. |
New and improved aggregate test procedures, providing the mix designer with a more reliable system for selecting and proportioning the optimum aggregate for paving mixtures; ways to avoid potential early durability problems. |
MD 2.4. Performance-Based Cementitious Materials Specifications |
$1 M–$2 M |
New AASHTO-formatted specifications for specifying cementitious materials used in concrete paving mixtures. |
Specifications that will allow the mix designer to make informed choices about the proper materials based on desired level of performance and with a clear understanding of compatibility or performance issues; materials specifications that keep pace with the dramatic changes in the materials themselves. |
MD 2.5. PCC Mix Durability Tests |
$2 M–$5 M |
Various AASHTO-formatted materials specifications and test procedures capable of evaluating the durability of concrete mixtures. |
Test procedures that will identify the potential of durability-related problems in the laboratory during mix design and in the field during placement; alleviation of durability-related issues, ranging from alkali-silica reaction (ASR) to freeze-thaw durability, and including numerous chemical and mechanical distress mechanisms. |
MD 2.6. PCC Mix Compatibility Tests |
$2 M–$5 M |
Various AASHTO-formatted test procedures capable of identifying compatibility problems within a mixture or between the mixture and the paving environment. |
Practical and accurate test procedures for identifying incompatibilities that will reduce cost and improve concrete paving performance; avoiding the increasing possibility of incompatibility from newer constituents added to concrete mixtures as well as conditions during placement, such as climate. |
MD 2.7. PCC Mix Property Test Development |
$2 M–$5 M |
Various AASHTO-formatted test procedures capable of quickly measuring concrete mix properties in a repeatable and reproducible fashion. |
New test procedures for measuring concrete mix properties that constitute a critical component of the mix design system, providing the data necessary by the models for optimization. |
MD 2.8. PCC Mix Thermal Tests |
$500 k–$1 M |
AASHTO-formatted test procedures for measuring critical thermodynamic properties of a concrete mix including calorimetry and thermal transport properties. |
Test procedures for thermal properties of concrete mixes that allow the industry to quantify the impact that the hydration process has on both the early-age behavior and long-term performance of the concrete pavement. |
MD 2.9. PCC Mix Performance Testing Equipment |
$2 M–$5 M |
AASHTO-formatted test procedures for new equipment (or a combination of existing equipment) capable of assessing the performance potential of a concrete mix (e.g., susceptibility to fatigue cracking or spalling). |
Increased concrete pavement quality through tracking the properties that are the most relevant to concrete pavement performance. |
MD 2.10. PCC Mix Functional Testing Equipment |
$2 M–$5 M |
AASHTO-formatted test procedures for new equipment (or a combination of existing equipment) capable of assessing the performance potential of a concrete mix (e.g., ability to construct a smooth, safe, and quiet surface). |
Increased concrete pavement quality through tracking the properties that are the most relevant to concrete pavement performance. |
MD 2.11. Expert System for PCC Mixes |
$1 M–$2 M |
A robust computerized expert system with an intuitive interface that allows users to access best practices and to troubleshoot. |
Preservation of institutional memory, which is fading as many industry experts retire; an expert system that captures their experience in a form that is easily accessible to anyone. |
Problem Statement MD 2.0. Framework for PCC Mix Design Laboratory Testing and Equipment (Subtrack MD 2)
Track: |
1. Performance-Based Concrete Pavement Mix Design System (MD) |
Subtrack: |
MD 2. PCC Mix Design Laboratory Testing and Equipment |
Approximate Phasing: |
Years 1–3 |
Estimated Cost: |
$200 k |
Subtrack MD 2 (PCC Mix Design Laboratory Testing and Equipment) provides a set of research problem statements that will culminate in a significantly improved state of the art and practice. As the funding becomes available, an initial effort will be necessary to develop a framework for the research to be accomplished within this subtrack. |
Tasks: |
- Examine the problem statements in subtrack MD 2 (PCC Mix Design Laboratory Testing and Equipment), modify as appropriate, and divide them into specific, manageable contracts.
- Arrange the contracts in a carefully sequenced plan that reflects a logical progress of research and available funding.
- Expand each of the broad research problem statements included in the subtrack into a detailed research plan with specific objectives, tasks, and funding recommendations.
- Review and provide direction for the various research contracts underway to ensure that they fulfill their objectives and allow future contracts to use their results. Guide the additional work required if a contract fails to achieve its objectives and additional work is necessary.
|
Benefits: |
An effective, coordinated, and productive research program. |
Products: |
A validated, sequenced, and detailed research framework for this subtrack. |
Implementation: |
The research will provide the organization and validation essential for the success of this subtrack. Implementing this problem statement will set the stage for the rest of the problem statements in subtrack MD 2 (PCC Mix Design Laboratory Testing and Equipment). |
Problem Statement MD 2.1. Laboratory Mixer to Replicate PCC Field Batching
Track: |
1. Performance-Based Concrete Pavement Mix Design System (MD) |
Subtrack: |
MD 2. PCC Mix Design Laboratory Testing and Equipment |
Approximate Phasing: |
Years 2–4 |
Estimated Cost: |
$1 M–$2 M |
The techniques used to mix concrete in the laboratory differ from field techniques. For example, differences are evident in charging sequences and mixing energy. This research will develop performance specifications for a new generation of laboratory mixers that can better replicate the full-sized mixers commonly used in concrete paving. The cost and efficiency of a laboratory mixer will be considered. If successful, the new laboratory mixer will evaluate new and innovative PCC mix designs more quickly for research, mix development, and QC. |
Tasks: |
- Identify available technologies and previous trials of similar laboratory mixers.
- Develop additional technology and equipment as needed.
- Compare various concrete mixtures as mixed in full-scale batching operations with those mixed in the new laboratory mixer. Comparisons should be made based on pertinent properties, such as air void structure, strength, and permeability.
- If a new mixer is successfully identified, develop an AASHTO-formatted standard.
|
Benefits: |
Lab equipment capable of simulating the full-scale batching process, resulting in more representative concrete test specimens and thus a more reliable mix design. |
Products: |
AASHTO-formatted specifications for constructing and operating a laboratory mixer capable of replicating the full-scale batching and mixing process. |
Implementation: |
This technology, if identified, can be a key component of the laboratory of the future that will feed key mix test results into the mix design system. |
Problem Statement MD 2.2. Laboratory Compactor to Replicate Concrete Paving Practice
Track: |
1. Performance-Based Concrete Pavement Mix Design System (MD) |
Subtrack: |
MD 2. PCC Mix Design Laboratory Testing and Equipment |
Approximate Phasing: |
Years 2–4 |
Estimated Cost: |
$1 M–$2 M |
The techniques employed to consolidate laboratory specimens (either in the field or in the lab) do not represent the nature of the concrete in place after paving. Differences in the source and energy of consolidation result in differences in the quantity, position, and orientation of the various concrete constituents within the mixture (particularly the air void structure). This research will develop a consolidation device that can better simulate the consolidation process that results from slipform paving (and other placement techniques as needed). |
Tasks: |
- Identify available technologies and previous trials of similar laboratory compactors.
- Develop additional technology and equipment as needed.
- Compare various concrete mixtures compacted in place (behind a slipform paver) with mixtures compacted using the new laboratory compactor. Comparisons should be made based on pertinent properties, such as air void structure, strength, and permeability.
- If a new compactor is identified, develop an AASHTO-formatted standard.
|
Benefits: |
Lab equipment capable of simulating the compacting effort of a slipform paver, resulting in more representative concrete test specimens and thus providing a more reliable mix design. |
Products: |
AASHTO-formatted specifications for constructing and operating a laboratory compactor capable of replicating the full-scale compacting (consolidating) effort induced by the vibration and extrusion process of a slipform paver. |
Implementation: |
This technology, if identified, can be a key component in future laboratories that will feed key mix test results into the mix design system. |
Problem Statement MD 2.3. Aggregate Tests for PCC Mix Characterization
Track: |
1. Performance-Based Concrete Pavement Mix Design System (MD) |
Subtrack: |
MD 2. PCC Mix Design Laboratory Testing and Equipment |
Approximate Phasing: |
Years 2–10 |
Estimated Cost: |
$2 M–$5 M |
Aggregates constitute the largest component of nearly all concrete mixes, by both weight and volume. As a result, the properties of the concrete mix are driven largely by the properties of the aggregates. Because of the high costs of mining and hauling aggregates, research is needed to develop procedures for identifying the most cost effective aggregate sources for a construction project that will meet the user’s durability, performance, and functional requirements. The use of an aggregate will take into account the total cost of the material, including consideration of haul distances, material quality, necessary mix design adjustments, and projected long-term PCC performance. An important aspect of this research will be to develop tests that can identify durable aggregates before the quarry wall is mined. Procedures also will be developed (or current procedures revised) for rapidly determining the ASR potential of concrete mixes made with this aggregate. Additionally, this research will identify ways to protect existing aggregate sources from urban development and to access sources that are difficult to retrieve due to environmental concerns and/or existing urban development. Above all, the test procedures developed here should clearly link to the proposed mix design system.
While this broad research will require further definition during the framework stage, specific aggregate properties expected to be researched under this task include cleanliness, thermal properties (especially coefficient of thermal expansion), and abrasion resistance, among others. To lower transport costs, lightweight aggregates should also be considered and evaluated. |
Tasks: |
- Identify the needs for aggregate laboratory testing, prioritized based on the impact that the properties have on concrete pavement durability and performance.
- Develop AASHTO-formatted aggregate test procedures as needed, establishing clear links to the mix design procedures.
- Connect the aggregate test procedures to other tracks, including those for QC and nondestructive testing (NDT).
|
Benefits: |
New and improved aggregate test procedures, providing the mix designer with a more reliable system for selecting and proportioning the optimum aggregate for paving mixtures; ways to avoid potential early durability problems. |
Products: |
Various AASHTO-formatted materials specifications and test procedures capable of evaluating aggregate properties most sensitive to the behavior, durability, performance, and function of both paving concrete and the concrete pavement. |
Implementation: |
Many new laboratory tests for concrete aggregates are expected. These tests will feed directly into the mix design system and be the foundation for more advanced tests as the state of the art evolves. |
Problem Statement MD 2.4. Performance-Based Cementitious Materials Specifications
Track: |
1. Performance-Based Concrete Pavement Mix Design System (MD) |
Subtrack: |
MD 2. PCC Mix Design Laboratory Testing and Equipment |
Approximate Phasing: |
Years 2–6 |
Estimated Cost: |
$1 M–$2 M |
Cementitious materials as they are currently specified (i.e., by percent replacement) and classified (i.e., by fineness and chemical composition) do not reflect their long-term performance as used in PCC pavements. Current methods of specification and classification also fail to reflect the compatibility of the cementitious materials with aggregates and chemical admixtures. This research will develop a cementitious materials specification that reflects the link between the various properties of the cementitious materials and performance and compatibility issues. The specification should be developed to differentiate the various uses of cementitious materials and their influence on concrete’s fresh properties, such as slump, air void characteristics, and set time; and on concrete’s hardened properties, such as strength and abrasion resistance. Ongoing efforts and specifications being developed through the American Society for Testing and Materials (ASTM) and other organizations should be considered. |
Tasks: |
- Identify existing and ongoing work in developing performance-based specifications for cement, supplementary cementing materials, and cementitious materials, both individually and as a combined material.
- Identify a structure for a performance-based specification that includes a suite of tests rationally connected to pavement performance.
- Develop an AASHTO-formatted draft specification and evaluate it based on the performance of existing pavement sections as well as the known cementitious materials properties.
- Refine the specification based on the evaluation and integrate it into the mix design system.
|
Benefits: |
Specifications that will allow the mix designer to make informed choices about the proper materials, based on desired level of performance and with a clear understanding of compatibility or performance issues; materials specifications that keep pace with the dramatic changes in the materials themselves. |
Products: |
New AASHTO-formatted specifications for specifying cementitious materials used in concrete paving mixtures. |
Implementation: |
A suite of tests will result that can be used to specify cementitious materials through performance predictions. These tests will provide inputs to the mix design system as well as other research tracks, including process (quality) control. |
Problem Statement MD 2.5. PCC Mix Durability Tests
Track: |
1. Performance-Based Concrete Pavement Mix Design System (MD) |
Subtrack: |
MD 2. PCC Mix Design Laboratory Testing and Equipment |
Approximate Phasing: |
Years 2–10 |
Estimated Cost: |
$2 M–$5 M |
Contractors and owner-agencies want to know whether a mix designed to last 30 or more years will last that long when placed in the field, particularly if the pavement is constructed under a warranty or performance-based specification. Likely, no single test will be able to guarantee that a pavement will last 30 or more years, largely because of variable environmental conditions and traffic/wheel loading over the life of the pavement. However, it should be possible to develop test methods to predict the probability that a given concrete mix will last for the intended design life. While this broad research will require further definition during the framework stage, many key mix durability characteristics should be investigated as needed, including freeze-thaw durability, ASR resistance, sulfate attack resistance, and steel corrosion potential. Research is needed to develop accelerated testing methods that more accurately predict the long-term strength, durability, and performance potential of concrete. These tests will allow the owner-agency or contractor to evaluate the mix design before construction as well as after placement, based on core samples removed from the newly placed pavement. An initial step may require additional research to define the minimum water-cement ratio in the field. Meanwhile, premature materials-related distress in concrete pavements appears to be growing more widespread. As a result, additional investigation is needed to identify the various potential causes of the observed problems. Research also is needed to develop improved sulfate-resistant concretes, especially for paving applications, and a broad program of research is needed to mitigate existing ASR conditions. Finally, this task should address air void and steel corrosion issues. |
Tasks: |
- Identify the various durability issues facing concrete pavements, discerning and linking research that addresses both the visible distresses and the fundamental mechanisms.
- Study available equipment and test procedures to identify the potential for and severity of the various deterioration mechanisms as a function of the concrete mix.
- Develop and integrate AASHTO-formatted lab test procedures that feed into the mix design system, allowing users to optimize a mix based on material durability and other criteria.
|
Benefits: |
Test procedures that will identify possible durability-related problems in the laboratory during mix design and in the field during placement; alleviation of durability-related issues ranging from ASR to freeze-thaw durability and including numerous chemical and mechanical distress mechanisms. |
Products: |
Various AASHTO-formatted materials specifications and test procedures capable of evaluating the durability of concrete mixtures. |
Implementation: |
A suite of tests will result that can be used to identify possible durability issues associated with a given mix design. These tests will provide inputs for the mix design system as well as other research tracks, including process (quality) control. |
Problem Statement MD 2.6. PCC Mix Compatibility Tests
Track: |
1. Performance-Based Concrete Pavement Mix Design System (MD) |
Subtrack: |
MD 2. PCC Mix Design Laboratory Testing and Equipment |
Approximate Phasing: |
Years 2–10 |
Estimated Cost: |
$2 M–$5 M |
Mineral and chemical admixtures currently are available for improving the essential properties of a concrete mix (such as strength, permeability, and freeze-thaw resistance). However, these admixtures often are used in combination in a PCC paving mix without a thorough understanding of the materials’ interaction or compatibility. For example, while a proper air void system is essential for durable concrete, excessive air voids reduce the effective cross-sectional area of concrete elements, decreasing concrete strength. Supplementary cementitious materials can cause further complications by creating an unstable air void system in freshly mixed concrete. This problem worsens when certain chemical admixtures also are used in the concrete. Research is needed to study the interaction and compatibility of various admixtures in PCC mixes and the effects that incompatibility may have on concrete properties and pavement performance. Research is also needed to develop accelerated testing methods that more accurately predict incompatibilities and their effects on long-term strength, durability, and performance. These tests will allow the owner-agency or contractor to evaluate the mix design before construction and ensure compatibility of mixture components before concrete placement. |
Tasks: |
- Identify known compatibility problems among PCC admixtures, including the effects admixtures have on concrete properties, such as workability and the air void system.
- Conduct laboratory testing to identify further compatibility problems.
- Determine the effects of incompatible materials on pavement performance.
- Determine the limits on proportions of incompatible materials.
- Develop AASHTO-formatted test procedures and associated equipment that can identify incompatibilities in concrete mixes in the lab.
- Integrate the lab test procedures into the mix design system to allow users to avoid mixture incompatibilities during the mix design process.
|
Benefits: |
Practical and accurate test procedures for identifying incompatibilities that will reduce cost and improve concrete paving performance; avoiding the increasing possibility of incompatibility from newer constituents added to concrete mixtures and due to conditions during placement, such as climate. |
Products: |
Various AASHTO-formatted test procedures capable of identifying compatibility problems within a mixture or between the mixture and the paving environment. |
Implementation: |
Guidelines and test procedures/equipment that identify potential incompatible materials in PCC paving mixes will result. These tests can be used during the mix design process as well as for QC during construction. |
Problem Statement MD 2.7. PCC Mix Property Test Development
Track: |
1. Performance-Based Concrete Pavement Mix Design System (MD) |
Subtrack: |
MD 2. PCC Mix Design Laboratory Testing and Equipment |
Approximate Phasing: |
Years 2–8 |
Estimated Cost: |
$2 M–$5 M |
Mix properties affect both the constructability and long-term performance of PCC pavements. While this broad research will require significant definition during the framework stage, some of the essential mix properties that may warrant investigation include water-cement ratio, permeability, air void system, and workability. While several tests that measure most of these properties currently exist, many of these test procedures are still somewhat crude or time-consuming and give varied results. For example, while it is simple to calculate water-cement ratio based on batch weights, this calculation may not accurately indicate the actual in place water-cement ratio due to addition of water at the job site, inaccurate estimates of aggregate moisture content, or water evaporation during transportation. Thin sections can be used to estimate the water-cement ratio of the hardened concrete, but this is time-consuming and generally occurs long after paving is finished. Research is needed to investigate essential mix properties and develop or further refine procedures for measuring these mix properties quickly and accurately. This research will identify essential mix properties affecting both constructability and pavement performance and develop testing equipment for measuring these properties. |
Tasks: |
- Identify essential mix properties that affect pavement constructability and performance.
- Identify and develop AASHTO-formatted test procedures and associated equipment for measuring these properties.
- Develop new equipment that can be used to measure essential mix properties in the lab and in the field quickly and accurately.
- Develop recommendations for deploying mix property testing equipment.
|
Benefits: |
New test procedures for measuring concrete mix properties that constitute a critical component of the mix design system, providing the data necessary by the models for optimization. |
Products: |
Various AASHTO-formatted test procedures capable of quickly measuring concrete mix properties in a repeatable and reproducible fashion. |
Implementation: |
This work will result in test equipment that will quickly and accurately measure essential mix properties. The test equipment can be used for trial batching during the mix design process and for QC during construction. |
Problem Statement MD 2.8. PCC Mix Thermal Tests
Track: |
1. Performance-Based Concrete Pavement Mix Design System (MD) |
Subtrack: |
MD 2. PCC Mix Design Laboratory Testing and Equipment |
Approximate Phasing: |
Years 3–6 |
Estimated Cost: |
$500 k–$1 M |
The FHWA HIPERPAVTM program is among a number of recent initiatives that have underscored the importance of heat development in concrete pavements. A concrete mixture generally can be characterized by a unique signature representing the amount and rate of heat generated through the hydration process. Measuring this characteristic requires a calorimeter, commonly isothermal, adiabatic, or semi-adiabatic. While the importance of this concrete characteristic has been demonstrated and accepted, no accepted standard for measurement yet exists. This research will develop a nonproprietary test standard suitable for AASHTO adoption. If both practical and cost effective, the standard should spur widespread acceptance of this test for characterizing a concrete mixture. A second goal in developing the specification should be to develop a test rugged enough for use in the field for routine QC. Finally, if the heat signature test is found to be sensitive to pavement performance, tests for other thermal properties should be developed during this task, including tests for the specific heat and thermal conductivity of the PCC. A precedent currently exists for evaluating these parameters within the Mechanistic-Empirical Pavement Design Guide.(1) |
Tasks: |
- Identify the mix thermal properties that are most sensitive for predicting concrete pavement behavior and performance.
- Identify existing lab tests to evaluate the most sensitive properties. Evaluation criteria should include ease of use, proprietary nature, cost, ruggedness, repeatability, and reproducibility.
- Select candidate lab tests and perform a structured evaluation of the equipment, comparing the test results to known standards, if possible.
- Develop specifications suitable for adoption by AASHTO.
|
Benefits: |
Test procedures for thermal properties of concrete mixes that allow the industry to quantify the impact of the hydration process on both the early-age behavior and long-term performance of the concrete pavement. |
Products: |
AASHTO-formatted test procedures for measuring critical thermodynamic properties of a concrete mix, including calorimetry and thermal transport properties. |
Implementation: |
A number of tests will result that can identify the thermal properties of concrete mixes. These tests will provide inputs for the mix design system as well as other research tracks, including process (quality) control and intelligent construction systems (ICS). |
Problem Statement MD 2.9. PCC Mix Performance Testing Equipment
Track: |
1. Performance-Based Concrete Pavement Mix Design System (MD) |
Subtrack: |
MD 2. PCC Mix Design Laboratory Testing and Equipment |
Approximate Phasing: |
Years 5–10 |
Estimated Cost: |
$2 M–$5 M |
Mix performance is one of the most important factors in determining pavement performance, particularly in the long term. Some essential performance properties include freeze-thaw resistance, abrasion resistance, and sulfate-attack resistance, among others. Understanding mix performance will help contractors and owner-agencies develop mixes that meet the design life requirements. Performance problems may not necessarily be caused by durability problems, such as material incompatibility and freeze-thaw resistance, but may simply result from improper mixture proportioning or material selection. This research will examine factors that affect mix performance and thereby affect pavement performance. Testing equipment will be developed to help predict mix performance quickly during the mix design process in the laboratory. |
Tasks: |
- Identify factors (e.g., mix proportions and materials) that affect mixture performance.
- Identify equipment or test procedures that can be used to predict mix performance.
- Refine existing equipment or develop new testing equipment that can be used to predict mix performance quickly.
- Work with contractors and owner-agencies to evaluate the test equipment.
- Develop AASHTO-formatted specifications and associated recommendations for deploying new testing equipment.
|
Benefits: |
Increased concrete pavement quality through tracking the properties that are the most relevant to concrete pavement performance. |
Products: |
AASHTO-formatted test procedures for new equipment (or a combination of existing equipment) capable of assessing the performance potential of a concrete mix (e.g., susceptibility to fatigue cracking or spalling). |
Implementation: |
Testing procedures and equipment that can predict mix performance in the laboratory will result. The testing equipment can be used by contractors and owner-agencies during the mix design process and for QC testing. |
Problem Statement MD 2.10. PCC Mix Functional Testing Equipment
Track: |
1. Performance-Based Concrete Pavement Mix Design System (MD) |
Subtrack: |
MD 2. PCC Mix Design Laboratory Testing and Equipment |
Approximate Phasing: |
Years 7–10 |
Estimated Cost: |
$2 M–$5 M |
Some properties of PCC mixes can affect the functional performance of PCC pavements, including mix placeability (which affects ride quality and tire-pavement noise), abrasion resistance (which affects ride quality and safety), and skid resistance (which affects safety). These PCC mix properties ultimately influence roadway user satisfaction, particularly regarding users’ safety and driving comfort. While these issues may not affect pavement performance directly, significant consequences can result if they are overlooked. For example, a pavement that is too noisy may require expensive sound walls, while a pavement with poor abrasion resistance may rut under studded tires and require costly rehabilitation. Research is needed to investigate the essential functional properties of PCC paving mixes and develop tests for measuring these properties. The tests should allow the contractor or owner-agency to predict functional performance during the mix design process quickly so adjustments can be made before construction. |
Tasks: |
- Identify important properties of PCC mixes that ultimately tie into functional pavement performance.
- Identify test procedures and equipment that can be used to measure these properties.
- Modify existing equipment or develop new equipment that quickly and accurately can measure the properties that predict pavement functional performance.
- Develop AASHTO-formatted specifications and associated recommendations for deploying functional testing equipment.
|
Benefits: |
Increased concrete pavement quality through tracking the properties that are the most relevant to concrete pavement performance. |
Products: |
AASHTO-formatted test procedures for new equipment (or a combination of existing equipment) capable of assessing the performance potential of a concrete mix (e.g., susceptibility to fatigue cracking or spalling). |
Implementation: |
This work will result in testing procedures and equipment that can measure mix properties to predict pavement functional performance. The tests can be used during the mix design process and for QC during construction. |
Problem Statement MD 2.11. Expert System for PCC Mixes
Track: |
1. Performance-Based Concrete Pavement Mix Design System (MD) |
Subtrack: |
MD 2. PCC Mix Design Laboratory Testing and Equipment |
Approximate Phasing: |
Years 3–10 |
Estimated Cost: |
$1 M–$2 M |
Recent concerns about early deterioration of concrete pavement indicate a need for tools that predict concrete durability problems during mixture proportioning and design. No limitations usually exist on the combination of materials that can produce workable and durable concrete. However, constituent materials with certain chemical attributes, such as high levels of alkali, may develop mixture durability problems. Data for long-term tests of concrete mixtures, such as the prism test and screening tests for such constituents as aggregate, are available from many States. Compiling these data into a large database could provide the foundation for an expert system to predict durability problems. This system could indicate the potential for material combination problems and guide engineers and contractors in developing mix designs for pavement projects.
Because of the rapid increase in the number of concrete production materials available, it is important to develop a national database that collects and synthesizes information about all concrete mixes used throughout the United States, from mix design to durability in the field. Clearly documenting the mixes that are successful for a particular application and set of materials and those that are unsuccessful will provide States and others a means to assess their own mixes without having to perform extensive and costly laboratory testing. The database will allow users to determine whether a certain mix design will be successful or unsuccessful. More specifically, this national database will contain information about the concrete materials, mix proportions, locations of use, pavement designs, fresh and hardened concrete properties, construction methods, and the long-term durability performance of the concrete mixes. It also will detail issues such as whether ASR, sulfate attack, freeze-thaw resistance, or any other fresh or hardened concrete property was inappropriate for a particular mixture and site condition. |
Tasks: |
- Identify available sources of information for the expert system, including existing syntheses, expert personnel, and existing databases.
- Identify a structure for the expert system that allows users intuitive access to the information and rapid and efficient population of the information during development.
- Develop a beta version of the system and establish a peer review process.
- Refine the expert system and prepare a form suitable for rapid implementation (e.g., consideration should be made for Internet deployment to keep the system dynamic).
|
Benefits: |
Preservation of institutional memory, which is fading as many industry experts retire; a system that captures their experience in a form that is easily accessible. |
Products: |
A robust computerized expert system with an intuitive interface that allows users to access best practices and troubleshoot. |
Implementation: |
An expert system will be developed that includes an extensive database of experience and other data related to paving concrete mixtures and their performance. This information should be kept dynamic with ongoing updates and feedback. |
SUBTRACK MD 3. PCC MIX DESIGN MODELING
This subtrack addresses the modeling needed to predict slab performance using the laboratory test results identified in the previous subtrack. The modeling also must be coordinated fully throughout this entire track. The research in the following problem statements will develop, improve, adapt, calibrate, and validate PCC pavement models. Table 4 provides an overview of this subtrack.
Table 4. Subtrack MD 3 overview.
Problem Statement |
Estimated Cost |
Products |
Benefits |
MD 3.0. Framework for PCC Mix Design Modeling (Subtrack MD 3) |
$150 k |
A validated, sequenced, and detailed research framework for this subtrack. |
An effective, coordinated, and productive research program. |
MD 3.1. Aggregate Models for Optimizing PCC Mixtures |
$250 k–$500 k |
Thoroughly documented models, also in computerized form, that can be used to optimize the sizing and blending of aggregate stockpiles for a concrete mix. |
Models that optimize the aggregate structure within a concrete mix that have been shown to improve a wide variety of fresh and hardened concrete properties. |
MD 3.2. Fresh PCC Pavement Behavior Models |
$1 M–$2 M |
Thoroughly documented models, also in computerized form, that can be used to predict the behavior of fresh concrete (e.g., rheology). |
Models that predict critical fresh concrete properties as a function of the mix to allow the mix design system to consider these factors more objectively. |
MD 3.3. Hardened PCC Pavement Behavior Models |
$250 k–$500 k |
Thoroughly documented models, also in computerized form, that can be used to predict the behavior of hardened concrete. |
Characterization of hardened concrete properties and behavior to optimize the mix design system for performance. |
MD 3.4. Improved PCC Pavement Performance Models Adaptation |
$250 k–$500 k |
Thoroughly documented models, also in computerized form, that can be used to predict the structural performance (e.g., faulting) of a concrete pavement as a function of mix properties. |
Performance models predicting the linkage between concrete pavement performance and mix properties in the mix design system; supplements for other ongoing efforts to develop these models. |
MD 3.5. Functional PCC Pavement Models Adaptation |
$250 k–$500 k |
Thoroughly documented models, also in computerized form, that can be used to predict the functional performance (e.g., smoothness) of a concrete pavement as a function of mix properties. |
Functional models predicting the linkage between concrete pavement function (e.g., smoothness, safety, noise) and mix properties in the mix design system; supplements for other ongoing efforts to develop these models. |
MD 3.6. Characterizing Concrete Materials Variability |
$250 k–$500 k |
Thorough documentation of each of the sources and degrees of variability in the concrete making process. |
Understanding variability well enough to quantify it objectively, thus remaining cost effective in design. |
MD 3.7. PCC Mix Model Calibration |
$1 M–$2 M |
A calibration report of the various models used to predict concrete mix behavior and concrete pavement performance; adjustments to the various models as needed. |
Proper calibration of the numerous models developed and assembled as part of this research track before widespread distribution of the system. |
MD 3.8. PCC Mix Model Validation |
$500 k–$1 M |
A validation report of the various models used to predict concrete mix behavior and concrete pavement performance; adjustments to the various models as needed. |
A validation effort conducted before release of the mix design system that assesses the predictive ability of the system in situations independent of the development and calibration activities. |
Problem Statement MD 3.0. Framework for PCC Mix Design Modeling (Subtrack MD 3)
Track: |
1. Performance-Based Concrete Pavement Mix Design System (MD) |
Subtrack: |
MD 3. PCC Mix Design Modeling |
Approximate Phasing: |
Years 1–3 |
Estimated Cost: |
$150 k |
Subtrack MD 3 (PCC Mix Design Modeling) provides a set of research problem statements that will culminate in a significantly improved state of the art and practice. As the funding becomes available, an initial effort will be necessary to develop a framework for the research to be accomplished within this subtrack. |
Tasks: |
- Examine the problem statements in subtrack MD 3 (PCC Mix Design Modeling), modify as appropriate, and divide them into specific, manageable contracts.
- Arrange the contracts in a carefully sequenced plan that reflects a logical progress of research and available funding.
- Expand each of the broad research problem statements included in the subtrack into a detailed research plan with specific objectives, tasks, and funding recommendations.
- Review and provide direction for the various research contracts underway to ensure that they fulfill their objectives and allow future contracts to use their results. Guide the additional work required if a contract fails to achieve its objectives and additional work is necessary.
|
Benefits: |
An effective, coordinated, and productive research program. |
Products: |
A validated, sequenced, and detailed research framework for this subtrack. |
Implementation: |
This research will provide the organization and validation essential for the success of this subtrack. Implementation of this problem statement will set the stage for the rest of the problem statements in subtrack MD 3 (PCC Mix Design Modeling). |
Problem Statement MD 3.1. Aggregate Models for Optimizing PCC Mixtures
Track: |
1. Performance-Based Concrete Pavement Mix Design System (MD) |
Subtrack: |
MD 3. PCC Mix Design Modeling |
Approximate Phasing: |
Years 2–4 |
Estimated Cost: |
$250 k–$500 k |
Aggregate packing is an important consideration for optimizing concrete mixtures. Aggregate packing is used to determine the optimal proportions of aggregate for a specific concrete mix, given the aggregates available for a particular project. The goal of aggregate packing is to minimize the voids in the aggregate skeleton, thereby minimizing the amount of cement paste needed. This not only strengthens the mix by maximizing the amount of aggregate, but also minimizes shrinkage, permeability, and porosity.
Additionally, minimizing the amount of cement paste reduces the cost of the mix, as cementitious materials are generally the most expensive component in concrete mixes. Research is needed to develop a method for characterizing the aggregate packing behavior in a concrete mixture based on the aggregate shape and gradation. |
Tasks: |
- Identify existing models suitable for predicting the optimum aggregate structure within a concrete mixture.
- Determine the suitability of the existing models for paving mixtures and conduct research to make necessary adjustments.
- Develop a beta version of the model through a stand-alone interface and evaluate the predictions against lab and field data.
- Develop the final model in a form suitable for rapid incorporation into the mix design system.
|
Benefits: |
Models that optimize the aggregate structure within a concrete mix that have been shown to improve a wide variety of fresh and hardened concrete properties. |
Products: |
Computerized models that can be used to optimize the sizing and blending of aggregate stockpiles for a concrete mix; model documentation. |
Implementation: |
The model developed under this effort will be used in the various predictive modes of the mix design system. |
Problem Statement MD 3.2. Fresh PCC Pavement Behavior Models
Track: |
1. Performance-Based Concrete Pavement Mix Design System (MD) |
Subtrack: |
MD 3. PCC Mix Design Modeling |
Approximate Phasing: |
Years 3–7 |
Estimated Cost: |
$1 M–$2 M |
Fresh PCC behavior affects the constructability and performance of PCC pavements, properties that significantly impact the cost and quality of the finished product. Ensuring optimal fresh PCC properties for a paving operation will improve paving efficiency, reduce labor costs, increase paving speed, and result in a finished product that meets durability and functional requirements. Concrete moisture variations, for example, significantly affect most concrete properties, such as strength and shrinkage. For example, distresses such as plastic shrinkage cracking, delamination spalling, and drying shrinkage cracking result from excessive moisture loss during construction. Likewise, the air void system significantly affects pavement constructability and durability. Modeling can predict fresh PCC behavior and pavement performance efficiently based on fresh PCC properties. Modeling also allows virtual adjustments to be made to PCC mixes before trial batching. Multiscale models are needed to predict and guide the entire concrete paving process, from microstructure to performance. More fundamental models will be developed that tie fresh PCC properties to constructability and performance, and those properties selected for accurate, reliable, and inexpensive field evaluation. These models will take into account various material properties, climatic conditions, admixtures, and construction techniques available for paving operations. The models will then be incorporated into easy-to-use software for both contractors and owner-agencies that can be incorporated into the broader mix design system developed in this research track. |
Tasks: |
- Identify existing models suitable for predicting the behavior of a fresh concrete mixture.
- Determine the suitability of the existing models to paving mixtures and conduct research to make necessary adjustments.
- Develop a beta version of the model through a stand-alone interface and evaluate the predictions against lab and field data.
- Develop the final model in a form suitable for rapid incorporation into the mix design system.
|
Benefits: |
Models that predict critical fresh concrete properties as a function of the mix to allow the mix design system to consider these factors more objectively. |
Products: |
Computerized models that can be used to predict the behavior of fresh concrete (e.g., rheology); model documentation. |
Implementation: |
This work will result in models that can be used to predict constructability and pavement performance based on fresh PCC properties. The models can be used both during the mix design process and as a replacement or supplement to QC tests during construction. |
Problem Statement MD 3.3. Hardened PCC Pavement Behavior Models
Track: |
1. Performance-Based Concrete Pavement Mix Design System (MD) |
Subtrack: |
MD 3. PCC Mix Design Modeling |
Approximate Phasing: |
Years 3–8 |
Estimated Cost: |
$250 k–500 k |
Understanding pavement behavior is essential for the pavement design process, as pavement behavior influences pavement characteristics (e.g., thickness, slab length), joint design, mix design, and construction techniques. Modeling pavement behavior is an efficient way to ensure that the pavement design is adequate for the given conditions. Improved models for understanding hardened PCC pavement behavior are needed to predict critical aspects such as curling and warping, joint functionality, and others. These models should take into account material properties, mix properties, construction conditions, and pavement characteristics. The models should also account for hardened PCC properties, such as creep, coefficient of thermal expansion, zero-stress temperature, slab temperature gradients, pavement support, and environmental conditions, among others. These new models will allow designers, contractors, and owner-agencies to make necessary adjustments to pavement design characteristics during the design process, well in advance of construction, as well as during construction. |
Tasks: |
- Identify existing models suitable for predicting hardened concrete behavior. The models selected should be used in concert with ongoing work in track 2 (Performance-Based Design Guide for New and Rehabilitated Concrete Pavement).
- Determine the suitability of the existing models for paving mixtures and conduct research to make necessary adjustments.
- Develop a beta version of the models through a stand-alone interface and evaluate the predictions against lab and field data.
- Develop the final models in a form suitable for rapid incorporation into the mix design system.
|
Benefits: |
Characterization of hardened concrete properties and behavior to optimize the mix design system for performance. |
Products: |
Computerized models that can be used to predict the behavior of hardened concrete; model documentation. |
Implementation: |
This work will result in models that predict hardened PCC pavement behavior, presented in the form of easy-to-use software. The models can be employed both during the design process and to make design adjustments during construction. This work assumes that the research done in track 2 (Performance-Based Design Guide for New and Rehabilitated Concrete Pavement) has been completed. The estimated cost for this research is above and beyond that in track 2. |
Problem Statement MD 3.4. Improved PCC Pavement Performance Models Adaptation
Track: |
1. Performance-Based Concrete Pavement Mix Design System (MD) |
Subtrack: |
MD 3. PCC Mix Design Modeling |
Approximate Phasing: |
Years 3–7 |
Estimated Cost: |
$250 k–$500 k |
When designing a PCC pavement, the pavement engineer specifies performance goals for both the plastic and hardened concrete. The owner and contractor want to predict this performance to ensure that what is specified and placed will meet the long-term goals. This research will develop new models or refine existing ones to evaluate the characteristics of given mix designs and thus predict long-term pavement performance. The models will take into account the mix properties as well as site characteristics and construction techniques to predict pavement performance. These models will be suitable for use during both the mix design process and construction so that necessary adjustments can be made quickly. |
Tasks: |
- Identify existing models suitable for predicting concrete pavement performance as a function of the concrete mixture. The models selected should be used in concert with ongoing work in track 2 (Performance-Based Design Guide for New and Rehabilitated Concrete Pavement).
- Determine the suitability of existing models to paving mixtures and conduct research to make necessary adjustments.
- Develop beta versions of the models through a stand-alone interface and evaluate the predictions against lab and field data.
- Develop the final models in a form suitable for rapid incorporation into the mix design system.
|
Benefits: |
Performance models predicting the linkage between concrete pavement performance and mix properties in the mix design system; supplements for other ongoing efforts to develop these models. |
Products: |
Computerized models that can be used to predict the structural performance (e.g., faulting) of a concrete pavement as a function of mix properties; model documentation. |
Implementation: |
This work will result in models that predict long-term pavement performance based on mix properties. The models will be usable at the mix design stage as well as during construction to rapidly assess the mixes being placed. This work assumes that the research done in track 2 (Performance-Based Design Guide for New and Rehabilitated Concrete Pavement) has been completed. The estimated cost for this research is above and beyond that in track 2. |
Problem Statement MD 3.5. Functional PCC Pavement Models Adaptation
Track: |
1. Performance-Based Concrete Pavement Mix Design System (MD) |
Subtrack: |
MD 3. PCC Mix Design Modeling |
Approximate Phasing: |
Years 4–9 |
Estimated Cost: |
$250 k–$500 k |
Functional PCC pavement performance ensures user satisfaction and pavement durability. Smoother pavements, for example, are not only more desirable to the user, but also reduce dynamic loading on the pavement, increasing pavement life. However, smoothness is not the only functional performance aspect. Tire-pavement noise and skid resistance are also key functional performance factors. The concrete mixture impacts these functional performance factors. Mixes that are difficult to place, for example, can result in rough pavements. Models are needed to predict functional performance during the mix design process. Predicting functional performance will allow contractors or owner-agencies to adjust the mix design so that the finished pavement will meet the functional requirements. The new models will also allow contractors to adjust the mix design as materials or construction conditions change during pavement placement. |
Tasks: |
- Identify existing models suitable for predicting the functional properties of a concrete pavement as a function of the concrete mixture. The models selected should be used in concert with ongoing work in track 2 (Performance-Based Design Guide for New and Rehabilitated Concrete Pavement).
- Determine the suitability of the existing models to paving mixtures and conduct research to make adjustments necessary
- Develop beta versions of the models through a stand-alone interface and evaluate the predictions against lab and field data.
- Develop the final models in a form suitable for rapid incorporation into the mix design system.
|
Benefits: |
Functional models predicting the linkage between concrete pavement function (e.g., smoothness, safety, noise) and mix properties in the mix design system; supplements for other ongoing efforts to develop these models. |
Products: |
Computerized models that can be used to predict the functional performance (e.g., smoothness) of a concrete pavement as a function of mix properties; model documentation. |
Implementation: |
This work will result in models to predict pavement functional performance based on mix design properties and materials. The models can be used during both the mix design process and construction. This work assumes that the research done in track 2 (Performance-Based Design Guide for New and Rehabilitated Concrete Pavement) has been completed. The estimated cost for this research is above and beyond that in track 2. |
Problem Statement MD 3.6. Characterizing Concrete Materials Variability
Track: |
1. Performance-Based Concrete Pavement Mix Design System (MD) |
Subtrack: |
MD 3. PCC Mix Design Modeling |
Approximate Phasing: |
Years 2–7 |
Estimated Cost: |
$250 k–$500 k |
This research will document the sources of and solutions to concrete pavement variability. A better understanding of variability in current PCC pavement construction is needed, including stockpiles, batching, transport, placement, finishing, and curing. Following a synthesis of work done in this area, the researcher should advance strategies to minimize variability through improved equipment, measuring devices, and operator influences. The impact of reducing variability should be assessed for: (1) contractor profitability, (2) specification tolerances, and (3) design safety factors. By reducing variability, modern pavement design procedures can be used, resulting in more cost effective designs that also improve overall pavement performance. The overall influence of variability on design safety and product acceptance must be better understood, especially product acceptance as it relates to the size of the product sample. |
Tasks: |
- Identify information sources for assessing the variability of concrete mixtures and other elements of the concrete paving process. This work should be done in concert with ongoing work in track 2 (Performance-Based Design Guide for New and Rehabilitated Concrete Pavement).
- Synthesize variability information and collect additional information as needed.
- Identify inputs for the mix design system that variability information would affect, considering the most appropriate means to consider risk and reliability in the mix design procedure.
|
Benefits: |
Understanding variability well enough to quantify it objectively, thus remaining cost effective in design. |
Products: |
Thorough documentation of each of the sources and degrees of variability in the concrete-making process. |
Implementation: |
This research will result in a better understanding of the sources of variability in the concrete paving process. This information, in turn, can be used in the mix design system to develop more reliable and cost effective designs. This work assumes that the research done in track 2 (Performance-Based Design Guide for New and Rehabilitated Concrete Pavement) has been completed. The estimated cost for this research is above and beyond that in track 2. |
Problem Statement MD 3.7. PCC Mix Model Calibration
Track: |
1. Performance-Based Concrete Pavement Mix Design System (MD) |
Subtrack: |
MD 3. PCC Mix Design Modeling |
Approximate Phasing: |
Years 4–8 |
Estimated Cost: |
$1 M–$2 M |
Developing the sophisticated PCC mix design system proposed in this research track will require numerous models and components that are based on varying degrees of calibrated relationships. Integrating these components into a larger system, however, introduces the need for an overall calibration. This calibration is required if users are to have confidence in the mix design system’s predictions. This research will organize a calibration effort that will evaluate a wide range of materials, site conditions, climates, construction techniques, pavement characteristics, and other variables. The result will be recommendations for adjustments to the mix design procedure that will increase the reliability of the predictions. |
Tasks: |
- Identify variables for calibration, such as materials, site conditions, and climates.
- Identify typical ranges for each variable.
- Perform laboratory calibrations for the different variables that can be tested in the lab.
- Perform onsite calibration tests where needed.
- Calibrate models for deployment.
|
Benefits: |
Proper calibration of the numerous models developed and assembled as part of this research track before widespread distribution of the system. |
Products: |
A calibration report of the various models used to predict concrete mix behavior and concrete pavement performance; adjustments to the various models as needed. |
Implementation: |
This work will result in calibrated models for the mix design system, considering a wide range of materials, site conditions, climates, construction techniques, and pavement characteristics. |
Problem Statement MD 3.8. PCC Mix Model Validation
Track: |
1. Performance-Based Concrete Pavement Mix Design System (MD) |
Subtrack: |
MD 3. PCC Mix Design Modeling |
Approximate Phasing: |
Years 5–10 |
Estimated Cost: |
$500 k–$1 M |
Although the PCC mix design system models will be calibrated for a wide range of materials, site conditions, climates, construction techniques, and pavement characteristics, validation using actual paving projects is required for the system to gain wide acceptance. This research will organize and conduct independent validation studies of the mix design system on actual paving projects. The projects will be selected to ensure that a wide variety of materials and conditions exists between projects. |
Tasks: |
- Identify possible candidate paving projects for model validation under varied conditions.
- Implement the mix design system during the paving project mix design process.
- Track problems or issues in the mix design system during paving operations.
- Based on the validation projects, make necessary modifications to the mix design system.
|
Benefits: |
A validation effort conducted before releasing the mix design system that assesses the predictive ability of the system in situations independent of the development and calibration activities. |
Products: |
A validation report of the various models used to predict concrete mix behavior and concrete pavement performance; adjustments to the various models as needed. |
Implementation: |
This work will result in a validated mix design system that is ready for incorporation into owner-agency pavement mix design practices. |
SUBTRACK MD 4. PCC MIX DESIGN EVALUATION AND IMPLEMENTATION
This subtrack addresses field evaluation and implementation procedures, provides a mechanism for user feedback, and prepares the products from this research track to be adopted. The following problem statements outline mix design system conferences and workshops, mobile laboratory demonstrations, Web-based training, and other technology transfer activities. Table 5 provides an overview of this subtrack.
Table 5. Subtrack MD 4 overview
Problem Statement |
Estimated Costs |
Products |
Benefits |
MD 4.0. Framework for PCC Mix Design Evaluation and Implementation (Subtrack MD 4) |
$150 k |
A validated, sequenced, and detailed research framework for this subtrack. |
An effective, coordinated, and productive research program. |
MD 4.1. PCC Pavement Mix Design System Conferences and Workshops |
$2 M–$5 M |
A series of conferences and workshops that include presenting the proper use of the new mix design system along with a background of the development. |
Workshops and conferences that provide vital components of the technology transfer for the performance-based mix design system; activities that offer users hands-on experience with the mix design system at various stages; valuable feedback for developing the system. |
MD 4.2. Support for FHWA Mobile Concrete Laboratory Demonstrations |
$1 M–$2 M |
A series of conferences and workshops that present the proper use of the new mix design system along with a background of the development; further demonstration of the Mobile Concrete Research Laboratory nationwide. |
A mobile concrete laboratory that allows potential users a firsthand look at available technology; an instrumental component in technology transfer; demonstrations of the performance-based mix design system along with the requisite laboratory tests. |
MD 4.3. Standardized Databases and Electronic Communications Protocols for the Concrete Pavement Industry |
$250 k–$500 k |
Industry standards for nomenclature and for measuring and reporting information and data used by the concrete paving industry. |
Industry standards that allow data to be assembled in a common format, resulting in a more efficient development effort; standardized system for the multifaceted concrete pavement industry to use in pooling materials, equipment, and other disciplines. |
MD 4.4. Web-Based Training System for Implementation of PCC Research Products |
$500 k–$1 M |
A Web-based training system capable of effectively training potential users of the numerous products developed under the performance-based mix design track. |
Mix design system training from remote locations; a feasible and cost effective training medium for an age in which broadband Internet access is becoming standard. |
MD 4.5. PCC Mix Design Equipment for States |
$1 M–$2 M |
Funding for purchasing the equipment recommended for use in the performance-based mix design system. |
Funding made available to allow State agencies to use the new equipment recommended as part of the mix design system. |
Problem Statement MD 4.0. Framework for PCC Mix Design Evaluation and Implementation (Subtrack MD 4)
Track: |
1. Performance-Based Concrete Pavement Mix Design System (MD) |
Subtrack: |
MD 4. PCC Mix Design Evaluation and Implementation |
Approximate Phasing: |
Years 1–3 |
Estimated Cost: |
$150 k |
Subtrack MD 4 (PCC Mix Design Evaluation and Implementation) provides a set of research problem statements that will culminate in a significantly improved state of the art and practice. As the funding becomes available, an initial effort will be necessary to develop a framework for the research to be accomplished within this subtrack. |
Tasks: |
- Examine the problem statements in subtrack MD 4 (PCC Mix Design Evaluation and Implementation), modify as appropriate, and divide them into specific, manageable contracts.
- Arrange the contracts in a carefully sequenced plan that reflects a logical progress of research and available funding.
- Expand each of the broad research problem statements included in the subtrack into a detailed research plan with specific objectives, tasks, and funding recommendations.
- Review and provide direction for the various research contracts underway to ensure that they fulfill their objectives and allow future contracts to use their results. Guide the additional work required if a contract fails to achieve its objectives and additional work is necessary.
|
Benefits: |
An effective, coordinated, and productive research program. |
Products: |
A validated, sequenced, and detailed research framework for this subtrack. |
Implementation: |
This research will provide the organization and validation essential for the success of this subtrack. Implementation of this problem statement will set the stage for the rest of the problem statements in subtrack MD 4 (PCC Mix Design Evaluation and Implementation). |
Problem Statement MD 4.1. PCC Pavement Mix Design System Conferences and Workshops
Track: |
1. Performance-Based Concrete Pavement Mix Design System (MD) |
Subtrack: |
MD 4. PCC Mix Design Evaluation and Implementation |
Approximate Phasing: |
Years 3–10 |
Estimated Cost: |
$2 M–$5 M |
Transportation agencies are often slow to adopt new technologies and techniques because they are unfamiliar with these innovations and lack resources for research. Workshops and conferences will provide an ideal environment for familiarizing and training agencies in the PCC pavement mix design system. These technology transfer activities will allow both contractors and owner-agencies to better understand the aspects of the mix design system and the benefits this system will provide for pavement construction and performance. |
Tasks: |
- Identify States and/or industry representatives willing to host mix design system workshops and conferences.
- Assemble pertinent information on the mix design system components.
- Conduct workshops and conferences, presenting mix design system information and providing hands-on training for the mix design software.
|
Benefits: |
Workshops and conferences that provide vital components of the technology transfer for the performance-based mix design system; activities that offer users hands-on experience with the mix design system at various stages; valuable feedback for developing the system. |
Products: |
A series of conferences and workshops that include presenting the proper use of the new mix design system along with a background of the development. |
Implementation: |
This research will result in numerous workshops and conferences on the PCC pavement mix design system at various venues throughout the United States. |
Problem Statement MD 4.2. Support for FHWA Mobile Concrete Laboratory Demonstrations
Track: |
1. Performance-Based Concrete Pavement Mix Design System (MD) |
Subtrack: |
MD 4. PCC Mix Design Evaluation and Implementation |
Approximate Phasing: |
Years 3–10 |
Estimated Cost: |
$1 M–$2 M |
The FHWA Mobile Concrete Laboratory brings the lab to the jobsite to introduce contractors and owner-agencies to concrete mix design and testing technology. With the development of a new mix design system and new testing equipment and procedures, onsite demonstrations using the Mobile Concrete Laboratory are necessary for introducing this new technology to contractors and owner-agencies. For this purpose, this research will provide funding to send the Mobile Concrete Research Laboratory to various projects throughout the United States. |
Tasks: |
- Identify potential projects and contractors and owner-agencies interested in Mobile Concrete Laboratory demonstrations.
- Demonstrate the mix design system and new concrete testing equipment at these project locations.
|
Benefits: |
A mobile concrete laboratory that allows potential users a firsthand look at available technology; an instrumental component in technology transfer; demonstrations of the performance-based mix design system along with the requisite laboratory tests. |
Products: |
A series of conferences and workshops that presents the proper use of the new mix design system along with a background of the development; further demonstration of the Mobile Concrete Laboratory nationwide. |
Implementation: |
This research will provide continued funding for sending the Mobile Concrete Laboratory to PCC paving projects throughout the country. |
Problem Statement MD 4.3. Standardized Databases and Electronic Communications Protocols for the Concrete Pavement Industry
Track: |
1. Performance-Based Concrete Pavement Mix Design System (MD) |
Subtrack: |
MD 4. PCC Mix Design Evaluation and Implementation |
Approximate Phasing: |
Years 2–10 |
Estimated Cost: |
$250 k–$500 k |
Successfully implementing all research products and practices depends on effective communication. Ineffective communication often delays concrete products bound for the market, delays and duplicates paperwork between suppliers and vendors, reduces management efficiency, loses the value added when concrete-related computerized guidelines work together, and decreases data accuracy due to transaction/conversion between incompatible systems or formats, among other problems.
As computing and Internet technologies advance, electronic communication forms become ubiquitous and convenient modes of effective communication. Extensible Markup Language (XML), originally designed to satisfy the demands of large-scale electronic publishing, has become an open standard for exchanging a wide variety of Web data. XML facilitates data generation and reading and ensures that the data structure is unambiguous. The benefits of using a common XML schema in the concrete pavement industries include distributing information (e.g., concrete mixture design specifications, concrete research findings, pavement design/construction information) through the Web or any electronic publishing and syndication service; processing commerce transactions electronically (concrete batch tickets, concrete lab test results); providing transparent management control in a multivendor environment (various contractors, concrete testing labs); formulating queries to obtain desired information (e.g., mix design alternatives, pros and cons of specific practices) from knowledge-based systems; and providing interoperability among various computerized concrete design guidelines/analyses. Both the PCA/NRMCA and ACI committee 235 have initiated XML schema for the concrete industries. However, a lack of funding and resources limited progress. NCHRP Project 20–64, “XML Schemas for Exchange of Transportation Data (TransXML),” is currently being conducted.
This work will result in a ConcreteXML schema based on the World Wide Web Consortium XML schema design principles and requirements. This ConcreteXML schema, with its own namespace, then can be merged into the TransXML under the overall XML schema framework by the consortium. In developing this working schema, an important task will include standardizing terms and XML vocabularies in all concrete pavement-related industries (e.g., State pavement management, State specifications, cement producers, admixture producers, aggregate suppliers, concrete testing labs, mix design firms, concrete batch plants, material delivery, paving companies, financial/inventory). Thus, any XML documents based in ConcreteXML can be validated easily and automated for quick and error-proof electronic data exchange. |
Tasks: |
- Identify systems for standardizing databases and electronic communications, such as XML.
- Standardize terms and XML vocabularies in all concrete paving-related industries.
- Implement a standard ConcreteXML or comparable system for all databases and electronic communications.
|
Benefits: |
Industry standards that allow data to be assembled in a common format, resulting in a more efficient development effort; standardized system for the multifaceted concrete pavement industry to use in pooling materials, equipment, and other disciplines. |
Products: |
Industry standards for nomenclature and for measuring and reporting information and data used by the concrete paving industry. |
Implementation: |
This work will result in a standardized protocol for databases and electronic communications for the concrete pavement industries |
Problem Statement MD 4.4. Web-Based Training System for Implementation of PCC Research Products
Track: |
1. Performance-Based Concrete Pavement Mix Design System (MD) |
Subtrack: |
MD 4. PCC Mix Design Evaluation and Implementation |
Approximate Phasing: |
Years 6–10 |
Estimated Cost: |
$500 k–$1 M |
Research project results often are implemented inadequately and thus are used incompletely. A mechanism for adequate research product technology transfer is therefore necessary. A Web-based service that contains information about research products from different research organizations should be developed. This Web-based service should include actual case studies, online software applications, documentation, and other resources to make research findings more accessible to the paving community. |
Tasks: |
- Compile information about new testing equipment and procedures and mix design software, including thorough documentation, case studies, downloadable software applications, photos, and video, if necessary.
- Develop Web-based training modules for the software and testing equipment.
- Create and maintain a Web site for accessing the training modules, providing updates for new products or refinements to existing products.
|
Benefits: |
Mix design system training from remote locations; a feasible and cost effective training medium for an age in which broadband Internet access is becoming standard. |
Products: |
A Web-based training system capable of effectively training potential users of the numerous products developed under the performance-based mix design track. |
Implementation: |
This research will result in Web-based training modules for new mix design software and testing equipment. |
Problem Statement MD 4.5. PCC Mix Design Equipment for States
Track: |
1. Performance-Based Concrete Pavement Mix Design System (MD) |
Subtrack: |
MD 4. PCC Mix Design Evaluation and Implementation |
Approximate Phasing: |
Years 6–10 |
Estimated Cost: |
$1 M–;$2 M |
Most States lack the funding necessary to purchase their own new and advanced equipment. Moreover, many contractors are reluctant to invest large amounts of capital in new equipment unless they are sure it will be profitable. Therefore, a vehicle that helps States purchase needed equipment should be established to promote such equipment for mix design testing. |
Tasks: |
Establish requirements for helping States purchase advanced equipment to test mix designs. |
Benefits: |
Funding made available to allow State agencies to use the new equipment recommended as part of the mix design system. |
Products: |
Funding for purchasing the equipment recommended for use in the performance-based mix design system. |
Implementation: |
This work will result in a vehicle that helps States purchase advanced equipment for PCC pavement mix design testing. |