Prefabricated Bridges Brochure
"Get in, get out, stay out."
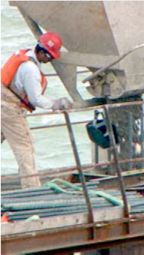
The American Association of State Highway Transportation Officials (AASHTO) Technology Implementation Group (TIG) was formed in December 2000 to facilitate rapid acceptance and implementation of high payoff and innovative technologies, and it has selected prefabricated bridge elements and systems as one of its technologies to champion for rapid implementation.
The following pages celebrate the emergence and growth of innovative prefabricated bridge technology and its implementation by forward-looking bridge owners, engineers, and builders. Prefabricated bridge elements and systems improve bridges and bridge building by affording the following advantages:
- Prefabricated elements and systems make bridge building less disruptive to the traveling public.
- Prefabricated elements and systems make bridges safer to build.
- Prefabricated elements and systems make bridge building less disruptive to the environment.
- Prefabricated elements and systems make bridge designs more constructible.
The innovative bridge projects featured in these pages solved site-specific challenges using the following prefabricated elements and systems:
- Bent caps, deck panels, stay-in-place deck forms, piling, deck planks, beams of various types, segmental match-cast pier units, concrete and steel composite superstructure units, box pier units, cylinder pile support columns, ramp sections, stair sections, crash walls, and truss spans.
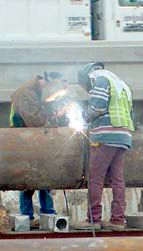
The bridges and their project contacts are as follows:
- I-95/James River Bridge-Virginia Department of Transportation: Dina N. Kukreja, P.E.; Dina.Kukreja@VirginiaDOT.org; (804) 786-5172.
- Route 7 over Route 50-Virginia Department of Transportation: Nicholas J. Roper, P.E.; Nicholas.Roper@VirginiaDOT.org; (703) 383-2117.
- George P. Coleman Bridge-Virginia Department of Transportation: George Clendenin, P.E.; George.Clendenin@VirginiaDOT.org; (804) 786-4575.
- Route 7 over Wolf River Bridge-Tennessee Department of Transportation: Edward P. Wasserman, P.E.; Ed.Wasserman@state.tn.us; (615) 741-3351.
- Keaiwa Stream Bridge-State of Hawaii Department of Transportation: Paul Santo, P.E.; paul_santo@exec.state.hi.us; (808) 692-7611.
- Cross Westchester Expressway Viaducts-New York State Department of Transportation: George A. Christian, P.E.; Gchristian@gw.dot.state.ny.us; (518) 485-7257.
- Main Street over Metro North Railroad-New York State Department of Transportation: George A. Christian, P.E.; Gchristian@gw.dot.state.ny.us; (518) 485-7257.
- Route 9/Metro North Pedestrian Bridge-New York State Department of Transportation: George A. Christian, P.E.; Gchristian@gw.dot.state.ny.us; (518) 485-7257.
- I-5/South 38th Street Interchange-Washington State Department of Transportation: Joseph Merth, P.E.; merthjo@wsdot.wa.gov; (360) 705-7166.
- Highway 47 over Seelye Brook-Minnesota Department of Transportation: Paul Kivisto, P.E.; paul.kivisto@dot.state.mn.us; (651) 747-2130.
- I-45/Pierce Elevated-Texas Department of Transportation: Kenneth L. Ozuna, P.E.; kozuna@dot.state.tx.us; (713) 802-5435.
- SH 66/Lake Ray Hubbard Bridge-Texas Department of Transportation: Lloyd M. Wolf, P.E.; lwolf@dot.state.tx.us; (512) 416-2279.
- Wesley Street Bridge-Texas Department of Transportation: Steven Hall, P.E.; shall3@dot.state.tx.us; (903) 586-9878.
- I-65/I-59 Interchange-Alabama Department of Transportation: Fred Conway, P.E.; conwayf@dot.state.al.us; (334) 242-6007.
- I-95/Chester Street Bridge-Pennsylvania Department of Transportation: R. Scott Christie, P.E.; schrist@dot.state.pa.us; (717) 787-2881.
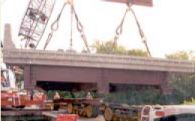
I-95/James River Bridge, Virginia
Minimal impact on motorists was a project goal for replacement of the superstructure of the I-95/James River Bridge, which carries approximately 110,000 vehicles per day through the city of Richmond. After considering alternatives, the Virginia Department of Transportation opted for night-only construction, most of which occurred between 7 PM and 6 AM Sunday through Thursday nights. During nighttime construction, one lane of traffic was kept open in each direction. For most spans, bridge preconstructed composite units (PCU's), which include an 8-¾-inch deck over steel plate girders, were precast at a nearby casting yard and then transported to the work site. Work crews cut out the old bridge span and removed it, prepared the gap for the new PCU, and set the new PCU in place.
|
Route 7 over Route 50, Virginia
Replacement of the Route 7 over Route 50 bridges in Fairfax County required Virginia DOT to replace approximately 14,000 square feet of deteriorating bridge deck. Virginia DOT opted to use precast deck panels to satisfy community concerns about reductions in the level of service. Operating only at night, crews saw-cut sections of the existing deck, lifted and removed them by crane, and immediately installed new deck panels that matched the deck cavity. They then placed a rapid-setting concrete overlay that supported full traffic after only three hours of curing. The bridge was completely open to traffic during the day.
|
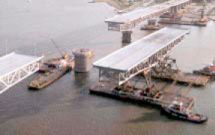
George P. Coleman Bridge, Virginia
In 1995, the largest double-swing bridge in the United States was dismantled and replaced in record time. A major goal was limiting bridge closure to avoid disrupting traffic of more than 27,000 vehicles a day. Lighter-weight modern materials allowed Virginia DOT designers to widen the new bridge but use the existing foundation. While approach spans were widened, truss spans were prefabricated nearby and then barged to the construction site. Six old spans were removed and six new ones placed in only nine days.
|
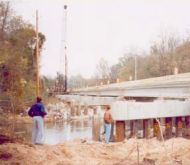
Route 57 over Wolf River Bridge, Tennessee
The Wolf River Bridge in Fayette County, Tennessee, crosses sensitive wetlands and carries the only east-west route through its geographic region. For the 20-span replacement bridge, the Tennessee Department of Transportation chose staged construction, maintaining one lane of traffic with timed signals. TDOT designers selected precast prestressed beams to facilitate speedy construction and allowed optional stay-in-place precast prestressed concrete deck forms. TDOT and the contractor developed details for precasting bent caps in two pieces to suit staged construction. Construction of the 1,408-foot long, 46-foot wide bridge was completed in 11 months without putting any equipment in the surrounding wetlands.
|
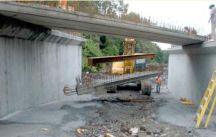
Keaiwa Stream Bridge, Hawaii
A record rainstorm in late 2000 caused major damage to the only route on the southeast side of the Big Island of Hawaii. The State of Hawaii Department of Transportation chose to replace the 80-foot Route 11 bridge near Pahala with a longer structure to prevent future damage from flooding. The new 7-span, 230- foot concrete bridge, using precast prestressed concrete planks on wall piers, with cast-in-place concrete topping, was in operation within seven months.
|
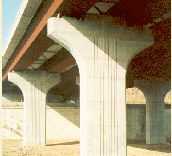
Cross Westchester Expressway Viaducts, New York
Required to maintain six lanes of congested traffic and limit construction on a restricted site during replacement of two major I-287 viaducts in Westchester County, the New York State Department of Transportation accepted the contractor's value-engineering proposal to incorporate precast segmental voided pier sections for each of the 42 piers, which consisted of 8-foot match-cast segments vertically post-tensioned together and to the footings. It also changed the cast-inplace deck to 10-foot-long by 9-inch-thick precast panels, 42 to 50 feet wide to match longitudinal construction stages, supported on pairs of multi-span continuous steel tub girders.
|
Main Street over Metro North Railroad, New York
Replacement of a through girder bridge over a busy commuter railroad in the village of Tuckahoe presented challenges for NYSDOT: maintaining 2-way traffic, conducting all work between 2 and 4 AM on weekends to limit disruptions for rail commuters and adjacent stores, maintaining utility lines while relocating them on the new bridge, and raising the railroad vertical clearance five inches without materially affecting the street profile. NYSDOT chose a proprietary system of precast prestressed concrete/steel composite superstructure modules that allowed for smaller beams than conventional construction, which helped attain the increased vertical clearance and had a short installation time.
|
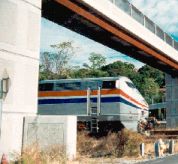
Route 9/Metro North Pedestrian Bridge, New York
Building a pedestrian bridge in the village of Croton-on-the- Hudson involved site restrictions, a requirement for aesthetic design, and the need to limit disruption on a heavily traveled highway and a major commuter railroad. NYSDOT chose two proprietary prefabricated composite superstructure spans with concrete parapets to bridge the 4-lane highway, service road, and five sets of railroad tracks. Twelve inch diameter precast piles support 3-section piers made of precast boxes stacked vertically and post-tensioned to a cast-in-place concrete footing, with precast parapets and a cast-in-place deck. Ramps are 35-foot-long precast concrete units and 20-foot precast stair sections, supported directly on precast columns with cast-in-place seats. Precast concrete's many available architectural treatments enabled meeting project aesthetic goals.
|
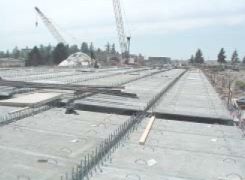
I-5/South 38th Street Interchange, Washington
To reduce construction time and minimize traffic disruption, the Washington State Department of Transportation chose precast stayin- place deck panels in the design of this 2-span, 325-foot replacement bridge over I-5 in Tacoma. The new post-tensioned box girder bridge uses precast tub girder segments. With no need to construct and remove conventional deck forms, lane closures on I-5 were greatly reduced. Leveling screws were used to adjust camber on the 3-½-inch thick precast pretensioned panels, and all 766 panels were placed within a week of limited nighttime I-5 lane closures.
|
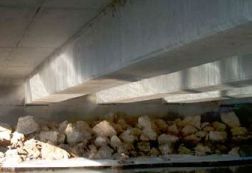
Highway 47 over Seelye Brook, Minnesota
This bridge replacement project required a shallow structure that was durable, economical, and quick to construct because no detour route was available. The Minnesota Department of Transportation opted for a low depth, rectangular precast beam system because the cast-in-place deck option would have required falsework below the structure that would have been susceptible to flood waters. The bridge has a 51-foot beam span, and the 9-inch deck is supported by the solid rectangular prestressed beams. Because the beams were shallower than the deeper I-shaped sections, they also eliminated the need to raise the existing profile grade and satisfied hydraulic and right of- way constraints for the project.
|
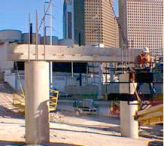
I-45/Pierce Elevated, Texas
When two 113- span sections of I-45 in Houston's central business district needed replacing, Texas Department of Transportation designers opted to speed construction by using precast bent caps on the existing columns. The bridge consists of twin structures, one northbound and one southbound, and each structure was completed in 95 days, a total of 226 spans replaced in 190 days. To connect the precast caps to the existing columns, the precast caps were anchored with post-tensioning bars and hardware.
|
SH 66/Lake Ray Hubbard, Texas
After 40 years of service, the narrow crossing of SH 66 over Lake Ray Hubbard was congested with commuters from suburbs east of Dallas. A replacement project to construct a pair of conventional prestressed concrete I-beam bridges changed after letting when the contractor asked to precast the substructure bent caps to eliminate the need for a barge crane, reducing time workers needed to operate near power lines. TxDOT designed a precast bent cap option with a cap-to-column connection and a construction procedure allowing early placement of caps and prestressed beams based on achieved cap concrete and cap grout connection strength. Using 43 precast bent caps saved nearly a week per cap on tasks associated with formwork, reinforcement, casting, curing, and inspection.
|
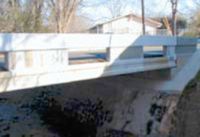
Wesley Street Bridge, Texas
One of only two routes into or out of a populated housing community, Wesley Street crosses Ragsdale Creek in Jacksonville, Texas. When the bridge required replacement, TxDOT opted for accelerated construction using precast prestressed slab beams. Work on the project began in October 2001 and was completed in January 2002.
|
I-65/I-59 Interchange, Alabama
When a fuel truck collision damaged a Birmingham bridge in the I-65/I-59 interchange in January 2002, the Alabama Department of Transportation opted for a wider replacement bridge with a longer span over the northbound lanes of I-65, the main north-south route through Alabama. The interchange carries an estimated 100,000 vehicles per day, and the bridge needed to be replaced quickly. For the 140-foot main span and the 75-foot approaches, the contractor proposed a value engineering girder re-design using bulb tee beams with a 14-day strength of 8,000 psi. Traffic was stopped for only 12 nighttime hours to set the 15 girders on the 140-foot span overhead. Construction was completed in just 37 days.
|
I-95/Chester Creek Bridge, Pennsylvania
On Memorial Day weekend in 1998, a fuel truck caught fire, closing this 358-foot long, 3-span continuous bridge. Severe sagging required the Pennsylvania Department of Transportation to replace approximately two-thirds of the superstructure. Shop drawings of the original girders were available, facilitating immediate material order and fabrication. New girders were delivered within two weeks of the fire, and the bridge was open by July 4th.
|
American Association of State Highway and Transportation Officials
AASHTO Technology Implementation Group (TIG)
Chair: Gary L. Hoffman, Pennsylvania Department of Transportation
Members:
- Ari Adler, Michigan Department of Transportation
- Charlie Churilla, Federal Highway Administration
- Joe Deneault, West Virginia Department of Transportation
- Dave Ekern, Minnesota Department of Transportation
- Tony Giancola, National Association of County Engineers
- Neil Hawks, Transportation Research Board
- Randy Iwasaki, California Department of Transportation
- Paul Krugler, Texas Department of Transportation
- Byron Lord, Federal Highway Administration
- John McCracken, Federal Highway Administration
- Gene Fong, Federal Highway Administration
- Doug Rose, Maryland Department of Transportation
- Len Sanderson, North Carolina Department of Transportation
- Warren Sick, Kansas Department of Transportation
- Haleem Tahir, American Association of State Highway and Transportation Officials
- Gary Taylor, Michigan Department of Transportation
- Paul Wells, New York State Department of Transportation
AASHTO TIG Implementation Panel for Prefabricated Bridge Elements and Systems
Chair: Mary Lou Ralls, Texas Department of Transportation
Members:
- John S. Dick, Precast/Prestressed Concrete Institute
- Daniel Dorgan, Minnesota Department of Transportation
- Hala Elgaaly, Federal Highway Administration
- David Graham, Georgia Department of Transportation
- Malcolm T. Kerley, Virginia Department of Transportation
- Richard Land, California Department of Transportation
- John Marcelle, Fort Miller Co., Inc.
- Ronald D. Medlock, Texas Department of Transportation
- James M. O'Connell, New York State Department of Transportation
- Arun Shirole, National Steel Bridge Alliance
- M. William Spence, Tidewater Skanska
Photo Credits
- front cover Texas DOT: SH 66/Lake Ray Hubbard
- page 2 Texas DOT: SH 66/Lake Ray Hubbard
- page 3 Texas DOT: SH 66/Lake Ray Hubbard
- page 4 Virginia DOT: I-95/James River Bridge
- page 5 Virginia DOT: George P. Coleman Bridge
- page 6 Tennessee DOT: Route 57 over Wolf River Bridge
- page 7 State of Hawaii DOT: Keaiwa Stream Bridge
- page 8 New York State DOT: Cross Westchester Expressway Viaducts
- page 9 New York State DOT: Route 9/Metro North Pedestrian Bridge
- page 10 Washington State DOT: I-5/South 38th Street Interchange
- page 11 Minnesota DOT: Highway 47 over Seelye Brook
- page 12 Texas DOT: I-45/Pierce Elevated
- page 13 Texas DOT: Wesley Street Bridge
- back cover Virginia DOT: I-95/James River Bridge
May 2002
AASHTO Technology Implementation Group (TIG)
http://www.aashtotig.org/
For more information, contact Haleem Tahir, (301) 975-5275, haleem.tahir@nist.gov
American Association of State Highway and Transportation Officials
444 North Capitol Street NW, Suite 249
Washington, DC 20001
(202) 624-5800
http://www.transportation.org/
Copyright © 2002 American Association of State Highway and Transportation Officials. All Rights Reserved.