Composite Bridge Decking: Phase I Design Report
APPENDIX L: FIRE TEST REPORT
Description of Tested Specimen
A full-depth panel measuring 3 feet by 7 feet was tested to evaluate its fire resistance properties. The standard design of the panel uses fire-resistant resin, but no further protection was provided. It was tested without a wearing surface. See figure 93.
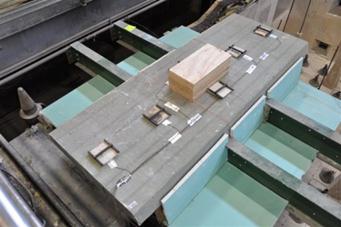
Figure 93. Photo. Test panel mounted on top of fire chamber.
Description of Test Setup
The test specimen was placed over the pilot scale combustion chamber, resting atop and perpendicular to two structural steel support beams (I-beams) spaced 24 inches on center (to be consistent with the proof-of-concept bridge in Allegany County). The support beams each measured 10.5 inches high with 4-inch-wide flanges and 0.25-inch web thickness. The surrounding exposed areas were enclosed with 1-inch-thick non-combustible gypsum shaft liner panels. Only a portion of the length was exposed to the fire over the combustion chamber.
Figure 94 shows the fire test chamber and the steel beams used to support the deck. This picture was taken after the test; note the peeled paint above the fire chamber.
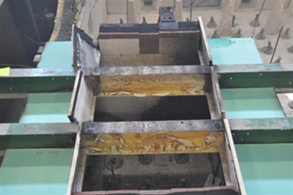
Figure 94. Photo. Support beams spaced at 2 feet.
The panel was loaded to a total superimposed load of 1,600 lb, nominally, using a water-filled steel tank, shown in figure 95, and instrumented with numerous thermocouples. Figure 96 and table 32 detail the placement of the thermocouples. The tank rested on the wood shown at the center of figure 93. This wood was dimensioned to reflect the standard AASHTO 10-inch by 20-inch footprint of a design vehicle.
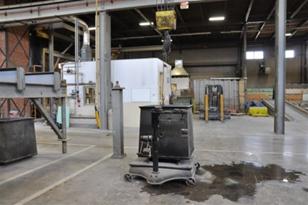
Figure 95. Photo. 1,600-lb water tank used as concentrated load.
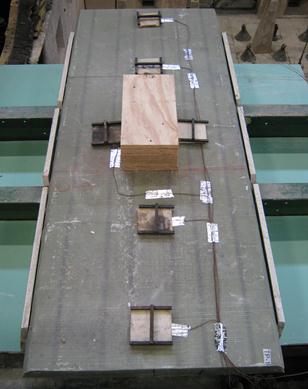
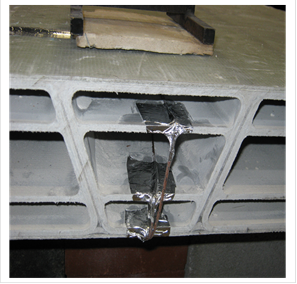
Figure 96. Photos. Placement of thermocouples on the test panel.
Thermocouple | X, Y Location | Z Location |
---|---|---|
TC01 | on longitudinal axis, 42" from transverse axis | top surface of deck panel |
TC02 | on longitudinal axis, 24" from transverse axis | top surface of deck panel |
TC03 | 10" from longitudinal axis, on transverse axis | top surface of deck panel |
TC04 | 10" from longitudinal axis, on transverse axis | top surface of deck panel |
TC05 | on longitudinal axis, 24" from transverse axis | top surface of deck panel |
TC06 | on longitudinal axis, 42" from transverse axis | top surface of deck panel |
TC07 | on longitudinal axis, on transverse axis | 1-3/8" from top surface of deck panel |
TC08 | on longitudinal axis, on transverse axis | 3-1/2" from top surface of deck panel |
TC09 | on longitudinal axis, on transverse axis | 4-5/8" from top surface of deck panel |
Test Program
The panel was loaded with the water tank before igniting the chamber and bringing the temperature to approximately 1,600 degrees Fahrenheit. The heat was applied for 20 minutes, at which time the test was stopped due to excessive smoke. Deflection measurements of the bridge deck panel, provided in table 33, were recorded at 1-minute intervals for the entire test duration. A technician sighted in on a leveling rod to measure the amount of deflection under load.
TC-797 | BRIDGE COMPOSITES LLC | K-1084 | 9/7/2012 | |||||||
---|---|---|---|---|---|---|---|---|---|---|
Time (min) | TC01 | TC02 | TC03 | TC04 | TC05 | TC06 | Grp Avg | TC07 | TC08 | TC09 |
0.00 | 76 | 76 | 76 | 76 | 76 | 77 | 76 | 77 | 76 | 78 |
0.25 | 77 | 76 | 76 | 76 | 76 | 77 | 76 | 77 | 76 | 78 |
0.50 | 76 | 76 | 76 | 76 | 76 | 77 | 76 | 77 | 76 | 78 |
0.75 | 76 | 76 | 76 | 76 | 76 | 77 | 76 | 79 | 76 | 77 |
1.00 | 76 | 76 | 76 | 76 | 76 | 77 | 76 | 82 | 76 | 78 |
1.25 | 76 | 76 | 76 | 76 | 76 | 77 | 76 | 87 | 76 | 78 |
1.50 | 76 | 76 | 76 | 76 | 76 | 77 | 76 | 95 | 76 | 77 |
1.75 | 76 | 76 | 76 | 76 | 76 | 77 | 76 | 104 | 76 | 78 |
2.00 | 76 | 76 | 76 | 76 | 76 | 77 | 76 | 125 | 77 | 78 |
2.25 | 76 | 76 | 76 | 76 | 76 | 77 | 76 | 137 | 77 | 78 |
2.50 | 76 | 76 | 76 | 76 | 76 | 77 | 76 | 147 | 77 | 77 |
2.75 | 76 | 76 | 76 | 76 | 76 | 77 | 76 | 157 | 78 | 78 |
3.00 | 76 | 76 | 76 | 76 | 76 | 77 | 76 | 165 | 79 | 78 |
3.50 | 76 | 76 | 76 | 76 | 76 | 77 | 76 | 174 | 80 | 78 |
3.75 | 76 | 76 | 76 | 76 | 76 | 77 | 76 | 182 | 81 | 78 |
4.00 | 76 | 76 | 76 | 76 | 76 | 77 | 76 | 189 | 82 | 78 |
4.25 | 76 | 76 | 76 | 76 | 76 | 77 | 76 | 197 | 83 | 78 |
4.50 | 76 | 76 | 76 | 76 | 76 | 77 | 76 | 204 | 85 | 78 |
4.75 | 76 | 76 | 76 | 76 | 76 | 77 | 76 | 211 | 87 | 78 |
5.00 | 76 | 76 | 76 | 76 | 76 | 77 | 76 | 218 | 89 | 78 |
5.25 | 76 | 76 | 76 | 76 | 76 | 77 | 76 | 225 | 91 | 78 |
5.50 | 76 | 76 | 76 | 76 | 76 | 77 | 76 | 233 | 93 | 78 |
5.75 | 76 | 76 | 76 | 76 | 76 | 77 | 76 | 239 | 94 | 78 |
6.00 | 76 | 76 | 76 | 76 | 76 | 77 | 76 | 240 | 96 | 78 |
6.25 | 76 | 76 | 76 | 76 | 76 | 77 | 76 | 239 | 98 | 78 |
6.50 | 76 | 76 | 76 | 76 | 76 | 77 | 76 | 240 | 100 | 78 |
6.75 | 76 | 76 | 76 | 76 | 76 | 77 | 76 | 242 | 102 | 78 |
7.00 | 76 | 76 | 76 | 76 | 76 | 77 | 76 | 245 | 103 | 78 |
7.25 | 76 | 76 | 76 | 76 | 76 | 77 | 77 | 248 | 105 | 78 |
7.50 | 76 | 76 | 76 | 76 | 76 | 77 | 77 | 251 | 106 | 78 |
7.75 | 76 | 76 | 76 | 76 | 76 | 77 | 77 | 254 | 108 | 77 |
8.00 | 76 | 76 | 76 | 76 | 76 | 77 | 77 | 258 | 110 | 78 |
8.25 | 76 | 76 | 76 | 76 | 76 | 77 | 77 | 261 | 112 | 79 |
8.50 | 76 | 76 | 76 | 76 | 76 | 77 | 77 | 266 | 114 | 79 |
8.75 | 76 | 76 | 76 | 76 | 76 | 77 | 77 | 270 | 115 | 79 |
9.00 | 76 | 76 | 76 | 76 | 76 | 77 | 77 | 274 | 117 | 79 |
9.25 | 76 | 76 | 76 | 76 | 76 | 77 | 77 | 278 | 118 | 79 |
9.50 | 76 | 76 | 76 | 76 | 76 | 77 | 77 | 282 | 120 | 79 |
9.75 | 76 | 76 | 76 | 76 | 76 | 77 | 77 | 286 | 121 | 79 |
10.00 | 76 | 76 | 76 | 76 | 76 | 77 | 77 | 291 | 123 | 79 |
10.25 | 76 | 76 | 76 | 76 | 76 | 77 | 78 | 295 | 125 | 79 |
10.50 | 76 | 76 | 76 | 76 | 76 | 77 | 78 | 299 | 126 | 79 |
10.75 | 76 | 76 | 76 | 76 | 76 | 77 | 78 | 303 | 128 | 79 |
11.00 | 76 | 76 | 76 | 76 | 76 | 77 | 78 | 307 | 131 | 79 |
11.25 | 76 | 76 | 76 | 76 | 76 | 77 | 78 | 311 | 132 | 80 |
11.50 | 76 | 76 | 76 | 76 | 76 | 77 | 78 | 316 | 133 | 80 |
11.75 | 76 | 76 | 76 | 76 | 76 | 77 | 78 | 320 | 136 | 80 |
12.00 | 76 | 76 | 76 | 76 | 76 | 77 | 78 | 325 | 138 | 80 |
12.25 | 76 | 76 | 76 | 76 | 76 | 77 | 78 | 331 | 139 | 80 |
12.50 | 76 | 76 | 76 | 76 | 76 | 77 | 79 | 337 | 140 | 80 |
12.75 | 76 | 76 | 76 | 76 | 76 | 77 | 79 | 342 | 140 | 80 |
13.00 | 76 | 76 | 76 | 76 | 76 | 77 | 79 | 348 | 144 | 80 |
13.25 | 76 | 76 | 76 | 76 | 76 | 77 | 79 | 354 | 146 | 81 |
13.50 | 76 | 76 | 76 | 76 | 76 | 77 | 79 | 360 | 148 | 81 |
13.75 | 76 | 76 | 76 | 76 | 76 | 77 | 79 | 365 | 150 | 81 |
14.00 | 76 | 76 | 76 | 76 | 76 | 77 | 79 | 369 | 152 | 81 |
14.25 | 76 | 76 | 76 | 76 | 76 | 77 | 80 | 374 | 154 | 81 |
14.50 | 76 | 76 | 76 | 76 | 76 | 77 | 80 | 379 | 156 | 82 |
14.75 | 76 | 76 | 76 | 76 | 76 | 77 | 80 | 384 | 158 | 82 |
15.00 | 76 | 76 | 76 | 76 | 76 | 77 | 80 | 389 | 159 | 82 |
15.25 | 76 | 76 | 76 | 76 | 76 | 77 | 80 | 395 | 161 | 82 |
15.50 | 76 | 76 | 76 | 76 | 76 | 77 | 80 | 401 | 164 | 83 |
15.75 | 76 | 76 | 76 | 76 | 76 | 77 | 80 | 407 | 167 | 83 |
16.00 | 76 | 76 | 76 | 76 | 76 | 77 | 80 | 413 | 168 | 83 |
16.25 | 76 | 76 | 76 | 76 | 76 | 77 | 81 | 420 | 171 | 83 |
16.50 | 76 | 76 | 76 | 76 | 76 | 77 | 81 | 427 | 172 | 84 |
16.75 | 76 | 76 | 76 | 76 | 76 | 77 | 81 | 432 | 174 | 84 |
17.00 | 76 | 76 | 76 | 76 | 76 | 77 | 81 | 438 | 177 | 84 |
17.25 | 76 | 76 | 76 | 76 | 76 | 77 | 81 | 443 | 179 | 84 |
17.50 | 76 | 76 | 76 | 76 | 76 | 77 | 82 | 448 | 180 | 84 |
17.75 | 76 | 76 | 76 | 76 | 76 | 77 | 82 | 453 | 181 | 84 |
18.00 | 76 | 76 | 76 | 76 | 76 | 77 | 82 | 458 | 185 | 85 |
18.25 | 76 | 76 | 76 | 76 | 76 | 77 | 82 | 463 | 187 | 85 |
18.50 | 76 | 76 | 76 | 76 | 76 | 77 | 82 | 467 | 189 | 85 |
18.75 | 76 | 76 | 76 | 76 | 76 | 77 | 83 | 473 | 191 | 86 |
19.00 | 76 | 76 | 76 | 76 | 76 | 77 | 83 | 477 | 194 | 86 |
19.25 | 76 | 76 | 76 | 76 | 76 | 77 | 83 | 481 | 196 | 87 |
19.50 | 76 | 76 | 76 | 76 | 76 | 77 | 83 | 484 | 197 | 87 |
19.75 | 76 | 76 | 76 | 76 | 76 | 77 | 76 | 488 | 200 | 88 |
20.00 | 86 | 83 | 87 | 87 | 82 | 78 | 84 | 493 | 203 | 89 |
At the end of the test, the panel was still carrying load and generally structurally sound, although the resin on the bottom had burned off, exposing glass fiber. The following photos illustrate the condition of the specimen afterwards.
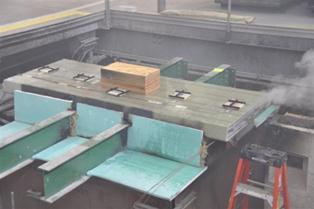
Figure 97. Photo. The test panel just after the test stopped. Note that the top surface kept cooler and ended up with little deterioration.
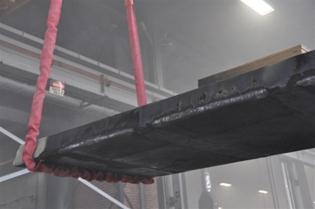
Figure 98. Photo. Specimen immediately after the test. Note the extent of damage on the bottom.
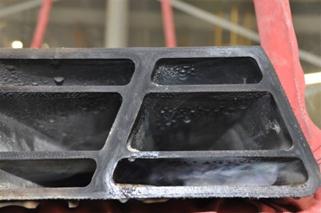
Figure 99. Photo. Close-up of the open end of the panel after the test.
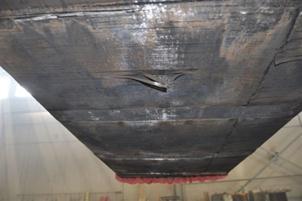
Figure 100. Photo. The glass fiber on the bottom has frayed due to burn-off of the resin matrix.
Results
The deck panel survived 1,600-degree Fahrenheit temperatures relatively well. The top surface did not rise much higher than room temperature (~80 degrees Fahrenheit). Although the bottom surface suffered extensive damage, the multi-celled structure protected the upper part and reduced the spread of flame and high temperatures. The panel carried the full 1,600 lb. superimposed load with a maximum deflection of 5/16 inches. There was no crushing of the tubes observed, no excessive bending, and the panel was still functional at the end of the test.