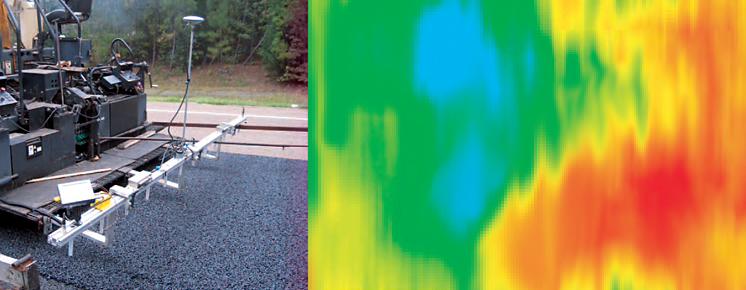
Using infrared (IR) imaging and ground-penetrating radar (GPR) for uniformity measurements on new hot-mix asphalt (HMA) layers.
Technologies to Enhance Quality Control on Asphalt Pavements (R06C)
Challenge
The uniformity of HMA materials is critical to the durability and performance of an asphalt product. Segregation and inadequate and non-uniform density continues to be a major construction-related problem around the nation, with a significant adverse impact on pavement service life. Commonly used QC testing procedures only provide limited information on the overall uniformity of the HMA product. The ability to provide information that is real-time, non-destructive, and covers the full pavement width for both thermal uniformity and densification will greatly aid in improving the quality of HMA.
Solution
SHRP2 examined two nondestructive techniques for measuring uniformity and potential defect areas in asphalt pavements during construction. Both technologies (infrared and radar) offer real-time testing of potentially 100 percent of the pavement area, providing much more inspection coverage than existing QC methods. These new technologies improve the state of the practice for obtaining quality control data in hot- or warm-mix construction.
The infrared technology focuses on the thermal uniformity equipment, which enables inspectors and paving crews to measure the real-time mat temperature and make adjustments. The GPR technology provides greater area information on pavement densification of thin lifts after rolling, allowing for quicker turnaround and potentially avoiding costly and time-sensitive nuclear testing.
Products include recommendations for equipment and testing protocols for using infrared and GPR for testing the entire surface area during new HMA construction, and IR guide specifications.
Benefits
Real-time temperature QC allows for prompt adjustments by the paving crew, thereby minimizing segregation problems that can occur when the temperature is too low. Using GPR technology reduces the reliance on single-point density gauges and instead provides greater pavement coverage. In addition to savings resulting from these innovations, near-term benefits include
- More uniformly constructed hot- and warm-mix asphalt layers
- Better in-place field density
- Improved communication among paving crews, their supervisors, and transportation agency personnel
- Improved ride
- Reduced discrepancies between contractor and agency test data
In the long term, implementation of these commercially available products could result in longer-lived pavements, enabling agencies to stretch their funding further and decrease user costs.
-
Save Lives
Evaluating uniformity of the pavement in real time with greater ease minimizes the need for future pavement corrective actions, thus reducing driver exposure to future roadway and work zone hazards.
-
Save Money
More inspection coverage helps avoid noncompliance penalties. Better quality control leads to smoother pavement for travelers and longer-lasting pavement for owners. Real-time density testing allows for quick and efficient field modification. Real-time temperature quality control enables prompt adjustments to avoid costly corrections later.
-
Save Time
Real-time testing results in time savings during construction operations. Increased testing coverage area lessens the need for corrective action due to low-density asphalt pavements.