Composite Bridge Decking: Phase I Design Report
APPENDIX D: GROUT SELECTION REPORT
Overview
The design solution selected for the replacement deck in this project utilizes an FRP profile with three cavities (see figure 14). These profiles will be bonded together to form a large deck unit. To improve the stiffness of the deck panel and to increase resistance to localized loading, the upper and lower cavities may be filled with an appropriate grout material. This grout may be used in either the upper or lower cavity or both. Development testing on the original design concept showed a significant increase in deck performance could be gained through use of the grout.
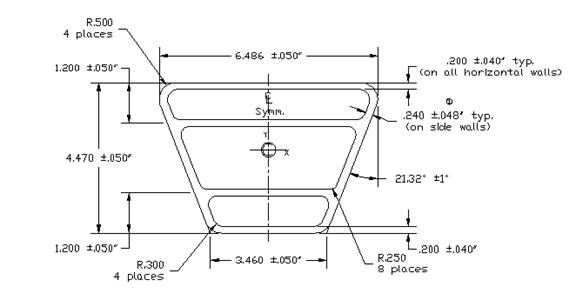
Figure 14. Diagram. Pultruded FRP combination tube
This appendix outlines work done to identify and select several grout products which may be suitable for use in the current design. Testing is performed to validate key selection parameters and a final recommendation is made for the current project.
Key Issues for the Grout
In assessing potential grout products for the application, the following issues were identified as important evaluation criteria:
- Compression strength.
- Workability.
- Cure shrinkage.
- Cure time.
- Adhesion to FRP substrate.
- Density.
- Cost.
- Industry acceptance.
Selection of Test Materials
The strategy adopted for selecting an appropriate grout for this structure was to identify several potential grout options based on published data and technical documentation.
There are two basic classes of grout which may be used for this design:
- Cementitious grout
- Polymer grout
Both classes were considered in this investigation.
The initial approach in identifying potential materials was to examine the approved material lists of several state DOTs for possible materials. Product manufacturers were then contacted to discuss the suitability of their product. Additional product recommendations from the project team and associated contacts were also considered. From these investigations the following products were identified as being potentially suitable for the current design:
- Target 1121 Cable Duct Grout, Non-shrink cement, Target Products Ltd.
- Target 1118 Unsanded Silica Fume Grout, Non-shrink cement, Target Products Ltd.
- Sikagrout 300 PT, Non-shrink cement, Sika Corporation
- Pro-Poxy 2000, Epoxy, DSC Unitex
- Pro-Poxy 2500, Epoxy, DSC Unitex
- Ipanol E-Grout, Epoxy, IPA Systems, Inc.
- Ipanol E-Flex RM, Epoxy, IPA Systems, Inc.
Summary of Published Performance Data
Table 18 provides performance information on the selected products, obtained from manufacturer data sheets.
Product | Type | Set Time, hrs | Shrinkage (28 days), % | Compression Strength (ksi) | |||
---|---|---|---|---|---|---|---|
1 day | 3 day | 7 day | 28 day | ||||
Target 1121 | Cement | 3 to 12 | <0.2 | 2.56 | 4.43 | 8.10 | 12.20 |
Target 1118 | Cement | 8 | exp: 1.5-2.5 | 2.90 | 5.08 | 7.25 | 8.70 |
Sikagrout 300PT | Cement | 3 to 12 | <0.2 exp: <2.0 |
3.00 | 5.00 | 7.00 | 8.00 |
Pro-Poxy 2000 | Epoxy | 0.3 to 4 | 0.005 | – | – | – | 14.50 |
Pro-Poxy 2500 | Epoxy | 0.5 | – | – | – | – | |
E-Grout | Epoxy | 1.5 | 0.005 | 11.00 | 15.00 | 15.00 | 15.00 |
E-Flex RM | Epoxy | 4 | 6.80 |
One of the difficulties in comparing manufacturer data for the cement grouts versus the epoxy grouts is that manufacturer testing is generally different for the two different types of material. Thus, the published data do not provide a straight comparison.
Testing Program
In addition to examination of the manufacturer data, physical testing was conducted to obtain additional performance data required for finite element analysis modeling and to confirm published figures. The following tests were conducted:
- ASTM C109 / C109M - 11b Standard Test Method for Compressive Strength of Hydraulic Cement Mortars (Using 2-in. or [50-mm] Cube Specimens).
- ASTM C78 / C78M - 10 Standard Test Method for Flexural Strength of Concrete (Using Simple Beam with Third-Point Loading).
- ASTM C39 / C39M - 12 Standard Test Method for Compressive Strength of Cylindrical Concrete Specimens.
Compression modulus values were obtained using C39 with 3-inch by 6-inch cylinders.
Testing was conducted at 1, 3, 7, and 14 days for compression strength. Compression modulus and modulus of rupture (flexure) were determined at 14 days. Fourteen-day testing was used instead of the standard 28 days because this particular application requires materials with rapid strength development. Full strength development within 7 days is seen as preferable for this application.
Test Results
Table 19 summarizes the results obtained through physical testing.
Product | Compression Strength (psi) | Modulus of Rupture (psi) | Compression Modulus (ksi) | |||
---|---|---|---|---|---|---|
1 day | 3 day | 7 day | 14 day | 14 day | 14 day | |
Target 1121 | 818 | 3154 | 6440 | 7448 | 834 | 952 |
Target 1118 | – | 6551 | 8221 | 8328 | 1218 | 983 |
Sikagrout 300PT | 2275 | 6904 | 7644 | 8581 | – | – |
Pro-Poxy 2000 | 9500 | 8092 | – | 11475 | 2099 | – |
Pro-Poxy 2500 | – | – | – | – | 2040 | 743 |
Ipanol E-Grout | 9293 | 14994 | 15206 | 15577 | 1900 | – |
Ipanol E-Flex RM | 5979 | 7596 | 7751 | 6849 | 3773 | – |
Observations on Physical Testing
One of the key challenges of this particular application scenario is the need to flow the grout through a narrow (~1 inch) cavity over a distance of up to 24 feet. This requires a material with good flow characteristics. All of the cement grouts demonstrate highly fluid behavior once properly mixed. While they are initially paste-like, there is a point in the mixing process when the material changes to a highly fluid behavior. It is anticipated that in this state the cement grouts could be pumped or flowed into the cavity.
The Pro-Poxy 2000 and Ipanol E-Grout are more viscous than the cement grouts but still exhibit enough flow where it is thought they could be successfully used in this application. It may be necessary to decrease the aggregate content of the E-Grout below the standard mix level to retain sufficient flow.
The Pro-Poxy 2500 is a mortar material rather than a grout and does not exhibit the flow characteristics required for this application. Therefore, it would not be suitable.
The resin component of the Ipanol E-Flex RM is considerably more viscous than the Ipanol E-Grout resin. This results in a mix with reduced flow characteristics. While not as paste-like as the Pro-Poxy 2500, the E-Flex RM may present challenges in filling the pultrusion cavity. Further testing would need to be conducted on a full-length tube specimen to properly assess the suitability of this material.
Working time is a significant issue in grout selection, as sufficient time must be available to mix and place the material before cure occurs. This is not typically a problem with the cement grouts due to their much longer cure times. For the epoxy grouts, this is more problematic. Once the resin has gelled, further working of the material is not possible. The Pro-Poxy 2000 and Ipanol E-Grout both display longer working times compared with the Pro-Poxy 2500 and Ipanol E-Flex systems. For all systems it will be necessary to carefully stage the mixing of the grout, and multiple batches will be required to ensure the material going into a particular tube is as fresh as possible. It is thought that the working time of the Pro-Poxy 2000 and Ipanol E-Grout should be sufficient for the application at hand. TheE-Flex system appears to be a much faster gelling products and the short gel time available with typical batch sizes may cause problems with filling the tube.
As can be seen from the test data, the epoxy products have a significant performance advantage over the cement products both in terms of final strength and rapid development of that strength. It can be seen that the epoxy products develop around 80 percent of their ultimate strength within 24 hours. This is a significant advantage in achieving the rapid production times envisaged for the bridge deck.
In terms of ultimate compression strength, the Pro-Poxy 2000 and Ipanol E-Grout display significantly higher strength than the cement grout options, with the Ipanol E-Grout exceeding 15 ksi. As expected, the modulus of rupture for the epoxy options is approximately twice that of the cement grouts.
While deflection under load was not measured, it was observed from the tests that the epoxy products deform significantly more than the cement grouts under failure load. The failure of the epoxy is also more progressive, rather than a sudden fracture. It is thought that this may make the epoxy products less susceptible to cracking in service, thereby preserving the integrity of the grouting in the tubes.
Conclusion
Table 20 shows an indication of the relative merits of the grouts, using a letter grade.
Grout | Adhesion | Density | Cost | Industry Acceptance |
---|---|---|---|---|
ProPoxy 2000 | A | A | C | B |
Ipanol E-Grout | A | A | C | B |
Ipanol E-Flex | A | A | C | B |
Target 1121 | C | B | B | A |
Target 1118 | C | B | B | A |
Sika 300PT | C | B | B | A |
Based on the investigations undertaken and the testing performed, the project team elected to use Ipanol E-Grout for grouting the FRP tubes in the deck. The E-Grout provided high strength performance at a reasonable cost. It appears to offer the required handling characteristics and working time for filling the tubes. It develops strength rapidly allowing the manufacture of the deck to proceed after only 1 day of grout curing. Further testing of performance in full-size grouted tubes confirmed the suitability of this selection. This brand epoxy grout was chosen over others primarily because of availability.