Asphalt Binder Cracking Device to reduce Low Temperature Asphalt Pavement Cracking
4C. SUPPLEMENTAL TEST (PILOT INTERLABORATORY STUDY)
The ruggedness testing focuses on "within Lab" variability not "between Lab" variability. Factors affecting "between Lab" may or may not influence "within Lab" variability.
As discussed in the previous section, over–trimming and the size of the protrusion diameter need to have tighter controls than other factors since they were determined to statistically affect ABCD cracking temperatures. Avoiding over–trimming depends on operator expertise while protrusion diameter is fixed by the type of mold provided to each lab. The harder–to–control factor of operator expertise is further addressed in this section which describes supplemental tests which have been conducted to address this issue.
In preparation for the Interlaboratory Study planned for Phase II, some of the ruggedness data performed under conditions close to the normal ABCD tests were reviewed (data #3, #7, #11, and #15). For these data, tests were performed with the regular protrusion mold and even trimming. For data #3 and #11 no turntable was used and samples were cooled for 50 min at 0°C prior to trimming. For data #7 and #15, turntables were used and samples were cooled for 20 min at 0°C prior to trimming. These data are given in Table 20 and 21 for ABCD cracking temperature and strain jump respectively.
The ASTM ruggedness procedure ignores interactions among variables. The resulting statistics also assume no interaction. In the ABCD ruggedness testing, there appear to be very significant variations in ABCD test proficiency among operators. The operator at the EZ Asphalt lab has performed the ABCD test for ten months since February 2008. Operators at the other two labs had no prior experience with ABCD; while one of them (NC) had many years of professional experience in asphalt material testing, the other (WI) started asphalt testing 1.5 years ago as he started graduate study. The level of operator experience is an important factor in explaining the ABCD ruggedness test results. Among laboratories, there was significant variability.
Binder ID | Lab | Cracking Temperature, C | Lab Avg Range (Max–Min) | |||||
---|---|---|---|---|---|---|---|---|
Data #3 | Data #7 | Data #11 | Data #15 | Mean | St Dev | |||
EZ 1 | WI | –30.1 | –33.8 | –32.9 | –30.8 | –31.9 | 1.7 | 2.1 |
NC | –30.3 | –28.7 | –27.4 | –32.9 | –29.8 | 2.4 | ||
EZ | –29.9 | –32.1 | –31.1 | –29.5 | –30.7 | 1.2 | ||
EZ 2 | WI | –39.3 | –38.4 | –42.9 | –42.1 | –40.7 | 2.2 | 5.8 |
NC | –35.8 | –34.9 | –33.5 | –35.2 | –34.9 | 1.0 | ||
EZ | –36.8 | –35.5 | –36.4 | –37.2 | –36.5 | 0.7 | ||
EZ 3 | WI | –37.9 | –40.1 | –38.4 | –40.8 | –39.3 | 1.4 | 4.5 |
NC | –36.5 | –31.8 | –35.8 | –35.1 | –34.8 | 2.1 | ||
EZ | –36.3 | –36.3 | –33.4 | –36.9 | –35.7 | 1.6 | ||
EZ 4 | WI | –47.3 | –47.0 | –48.8 | –46.5 | –47.4 | 1.0 | 4.9 |
NC | –45.3 | –41.9 | –39.6 | –43.1 | –42.5 | 2.4 | ||
EZ | –45.0 | –44.5 | –44.0 | –43.9 | –44.4 | 0.5 |
Binder ID | Lab | ABCD Cracking Temperature, C | Lab Avg Range (Max–Min) | |||||
---|---|---|---|---|---|---|---|---|
Data #3 | Data #7 | Data #11 | Data #15 | Mean | St Dev | |||
EZ 1 | WI | 97.5 | 27.2 | 17.0 | 64.3 | 51.5 | 36.8 | 35.1 |
NC | 18.9 | 8.1 | 12.8 | 25.7 | 16.4 | 7.6 | ||
EZ | 29.4 | 35.2 | 23.9 | 20.8 | 27.3 | 6.3 | ||
EZ 2 | WI | 38.6 | 26.3 | 44.7 | 32.6 | 35.6 | 7.9 | 19.5 |
NC | 8.9 | 28.4 | 13.4 | 13.4 | 16.0 | 8.5 | ||
EZ | 34.8 | 25.9 | 31.4 | 31.2 | 30.8 | 3.7 | ||
EZ 3 | WI | 25.4 | 27.7 | 24.9 | 29.5 | 26.9 | 2.1 | 9.0 |
NC | 22.8 | 8.4 | 28.7 | 23.8 | 20.9 | 8.7 | ||
EZ | 20.4 | 23.2 | 9.1 | 18.9 | 17.9 | 6.1 | ||
EZ 4 | WI | 28.6 | 35.4 | 43.1 | 31.2 | 34.6 | 6.3 | 20.5 |
NC | 28.4 | 21.1 | 18.1 | 10.5 | 19.5 | 7.4 | ||
EZ | 48.3 | 41.4 | 34.5 | 35.7 | 40.0 | 6.3 |
To develop a better test procedure, additional tests were conducted at the EZ Asphalt lab to investigate the effect of cooling at room temperature before trimming (rather than cooling at 0°C). EZ Asphalt also ran tests to investigate the effect of rotating the ABCD ring after trimming to reduce variation in the strain jump. After trimming, rotating the ABCD ring about 5 to 30 degrees and back breaks any bond that was formed between the ABCD ring and the binder. While lubrication is the major factor allowing the binder to contract freely against the ring, rotating the ring further reduces friction between the binder and ring. Cooling at room temperature for one hour resulted in much easier trimming than at 0°C, thus more consistent sample preparation when investigated by having a new person conduct tests at the EZ Asphalt lab.
Over the last several years, Dr. Kim investigated room temperature trimming for various time periods. The duration of cooling was not determined to be a critical variable so long as it was at least 45 minutes. From Dr. Kim's historical work with ABCD cooling times, one hour was selected.
Rotating the ring reduced the standard deviation among the EZ Asphalt samples. EZ Asphalt then tested all four binders used in the ruggedness test again but with room temperature cooling, four turntables, ring rotation, and in four identical standard molds. The standard molds all had the standard protrusion diameter and did not have an indentation (the indentation used in the ruggedness molds simulated over–trimming). These standard tests were all run at a cooling rate of 20°C per hour (rather than 18 and 22°C/hr in the original ruggedness tests).
While investigating the effect of ring rotation and room temperature cooling at the EZ Asphalt lab, a video was received from the WI lab showing its trimming technique.The WI trimming does not agree with the trimming method shown in EZ Asphalt's training video. The WI trimming method tends to push excess binder back into the annulus rather than removing the excess. EZ Asphalt surmised that the WI trimming method could easily account for the higher standard deviations among their samples as well as the deviations between the WI average cracking temperatures and those of NC and EZ Asphalt.
As a result of viewing the WI video, EZ Asphalt asked WI to test an EZ3 binder using the trimming method shown in the EZ Asphalt video. Their results were much better. EZ Asphalt then mailed both the NC and WI labs additional cans of all four binders. Then NC and WI tested all four binders using the four standard identical molds (standard protrusion, no indent), four turntables, room temperature cooling for one hour, ring rotation, and cooling rate of 20°C/hr (and for WI, the proper trimming method). The results of the supplement tests are given in Tables 22 and 23 for cracking temperature and strain jump. respectively. By using the standard procedure (and proper WI trimming), the standard deviations of "within lab" measurements as well as between lab variability became smaller for both ABCD cracking temperature and strain jump. The "Max–Min" values in the Tables became smaller. The "Max–Min" value for a binder was computed by subtracting the minimum mean value for the binder from the maximum mean value for the binder. For instance in Table 22 for EZ3, "Max–Min" = 38.2–35.2=2.1°C (other values may not be exact due to round–off when the table was imported from Excel). This value represents the variation among the three different labs for the same binder. The standard procedure (and proper WI trimming) reduced the EZ1 "Max–Min" from 2.1°C to 1.5°C, EZ2 from 5.8°C to 1.3°C, EZ3 from 4.5°C to 3.0°C and EZ4 from 4.9°C to 1.1°C.
As shown in Tables 24 and 25, EZ Asphalt lab results (most experienced ABCD operator) were least affected by changing the test procedure and WI lab results (least experienced ABCD operator) were most affected. Polymer modified binder results (EZ2 and EZ4) improved more than unmodified binder results.
Binder ID | Lab | ABCD Cracking Temperature, C | Lab Avg Range (Max–Min) | |||||
---|---|---|---|---|---|---|---|---|
Rep #1 | Rep #2 | Rep #3 | Rep #4 | Mean | St Dev | |||
EZ 1 | WI | –32.2 | –31.6 | –31.1 | –31.7 | –31.7 | 0.4 | 1.5 |
NC | –30.5 | –26.9 | –31.4 | –31.7 | –30.1 | 2.2 | ||
EZ | –32.3 | –29.5 | –31.1 | –30.9 | –30.9 | 1.2 | ||
EZ 2 | WI | –37.5 | –38.6 | –37.1 | –37.7 | 0.7 | 1.3 |
|
NC | –37.0 | –36.2 | –34.8 | –37.8 | –36.5 | 1.3 | ||
EZ | –36.5 | –36.7 | –37.7 | –35.6 | –36.6 | 0.8 | ||
EZ 3 | WI | –36.1 | –40.4 | –36.9 | –39.3 | –38.2 | 2.0 | 3.0 |
NC | –35.5 | –36.6 | –34.8 | –33.8 | –35.2 | 1.2 | ||
EZ | –36.2 | –36.9 | –35.8 | –37.7 | –36.6 | 0.8 | ||
EZ 4 | WI | –43.1 | –43.5 | –42.8 | –44.5 | –43.5 | 0.8 | 1.1 |
NC | –46.5 | –43.9 | –42.6 | –45.1 | –44.5 | 1.7 | ||
EZ | –44.7 | –43.7 | –43.2 | –44.1 | –43.9 | 0.6 |
Binder ID | Lab | ABCD Cracking Temperature, C | Lab Avg Range (Max–Min) | |||||
---|---|---|---|---|---|---|---|---|
Data #3 | Data #7 | Data #11 | Data #15 | Mean | St Dev | |||
EZ 1 | WI | 33.1 | 30.7 | 21.3 | 36.5 | 30.4 | 6.5 | 10.5 |
NC | 25.4 | 18.3 | 32.4 | 29.0 | 26.3 | 6.0 | ||
EZ | 43.3 | 38.0 | 28.0 | 37.7 | 36.7 | 6.4 | ||
EZ 2 | WI | 17.9 | 36.7 | 30.9 | 28.5 | 9.7 | 6.9 |
|
NC | 35.8 | 37.3 | 32.5 | 21.1 | 31.7 | 7.3 | ||
EZ | 37.9 | 42.8 | 29.3 | 28.1 | 35.4 | 7.1 | ||
EZ 3 | WI | 13.1 | 43.5 | 20.5 | 33.6 | 27.7 | 13.6 | 8.8 |
NC | 17.7 | 29.1 | 17.0 | 23.4 | 21.8 | 5.6 | ||
EZ | 31.1 | 33.7 | 19.1 | 38.7 | 30.7 | 8.3 | ||
EZ 4 | WI | 29.3 | 47.7 | 22.1 | 25.9 | 31.2 | 11.4 | 11.0 |
NC | 30.0 | 36.2 | 49.2 | 32.9 | 37.1 | 8.4 | ||
EZ | 54.5 | 42.9 | 28.7 | 42.8 | 42.2 | 10.5 |
Lab | Asphalt Binder | Max–Min (C) | |||
---|---|---|---|---|---|
EZ1 | EZ2 | EZ3 | EZ4 | ||
WI | –0.2 | –3.0 | –1.1 | –3.9 | 3.7 |
NC | –0.3 | 1.6 | 0.4 | 2.1 | 2.4 |
EZ | 0.3 | 0.2 | 0.9 | –0.4 | 1.4 |
Lab | Asphalt Binder | Max–Min (µå) | |||
---|---|---|---|---|---|
EZ1 | EZ2 | EZ3 | EZ4 | ||
WI | 21.1 | 7.1 | –0.8 | 3.3 | 21.9 |
NC | –9.9 | –15.7 | –0.9 | –17.6 | 16.7 |
EZ | –9.4 | –4.6 | –12.8 | –2.2 | 10.5 |
Analysis of variance (ANOVA) in Table 26 reveals that the ABCD test procedure used in the original ruggedness test caused "laboratory" to be a very significant factor affecting ABCD cracking temperatures (p–value < 0.01). This means that ABCD cracking temperatures for the same samples determined at three laboratories are significantly different. Of all variability in ABCD cracking temperature, 81.3% (1178.4/1449.3) was due to the difference in asphalt binders and 10.9% (157.8/1449.3) was due to laboratories. When the new ABCD test procedure (cooling to room temperature prior to trimming, and ring rotation) was used in supplemental ruggedness tests, the variability caused by laboratories was significantly reduced and became insignificant (p–value > 0.05) as shown in Table 27. Of all variability in ABCD cracking temperature using the new procedure, 92.3% of the variability was due to the difference in asphalt binders and only 1.0% was due to laboratories.
As shown in Tables 28 and 29, by changing ABCD test procedure, the effects of laboratories on ABCD strain jump at fracture were significantly reduced (from p–value <0.01 to p–value = 0.04), and the effect of the asphalt binder became significant (from p–value = 0.24 to p–value = 0.04). Figures 9 and 10 also show the improved "between lab" variation.
Source | Type III Sum of Squares | df | Mean Square | F | p–value |
---|---|---|---|---|---|
Corrected Model | 1336.210a | 5 | 267.242 | 99.230 | .000 |
Intercept | 67028.327 | 1 | 67028.327 | 24888.313 | .000 |
Lab | 157.841 | 2 | 78.921 | 29.304 | .000 |
Binder | 1178.369 | 3 | 392.790 | 145.847 | .000 |
Error | 113.113 | 42 | 2.693 | ||
Total | 68477.650 | 48 | |||
Corrected Total | 1449.323 | 47 |
a. R Squared = .922 (Adjusted R Squared = .913)
Source | Type III Sum of Squares | df | Mean Square | F | p–value |
---|---|---|---|---|---|
Corrected Model | 1039.126a | 5 | 207.825 | 114.331 | .000 |
Intercept | 64593.220 | 1 | 64593.220 | 35534.799 | .000 |
Lab | 10.858 | 2 | 5.429 | 2.987 | .062 |
Binder | 1027.985 | 3 | 342.662 | 188.509 | .000 |
Error | 74.528 | 41 | 1.818 | ||
Total | 65834.607 | 47 | |||
Corrected Total | 1113.654 | 46 |
a. R Squared = .933 (Adjusted R Squared = .925)
Source | Type III Sum of Squares | df | Mean Square | F | p–value |
---|---|---|---|---|---|
Corrected Model | 3632.440a | 5 | 726.488 | 4.261 | .003 |
Intercept | 37940.630 | 1 | 37940.630 | 222.538 | .000 |
Lab | 2880.543 | 2 | 1440.271 | 8.448 | .001 |
Binder | 751.897 | 3 | 250.632 | 1.470 | .236 |
Error | 7160.600 | 42 | 170.490 | ||
Total | 48733.670 | 48 | |||
Corrected Total | 10793.040 | 47 |
a. R Squared = .337 (Adjusted R Squared = .258)
Source | Type III Sum of Squares | df | Mean Square | F | p–value |
---|---|---|---|---|---|
Corrected Model | 1089.847a | 5 | 217.969 | 3.118 | .018 |
Intercept | 46782.101 | 1 | 46782.101 | 669.287 | .000 |
Lab | 470.048 | 2 | 235.024 | 3.362 | .044 |
Binder | 619.209 | 3 | 206.403 | 2.953 | .044 |
Error | 2865.833 | 41 | 69.898 | ||
Total | 50980.317 | 47 | |||
Corrected Total | 3955.680 | 46 |
a. R Squared = .276 (Adjusted R Squared = .187)
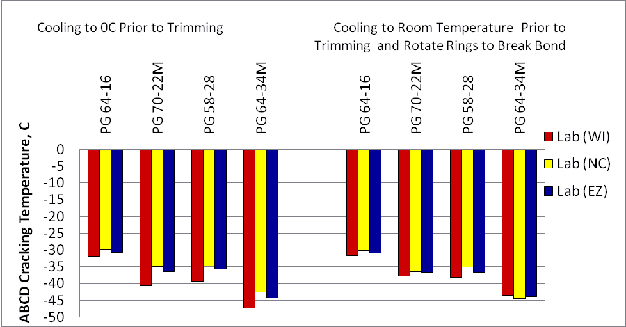
Figure 9. Effects of Sample Preparation Procedures on ABCD Cracking Temperature
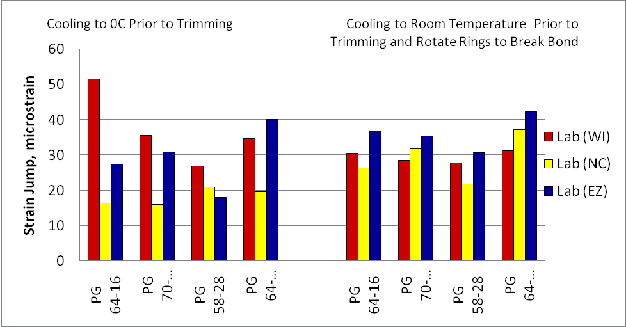
Figure 10. Effects of Sample Preparation Procedures on Strain Jump
4D. Survey of Ruggedness Participants
North Central Superpave Center and University of Wisconsin – Madison completed surveys evaluating their experiences with ABCD in the ruggedness testing and pilot interlaboratory testing. The survey was designed by EZ Asphalt and consisted of 23 questions rating aspects such as pouring, trimming, connecting wires, and running the software on a scale of 1 to 5 with 1 being poorest and 5 being highest rating. In all the questions, a response of 5 would be the most favorable for the ABCD. NC and WI survey results yielded averages of 3.9 and 4.3, respectively. NC was most critical of the difficulty in constructing the pouring spout and computer problems. WI was most critical of the computer requiring a re–start after every test and the pourability of the binders. EZ Asphalt will work to solve these problems. Complete survey results for NC and WI appear in Appendix B.
Conclusion
The ABCD has been evaluated in Phase 1 for refinement of test procedures, field validation of the ABCD, refinement of equipment and analysis software, and ruggedness testing. Throughout the year of Phase 1 investigations, the ABCD device was improved to the point where it only must now undergo Interlaboratory testing for it to be a saleable device.
In Phase 1, the silicone mold was modified, the cooling rate was optimized, and turntables were incorporated. Many binders were tested for continuous improvement of the ABCD. Ruggedness testing is an important aspect of bringing a new test device to market. Successful ruggedness testing of the ABCD at the North Central Superpave Center, University of Wisconsin – Madison, and EZ Asphalt laboratories showed that the ABCD is ready for Interlaboratory Testing in Phase 2. The ABCD has the potential to save the country significant funds since it provides a direct, consistent, and accurate determination of the cracking temperature and strength of aged, unaged, polymer–modified, and unmodified binders. It provides a cracking temperature that mimics field results more reliably than existing methods and will likely prove to be very economical for the industry.