Asphalt Binder Cracking Device to reduce Low Temperature Asphalt Pavement Cracking
TASK 4. RUGGEDNESS TEST
The purpose of the ruggedness test is to identify sources of variation in ABCD testing. ABCD units and asphalt binder samples were delivered to North Central Superpave Center (NC) and University of Wisconsin, Madison (WI) asphalt laboratories. Sang–Soo Kim of EZ Asphalt provided one day on–site training at each laboratory to the equipment operators (August 25–27, 2008). The ruggedness test was designed following ASTM C 1067 – 00 "Standard Practice for Conducting A Ruggedness or Screening Program for Test Methods for Construction Materials". Of seven factors considered, the effect of lubrication was dropped from the test since conducting the ABCD test without lubrication might seriously damage ABCD rings during cleaning.
4A. Seven factors being studied in Ruggedness Test
-
Cooling Rate (18C/hr versus 22C/hr)
Temperature profiles to be used is
18°C/hr 22°C/hr 20°C to 0°C in 0.5 hour (30 minutes)
0°C to –63°C in 3.5 hours (3 hour 30 minutes)
–63 to 25°C in 0.5 hour (30 minutes)
Hold at 25°C for 1.0 hour20°C to 0°C in 0.5 hour (30 minutes)
0°C to –66°C in 3.0 hours
–66 to 25°C in 0.5 hour (30 minutes)
Hold at 25°C for 1.0 hour -
Size of Protrusion (5.85mm diameter vs. 6.35mm diameter [0.23" versus 0.25"])
The two larger protrusion molds also have a hole at the opposite side.
-
Sample Trimming (0.8mm over trimming versus even trimming)
For over trimming, 0.8 mm depression (about 5 cm long) is created at the surface of two silicone molds. Carefully trim the asphalt binder so that the trimmed surface is flush with the mold surface.
-
Lubrication (No Lubrication versus Lubrication)Two molds and 2 ABCD rings are lubricated with glycerin–talc mixture.The other 2 molds and rings are kept clean and dry without lubrication. -
No Turntable versus Turntable
For 'no turntable test', carefully conduct pouring, trimming, testing and other handling without the use of turntable. For turntable test, place the molds on the turntable and then perform pouring, trimming, testing and other handling.
-
No cold joint versus cold joint
To create cold joints in ABCD sample, fill the mold ½ full with the heated asphalt binder. Place the half filled mold in 0°C chamber for 5 minutes and place the binder container back in the 170° oven for 5 minutes. After 5 minutes, completely fill the mold with the heated asphalt binder.
-
Conditioning time before starting test (0 minute vs. 30 minutes)
All 4 samples are placed in 0°C chamber at the same time. For 30 minute conditioning time, remove two samples after 20 minutes from the 0°C chamber. Trim the sample and then place them in the room temperature for 30 minutes. The other two samples are removed after 50 minutes at the 0°C chamber. Trim them and then start the test immediately.
Each lab was instructed to follow test procedure given below.
The laboratories used the following mold identification numbers:
Mold #1: Smaller diameter (0.23") protrusion and no depression on the surface.
Mold #2: Smaller diameter (0.23") protrusion and 0.8mm depression on the surface.
Mold #3: Larger diameter (0.25") protrusion and no depression on the surface.
Mold #4: Larger diameter (0.25") protrusion and 0.8mm depression on the surface.
For Each Binder
Mold #1 | Mold #2 | Mold #3 | Mold #4 | |
---|---|---|---|---|
Cooling Rate | 18°C/hr | 18°C/hr | 18°C/hr | 18°C/hr |
Turn Table | None | Turn Table | None | Turn Table |
Cold Joint | None | Cold Joint | Cold Joint | None |
Conditioning Time | 30 minutes | 0 minute | 0 minute | 30 minutes |
Data #1 | Data #2 | Data #3 | Data #4 |
Mold #1 | Mold #2 | Mold #3 | Mold #4 | |
---|---|---|---|---|
Cooling Rate | 22°C/hr | 22°C/hr | 22°C/hr | 22°C/hr |
Turn Table | Turn Table | None | Turn Table | None |
Cold Joint | None | Cold Joint | Cold Joint | None |
Conditioning Time | 0 minutes | 30 minute | 30 minute | 0 minutes |
Data #5 | Data #6 | Data #7 | Data #8 |
Repeat Run #1 and Run #2
Mold #1 | Mold #2 | Mold #3 | Mold #4 | |
---|---|---|---|---|
Cooling Rate | 18°C/hr | 18°C/hr | 18°C/hr | 18°C/hr |
Turn Table | None | Turn Table | None | Turn Table |
Cold Joint | None | Cold Joint | Cold Joint | None |
Conditioning Time | 30 minutes | 0 minute | 0 minute | 30 minutes |
Data #9 | Data #10 | Data #11 | Data #12 |
Mold #1 | Mold #2 | Mold #3 | Mold #4 | |
---|---|---|---|---|
Cooling Rate | 22°C/hr | 22°C/hr | 22°C/hr | 22°C/hr |
Turn Table | Turn Table | None | Turn Table | None |
Cold Joint | None | Cold Joint | Cold Joint | None |
Conditioning Time | 0 minutes | 30 minute | 30 minute | 0 minutes |
Data #13 | Data #14 | Data #15 | Data #16 |
'No Lubrication' was dropped due to the possibility of damaging ABCD rings.
The four binders used in the study are as follows:
EZ 1 | EZ 2 | EZ 3 | EZ 4 |
---|---|---|---|
PG 64–16 (AAM–1) | PG 70–22M (SBS) | PG 58–28 (AAA–1) | PG 64–34M (SBS) |
All binders were RTFO aged followed by PAV aging and degassing prior to sending them to the participating laboratories. The specimen cooling rate is determined by the slope of the best fit line of ten data points (about 0.56°C change during 100 seconds) prior to cracking. The average and the standard deviation of the specimen cooling rate of test specimens for each lab are as follows:
Laboratory | WI | NC | EZ | |||
---|---|---|---|---|---|---|
Cooling Rate | Low | High | Low | High | Low | High |
Average, C/hr | –18.6 |
–22.8 |
–18.7 |
–22.9 |
–18.8 |
–23.2 |
st. dev., C/hr | 0.25 |
0.55 |
0.32 |
0.38 |
0.30 |
0.93 |
When the slope of a longer time period is used, the specimen cooling rate approaches the intended rates
(18 and 22°C/hr).
4B. Ruggedness Test Results
4B.1. ABCD Cracking Temperature
On November 15, 2008, the last set of ruggedness test results were received. Following ASTM C 1067, ABCD cracking temperature data (Table 13) were analyzed and summarized in Table 14. Following the ASTM ruggedness analysis procedure, any factors with F Statistics greater than 5.59 are considered to have significant effects on ABCD cracking temperature with 5% significance level. Standard deviation is the Root–Mean–Square–Error (RMSE). When reviewed for each combination of four asphalt binder types and three laboratories, there are 12 cases as shown in Table 14. The size of protrusion and the over–trimming were the factors affecting test results most significantly (four significant cases each). Formation of a cold joint during sample preparation had two significant cases. Cooling rate and conditioning time had one significant case each.
The required ASTM ruggedness analyses presented in the previous paragraph addressed the significant variables at a given laboratory and for a given asphalt binder. The required analyses do not directly compare the laboratories statistically. Therefore, in addition to the required analyses, EZ Asphalt investigated the overall statistical differences using Analysis of Variance (ANOVA) with the results shown in Table 15. As expected, ABCD cracking temperature clearly differentiates between asphalt types (F value = 436, p–value < 0.001). However, there are significant variations in cracking temperature between laboratories. Among the ruggedness factors, only 'Over Trim' is statistically significant in affecting ABCD cracking temperature (significance level less than 1%).
Lab | Binder ID | Data: ABCD Cracking Temperature, C | |||||||||||||||
---|---|---|---|---|---|---|---|---|---|---|---|---|---|---|---|---|---|
#1 | #2 | #3 | #4 | #5 | #6 | #7 | #8 | #9 | #10 | #11 | #12 | #13 | #14 | #15 | #16 | ||
WI | EZ 1 | –31.2 | –26.8 | –30.1 | –29.4 | –34.8 | –32.0 | –32.9 | –30.4 | –33.3 | –33.7 | –33.8 | –30.8 | –30.4 | –29.5 | –30.8 | –31.4 |
EZ 2 | –41.0 | –37.7 | –39.3 | –42.2 | –38.6 | –40.1 | –42.9 | –37.5 | –41.5 | –36.9 | –38.4 | –39.2 | –39.0 | –40.3 | –42.1 | –38.3 | |
EZ 3 | –35.6 | –40.0 | –37.9 | –35.7 | –37.4 | –39.5 | –38.4 | –37.9 | –41.9 | –37.4 | –40.1 | –37.3 | –38.6 | –39.9 | –40.8 | –35.5 | |
EZ 4 | –48.3 | –47.1 | –47.3 | –44.8 | –50.8 | –48.5 | –48.8 | –46.0 | –45.3 | –42.4 | –47.0 | –44.9 | –47.4 | –45.4 | –46.5 | –45.4 | |
NC | EZ 1 | –30.2 | –30.6 | –30.3 | –28.3 | –31.2 | –32.9 | –27.4 | –28.5 | –32.4 | –32.6 | –28.7 | –30.3 | –33.2 | –31.4 | –32.9 | –31.8 |
EZ 2 | –32.1 | –32.2 | –35.8 | –32.6 | –36.1 | –33.6 | –33.5 | –35.9 | –34.9 | –33.4 | –34.9 | –38.9 | –33.2 | –32.7 | –35.2 | –37.6 | |
EZ 3 | –39.1 | –36.3 | –36.5 | –36.1 | –35.6 | –37.1 | –35.8 | –36.7 | –38.1 | –37.6 | –31.8 | –34.7 | –37.7 | –36.6 | –35.1 | –36.8 | |
EZ 4 | –46.3 | –40.8 | –45.3 | –41.0 | –44.9 | –46.6 | –39.6 | –41.9 | –41.3 | –40.3 | –41.9 | –41.2 | –43.9 | –39.4 | –43.1 | –43.7 | |
EZ | EZ 1 | –31.0 | –29.2 | –29.9 | –28.3 | –30.0 | –30.9 | –31.1 | –29.1 | –29.8 | –33.3 | –32.1 | –28.3 | –29.8 | –28.3 | –29.5 | –28.9 |
EZ 2 | –36.3 | –36.3 | –36.8 | –34.8 | –36.4 | –36.9 | –36.4 | –33.2 | –36.3 | –37.2 | –35.5 | –34.4 | –36.4 | –37.0 | –37.2 | –34.8 | |
EZ 3 | –35.2 | –32.9 | –36.3 | –32.8 | –33.1 | –33.2 | –33.4 | –35.0 | –34.4 | –35.5 | –36.3 | –34.9 | –36.2 | –37.0 | –36.9 | –34.5 | |
EZ 4 | –44.9 | –43.7 | –45.0 | –42.8 | –43.3 | –43.0 | –44.0 | –41.0 | –43.9 | –42.8 | –44.5 | –43.0 | –44.3 | –44.0 | –43.9 | –42.2 |
Lab | Binder | Data: ABCD Strain Jump at Fracture, ìå | |||||||||||||||
---|---|---|---|---|---|---|---|---|---|---|---|---|---|---|---|---|---|
#1 | #2 | #3 | #4 | #5 | #6 | #7 | #8 | #9 | #10 | #11 | #12 | #13 | #14 | #15 | #16 | ||
WI | EZ 1 | 39.7 | 17.0 | 97.5 | 33.8 | 47.9 | 26.0 | 17.0 | 19.9 | 32.3 | 40.4 | 27.2 | 21.0 | 46.3 | 97.7 | 64.3 | 65.0 |
EZ 2 | 54.0 | 36.7 | 38.6 | 36.7 | 42.1 | 37.8 | 44.7 | 31.4 | 58.8 | 20.4 | 26.3 | 33.4 | 36.6 | 47.2 | 32.6 | 49.9 | |
EZ 3 | 18.5 | 45.6 | 25.4 | 21.3 | 30.6 | 41.0 | 24.9 | 26.0 | 45.6 | 25.1 | 27.7 | 38.8 | 31.2 | 47.8 | 29.5 | 18.4 | |
EZ 4 | 62.8 | 29.3 | 28.6 | 47.9 | 74.9 | 65.5 | 43.1 | 55.4 | 59.8 | 35.9 | 35.4 | 28.2 | 54.9 | 40.4 | 31.2 | 35.8 | |
NC | EZ 1 | 32.6 | 25.2 | 18.9 | 12.0 | 25.4 | 29.6 | 12.8 | 8.8 | 31.4 | 14.0 | 8.1 | 23.6 | 33.8 | 29.3 | 25.7 | 40.9 |
EZ 2 | 7.1 | 14.7 | 8.9 | 9.8 | 21.5 | 16.6 | 13.4 | 28.1 | 9.9 | 9.1 | 28.4 | 33.7 | 8.6 | 9.6 | 13.4 | 43.0 | |
EZ 3 | 12.0 | 17.7 | 22.8 | 22.0 | 18.9 | 34.4 | 28.7 | 34.9 | 32.0 | 30.0 | 8.4 | 23.8 | 39.1 | 18.7 | 23.8 | 29.2 | |
EZ 4 | 31.4 | 11.6 | 28.4 | 17.1 | 20.7 | 38.4 | 18.1 | 18.0 | 14.3 | 16.1 | 21.1 | 12.7 | 21.1 | 15.6 | 10.5 | 16.5 | |
EZ | EZ 1 | 37.0 | 39.7 | 29.4 | 31.2 | 39.4 | 47.9 | 23.9 | 35.2 | 30.6 | 37.5 | 35.2 | 29.8 | 25.5 | 27.8 | 20.8 | 26.8 |
EZ 2 | 42.2 | 28.6 | 34.8 | 34.8 | 40.2 | 49.7 | 31.4 | 32.9 | 38.7 | 44.8 | 25.9 | 35.5 | 40.5 | 41.8 | 31.2 | 40.5 | |
EZ 3 | 30.5 | 16.3 | 20.4 | 13.6 | 26.2 | 11.5 | 9.1 | 26.4 | 24.3 | 27.4 | 23.2 | 23.3 | 34.0 | 33.1 | 18.9 | 24.6 | |
EZ 4 | 64.8 | 49.9 | 48.3 | 38.5 | 48.7 | 52.3 | 34.5 | 33.9 | 46.6 | 46.4 | 41.4 | 44.4 | 52.4 | 51.6 | 35.7 | 41.8 |
Lab | Asphalt | Std. Dev. (RMSE) | Cooling Rate | Protrusion | Over Trim | Lubrication | Turn Table | Cold Joint | Condition Time |
---|---|---|---|---|---|---|---|---|---|
WI | EZ 1 | 2.34 | NS | NS | NS | NT | NS | NS | NS |
EZ 2 | 0.83 | NS | NS | 58.27 | NT | NS | NS | 1432.82 | |
EZ 3 | 1.93 | NS | NS | NS | NT | NS | NS | NS | |
EZ 4 | 1.87 | 8.36 | NS | 36.40 | NT | NS | NS | NS | |
NC | EZ 1 | 1.87 | NS | 16.51 | NS | NT | NS | NS | NS |
EZ 2 | 1.91 | NS | 13.75 | NS | NT | NS | NS | NS | |
EZ 3 | 1.54 | NS | 27.57 | NS | NT | NS | NS | NS | |
EZ 4 | 2.49 | NS | NS | NS | NT | NS | NS | NS | |
EZ | EZ 1 | 1.39 | NS | NS | NS | NT | NS | NS | NS |
EZ 2 | 0.57 | NS | 82.70 | 18.82 | NT | NS | 122.44 | NS | |
EZ 3 | 1.65 | NS | NS | NS | NT | NS | NS | NS | |
EZ 4 | 0.63 | NS | NS | 133.54 | NT | NS | 7.44 | NS |
NS: not significant at 95% confidence level
NT: not tested
Critical F Statistics at 95% confidence level = 5.59
Source | Type III SS | df | Mean Square | F | Sig. |
---|---|---|---|---|---|
Corrected Model | 4860.693(a) |
11 |
441.881 |
130.313 |
.000 |
Intercept | 263551.470 |
1 |
263551.470 |
77722.475 |
.000 |
Lab | 365.832 |
2 |
182.916 |
53.943 |
.000 |
Asphalt | 4434.398 |
3 |
1478.133 |
435.908 |
.000 |
Cool Rate | 3.825 |
1 |
3.825 |
1.128 |
.290 |
Protrusion | 10.407 |
1 |
10.407 |
3.069 |
.082 |
Over Trim | 39.513 |
1 |
39.513 |
11.652 |
.001 |
Turn Table | 3.440 |
1 |
3.440 |
1.014 |
.315 |
Cold Joint | 1.860 |
1 |
1.860 |
.549 |
.460 |
Condition Time | 1.418 |
1 |
1.418 |
.418 |
.519 |
Error | 610.367 |
180 |
3.391 |
||
Total | 269022.530 |
192 |
|||
Corrected Total | 5471.060 |
191 |
a R Squared = .888 (Adjusted R Squared = .882)
Linear regression can provide quantified measures of significant variables, in terms of factor adjusted mean differences as shown in Table 16. In comparison to EZ Asphalt lab data, the average ABCD cracking temperatures determined by NC lab is 0.019°C warmer and those WI is 2.9°C lower. In comparison to EZ 1 binder (PG 64–16), EZ 2 (PG 70–22M) showed 6.0°C lower ABCD cracking temperatures on average; 5.8°C and 13.5°C lower for EZ 3 (PG 58–28) and EZ 4 (PG 63–34M), respectively. Figure 7 shows the average effects of laboratory and binder type. 'Over Trim' by 0.8mm resulted in 0.9°C warmer ABCD cracking temperatures on average. All other factors' influence in ABCD cracking temperature was less than 0.50°C and was not statistically significant.
Model | Unstandardized Coefficients | Standardized Coefficients | t | Sig. | ||
---|---|---|---|---|---|---|
B (°C) | Std. Error (°C) | Beta | ||||
1 | (Constant) | –30.226 |
.460 |
–65.657 |
.000 |
|
NC | .019 |
.326 |
.002 |
.058 |
.954 |
|
WI | –2.919 |
.326 |
–.258 |
–8.966 |
.000 |
|
EZ2 | –6.042 |
.376 |
–.490 |
–16.073 |
.000 |
|
EZ3 | –5.825 |
.376 |
–.473 |
–15.497 |
.000 |
|
EZ4 | –13.540 |
.376 |
–1.098 |
–36.021 |
.000 |
|
CoolRate | –.282 |
.266 |
–.026 |
–1.062 |
.290 |
|
Protrusion | .466 |
.266 |
.044 |
1.752 |
.082 |
|
OverTrim | .907 |
.266 |
.085 |
3.414 |
.001 |
|
TurnTable | .268 |
.266 |
.025 |
1.007 |
.315 |
|
ColdJoint | –.197 |
.266 |
–.018 |
–.741 |
.460 |
|
Condition | –.172 |
.266 |
–.016 |
–.647 |
.519 |
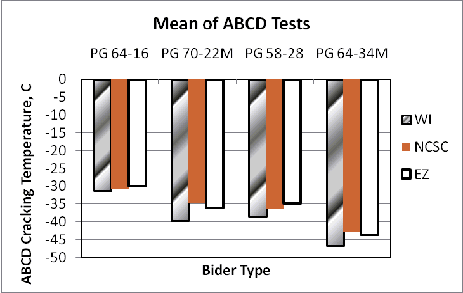
Figure 7. ABCD Ruggedness Test Results (Cracking Temperature); Comparison of Laboratory and Binder Type
4B.2 Strain Jump at Fracture
ABCD strain jump (å) at fracture can be converted into the fracture stress of the asphalt binder (óf ) as follows:
óf = (K) å EABCD AABCD/Abinder (or óf = 147 å kPa)
where,
K = stress concentration factor, 2.02
EABCD = Young's modulus of ABCD ring, 140 GPa
AABCD = Cross sectional area of ABCD ring, 21.0 x 10–6 mm2
Abinder = Cross sectional area of asphalt binder, 40.3 x 10–6 mm2
Following ASTM C 1067, data (Table 13) were analyzed and summarized in Table 17. When reviewed for each combination of four asphalt binder types and three laboratories, there are 12 cases as shown. The size of protrusion is the factor affecting test results most significantly (six significant cases). For all four binders tested at the EZ Asphalt laboratory, the effect of protrusion size is significant. Lack of significance for other laboratories may be due to larger overall test variability (within lab).
Lab | Asphalt | Std. Dev. (RMSE) | Cooling Rate | Protrusion | Over Trim | Lubrication | Turn Table | Cold Joint | Condition Time |
---|---|---|---|---|---|---|---|---|---|
WI | EZ 1 | 30.74 |
NS |
NS |
NS |
NT |
NS |
NS |
NS |
EZ 2 | 8.13 |
NS |
NS |
NS |
NT |
NS |
NS |
5.99 |
|
EZ 3 | 9.97 |
NS |
NS |
NS |
NT |
NS |
NS |
NS |
|
EZ 4 | 11.30 |
7.89 |
52.80 |
NS |
NT |
NS |
40.45 |
NS |
|
NC | EZ 1 | 10.14 |
NS |
NS |
NS |
NT |
NS |
NS |
NS |
EZ 2 | 9.45 |
NS |
6.46 |
NS |
NT |
NS |
NS |
NS |
|
EZ 3 | 9.59 |
NS |
NS |
NS |
NT |
NS |
NS |
NS |
|
EZ 4 | 7.77 |
NS |
NS |
NS |
NT |
8.09 |
NS |
NS |
|
EZ | EZ 1 | 6.89 |
NS |
12.12 |
NS |
NT |
NS |
NS |
NS |
EZ 2 | 5.44 |
NS |
24.35 |
NS |
NT |
NS |
NS |
NS |
|
EZ 3 | 7.46 |
NS |
7.77 |
NS |
NT |
NS |
7.22 |
NS |
|
EZ 4 | 5.61 |
NS |
169.3 |
NS |
NT |
NS |
NS |
NS |
NS: not significant at 95% confidence level
NT: not tested
Critical F Statistics at 95% confidence level = 5.59
In preparation for the Interlaboratory test, the statistical difference between laboratories was also examined and the results are given Table 18. ABCD strain jump at fracture can differentiate asphalt types (F value = 6.68, p–value < 0.001). Among the ruggedness factors, 'Protrusion' size and use of 'Turn Table' are statistically significant in affecting ABCD strain jump (significance level less than 1%).
Linear regression provides quantified measures of these differences, in terms of factor adjusted mean differences as shown in Table 19. In comparison to EZ Asphalt lab data, the average ABCD strain jump determined by NC lab is 13 ìå lower and that by WI is 5 ìå higher. Increasing the protrusion diameter from 5.84 mm (0.23 in.) to 6.34 mm (0.25 in.) lowered the strain jump at failure by 5 ìå. The use of turntables in sample preparation and handling also lowered the strain jump at failure by 4 ìå. Figure 8 shows the average effects of laboratory and binder type on ABCD strain jump at fracture.
Source | Type III Sum of Squares | df | Mean Square | F | Sig. |
---|---|---|---|---|---|
Corrected Model | 17545.530(a) |
11 |
1595.048 |
11.190 |
.000 |
Intercept | 194298.025 |
1 |
194298.025 |
1363.055 |
.000 |
Lab | 11749.674 |
2 |
5874.837 |
41.214 |
.000 |
AC | 2857.001 |
3 |
952.334 |
6.681 |
.000 |
CoolRate | 410.670 |
1 |
410.670 |
2.881 |
.091 |
Protrusion | 1346.201 |
1 |
1346.201 |
9.444 |
.002 |
OverTrim | 3.521 |
1 |
3.521 |
.025 |
.875 |
TurnTable | 900.467 |
1 |
900.467 |
6.317 |
.013 |
ColdJoint | 269.327 |
1 |
269.327 |
1.889 |
.171 |
Condition | 8.670 |
1 |
8.670 |
.061 |
.805 |
Error | 25658.284 |
180 |
142.546 |
||
Total | 237501.840 |
192 |
|||
Corrected Total | 43203.815 |
191 |
a R Squared = .406 (Adjusted R Squared = .370)
Model | Unstandardized Coefficients | Standardized Coefficients | t | Sig. | ||
---|---|---|---|---|---|---|
B | Std. Error | Beta | ||||
1 | (Constant) | 40.078 |
2.985 |
13.427 |
.000 |
|
NC | –13.270 |
2.111 |
–.417 |
–6.288 |
.000 |
|
WI | 5.336 |
2.111 |
.168 |
2.528 |
.012 |
|
EZ2 | –1.798 |
2.437 |
–.052 |
–.738 |
.462 |
|
EZ3 | –6.796 |
2.437 |
–.196 |
–2.789 |
.006 |
|
EZ4 | 3.940 |
2.437 |
.114 |
1.617 |
.108 |
|
CoolRate | 2.925 |
1.723 |
.097 |
1.697 |
.091 |
|
Protrusion | –5.296 |
1.723 |
–.177 |
–3.073 |
.002 |
|
OverTrim | –.271 |
1.723 |
–.009 |
–.157 |
.875 |
|
TurnTable | –4.331 |
1.723 |
–.144 |
–2.513 |
.013 |
|
ColdJoint | –2.369 |
1.723 |
–.079 |
–1.375 |
.171 |
|
Condition | .425 |
1.723 |
.014 |
.247 |
.805 |
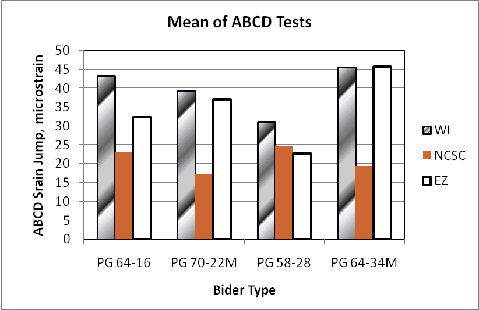
Figure 8. ABCD Ruggedness Test Results (Strain Jump); Comparison of Laboratory and Binder Type
The analysis of the ruggedness test shows that ABCD testing is
- Able to differentiate different asphalt binders in terms of their low temperature cracking potential and strength (strain jump at failure).
- At each laboratory, the ABCD test results were reproducible.
However, as the statistics above indicate, there was significant variability among laboratories. Therefore, the EZ Asphalt Technology laboratory performed investigative testing which resulted in modifying the ABCD test procedure. Then, additional samples of the binders (EZ1, EZ2, EZ3, and EZ4) were sent to the NC and WI labs, and those labs conducted supplemental tests to validate the updated ABCD test procedure.