Long-Term Plan for Concrete Pavement Research and Technology - The Concrete Pavement Road Map: Volume II, Tracks
Track 5. Concrete Pavement Equipment Automation and Advancements (EA)
TRACK 5 (EA) OVERVIEW
The problem statements in this track propose process improvements and equipment developments for high-speed, high-quality concrete paving equipment. Research on technologies like those listed below are needed to meet the concrete paving industry’s projected needs and the traveling public’s expectations for highway performance in the future:
- Next generation of concrete batching equipment.
- Next generation of concrete placement equipment that addresses new construction processes.
- Behind-the-paver equipment to improve quality, speed, and cost-effectiveness.
- Mechanized ways to place and control subdrains and other foundation elements.
- Next generation of equipment that will integrate the removal/replacement of the slab in one-pass construction.
- Improved repair processes that decrease the time of operations and provide the workforce and traveling public with less exposure.
- Methods for evaluating the new equipment on actual constructions projects.
Efforts in the area of equipment automation and advancements will require collaborative partnerships between equipment manufacturers, contractors, and State highway agencies. After equipment concepts have been established, it is hoped that contractors and industry will be willing to invest in developing new equipment. Involving contractors and industry from the start is essential for ensuring the equipment is practical for actual implementation. This private funding will also help introduce the new equipment into everyday practice much faster than if development and implementation costs were solely carried by the government.
Stringless, global positioning system (GPS) control of slipform paving equipment is just one example of many pioneering technologies that, if further developed and tested, could increase efficiency, lower costs, and increase performance for the concrete paving industry.
The following introductory material summarizes the goal and objectives for this track and the gaps and challenges for its research program. A phasing chart is included to show the approximate sequencing of the problem statements in the track. A table of estimated costs provides the projected cost range for each problem statement, depending on the research priorities and scope determined in implementation. The problem statements, grouped into subtracks, then follow.
Track Goal
Concrete paving process improvements and equipment advancements will expedite and automate PCC pavement rehabilitation and construction, resulting in high-quality concrete pavements, reduced waste, and safer working environments.
Track Objectives
- Develop batching equipment that will produce better quality concrete mixes by optimizing the materials used and allowing rapid adjustment of mix proportions.
- Improve paving techniques and equipment to produce higher quality concrete pavements, while optimizing material use and reducing construction time and processes.
- Improve techniques for curing, texturing, and jointing concrete pavements, while allowing pavements to be opened to traffic more quickly.
- Improve equipment and techniques for expedited subbase stabilization and subdrain installation.
- Develop equipment for rapid in place reconstruction of concrete pavements using existing/recycled materials.
- Improve and automate techniques and equipment for rapid CPR.
- Introduce contractors and owner-agencies to new advanced equipment and help them purchase such equipment.
Research Gaps
- Lack of formal partnering that justifies equipment development economics.
- Lack of framework and justification for automation technology.
- Lack of incentives to develop innovative and durable equipment.
- Lack of automated material/concrete property characterization.
- Lack of knowledge about advancing higher order use of recycled concrete materials.
- Lack of a continuing working relationship among equipment manufacturers, contractors, and State highway agencies.
Research Challenges
- Develop advanced automated equipment that contractors and owner-agencies can afford to invest in and bring the equipment industry and the State highway agencies together to work strategically in a cost-sharing atmosphere.
- Develop equipment that will automate construction processes but still allow human intervention to make necessary adjustments and to assure that the workforce is trained effectively.
- Develop equipment and techniques that are practical to use and durable under construction conditions and establish performance specifications that allow the use of innovative equipment.
- Identify the effect of material properties (e.g., aggregate shape and texture) and concrete properties (e.g., rheology) on pavement performance and determine how these properties can be identified using automated equipment.
- Determine the usability of recycled materials in light of long-term pavement performance, learn how to properly crush and grade the recycled material, and find innovative uses for the fines.
- Establish long-term relationships that jointly define the potential equipment advancement market and determine ways to breakdown evaluation processes at State borders.
Research Track 5 (EA) Phasing
The horizontal bar chart in figure 5 shows the approximate time phasing of the problem statements in this track grouped by subtrack across 10 years. The phasing information here is a summary of the approximate phasing included with the full written description of each problem statement in this track.
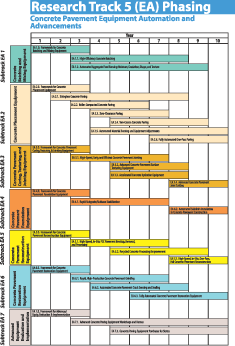
Click to enlarge or view alternative text
Figure 5. Track 5 (EA) subtrack and problem statement phasing chart.
Research Track 5 (EA) Estimated Costs
Table 24 shows the estimated costs for this research track.
Table 24. Research track 5 (EA) estimated costs.
Problem Statement |
Estimated Cost |
Subtrack EA 1. Concrete Batching and Mixing Equipment |
EA 1.0. Framework for Concrete Batching and Mixing Equipment (Subtrack EA 1) |
$150 k |
EA 1.1. High-Efficiency Concrete Batching |
$250 k–$500 k |
EA 1.2. Automated Aggregate Feed Sensing: Moisture, Gradation, Shape, and Texture |
$500 k–$1 M |
Subtrack EA 2. Concrete Placement Equipment |
EA 2.0. Framework for Concrete Placement Equipment (Subtrack EA 2) |
$200 k |
EA 2.1. Stringless Concrete Paving |
$1 M-$2 M |
EA 2.3. Zero-Clearance Paving |
$500 k–$1 M |
EA 2.4. Two-Course Concrete Paving |
$1 M–$2 M |
EA 2.5. Automated Material Sensing and Equipment Adjustments |
$2 M–$5 M |
EA 2.6. Fully Automated One-Pass Paving |
$2 M–$5 M |
Subtrack EA 3. Concrete Pavement Curing, Texturing, and Jointing Equipment |
EA 3.0. Framework for Concrete Pavement Curing, Texturing, and Jointing Equipment (Subtrack EA 3) |
$150 k |
EA 3.1. High-Speed, Early, and Efficient Concrete Pavement Jointing |
$1 M–$2 M |
EA 3.2. Advanced Concrete Pavement Surface Texturing Equipment |
$1 M–$2 M |
EA 3.3. Accelerated Concrete Hydration Equipment |
$1 M–$2 M |
EA 3.4. Advanced Concrete Pavement Joint Forming |
$500 k–$1 M |
Subtrack EA 4. Concrete Pavement Foundation Equipment |
EA 4.0. Framework for Concrete Pavement Foundation Equipment (Subtrack EA 4) |
$150 k |
EA 4.1. Rapid Subgrade/Subbase Stabilization |
$1 M–$2 M |
EA 4.2. Automated Subdrain Installation in Concrete Pavement Construction |
$1 M–$2 M |
Subtrack EA 5. Concrete Pavement Reconstruction Equipment |
EA 5.0. Framework for Concrete Pavement Reconstruction Equipment (Subtrack EA 5) |
$200 k |
EA 5.1. High-Speed, In Situ PCC Pavement Breakup, Removal, and Processing |
$2 M–$5 M |
EA 5.2. Recycled Concrete Processing/Improvement |
$1 M–$2 M |
EA 5.3. High-Speed, In Situ, One-Pass, Full Concrete Pavement Reconstruction |
$2 M–$5 M |
Subtrack EA 6. Concrete Pavement Restoration Equipment |
EA 6.0. Framework for Concrete Pavement Restoration Equipment (Subtrack EA 6) |
$150 k |
EA 6.1. Rapid, High-Production Concrete Pavement Grinding |
$1 M–$2 M |
EA 6.2. Automated Concrete Pavement Crack Sensing and Sealing |
$500 k–$1 M |
EA 6.3. Fully Automated Concrete Pavement Restoration Equipment |
$1 M–$2 M |
Subtrack EA 7. Advanced Equipment Evaluation and Implementation |
EA 7.0. Framework for Advanced Equipment Evaluation and Implementation (Subtrack EA 7) |
$150 k |
EA 7.1. Advanced Concrete Paving Equipment Workshops and Demonstrations |
$2 M–$5 M |
EA 7.2. Concrete Paving Equipment Purchases for States |
$2 M–$5 M |
Track 5 (EA) |
Total |
$25.65 M–$56.15 M |
Track Organization: Subtracks and Problem Statements
Track 5 (EA) problem statements are grouped into seven subtracks:
- Subtrack EA 1. Concrete Batching and Mixing Equipment.
- Subtrack EA 2. Concrete Placement Equipment.
- Subtrack EA 3. Concrete Pavement Curing, Texturing, and Jointing Equipment.
- Subtrack EA 4. Concrete Pavement Foundation Equipment.
- Subtrack EA 5. Concrete Pavement Reconstruction Equipment.
- Subtrack EA 6. Concrete Pavement Restoration Equipment.
- Subtrack EA 7. Advanced Equipment Evaluation and Implementation.
Each subtrack is introduced by a brief summary of the subtrack’s focus and a table listing the titles, estimated costs, products, and benefits of each problem statement in the subtrack. The problem statements follow.
SUBTRACK EA 1. CONCRETE BATCHING AND MIXING EQUIPMENT
.This subtrack focuses on the batch plant operation, looking for joint ventures with industry to design the next generation of batching equipment. Table 25 provides an overview of this subtrack.
Table 25. Subtrack EA 1 overview.
Problem Statement |
Estimated Cost |
Products |
Benefits |
EA 1.0. Framework for Concrete Batching and Mixing Equipment (Subtrack EA 1) |
$150 k |
A validated, sequenced, and detailed research framework for this subtrack. |
An effective, coordinated, and productive research program. |
EA 1.1. High- Efficiency Concrete Batching |
$250 k–$500 k |
More efficient batching techniques and equipment. |
More efficient batching techniques and equipment that use materials better, produce higher quality concrete mixes, and allow for automatic adjustments to concrete mixes. |
EA 1.2. Automated Aggregate Feed Sensing: Moisture, Gradation, Shape, Texture |
$500 k–$1 M |
Automated, high-speed aggregate property classification techniques and equipment. |
Automated aggregate classification, allowing concrete mixes to be finetuned automatically based on the aggregate properties and allowing immediate approval or rejection of a given material, resulting in higher quality concrete mixes. |
Problem Statement EA 1.0. Framework for Concrete Batching and Mixing Equipment (Subtrack EA 1)
Track: |
5. Equipment Automation and Advancements (EA) |
Subtrack: |
EA 1. Concrete Batching and Mixing Equipment |
Approximate Phasing: |
Years 1–3 |
Estimated Cost: |
$150 k |
Subtrack EA 1 (Concrete Batching and Mixing Equipment) provides a set of research problem statements that will culminate in a significantly improved state of the art and practice. As the funding becomes available, an initial effort will be necessary to develop a framework for the research to be accomplished within this subtrack. |
Tasks:
- Examine the problem statements in subtrack EA 1 (Concrete Batching and Mixing Equipment), modify as appropriate, and divide them into specific, manageable contracts.
- Arrange the contracts in a carefully sequenced plan that reflects a logical progress of research and available funding.
- Expand each of the broad research problem statements included in the subtrack into a detailed research plan with specific objectives, tasks, and funding recommendations.
- Review and provide direction for the various research contracts underway to ensure that they fulfill their objectives and allow future contracts to use their results. Guide the additional work required if a contract does not achieve its objectives and additional work is necessary.
|
Benefits: |
An effective, coordinated, and productive research program. |
Products: |
A validated, sequenced, and detailed research framework for this subtrack. |
Implementation: |
This research will provide the organization and validation essential for the success of this subtrack. Implementation of this problem statement will set the stage for the rest of the problem statements in subtrack EA 1 (Concrete Batching and Mixing Equipment). |
Problem Statement EA 1.1. High-Efficiency Concrete Batching (Subtrack EA 1)
Track: |
5. Equipment Automation and Advancements (EA) |
Subtrack: |
EA 1. Concrete Batching and Mixing Equipment |
Approximate Phasing: |
Years 3–8 |
Estimated Cost: |
$250 k–$500 k |
Concrete pavement mixes are evolving continually, becoming more complex as new admixtures are added to produce a better product. More complex mixes require greater attention to mix batching to ensure that proper equipment is being used and that the mixer is charged with the right proportion of each material at the proper time. For example, with newer, more complex mixes, the rheological mix properties must meet the specified requirements for the particular application ( slipform paving, fixed-form paving), because rheological properties can affect significantly the efficiency of the paving operation and the quality of the finished product. More efficient batching processes that also can be adjusted automatically are needed. For example, a passing cold front during a paving operation may prompt the contractor to reduce the amount of fly ash in the mix to account for the changing climatic conditions. New, efficient batching processes will allow this type of adjustment without delaying delivery of the fresh concrete. In addition, alternative batching techniques, such as on-grade ultrasonic concrete mixers that mix the concrete at the paving operation rather than at a central batch plant to improve paving efficiency, need to be examined.
These examples suggest that better understanding the aggregate properties is important for paving operations and pavement performance. Digital imaging processing techniques have been developed for aggregate sample scanning and shape and texture analysis. However, current technology is timeconsuming and expensive, and the equipment may not be suited for use at a batch plant or quarry. Therefore, research that improves imaging equipment efficiency or develops new technology is needed so that a large sample of aggregate can be scanned and analyzed quickly. Sieve analyses and moisture content measurements accurately depict aggregate gradation and moisture content, respectively, but both can be time-consuming and represent a small sample of the aggregate used for a given project. Techniques that can quickly determine the gradation and moisture content of a much larger aggregate sample could benefit concrete paving projects. New technologies such as these will help contractors and owner-agencies quickly determine the suitability of a given aggregate. The aggregate then can be either rejected or reprocessed (i.e., crushed) or the pay factor adjusted before the aggregate is used in a concrete mix. |
Tasks:
- Identify the most commonly used batching operations for concrete paving projects.
- Identify current batching operation limitations based on contractor and owner-agency experience.
- Work with contractors and industry (batch plant manufacturers, paving machine manufacturers) to modify or develop existing or new batching equipment that will permit automatic adjustments.
- Identify alternative batching techniques (such as on-grade ultrasonic mixers) that could improve paving efficiency and quality.
- Recommend new batching equipment or modifications to existing equipment as well as alternative batching techniques.
|
Benefits: |
More efficient batching techniques and equipment that use materials better, produce higher quality concrete mixes, and allow for automatic adjustments to concrete mixes. |
Products: |
More efficient batching techniques and equipment. |
Implementation: |
This research will recommend new batching equipment or modifications to existing equipment as well as alternative batching techniques. |
Problem Statement EA 1.2. Automated Aggregate Feed Sensing: Moisture, Gradation, Shape, and Texture
Track: |
5. Equipment Automation and Advancements (EA) |
Subtrack: |
EA 1. Concrete Batching and Mixing Equipment |
Approximate Phasing: |
Years 3–9 |
Estimated Cost: |
$500 k–$1 M |
Aggregate properties, such as shape, texture, moisture content, and gradation, significantly influence the packing and bonding characteristics of coarse aggregates as well as the rheological properties of concrete mixes. For example, elongated and flaky aggregates do not pack together in a concrete mix as well as rounded aggregates. Smooth, rounded aggregates do not bond as strongly as crushed aggregates with jagged, fractured faces. Well-graded aggregates tend to produce more workable mixes with better durability. Aggregates with a higher moisture content than predicted produce a mix with a lower watercement ratio, which can weaken hardened concrete and reduce its durability. |
Tasks:
- Identify aggregate properties (shape, texture, moisture content, gradation) that affect concrete mix properties and pavement performance
- Identify existing techniques for determining aggregate shape, texture, gradation, and moisture content and the advantages and disadvantages of each.
- Modify or develop new or existing equipment to scan large aggregate samples rapidly.
- Conduct field trials or case studies with existing (modified) or new equipment.
|
Benefits: |
Automated aggregate classification, allowing concrete mixes to be automatically fine-tuned based on the aggregate properties and allowing immediate approval or rejection of a given material, resulting in higher quality concrete mixes. |
Products: |
Automated, high-speed aggregate property classification techniques and equipment. |
Implementation: |
This research will result in new equipment for faster classification of aggregate properties in the field. |
SUBTRACK EA 2. CONCRETE PLACEMENT EQUIPMENT
This subtrack focuses on the placement equipment, looking for joint ventures with industry to design the next generation of batching equipment. It also addresses new construction processes that depend on equipment. Table 26 provides an overview of this subtrack.
Table 26. Subtrack EA 2 overview.
Problem Statement |
Estimated Cost |
Products |
Benefits |
EA 2.0. Framework for Concrete Placement Equipment (Subtrack EA 2) |
$200 k |
A validated, sequenced, and detailed research framework for this subtrack. |
An effective, coordinated, and productive research program. |
EA 2.1. Stringless Concrete Paving |
$1 M-$2 M |
Stringless concrete paving technology and equipment. |
Stringless paving technology that will eliminate common pavement smoothness issues, such as chord effects, sag effects, and random survey effects, and improve paving efficiency. |
EA 2.2. Roller- Compacted Concrete Paving |
$250 k–$500 k |
Guidelines and recommendations for using roller-compacted concrete (RCC) in highway pavements. |
Guidelines and recommendations that can help construct durable, highstrength RCC pavements, possibly beginning with pilot projects and eventually progressing toward urban highway pavements. |
EA 2.3. Zero-Clearance Paving |
$500 k–$1 M |
Advancements in zero- or minimum-clearance paving equipment. |
Zero- or minimum-clearance paving machines that will enhance the flexibility of PCC paving, permitting slipform paving next to fixed barriers and eliminating the need for widening the paver tracks. |
EA 2.4. Two-Course Concrete Paving |
$1 M–$2 M |
Guidelines and recommendations for twocourse paving construction procedures. |
Guidelines and recommendations that can be used for constructing twocourse concrete pavements, beginning with pilot projects and progressing to urban highway pavements. |
EA 2.5. Automated Material Sensing and Equipment Adjustments |
$2 M–$5 M |
Fully automated, material sensing concrete paving equipment. |
Material sensing paving equipment that will detect changes in concrete rheological properties as it is fed into the paver and automatically adjust paver speed, vibration, and extrusion pressure, resulting in better quality concrete pavement. |
EA 2.6. Fully Automated One-Pass Paving |
$2 M–$5 M |
One-pass concrete paving equipment. |
One-pass paving equipment that will perform all processes in a single pass, including concrete placement, finishing, texturing, curing, and jointing, making adjustments automatically and resulting in a very efficient paving operation. |
Problem Statement EA 2.0. Framework for Concrete Placement Equipment (Subtrack EA 2)
Track: |
5. Equipment Automation and Advancements (EA) |
Subtrack: |
EA 1. Concrete Batching and Mixing Equipment |
Approximate Phasing: |
Years 1–3 |
Estimated Cost: |
$200 k |
Subtrack EA 2 (Concrete Placement Equipment) provides a set of research problem statements that will culminate in a significantly improved state of the art and practice. As the funding becomes available, an initial effort will be necessary to develop a framework for the research to be accomplished within this subtrack. |
Tasks:
- Examine the problem statements in subtrack EA 2 (Concrete Placement Equipment), modify as appropriate, and divide them into specific, manageable contracts.
- Arrange the contracts in a carefully sequenced plan that reflects a logical progress of research and available funding.
- Expand each of the broad research problem statements included in the subtrack into a detailed research plan with specific objectives, tasks, and funding recommendations.
- Review and provide direction for the various research contracts underway to ensure that they fulfill their objectives and allow future contracts to use their results. Guide the additional work required if a contract fails to achieve its objectives and additional work is necessary.
|
Benefits: |
An effective, coordinated, and productive research program. |
Products: |
A validated, sequenced, and detailed research framework for this subtrack. |
Implementation: |
This research will provide the organization and validation essential for the success of this subtrack. Implementation of this problem statement will set the stage for the rest of the problem statements in subtrack EA 2 (Concrete Placement Equipment). |
Problem Statement EA 2.1. Stringless Concrete Paving
Track: |
5. Equipment Automation and Advancements (EA) |
Subtrack: |
EA 1. Concrete Batching and Mixing Equipment |
Approximate Phasing: |
Years 2–8 |
Estimated Cost: |
$1 M–$2 M |
Modern concrete paving construction conventionally uses physical guidance systems, such as stringlines, for the slipform pavers. However, several drawbacks of using the stringline system may mar the finished pavement surface (e.g., the chord effect, sag effect, and random survey effect). Although the adverse impacts of the stringline system may be mitigated with stringline length optimization techniques, another solution uses stringless technologies. Stringless paving is not a new idea—it often is used to construct asphalt pavement, and various stringless paving technologies have been developed, tested, and improved in the past decade. However, stringless paving is still a fairly new technology, and only limited slipform pavers have been used in experiments with stringless technologies. Developing stringless paving technologies commonly begins with collecting survey data and building a database, such as the Geographic Information System (GIS). Computer-aided design and modeling for the pavement system follows. A noncontact guidance system then ties the paving surface to the 3D GIS and guides the movements of all paving equipment during construction. Noncontact sensors can be either GPS- or laserbased. Stringless paving research shows that laser-based sensors are more accurate, with a vertical deviation of 10 millimeters (mm) (0.4 inch). To achieve stringless paving successfully, the survey data and onsite guidance system must update the equipment’s position quickly. A good system deviation may be 2.5 mm (0.1 inch) vertically and 5.1 mm (0.2 inch) horizontally. Despite the limited success mentioned above, achieving the target vertical control deviation when paving through horizontal/vertical curves and superelevated sections is difficult.
This research will explore better guidance systems to improve stringless concrete paving technologies, even for paving at horizontal/vertical curves and superelevation. The TRIZ system, an algorithm known for systematic innovation and technical creativity, is recommended to achieve the research goals. This research also will demonstrate the system for future concrete technology innovation. |
Tasks:
- Identify existing stringless paving technology for PCC pavements.
- Identify advantages and disadvantages of existing technology and places for improvement.
- Work with owner-agencies and industry representatives to modify existing equipment or develop new equipment for stringless paving.
- Conduct field trials of the improved technology and recommend further refinement.
|
Benefits: |
Stringless paving technology that will eliminate common pavement smoothness issues, such as chord effects, sag effects, and random survey effects, and improve paving efficiency. |
Products: |
Stringless concrete paving technology and equipment. |
Implementation: |
This work will develop stringless concrete paving equipment. |
Problem Statement EA 2.2. Roller-Compacted Concrete Paving
Track |
5. Equipment Automation and Advancements (EA) |
Subtrack: |
EA 2. Concrete Placement Equipment |
Approximate Phasing: |
Years 3–6 |
Estimated Cost: |
$250 k–$500 k |
RCC has been used in concrete pavements for many years, primarily in industrial areas such as shipping yards, in which heavy wheel loads are common and pavement smoothness is not a concern. RCC has proven to be a very durable, high-strength paving material for these applications, and placement techniques now use common equipment similar to HMA paving machines. RCC pavement’s poor smoothness characteristics have made contractors reluctant to use RCC for highway pavement applications. However, recent advancements in diamond grinding technology and improvements to slipform paving equipment indicate that RCC should be examined more thoroughly for highway pavement applications. Improved durability, reduced permeability, and reduced slab thickness make RCC an appealing alternative for highway pavement applications. This research will explore the feasibility of using RCC for highway facilities in light of new advancements in pavement technology. |
Tasks:
- Identify projects that have used RCC pavement, documenting design details, materials, construction procedures, and problems with the materials or construction.
- Identify potential issues associated with using RCC for highway pavements.
- Identify potential solutions that make RCC viable for highway pavements.
- Work with owner-agencies to develop RCC pavement pilot projects.
- Develop guidelines and recommendations for using RCC in highway pavements.
|
Benifits: |
Guidelines and recommendations that can help construct durable, high-strength RCC pavements, possibly beginning with pilot projects and eventually progressing toward urban highway pavements. |
Products: |
Guidelines and recommendations for using RCC in highway pavements. |
Implementation: |
This research will result in guidelines and recommendations for using RCC in highway pavements. |
Problem Statement EA 2.3. Zero-Clearance Paving
Track: |
5. Equipment Automation and Advancements (EA) |
Subtrack: |
EA 2. Concrete Placement Equipment |
Approximate Phasing: |
Years 4–7 |
Estimated Cost: |
$500 k–$1 M |
Zero-clearance (or minimum-clearance) pavers often are required next to fixed objects, such as median barriers or guardrails. Although most HMA pavers are zero-clearance pavers, the size and weight of PCC slipform pavers make zero (or minimum) clearance very difficult. However, because such paving equipment always will be needed, this technology must be developed further. This research will examine the requirements for zero-clearance pavers, the current technology, and refinements to existing technology or new developments needed for zero-clearance paving applications. |
Tasks:
- Identify available zero- or minimum-clearance paving equipment and its limitations.
- Identify contractor and owner-agency requirements for zero-clearance paving.
- Work with contractors and industry representatives to modify existing equipment or develop new equipment for zero-clearance paving.
- Work with owner-agencies and contractors to conduct case studies or pilot projects to evaluate any new or refined zero-clearance pavers.
|
Benifits: |
Zero- or minimum-clearance paving machines that will enhance the flexibility of PCC paving, permitting slipform paving next to fixed barriers and eliminating the need for wider paver tracks. |
Products: |
Advancements in zero- or minimum-clearance paving equipment. |
Implementation: |
This work will result in new or modified equipment for zero-clearance paving. |
Problem Statement EA 2.4. Two-Course Concrete Paving
Track: |
5. Equipment Automation and Advancements (EA) |
Subtrack: |
EA 2. Concrete Placement Equipment |
Approximate Phasing |
Years 5–9 |
Estimated Cost |
$1 M–$2 M |
Two-course concrete pavements can reduce construction costs while providing a pavement performance equal to or greater than that of conventional concrete pavement. Recent advances in ultrathin whitetopping (UTW) have shown that a durable, high-strength concrete surface has advantages in highstress areas. Some sections of two-course pavement have been constructed in the United States, but these sections have not been analyzed (or the results have not been distributed to a large audience of pavement specifiers). For example, a 1993 European demonstration in Michigan was a two-course construction pavement. However, followup studies have not been conducted to determine project performance. Also, RCC for the lower course of a two-course system has not been researched. |
Tasks:
- Identify two-course pavements that have been constructed in the United States and abroad, documenting materials, construction techniques, and performance.
- Identify advantages and disadvantages of the various two-course paving techniques.
- Identify needs or applications for two-course paving from owner-agencies.
- Develop recommendations for two-course paving materials and construction procedures.
- Work with owner-agencies to develop case studies or pilot projects that use two-course paving techniques.
|
Benifits: |
Guidelines and recommendations that can be used for constructing two-course concrete pavements, beginning with pilot projects and progressing to urban highway pavements. |
Products: |
Guidelines and recommendations for two-course concrete paving construction procedures. |
Implementation: |
This research will recommend two-course concrete paving materials and construction procedures. |
Problem Statement EA 2.5. Automated Material Sensing and Equipment Adjustments
Track: |
5. Equipment Automation and Advancements (EA) |
Subtrack: |
EA 2. Concrete Placement Equipment |
Approximate Phasing: |
Years 4–10 |
Estimated Cost: |
$2 M–$5 M |
Rheological concrete properties greatly affect slipform paving operations. slipform paving machines extrude concrete, making it necessary to fluidize the material while forcing it through the mold (pan). Variations in concrete properties, such as workability, can alter the extrusion effectiveness and vary pavement shape and smoothness results. These variations also affect the timing of finishing, surface texturing, and curing. To maintain consistent extrusion pressures and improve slipforming results, it is necessary to identify concrete’s rheological properties and use this information as feedback for the slipform paving machine. The speed, vibration, and extrusion pressure of the paving machine and the timing of other operations then can be adjusted for the varying concrete mix properties. The more automated this process is, the less human error will be a factor, and the more quickly adjustments can be made. First, research must determine the optimal operating ranges for paving machines and the timing of paving operations for concrete mixes with varying rheological properties. This information then can be used to program paving trains to adjust speed and timing automatically based on concrete properties. In addition, techniques for automatically measuring or detecting concrete rheological properties need to be developed. These techniques will allow for a fully automated paving process that will check concrete properties continuously and adjust the operation as necessary. |
Tasks: |
- Identify concrete mix properties that affect slipform paving operations.
- Determine optimal operating ranges (speed, vibration, extrusion pressure, timing of finishing, texturing, and curing) for common slipform pavers based on varying concrete rheological properties.
- Develop semiautomated or fully automated techniques for measuring the rheological properties of fresh concrete deposited in front of the paver.
- Work with industry representatives and paving contractors to modify paving equipment to adjust the operation automatically based on concrete properties.
- Work with industry representatives and owner-agencies to conduct pilot projects or field trials using the automated equipment.
|
Benefits: |
Material sensing paving equipment that will detect changes in concrete rheological properties as it is fed into the paver and make automatic adjustments to paver speed, vibration, and extrusion pressure, resulting in better quality concrete pavement. |
Products: |
Fully automated, material sensing concrete paving equipment. |
Implementation: |
This work will fully automate paving equipment that can measure concrete properties and adjust the paving operations based on those properties. |
Problem Statement EA 2.6. Fully Automated One-Pass Paving
Track: |
5. Equipment Automation and Advancements (EA) |
Subtrack: |
EA 2. Concrete Placement Equipment |
Approximate Phasing: |
Years 7–10 |
Estimated Cost: |
$2 M–$5 M |
Several components constitute a typical paving operation, including concrete placement, finishing, texturing (turf drag or tining), curing, and joint sawcutting. These processes usually are separate from each other, often slowing the paving operation and preventing the pavement from being opened to traffic quickly. Incorporating these numerous, independent paving activities into a single automated one-pass process should be explored further. To meet fast-track criteria, dowels and tie bars could be vibrated in, the joint grooves could be formed into the fresh concrete, and the surface texturing and curing would follow immediately. No subsequent operations behind the slipform operation would be required. |
Tasks: |
- Identify existing automated processes for slipform paving operations (automatic dowel bar/tie bar inserters, automatic finishers, etc.).
- Develop new techniques for other automated slipform paving processes (such as joint forming).
- Work with slipform industry representatives and contractors to integrate all processes into an automated one-pass operation.
- Work with contractors and owner-agencies to conduct pilot projects using one-pass slipform equipment.
|
Benefits: |
One-pass paving equipment that will perform all processes in a single pass, including concrete placement, finishing, texturing, curing, and jointing, making adjustments automatically and resulting in a very efficient paving operation. |
Products: |
One-pass concrete paving equipment. |
Implementation: |
This work will result in automated one-pass concrete paving equipment. |
SUBTRACK EA 3. CONCRETE PAVEMENT CURING, TEXTURING, AND JOINTING EQUIPMENT
This subtrack focuses on the key behind-the-paver equipment. It aims to advance the state of the art beyond labor-intensive operations to improve quality, speed, and cost-effectiveness. Table 27 provides an overview of this subtrack.
Table 27. Subtrack EA 3 overview
Problem Statement |
Estimated Cost |
Products |
Benefits |
EA 3.0. Framework for Concrete Pavement Curing, Texturing, and Jointing Equipment (Subtrack EA 3) |
$150 k |
A validated, sequenced, and detailed research framework for this subtrack. |
An effective, coordinated, and productive research program. |
EA 3.1. High-Speed, Early, and Efficient Concrete Pavement Jointing |
$1 M–$2 M |
High-speed jointing equipment for early-age concrete and/or best practice recommendations for sawcutting. |
New techniques and equipment for early jointing and recommendations for sawcutting to ensure that joints are cut cleanly at the earliest possible time; improved joints that result in better pavement performance. |
EA 3.2. Advanced Concrete Pavement Surface Texturing Equipment |
$1 M–$2 M |
New equipment for surface texturing. |
New surface texturing equipment and techniques that will meet consistent skid resistance, tire-pavement noise, and rideability requirements without compromising the pavement surface integrity. |
EA 3.3. Accelerated Concrete Hydration Equipment |
$1 M–$2 M |
Equipment for accelerating the hydration of PCC pavements. |
Accelerated hydration techniques that allow joints to be cut sooner and permit earlier opening to traffic without using exotic, fast-setting mixes. |
EA 3.4. Advanced Concrete Pavement Forming |
$500 k–$1 M |
New equipment or techniques for forming joints. |
New techniques and equipment for forming joints that will improve joint quality and allow for earlier jointing, resulting in better joint control and performance. |
Problem Statement EA 3.0. Framework for Concrete Pavement Curing, Texturing, and Jointing Equipment (Subtrack EA 3)
Track: |
5. Equipment Automation and Advancements (EA) |
Subtrack: |
EA 3. Concrete Pavement Curing, Texturing, and Jointing Equipment |
Approximate Phasing: |
Years 1–3 |
Estimated Cost: |
$150 k |
Subtrack EA 3 (Concrete Pavement Curing, Texturing, and Jointing Equipment) provides a set of research problem statements that will culminate in a significantly improved state of the art and practice. As the funding becomes available, an initial effort will be necessary to develop a framework for the research to be accomplished within this subtrack. |
Tasks: |
- Examine the problem statements in subtrack EA 3 (Concrete Pavement Curing, Texturing, and Jointing Equipment), modify as appropriate, and divide them into specific, manageable contracts.
- Arrange the contracts in a carefully sequenced plan that reflects a logical progress of research and available funding.
- Expand each of the broad research problem statements included in the subtrack into a detailed research plan with specific objectives, tasks, and funding recommendations.
- Review and provide direction for the various research contracts underway to ensure that they fulfill their objectives and allow future contracts to use their results. Guide the additional work required if a contract does not achieve its objectives and additional work is necessary.
|
Benefits: |
An effective, coordinated, and productive research program. |
Products: |
A validated, sequenced, and detailed research framework for this subtrack. |
Implementation: |
This research will provide the organization and validation essential for the success of this subtrack. Implementation of this problem statement will set the stage for the rest of the problem statements in subtrack EA 3 (Concrete Pavement Curing, Texturing, and Jointing Equipment). |
Problem Statement EA 3.1. High-Speed, Early, and Efficient Concrete Pavement Jointing
Track: |
5. Equipment Automation and Advancements (EA) |
Subtrack: |
EA 3. Concrete Pavement Curing, Texturing, and Jointing Equipment |
Approximate Phasing: |
Years 3–7 |
Estimated Cost: |
$1 M–$2 M |
Joints can affect PCC structural and functional pavement performance significantly, making jointing a critical process in pavement construction. While many techniques can be used, such as inserts and hand grooving, sawcutting has been the predominant technique due to the end product’s high quality and relatively low cost. However, sawcutting requires special considerations. From a construction standpoint, sawcutting joints as quickly as possible opens the pavement to traffic more quickly. However, sawcutting the joints too soon causes raveling distress along the joint, while uncontrolled cracking may develop if joints are cut too late. Also, sawcut depth is usually specified as one-third or one-fourth of the pavement depth to ensure that cracks form at predetermined locations, but this depends on the maximum aggregate size used, among other factors. Previous efforts have developed guidelines to determine the sawcutting window and optimum depth, but no standard procedures or guidelines have been adopted. Additionally, new jointing techniques/technologies must be considered if the construction windows are to be narrowed further. Research that fully examines and documents sawcutting and alternative high-speed jointing techniques is needed to prevent delays in opening the pavement to traffic. |
Tasks: |
- Identify previously used, early-age jointing techniques, documenting advantages and disadvantages of the different techniques.
- Identify pavement sections that have used each of the jointing techniques and document joint performance.
- Work with industry and contractors to modify existing early-age jointing techniques or develop new ones.
- Develop recommendations and/or best practice guidelines for high-speed, early-age jointing techniques.
- Work with owner-agencies and contractors to evaluate new jointing techniques on pilot projects.
|
Benefits: |
New techniques and equipment for early jointing and recommendations for sawcutting to ensure that joints are cut cleanly at the earliest possible time; improved joints that result in better pavement performance. |
Products: |
High-speed jointing equipment for early-age concrete and/or best practice recommendations for sawcutting. |
Implementation: |
This work will recommend best practice guidelines for high-speed, early-age jointing techniques. |
Problem Statement EA 3.2. Advanced Concrete Pavement Surface Texturing Equipment
Track: |
5. Equipment Automation and Advancements (EA) |
Subtrack: |
EA 3. Concrete Pavement Curing, Texturing, and Jointing Equipment |
Approximate Phasing: |
Years 5–8 |
Estimated Cost: |
$1 M–$2 M |
Surface texture is a critical aspect of concrete pavements, affecting safety, tire-pavement noise, and rideability. Surface texture provides skid resistance—particularly important in wet driving conditions— and can even channel water away from the pavement-tire interface, in the case of tining. However, surface texture also increases tire-pavement noise and degrades rideability if not properly constructed. Unfortunately, some of the best surface textures for providing skid resistance also can be the noisiest and the most difficult to construct properly.
This research will investigate new surface texturing equipment and techniques that provide the desired balance of skid resistance, low noise levels, and rideability. Texturing equipment should provide a consistent surface texture soon after finishing the pavement surface. Also, surface texturing techniques should not compromise the concrete surface integrity. |
Tasks: |
- Identify commonly used surface texturing techniques and equipment and their limitations.
- Identify new, documented surface texturing techniques and equipment to improve skid resistance, reduce tire-pavement noise, and improve rideability.
- Determine typical characteristics (skid resistance, tire-pavement noise, rideability) documented for each technique.
- Work with contractors and industry to develop and/or apply new surface texturing equipment and techniques.
- Develop recommendations for new use of surface texturing techniques and equipment.
- Work with owner-agencies and contractors to evaluate new techniques and equipment using pilot projects.
|
Benefits: |
New surface texturing equipment and techniques that will meet consistent skid resistance, tire-pavement noise, and rideability requirements without compromising the pavement surface integrity. |
Products: |
New equipment for surface texturing. |
Implementation: |
This work will result in surface texturing equipment and/or techniques and recommendations for their use. |
Problem Statement EA 3.3. Accelerated Concrete Hydration Equipment
Track: |
5. Equipment Automation and Advancements (EA) |
Subtrack: |
EA 3. Concrete Pavement Curing, Texturing, and Jointing Equipment |
Approximate Phasing: |
Years 5–8 |
Estimated Cost: |
$1 M–$2 M |
Accelerating PCC hydration will allow the material to reach its required strength faster. For PCC pavements, accelerating the hydration process will help the pavement to be finished, textured, jointed, and cured more quickly, allowing it to open to traffic earlier. Techniques for accelerating hydration should be explored further so they can be applied to fast-track PCC paving operations. Microwave-induced setting is one such technique that instantly heats the concrete internally to initiate the setting, allowing finishing, jointing, texturing, and curing to be completed in the trailing forms and eliminating the need to return for joint sawing. Induction heating, which heats steel fibers in the concrete mixture with an externally applied electric current, is another technique that can accelerate setting. |
Tasks: |
- Identify accelerated hydration techniques and equipment that could be applied to concrete pavement construction.
- Determine the advantages and disadvantages of each technique, analyzing the cost versus benefit and investigating the effects of accelerated hydration on PCC pavement performance.
- Work with contractors and industry representatives to develop techniques/equipment for accelerated hydration.
- Work with owner-agencies and contractors to develop pilot studies for implementing accelerated hydration on PCC pavement projects.
|
Benefits: |
Accelerated hydration techniques that allow joints to be cut sooner and permit earlier opening to traffic without using exotic, fast-setting mixes. |
Products: |
Equipment for accelerating the hydration of PCC pavements. |
Implementation: |
This work will result in accelerated hydration techniques/equipment for PCC pavement construction. |
Problem Statement EA 3.4. Advanced Concrete Pavement Joint Forming
Track: |
5. Equipment Automation and Advancements (EA) |
Subtrack: |
EA 3. Concrete Pavement Curing, Texturing, and Jointing Equipment |
Approximate Phasing: |
Years 8–10 |
Estimated Cost: |
$500 k–$1 M |
Sawcutting long has been the preferred method for forming contraction joints in PCC pavements. Lightweight, early-entry saws have been developed; these allow the contractor to sawcut joints much earlier than did previous saws However, because concrete saws are rotary, raveling and spalling often can result, even if the concrete has hardened sufficiently. Sawcutting is also time-consuming and can give variable results, depending on the saw operator.
This research will investigate advanced joint cutting techniques. Laser cutting, water jets, or other highenergy techniques may provide much better results under a more controlled process. Low-tech solutions such as the bobsled also might be refined in this research. New techniques should provide better, more consistent results for early-age joint cutting. Ideally, new techniques will permit joint cutting immediately after surface texturing, allowing a one-pass paving process. |
Tasks: |
- Identify techniques and equipment that could be used for early-age concrete joint forming.
- Evaluate new techniques/equipment for their applicability to concrete pavement jointing, including speed, cutting consistency, and cost.
- Work with industry and contractors to apply new jointing techniques and equipment to paving operations.
- Work with contractors and owner-agencies to develop pilot projects that use the new jointing techniques and equipment.
|
Benefits: |
New techniques and equipment for forming joints that will improve joint quality and allow for earlier jointing, resulting in better joint control and performance. |
Products: |
New equipment or techniques for forming joints. |
Implementation: |
This work will result in new techniques and/or equipment for forming joints that are suitable for early-age concrete pavement. |
SUBTRACK EA 4. CONCRETE PAVEMENT FOUNDATION EQUIPMENT
This subtrack focuses on ways to place and control the foundation elements, including ways to mechanize the placement of subdrains. Table 28 provides an overview of this subtrack.
Table 28. Subtrack EA 4 overview.
Problem Statement |
Estimated Cost |
Products |
Benefits |
EA 4.0. Framework for Concrete Pavement Foundation Equipment (Subtrack EA 4) |
$150 k |
A validated, sequenced, and detailed research framework for this subtrack. |
An effective, coordinated, and productive research program. |
EA 4.1. Rapid Subgrade/Subbase Stabilization |
$1 M–$2 M |
New techniques and equipment for rapid subgrade/subbase stabilization. |
Rapid subgrade/subbase stabilization that will allow subgrade/subbase support to be repaired and restored before placing new pavement in a short construction window. |
EA 4.2. Automated Subdrain Installation in Concrete Pavement Construction |
$1 M–$2 M |
New techniques and equipment for automated subdrain installation. |
Automated subdrain installation that permits the process to be completed in a single pass immediately in front of the paver, thus expediting construction. |
Problem Statement EA 4.0. Framework for Concrete Pavement Foundation Equipment (Subtrack EA 4)
Track: |
5. Equipment Automation and Advancements (EA) |
Subtrack: |
EA 4. Concrete Pavement Foundation Equipment |
Approximate Phasing: |
Years 1–3 |
Estimated Cost: |
$150 k |
Subtrack EA 4 (Concrete Pavement Foundation Equipment) provides a set of research problem statements that will culminate in a significantly improved state of the art and practice. As the funding becomes available, an initial effort will be necessary to develop a framework for the research to be accomplished within this subtrack. |
Tasks: |
- Examine the problem statements in subtrack EA 4 (Concrete Pavement Foundation Equipment), modify as appropriate, and divide them into specific, manageable contracts.
- Arrange the contracts in a carefully sequenced plan that reflects a logical progress of research and available funding.
- Expand each of the broad research problem statements included in the subtrack into a detailed research plan with specific objectives, tasks, and funding recommendations.
- Review and provide direction for the various research contracts underway to ensure that they fulfill their objectives and allow future contracts to use their results. Guide the additional work required if a contract fails to achieve its objectives and additional work is necessary.
|
Benefits: |
An effective, coordinated, and productive research program. |
Products: |
A validated, sequenced, and detailed research framework for this subtrack. |
Implementation: |
This research will provide the organization and validation essential for the success of this subtrack. Implementation of this problem statement will set the stage for the rest of the problem statements in subtrack EA 4 (Concrete Pavement Foundation Equipment). |
Problem Statement EA 4.1. Rapid Subgrade/Subbase Stabilization
Track: |
5. Equipment Automation and Advancements (EA) |
Subtrack: |
EA 4. Concrete Pavement Foundation Equipment |
Approximate Phasing: |
Years 3–7 |
Estimated Cost: |
$1 M–$2 M |
One of the problems with fast-track paving (i.e., overnight construction using fast-setting/high-early strength or precast concrete) is stabilizing the existing base material. The pavements being replaced often have deteriorated due to problems with the base material, such as pumping or swelling, resulting in voids beneath the pavement. Using conventional paving techniques, the base material can be replaced or treated (cement/lime/asphalt stabilization) to mitigate these problems. Unfortunately, most existing stabilization techniques cannot be completed in a short (e.g., overnight) construction window because many materials currently used for stabilization cannot be used for overnight stabilization processes. Therefore, research should develop rapid base stabilization and restoration techniques that can be completed within short construction windows. This may require new equipment for rapid stabilization or even new materials. The techniques developed should be able to be incorporated into a one pass pavement removal and replacement operation that uses high-early strength or precast concrete. |
Tasks: |
- Identify existing stabilization materials and techniques.
- Evaluate existing stabilization materials and techniques for their applicability to rapid stabilization (i.e., overnight and one-pass operations).
- Work with contractors and industry representatives to modify or develop new equipment and materials for rapid stabilization.
- Work with contractors and owner-agencies to develop pilot studies that use rapid stabilization techniques and materials.
|
Benefits: |
Rapid subgrade/subbase stabilization that will allow subgrade/subbase support to be repaired and restored before placing new pavement in a short construction window. |
Products: |
New techniques and equipment for rapid subgrade/subbase stabilization. |
Implementation: |
This research will result in new techniques, equipment and/or materials for rapid stabilization. |
Problem Statement EA 4.2. Automated Subdrain Installation in Concrete Pavement Construction
Track: |
5. Equipment Automation and Advancements (EA) |
Subtrack: |
EA 4. Concrete Pavement Foundation Equipment |
Approximate Phasing: |
Years 8–10 |
Estimated Cost: |
$1 M–$2 M |
While certain regions of the United States require pavement subdrains, installing these subdrains is often costly and time-consuming. Research is needed to explore ways to install subdrains quickly and efficiently during the paving operation. Ideally, automated installation equipment would install the subdrains immediately in front of the paving operation, eliminating the need for two separate construction processes and additional construction time. Subdrain installation would thus be a one-pass operation that includes excavation, drain installation, and backfilling. |
Tasks: |
- Identify typical subdrain specifications required by owner-agencies and viable new subdrain specifications.
- Work with contractors and industry representatives to develop automated subdrain installation equipment that could be completed in one pass in front of the paving operation.
- Work with owner-agencies and contractors to develop pilot projects that demonstrate automated subdrain installation.
|
Benefits: |
Automated subdrain installation that permits the process to be completed in a single pass immediately in front of the paver, thus expediting construction. |
Products: |
New techniques and equipment for automated subdrain installation. |
Implementation: |
This work will result in new techniques and/or equipment for rapid automated subdrain installation in concrete pavement construction. |
SUBTRACK EA 5. CONCRETE PAVEMENT RECONSTRUCTION EQUIPMENT
This subtrack focuses on the next generation of equipment that will integrate the removal/ replacement of the slab in one-pass construction. Table 29 provides an overview of this subtrack.
Table 29. Subtrack EA 5 overview.
Problem Statement |
Estimated Cost |
Products |
Benefits |
EA 5.0. Framework for Concrete Pavement Reconstruction Equipment (Subtrack EA 5) |
$200 k |
A validated, sequenced, and detailed research framework for this subtrack. |
An effective, coordinated, and productive research program. |
EA 5.1. High-Speed, In Situ PCC Pavement Breakup, Removal, and Processing |
$2 M–$5 M |
Equipment for high-speed, one-pass, in situ breaking up, removing, and processing PCC pavement. |
Equipment that will permit old concrete pavement to be broken up, removed, and processed in place, allowing the concrete material to be recycled into base material or new concrete and significantly reducing or even eliminating waste material. |
EA 5.2. Recycled Concrete Processing/ Improvement |
$1 M–$2 M |
quipment and recommendations for separating crushed concrete into usable materials. |
Equipment that will separate crushed concrete properly into materials that can be used for new concrete, minimizing or eliminating waste from reconstructed concrete pavements. |
EA 5.3. High-Speed, In Situ, One-Pass, Full Concrete Pavement Reconstruction |
$2 M–$5 M |
New equipment for one-pass pavement reconstruction. |
Equipment that permits one-pass concrete pavement reconstruction, including breaking up, removing, and processing the old pavement, and placing the new pavement using recycled materials from the old pavement; expedited pavement reconstruction with no waste generated. |
Problem Statement EA 5.0. Framework for Concrete Pavement Reconstruction Equipment (Subtrack EA 5)
Track: |
5. Equipment Automation and Advancements (EA) |
Subtrack: |
EA 5. Concrete Pavement Reconstruction Equipment |
Approximate Phasing: |
Years 1–3 |
Estimated Cost: |
$200 k |
Subtrack EA 5 (Concrete Pavement Reconstruction Equipment) provides a set of research problem statements that will culminate in a significantly improved state of the art and practice. As the funding becomes available, an initial effort will be necessary to develop a framework for the research to be accomplished within this subtrack. |
Tasks: |
- Examine the problem statements in subtrack EA 5 (Concrete Pavement Reconstruction Equipment), modify as appropriate, and divide them into specific, manageable contracts.
- Arrange the contracts in a carefully sequenced plan that reflects a logical progress of research and available funding.
- Expand each of the broad research problem statements included in the subtrack into a detailed research plan with specific objectives, tasks, and funding recommendations.
- Review and provide direction for the various research contracts underway to ensure that they fulfill their objectives and allow future contracts to use their results. Guide the additional work required if a contract fails to achieve its objectives and additional work is necessary.
|
Benefits: |
An effective, coordinated, and productive research program. |
Products: |
A validated, sequenced, and detailed research framework for this subtrack. |
Implementation: |
This research will provide the organization and validation essential for the success of this subtrack. Implementation of this problem statement will set the stage for the rest of the problem statements in subtrack EA 5 (Concrete Pavement Reconstruction Equipment). |
Problem Statement EA 5.1. High-Speed, In Situ PCC Pavement Breakup, Removal, and Processing
Track: |
5. Equipment Automation and Advancements (EA) |
Subtrack: |
EA 5. Concrete Pavement Reconstruction Equipment |
Approximate Phasing: |
Years 3–7 |
Estimated Cost: |
$2 M–$5 M |
With the current aging infrastructure, many concrete pavements require complete replacement rather than minor rehabilitation. Unfortunately, many of these pavements are located in urban areas that permit only short construction windows for removing and replacing the pavement. Removing the existing pavement can be the most time-consuming aspect of this process. Research should investigate the high-speed breakup, removal, and processing of the old pavement material. Ideally, a one-pass operation would breakup the pavement, remove it, and crush it into manageably sized material that can then be reused as base material or concrete aggregate. Breaking up and removing old material should not damage the underlying base material or compromise its integrity. Nonimpact methods, such as lasers, should be investigated as possible techniques for breaking up the old concrete. Breakup and processing also should consider concrete pavements with and without asphalt overlays and determine how to separate the two materials. |
Tasks: |
- Identify techniques for breaking up existing concrete pavements with or without asphalt overlays, including such new nonimpact technologies as lasers.
- Identify techniques for removing and processing the material in situ, including techniques for separating asphalt overlay material from PCC material.
- Work with industry representatives and contractors to develop new techniques and equipment for high-speed breaking up, removing, and processing old pavements.
- Work with owner-agencies to develop pilot studies that use new breakup and removal processes.
|
Benefits: |
Equipment that will permit old concrete pavement to be broken up, removed, and processed in place, allowing the concrete material to be recycled into base material or new concrete and significantly reducing or even eliminating waste material. |
Products: |
Equipment for high-speed, one-pass, in situ breaking up, removing, and processing PCC pavement. |
Implementation: |
This work will result in new equipment for high-speed breakup, removal, and processing of concrete pavement with or without asphalt overlays. |
Problem Statement EA 5.2. Recycled Concrete Processing/Improvement
Track: |
5. Equipment Automation and Advancements (EA) |
Subtrack: |
EA 5. Concrete Pavement Reconstruction Equipment |
Approximate Phasing: |
Years 5–9 |
Estimated Cost: |
$1 M–$2 M |
Reconstructing concrete pavements produces large stockpiles of old concrete material that can be reused in some form for new construction. Several studies have examined sophisticated methods to separate concrete into components that can be used as aggregates and cement precursors. One method heats concrete to between 650 and 700 °C (1,202 and 1,292 °F) in an electrical furnace. Another promising technology called Franka-Stein treats concrete in a powerful electric arc using electrodynamic fragmentation, which separates the electrically weak material boundaries prevalent in concrete. In addition to producing clean aggregate, the Franka-Stein process separates cementitious material that can replace natural raw material in cement production. Research is needed to investigate these recycling methods further to determine their cost-effectiveness, considering the energy consumption of the separation process. |
Tasks: |
- Identify existing processes for separating recycled concrete, including Franka-Stein and others.
- Evaluate the effectiveness of the separation processes and the suitability of the resulting material for reuse in new concrete pavement.
- Evaluate the cost versus benefit of different recycling processes, considering the energy consumption of the separation process.
- Work with contractors and industry representatives to develop new equipment or modify and adapt existing equipment for rapid recycling of concrete pavement.
|
Benefits: |
Equipment that will separate crushed concrete properly into materials that can be used for new concrete, minimizing or eliminating waste from reconstructed concrete pavements. |
Products: |
Equipment and recommendations for separating crushed concrete into usable materials. |
Implementation: |
This work will result in equipment for recycling and processing concrete pavement and recommendations for using recycled materials in new concrete. |
Problem Statement EA 5.3. High-Speed, In Situ, One-Pass, Full Concrete Pavement Reconstruction
Track: |
5. Equipment Automation and Advancements (EA) |
Subtrack: |
EA 5. Concrete Pavement Reconstruction Equipment |
Approximate Phasing: |
Years 8–10 |
Estimated Cost: |
$2 M–$5 M |
The traveling public expects and demands fewer delays, often making user costs the highest expense for a major reconstruction project. For major reconstruction efforts, traffic control barrels are positioned to alter traffic flow around the work site for weeks or months, straining public travel through the area. Therefore, agencies often delay necessary highway reconstruction or choose less disruptive repairs to avoid traffic interruptions. These decisions eventually strain the State’s pavement network, since the majority of the network has a short expected life. In addition, material is removed and hauled offsite during reconstruction—this is a labor-intensive process that often increases the cost and extends the length of reconstruction projects. However, improved equipment capable of removing, recycling, mixing and placing concrete pavement using a single, continuous operation would ease reconstruction.
The process would require a marriage of mobile crushing and screening with a mixer and slipform paver. This research will conceptualize and build efficient and effective methods and/or processes that will permit recycling, mixing, and placing of existing concrete pavement using a single continuous operation. A recent initiative in Europe advanced the linear quarry, in which materials generated by the reclamation of the existing pavement structure would be reprocessed into the new structure along the same alignment. While this concept has been limited to HMA pavements, this research will explore the same concept for concrete pavements. The feasibility of crushing, collecting, sizing, batching, and placing concrete pavements within the right of way should be studied. If the feasibility study returns positive results, additional provisions should be made to test this concept in the field. |
Tasks: |
- Identify existing linear quarry technology for in situ material processing and recycling.
- Identify existing equipment for in situ PCC materials removal and processing.
- Determine the viability of using reprocessed concrete materials for new pavement.
- Complete a feasibility study that incorporates breaking up, removing, crushing, sizing, batching, and placing new concrete in a single operation within the right-of-way.
- Conceptualize and develop high-speed one-pass, in situ reconstruction equipment.
|
Benefits: |
Equipment that permits one-pass concrete pavement reconstruction, including breaking up, removing, and processing the old pavement, and placing the new pavement using recycled materials from the old pavement; expedited pavement reconstruction with no waste generated. |
Products: |
New equipment for one-pass concrete pavement reconstruction. |
Implementation: |
This work will assess the feasibility of high-speed, one-pass, in situ reconstruction equipment, and possibly develop such equipment. |
SUBTRACK EA 6. CONCRETE PAVEMENT RESTORATION EQUIPMENT
This subtrack focuses on the repair processes, aiming to speed the operations and provide the workforce and traveling public with less exposure to the process. Table 30 provides an overview of this subtrack.
Table 30. Subtrack EA 6 overview.
Problem Statement |
Estimated Cost |
Products |
Benefits |
EA 6.0. Framework for Concrete Pavement Restoration Equipment (Subtrack EA 6) |
$150 k |
A validated, sequenced, and detailed research framework for this subtrack. |
An effective, coordinated, and productive research program. |
EA 6.1. Rapid, High- Production Concrete Pavement Grinding |
$1 M–$2 M |
More efficient, high-production grinding equipment. |
High-production grinding equipment that will permit faster, more efficient concrete pavement grinding, reducing construction time and ground surface variability by grinding a wider section of pavement with a single pass. |
EA 6.2. Automated Concrete Pavement Crack Sensing and Sealing |
$500 k–$1 M |
Automated crack sensing and crack sealing equipment/vehicle. |
Automated concrete pavement crack sensing and crack sealing equipment that requires less labor, minimal traffic control, and provides a safer working environment for crack sealing. |
EA 6.3. Fully Automated Concrete Pavement Restoration Equipment |
$1 M–$2 M |
Fully automated one-pass DBRs and patching equipment. |
Fully automated DBR and patching equipment that will expedite these CPR processes, requiring less labor and lowering costs. |
|
|
|
|
Problem Statement EA 6.0. Framework for Concrete Pavement Restoration Equipment (Subtrack EA 6)
Track: |
5. Equipment Automation and Advancements (EA) |
Subtrack: |
EA 6. Concrete Pavement Restoration Equipment |
Approximate Phasing: |
Years 1–3 |
Estimated Cost: |
$150 k |
Subtrack EA 6 (Concrete Pavement Restoration Equipment) provides a set of research problem statements that will culminate in a significantly improved state of the art and practice. As the funding becomes available, an initial effort will be necessary to develop a framework for the research to be accomplished within this subtrack. |
Tasks: |
- Examine the problem statements in subtrack EA 6 (Concrete Pavement Restoration Equipment), modify as appropriate, and divide them into specific, manageable contracts.
- Arrange the contracts in a carefully sequenced plan that reflects a logical progress of research and available funding.
- Expand each of the broad research problem statements included in the subtrack into a detailed research plan with specific objectives, tasks, and funding recommendations.
- Review and provide direction for the various research contracts underway to ensure that they fulfill their objectives and allow future contracts to use their results. Guide the additional work required if a contract does not achieve its objectives and additional work is necessary.
|
Benefits: |
An effective, coordinated, and productive research program. |
Products: |
A validated, sequenced, and detailed research framework for this subtrack. |
Implementation: |
This research will provide the organization and validation essential for the success of this subtrack. Implementation of this problem statement will set the stage for the rest of the problem statements in subtrack EA 6 (Concrete Pavement Restoration Equipment). |
Problem Statement EA 6.1. Rapid, High-Production Concrete Pavement Grinding
Track: |
5. Equipment Automation and Advancements (EA) |
Subtrack: |
EA 6. Concrete Pavement Restoration Equipment |
Approximate Phasing: |
Years 3–7 |
Estimated Cost: |
$1 M–$2 M |
Diamond grinding technology has reached the point where meeting the most stringent ride quality specifications is not difficult for an experienced operator. Unfortunately, the process is still very slow, and each pass generally is limited to a 0.91- to 1.2-m (3- to 4-ft) width. Because CPR programs increasingly demand concrete pavement grinding, research is needed to develop high-production diamond grinding equipment and techniques. A new generation of grinding equipment that quickly grinds full 3.7-m (12-ft) lane widths or more in a single pass will meet the demands of CPR programs. New grinding equipment should incorporate slurry extraction and retention. If diamond grinding equipment cannot meet the new CPR requirements, alternative grinding equipment should also be investigated. |
Tasks: |
- Identify the grinding production needs of contractors and owner-agencies.
- Identify limitations on existing diamond grinding equipment.
- Identify alternative grinding equipment and determine its suitability for concrete paving applications.
- Work with industry representatives and contractors to modify existing equipment or develop new equipment to meet grinding production needs.
|
Benefits: |
High-production grinding equipment that will permit faster, more efficient concrete pavement grinding, reducing construction time and ground surface variability by grinding a wider section of pavement with a single pass. |
Products: |
High-production grinding equipment that will permit faster, more efficient concrete pavement grinding, reducing construction time and ground surface variability by grinding a wider section of pavement with a single pass. |
Implementation: |
This work will result in equipment for high-production concrete pavement grinding. |
Problem Statement EA 6.2. Automated Concrete Pavement Crack Sensing and Sealing
Track: |
5. Equipment Automation and Advancements (EA) |
Subtrack: |
EA 6. Concrete Pavement Restoration Equipment |
Approximate Phasing: |
Years 4–8 |
Estimated Cost: |
$500 k–$1 M |
Crack sealing is necessary maintenance that prevents water and debris from intruding into PCC pavement cracks. Water and debris intrusion can result in corrosion of the reinforcement and spalling at the cracks. However, crack sealing is time-consuming and labor-intensive. Research is needed to investigate the viability of automated crack sensing and crack sealing equipment. Automated processes would not only eliminate much of the manual labor involved, but also would create a safer working environment, possibly eliminating the need for traffic control during sealing operations. Automated crack sensing equipment could be vehicle-mounted and could use visual imaging, laser scanning, or other techniques to detect cracks. After crack detection, vehicle-mounted sealing equipment could then seal the crack with epoxy, asphalt, or other material. Although automated sealing would be impossible at high speeds, vehicle-mounted equipment would only require a moving traffic control setup. |
Tasks: |
- Identify existing equipment or develop new automated concrete pavement crack sensing equipment.
- Identify existing equipment or develop new automated crack sealing equipment.
- Develop equipment for integrating crack sensing and crack sealing into a single operation.
|
Benefits: |
Automated concrete pavement crack sensing and crack sealing equipment that requires less labor, minimal traffic control, and provides a safer working environment for crack sealing. |
Products: |
Automated crack sensing and crack sealing equipment/vehicle. |
Implementation: |
This work will result in automated concrete pavement crack sensing and crack sealing equipment. |
Problem Statement EA 6.3. Fully Automated Concrete Pavement Restoration Equipment
Track: |
5. Equipment Automation and Advancements (EA) |
Subtrack: |
EA 6. Concrete Pavement Restoration Equipment |
Approximate Phasing: |
Years 6–10 |
Estimated Cost: |
$1 M–$2 M |
DBR have become a well-established and proven technique for restoring load transfer across concrete pavement cracks and joints. Full- and partial-depth patching techniques commonly repair failed slab segments and spalling, respectively. However, these techniques are still labor-intensive and timeconsuming. This research will conceptualize and develop fully automated equipment for both DBR and slab patching. The equipment should complete these CPR techniques in a one-pass process. For DBR, this will include cutting and cleaning slots across a crack or joint, inserting the dowel bars, and patching the slots. If possible, the process will also incorporate diamond grinding. Patching will include sawing and removing the existing concrete, inserting tie/dowel bars as necessary, and placing, consolidating, and curing patching material. In all cases, the equipment should adequately retrofit an entire lane width in a single pass. |
Tasks: |
- Determine the equipment feasibility for one-pass DBR and/or patching operations. Examine alternative patching materials and the feasibility of incorporating diamond grinding into the operation.
- Determine the production requirements (speed of operation) for these CPR operations.
- Conceptualize and develop one-pass CPR equipment.
|
Benefits: |
Fully automated DBR and patching equipment that will expedite these CPR processes, requiring less labor and lowering costs. |
Products: |
Fully automated one-pass DBR and patching equipment. |
Implementation: |
This work will result in fully automated DBR and concrete slab patching equipment. |
SUBTRACK EA 7. ADVANCED EQUIPMENT EVALUATION AND IMPLEMENTATION
This subtrack provides the resources for evaluating the new equipment on actual construction projects. Table 31 provides an overview of this subtrack.
Table 31. Subtrack EA 7 overview.
Problem Statement |
Estimated Cost |
Products |
Benefits |
EA 7.0. Framework for Advanced Equipment Evaluation and Implementation (Subtrack EA 7) |
$150 k |
A validated, sequenced, and detailed research framework for this subtrack. |
An effective, coordinated, and productive research program. |
EA 7.1. Advanced Concrete Paving Equipment Workshops and Demonstrations |
$2 M–$5 M |
Workshops and product demonstrations for advanced PCC construction/ rehabilitation equipment. |
Workshops and product demonstrations that provide a cost effective opportunity for familiarizing contractors and owneragencies with new equipment and technologies and training employees. |
EA 7.2. Concrete Paving Equipment Purchases for States |
$2 M–$5 M |
Vehicle for helping States purchase advanced pavement construction/ rehabilitation equipment. |
Advanced equipment for concrete pavement construction and rehabilitation that States can afford. |
Problem Statement EA 7.0. Framework for Advanced Equipment Evaluation and Implementation (Subtrack EA 7)
Track: |
5. Equipment Automation and Advancements (EA) |
Subtrack: |
EA 7. Advanced Equipment Evaluation and Implementation |
Approximate Phasing: |
Years 1–3 |
Estimated Cost: |
$150 k |
Subtrack EA 7 (Advanced Equipment Evaluation and Implementation) provides a set of research problem statements that will culminate in a significantly improved state of the art and practice. As the funding becomes available, an initial effort will be necessary to develop a framework for the research to be accomplished within this subtrack. |
Tasks: |
- Examine the problem statements in subtrack EA 7 (Advanced Equipment Evaluation and Implementation), modify as appropriate, and divide them into specific, manageable contracts.
- Arrange the contracts in a carefully sequenced plan that reflects a logical progress of research and available funding.
- Expand each of the broad research problem statements included in the subtrack into a detailed research plan with specific objectives, tasks, and funding recommendations.
- Review and provide direction for the various research contracts underway to ensure that they fulfill their objectives and allow future contracts to use their results. Guide the additional work required if a contract does not achieve its objectives and additional work is necessary.
|
Benefits: |
An effective, coordinated, and productive research program. |
Products: |
A validated, sequenced, and detailed research framework for this subtrack. |
Implementation: |
This research will provide the organization and validation essential for the success of this subtrack. Implementation of this problem statement will set the stage for the rest of the problem statements in subtrack EA 7 (Advanced Equipment Evaluation and Implementation). |
Problem Statement EA 7.1. Advanced Concrete Paving Equipment Workshops and Demonstrations
Track: |
5. Equipment Automation and Advancements (EA) |
Subtrack: |
EA 7. Advanced Equipment Evaluation and Implementation |
Approximate Phasing: |
Years 3–10 |
Estimated Cost: |
$2 M–$5 M |
As with many new technologies, transportation agencies often are slow to adopt new techniques and equipment because they are unfamiliar with these new technologies and lack research resources. Workshops and product demonstrations offer an ideal environment for familiarizing agencies with new and advanced equipment and technologies. These workshops and product demonstrations will train both contractors and owner-agencies in the new equipment through hands-on workshops and demonstrations. If a particular product generates enough interest, product demonstrations may even be taken to States. |
Tasks: |
- Compile information on advanced concrete paving equipment and coordinate workshops and product demonstrations.
- Present and demonstrate advanced equipment to workshop audiences, emphasizing the need for and benefits of such equipment.
|
Benefits: |
Workshops and product demonstrations that provide a cost effective opportunity for familiarizing contractors and owner-agencies with new equipment and technologies and training employees. |
Products: |
Workshops and product demonstrations for advanced PCC construction/rehabilitation equipment. |
Implementation: |
This research will develop numerous workshops and product demonstrations for advanced concrete paving equipment at various venues throughout the United States. |
Problem Statement EA 7.2. Concrete Paving Equipment Purchases for States
Track: |
5. Equipment Automation and Advancements (EA) |
Subtrack: |
EA 7. Advanced Equipment Evaluation and Implementation |
Approximate Phasing: |
Years 5–10 |
Estimated Cost: |
$2 M–$5 M |
Most States lack the funding necessary to purchase their own new advanced equipment. Moreover, many contractors are reluctant to invest large amounts of capital in new equipment unless it is certain to be profitable. Guidelines should be established that help States purchase needed equipment and promote the use of such equipment for PCC pavement construction and rehabilitation. |
Tasks: |
- Establish guidelines for helping States purchase advanced equipment for PCC pavement construction and rehabilitation.
- Recommend a process for identifying, prioritizing, and obtaining needed equipment.
|
Benefits: |
Advanced equipment for concrete pavement construction and rehabilitation that States can afford. |
Products: |
Vehicle for helping States purchase advanced pavement construction/rehabilitation equipment. |
Implementation: |
This work will result in a vehicle for helping States purchase advanced equipment for PCC pavement construction and rehabilitation. |