Publications
UNPAVED ROAD DUST MANAGEMENT
A Successful Practitioner's Handbook
Previous Chapter « Table of Contents » Next Chapter
CHAPTER 5 - SELECTING A CHEMICAL TREATMENT
INTRODUCTION
There are more than 150 proprietary unpaved road additives on the market in the United States, ranging from general purpose dust palliatives that work well under a range of conditions to soil- specific stabilizers that have been developed to improve the properties of certain high clay content soils. There is also a growing tendency to combine two or more additives into a single product to enhance performance. Most additives can be categorized, based on chemistry, to aid selection for a specific additive. To properly select an additive for a roadway, the material properties, geometry, traffic levels, and climate must be known.
THE PROBLEM
The variety of choices of unpaved road chemical treatments available to the road manager is overwhelming given the extremely wide range of proprietary products available, the lack of specifications, and the lack of published scientific research comparing the various additive categories and additives within categories. Consequently, road managers invariably have to rely on the limited experience of others or the recommendations of additive suppliers and vendors who often provide conflicting information. Secondly, road managers usually only do limited testing of road materials and consequently choices of chemical treatment are often not compatible with the materials in the wearing course, leading to poor performance. In these instances, the chemical treatments are usually incorrectly blamed for the poor performance, whereas the lack of knowledge/information leading to inappropriate choices is usually the culprit.
LEARNING POINTS FROM THE SCAN TOUR
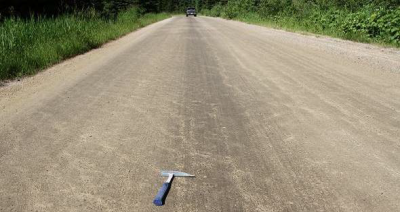
Figure 28. Photo. Magnesium chloride road.
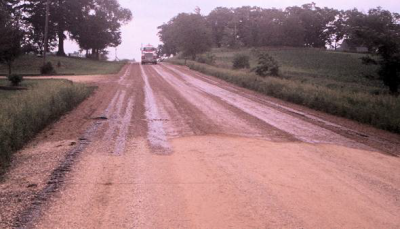
Figure 29. Photo. Lignosulfonate road.
Road manager experience in selecting chemical treatments varied considerably across the locations visited. Magnesium chloride was the treatment of choice in many areas (Figure 28), this being attributed to a proven track record and cost- effectiveness, ready availability, and ease of application. There were, however, growing concerns about potential long-term environmental impacts associated with annual applications. In some locations, road managers had again researched the topic and considered alternatives such as lignosulfonate (Figure 29), typically following the US Forest Service Dust Palliative Selection and Application Guide and experience and/or recommendations from other experienced managers in neighboring jurisdictions.
Cooperation also existed between some road managers and suppliers to "engineer" additives to
better resolve the needs of a particular road condition. Most scan tour hosts were unaware of the full performance capabilities of available additives or how to select an appropriate additive with confidence for a particular situation.
Most road managers were concerned about the lack of specifications for unpaved road chemical additives, dealing with the proprietary nature of many treatments, and how to incorporate chemical treatment requirements into their documents and specifications. One vendor noted that they were occasionally asked by road managers to help write bid specifications to suit their specific additive!
RECOMMENDED APPROACH
The performance of unpaved road chemical treatments is primarily influenced by how well the treatment is matched to the material properties of the wearing course materials. Traffic volume and type, road geometry and climate are of lesser importance, but will still influence the choice and need to be considered before any final decision is made. The approach recommended in this handbook advocates first understanding the materials, which requires inexpensive testing and simple interpretation of the test results, and then selecting an additive category considering the material properties, traffic, geometry, and climate.
Know Your Materials
It is important to note that aggregate gradation specifications for the riding surface of unsurfaced roadways are not the same as those for hot mix asphalt, portland cement concrete pavement, or even thouse of the base course.
Users of unpaved roads are fundamentally unhappy with dust and poor ride in dry conditions, and slippery, impassable roads in wet conditions. Meanwhile, practitioners are mainly focused on minimizing costs while providing a safe and acceptable level of service. All of these issues are a function of material properties and the way the road is constructed and maintained.
A finished road is only as good as the materials that form the riding surface. Most unpaved roads in the United States have some form of imported aggregate base and wearing course. Much of this aggregate comes from commercial sources that also supply contractors and various departments of transportation. Consequently, the aggregate supplied for unpaved roads will usually meet the specifications of the supplier's greatest need; typically asphalt concrete, portland cement concrete, or aggregate base for paved roads (Figure 30). Many practitioners mistakenly believe that if materials meet the specifications for aggregate base in a paved highway, it will also work well as an unpaved road wearing course. This is an incorrect assumption! Aggregate base used in paved roads is confined by the chip seal, asphalt or concrete on the surface and gradings are optimized for strength alone as it is not directly exposed to traffic abrasion or the weather. A different set of material specifications is needed for unpaved road wearing courses to compensate for the lack of surface containment.
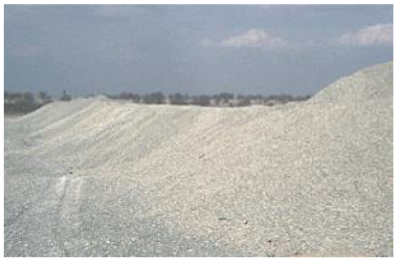
Figure 30. Photo. Aggregate for asphalt concrete.
Key material properties influencing unpaved road performance include the grading or particle size distribution, the fines content, the clay content, and the material shear strength. These are determined from basic material indicator tests including a grading analysis (for example, AASHTO T 27 or ASTM C136), a plasticity test (Atterberg Limits [AASHTO T 89 and T 90 or ASTM D4318] or bar linear shrinkage [Caltrans CT 228 or Texas Tex- 107-E]), and a strength test (for example, California Bearing Ratio [CBR, AASHTO T 193 or ASTM D1883]), all of which are simple to do and cost very little (Figure 31). In fact, the costs are negligible in terms of the costs of gravel replacement and selecting the correct chemical treatment and are recovered many times over in the extended life of the road and reduced maintenance requirements. The small savings enjoyed up front by skipping material testing will invariably mean higher costs later on because of early replacement of gravel and the need for more frequent maintenance. Most specifications are based on these or similar tests and typically provide an envelope of parameters for each, which the aggregate supplier or practitioner needs to meet.
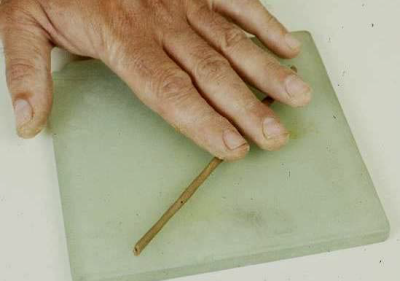
Figure 31. Photo. Plasticity test.
Understand How Material Properties Influence Performance
There are a range of recommendations, guidelines, and specifications for unpaved road base and wearing course materials. Most need to be adapted to suit local conditions and material availability. Many chemical treatments can be used to overcome limitations in material properties. However, many road managers have difficulty in interpreting test results, especially with regard to understanding performance if a grading envelope and a single plasticity criterion cannot be met by an aggregate supplier or in gravel located on the road owner's property. The following simple three-step procedure, based on research in southern Africa (Technical Recommendations for Highways, No.20) and adapted for international use, can be used to interpret key test results, assess the applicability of local material specifications, and understand how unpaved roads will perform if a particular material is used. It can also be used to make a decision regarding material choice, road design specifications, and chemical treatment selection. This procedure is a guide only and NOT a new specification, nor is it intended that it replace existing specifications. It may need to be refined for particular situations and calibrated for local conditions.
Step 1 - Test Result Analysis
- Grading Analysis
In this recommended approach, only four key sieve sizes are required for the grading analysis. These are the 1.0 in., #4, #8, and the #40 (25 mm, 4.75 mm, 2.36 mm, and
0.425 mm) sieves. The first three are used to check for the correct mix of coarse, intermediate, and fine particles using the following simple formula known as the grading coefficient (Gc):
Gc = ((P1.0 in. - P#8) x P#4) / 100 or
Gc = ((P25 mm - P2.36 mm) x P4.75 mm) / 100
Where P is percent passing
Although the grading coefficient is determined using material passing the 1.0 in. (25 mm) sieve, a maximum size of 1½ in. to 1¾ in. (40 mm to 45 mm) is preferable to provide adequate all-weather passability. The use of aggregates larger than this will reduce ride quality, make it noisy to travel on, and cause problems for the maintenance grader operator.
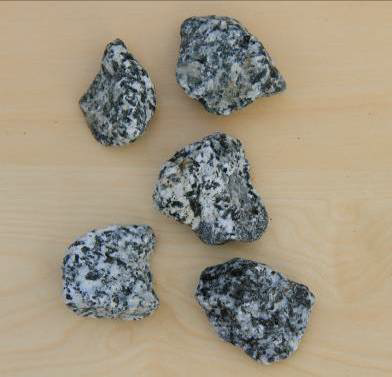
Figure 32. Photo. Cubicle aggregate.
The percentage material passing the #200 (0.075 mm or 75 µm) sieve is also a useful indicator of how an unpaved road will perform and can influence the decision of what treatment to use. High percentages of material (that is, >20%) passing this sieve imply that the road will be dusty when dry and may become slippery when wet. Low percentages (that is, <10%), imply that the road will washboard and require regular grader maintenance. Many unpaved road wearing course specifications based on paved road base course specifications limit this fines content to about 5 percent in the mistaken belief that this will reduce dust. Determination of the percent passing the #200 sieve (usually done using a wet process as part of a standard grading analysis) is, however, not as simple as determining the percent passing the #8 sieve (which can be done dry if necessary when checking aggregates in the field). Consequently for understanding general performance, the #200 material is factored into the grading coefficient
equation as part of the #8 sieve material. However, the percent passing the #200 sieve is required for optimal chemical treatment selection.
The angularity of the aggregate should also be checked during the sieve analysis. Cubicle material (Figure 32) has better interlock than rounded material (e.g., uncrushed alluvial aggregates) and consequently rounded aggregate (Figure 33) should be crushed to obtain at least two fracture faces to enhance interlock and prevent raveling.
- Clay Content
The percent passing the #40 sieve is used together with the bar linear shrinkage (BLS), or plasticity index (determined from the Atterberg Limit tests if the BLS test cannot be undertaken), to optimize the clay content using the following simple formula known as the shrinkage product (Sp):
Sp = BLS x P#40 if the bar linear shrinkage is used, or Sp = (PI x 0.5) x P#40 if plasticity index is used
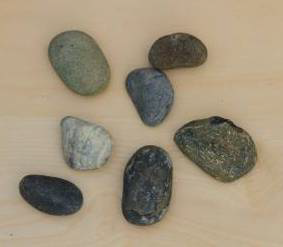
Figure 33. Photo. Rounded aggregate.
(Note that using the bar linear shrinkage (Figure 34) to determine the shrinkage product is more accurate than using the plasticity index, especially for silty non- plastic or slightly plastic materials. These materials often have a plasticity index of zero, and consequently also a shrinkage product of zero if the above formula is used. However, they will usually have some shrinkage [that is, BLS > 0], thereby providing a number to work with to better estimate expected performance).
- Bearing Capacity
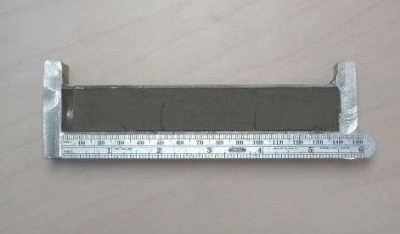
Figure 34. Photo. Bar linear shrinkage test.
The California Bearing Ratio (CBR) performed on material in the laboratory is the most commonly used bearing capacity test. No formulas are required to interpret the results from this test.
Step 2 - Test Result Interpretation
Optimal unpaved road performance will usually be achieved when the wearing course materials meet the following:
- The grading coefficient is between 15 and 35. Although not directly measured in the grading coefficient formula, a fines content (material passing the #200 sieve) of between 12 and 15 percent is typically required to meet the grading coefficient requirements.
- The shrinkage product is between 100 and 365 (or between 100 and 250 if dust is a major concern and no dust control treatment is planned). Many unpaved road specifications based on paved road base course specifications limit or even exclude any clay content in the mistaken belief that this will also reduce dust.
- Assuming that the road has a quality base course with adequate CBR, the soaked CBR of the wearing course should be above a minimum of 15. If the traffic is predominantly trucks and the road is in a high rainfall area or storms of high intensity are common, a higher CBR may be desirable if passability problems are an issue. However, higher CBR materials tend to have low clay contents and consequently washboarding may be a problem. Therefore, a balance between CBR and shrinkage product needs to be determined for optimal performance for specific traffic type and volume.
When these optimal grading coefficient and shrinkage product limits are met, good performance is achieved as shown below in a simple performance prediction chart in Figure 35. The chart also demonstrates the likely consequences of not meeting the criteria.
The factors that contribute to each of these predicted material performances are discussed below.
- Erodible materials are typically fine grained and have some plasticity. They generally perform well when used in roads on flat terrain or in areas of very low rainfall. In other areas they will quickly erode during rainfall, leaving channels in the road that are dangerous and unpleasant to drive over and expensive to maintain. Examples of roads built with materials falling in this area of the chart are shown in Figure 36 and Figure 37. The eroded material usually ends up where it is not wanted (for example, blocking drains or flowing into streams or onto adjacent land).
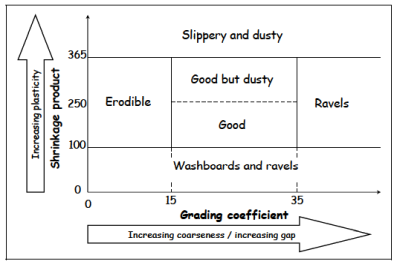
View larger version of Figure 35
Figure 35. Chart. Material performance predictor chart (adapted from Paige-Green 1989).
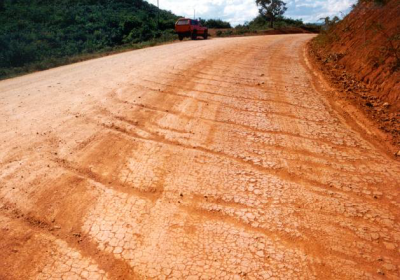
Figure 36. Photo. Transverse erosion.

Figure 37. Photo. Longitudinal erosion.
- Materials that washboard (corrugate) and ravel are usually poorly graded or gap-graded (absence or insufficient quantities of certain sizes leading to poor aggregate interlock) and lack fines and plasticity. Consequently the particles do not bind together, leading to washboarding, raveling and, ultimately, gravel loss, and thus a poor and unsafe ride on a surface requiring regular maintenance. These materials are also prone to erosion during rainfall. Examples of roads built with materials falling in this area of the chart are shown in Figure 38 and Figure 39.
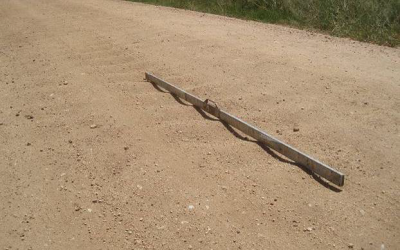
Figure 38. Photo. Washboarding (corrugation).
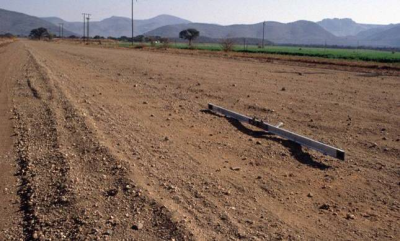
Figure 39. Photo. Washboarding and raveling.
- Materials that ravel have some plasticity, but are gap-graded. The presence of clay usually limits washboarding but does not prevent raveling. Examples of roads built with materials falling in this area of the chart are shown in Figure 40. Windshield damage is a major problem on these roads.
- Materials that are slippery when wet and very dusty when dry typically have high fines and clay contents. Examples of roads built with materials falling in this area of the chart are shown in Figure 41 and Figure 42. Increasing clay content also results in decreasing CBR, leading to poor passability in addition to the slipperiness Figure 43).
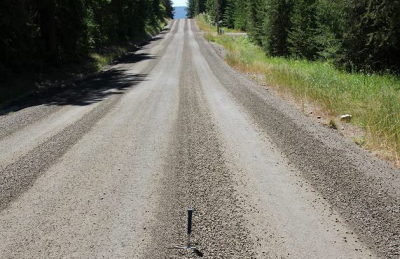
Figure 40. Photo. Raveling.
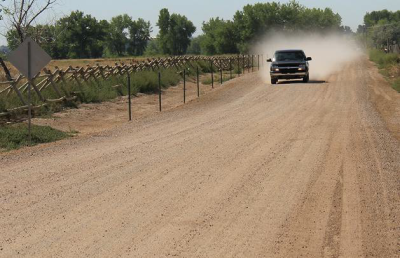
Figure 41. Photo. Dusty when dry.
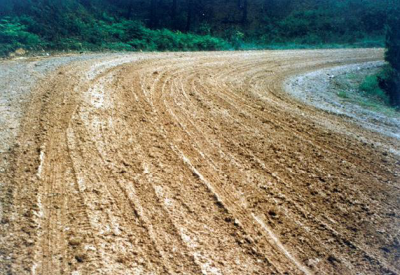
Figure 42. Photo. Slippery when wet.
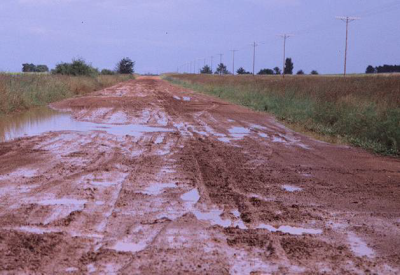
Figure 43. Photo. Impassable.
- Well-graded materials with moderate clay contents will perform well, but may be dusty during dry conditions. Examples of roads built with materials falling in this area of the chart are shown in Figure 44.
- Finally, well-graded materials with some clay will perform well with a minimum of maintenance. Examples of roads built with materials falling in this area of the chart are shown in Figure 45.
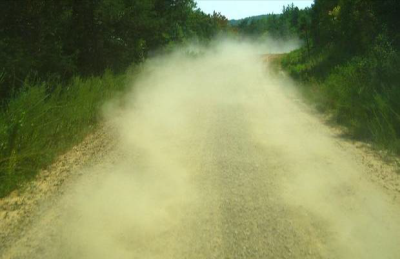
Figure 44. Photo. Good but dusty.
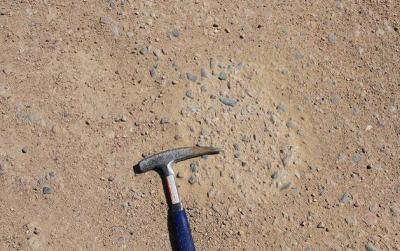
Figure 45. Photo. Good material.
Step 3 - Material Selection Decision
If materials falling within the good performing area on the chart are readily available, the decision is easy. Use these materials to construct a good road! If they are not readily available the practitioner needs to decide on an appropriate course of action as follows:
- Weigh the consequences with the probability of occurrence:
- Erodible materials can be used in flat areas and areas with low rainfall or low intensity rainfall events.
- Materials that washboard or ravel can be used on roads with low-traffic volumes traveling at low speeds. They can also be used if the practitioner is prepared to regularly blade or drag the road. The costs of this maintenance should be compared with importing better gravel from elsewhere. If the road is generally only used to access residences, the homeowners may be willing to tow a simple tire drag themselves to smooth washboarding and raveled areas.
- Materials that are slippery or impassable can be considered on low traffic volume roads in low rainfall areas if the road can be closed during problem events.
- Good but dusty materials can be used with appropriate speed restrictions or a suitable dust palliative.
- Use the material "as is," but adjust maintenance programs accordingly:
- Blade the road more frequently to remove erosion channels or washboarding and redistribute raveled material.
- Close the road during slippery or impassable conditions.
- Seek alternative aggregate suppliers who can provide the requested material.
- Blend two materials to meet the required grading coefficient and shrinkage product. This usually requires the addition of small amounts of clay if commercially obtained aggregate is used.
- Use a dust palliative or stabilizer to provide additional binding to the material, but remember that it is usually cheaper to use fines to fill voids (that is, meet the grading coefficient and shrinkage product requirements) than to use a chemical.
Selecting an Appropriate Chemical Treatment
Additive Types
Although there are more than 150 proprietary chemical treatments available on the market through as many additive suppliers, vendors, and distributors, most can be categorized into one of seven main categories (See Appendix E for a detailed summary of the categories). There is, however, a growing trend to blend additives from two or more categories to optimize performance for specific road conditions. The seven categories are:
- Water Absorbing. These treatments function by absorbing small quantities of water from the atmosphere, which agglomerates the fines and holds the aggregate matrix together through suction forces. The most common products in this category are magnesium chloride (Figure 46) and calcium chloride (Figure 47), both of which are commonly used for dust control in the United States. There is a considerable published record on the use of these additives and a significant history of application. Marginal increases in strength are possible, mostly due to improved compaction. They are water soluble and do not provide sufficient strength improvement to warrant consideration as soil stabilizers. Roads treated with these additives can be maintained with conventional unpaved road techniques (that is, grader blading after light rain or water application).
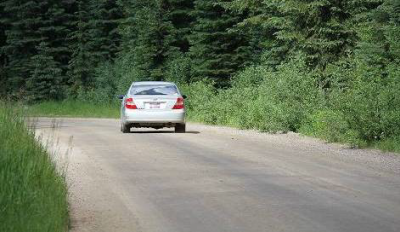
Figure 46. Photo. Magnesium chloride.
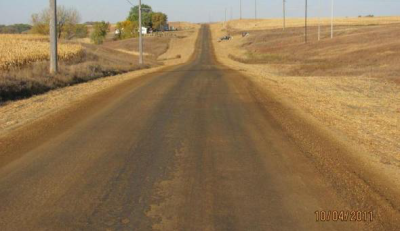
Figure 47. Photo. Calcium chloride.
- Organic Non-Petroleum or Natural Polymers. These treatments act as "glue" that agglomerates the fines and coarser particles together. This category includes lignosulfonates (Figure 48), tree resins, tree oils, vegetable oils and molasses-based products. They are by-products from plant- based industries including sulfite processes commonly used in pulp and paper industries, vegetable oil and tannin extraction, ethanol production, and sugar refining. Their composition is variable and depends on the plant matter and chemicals used during processing. Most are water soluble. They are effective dust palliatives but do not provide sufficient strength improvement for consideration as soil stabilizers. Treated roads can be maintained with conventional unpaved road techniques.
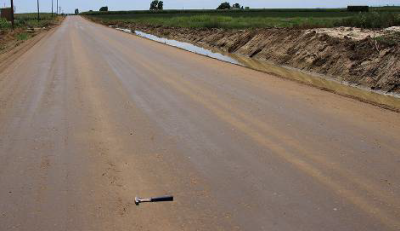
Figure 48. Photo. Lignosulfonate.
- Organic Petroleum and Petroleum Resins. Organic petroleum treatments are typically diluted asphalt emulsions that provide both strength improvement and dust control through a cementing action. They do not leach out during rainfall, but are difficult to maintain with conventional unpaved road maintenance equipment if a hard crust forms. Petroleum resins (Figure 49) are usually a blend of natural polymers and petroleum- based additives. They have a similar binding action to natural polymers but are more resistant to leaching by water. They are effective dust palliatives, but usually do not provide sufficient strength improvement for consideration as soil stabilizers when applied at economical application rates. They are difficult to maintain with conventional unpaved road maintenance equipment if a hard crust forms. Mineral oils and base oils are effective for dust suppression, but not for stabilization. They are not water soluble, but can be displaced from the soil particles by water. They usually do not form a crust and treated roads can be maintained with conventional unpaved road maintenance equipment.
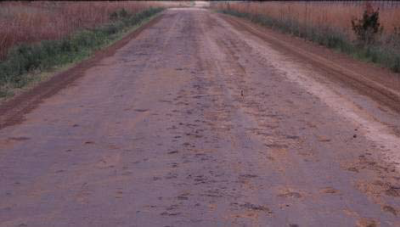
Figure 49. Photo. Petroleum resin.
- Synthetic Polymer Emulsions. Synthetic polymer emulsions (Figure 50), or polymer dispersions, are suspensions of synthetic polymers in which the monomers are polymerized in a dominantly aqueous medium. Once the aqueous medium has evaporated, the active ingredients glue the aggregate particles to each other. Numerous formulations have been developed for various soil-conditioning applications.
Depending on the formulation and
application rate, they are effective in both dust control and strength improvement (stabilization) applications. Roads treated with these additives are usually difficult to maintain using conventional unpaved road techniques because of damage to the skin/crust that forms on the surface.
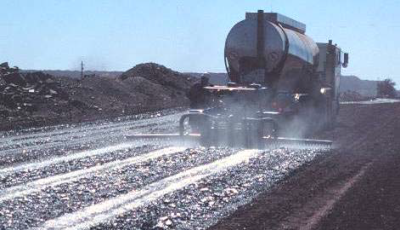
Figure 50. Photo. Synthetic polymer.
- Synthetic Fluids. These treatments include synthetic base fluids and unique formulations of synthetic iso-alkanes (Figure 51). They are
effective dust palliatives, but do not generally provide sufficient strength improvement for consideration as soil stabilizers. They can be modified with other binders if strength improvement is required. Roads treated with synthetic fluids can be maintained with conventional unpaved road techniques. Maintainability of roads treated with synthetic fluid blends will depend on the formulation and application rate and method.
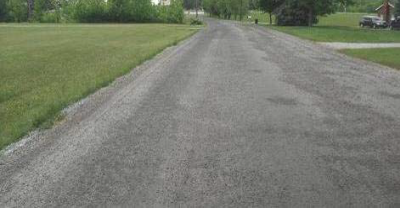
Figure 51. Photo. Synthetic fluid.
- Electrochemical/Sulfonated Oils. Electrochemical additives (Figure 52), sulfonated oils (Figure 53), sulfonated petroleum products (SPPs) or ionic stabilizers rely on ionic exchange reactions to perform their expected functions satisfactorily. Their "active ingredients" are mostly hydrocarbon mineral
oils modified with sulfuric acid to form a sulfonic acid. Sulfonated oils are all "surface active agents" (surfactants) and have the ability to fix, displace, or replace exchange cations in clays and to make the soil materials (particularly clay minerals but not necessarily only clays) hydrophobic by displacing adsorbed water and water of hydration, and preventing re-adsorption of this water. They are highly susceptible to ion exchange reactions in which appropriate inorganic ions present on mineral surfaces (particularly clays) and in clay interlayers are replaced by, or attached to, the organic molecules. This reduces the mobility of the ions and functionally reduces the plasticity of the material. Once an ion exchange reaction has occurred and the sulfonic acid is attached to a mineral particle, the so-called hydrophobic tails of the sulfonated oils are directed away from the particle and form an oily protective layer around it. In theory, this has the effect of reducing the thickness of the electrical double layer and of preventing water from gaining access to the clay mineral particle. With this reduced double layer thickness, it now becomes theoretically possible to achieve a greater degree of compaction in the material and also to reduce the possible water absorption of the material in the long term. They can be maintained with conventional unpaved road techniques.
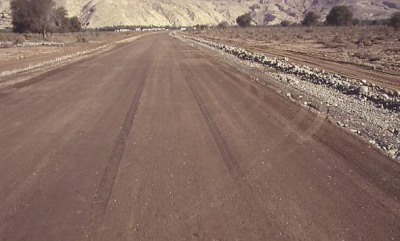
Figure 52. Photo. Electrochemical additive.
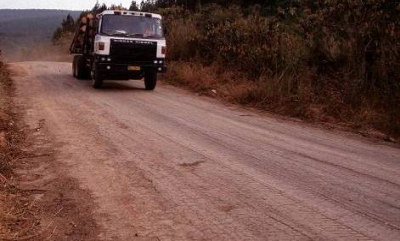
Figure 53. Photo. Sulfonated oil.
- Enzymes. As with sulfonated oils, enzymes (Figure 54) are proprietary products, the formulations of which are not made public.
Little useful documentation on the exact process of stabilization is available, although some form of microbial activity to neutralize the activity of clay is a central theme of some product brochures. Material requirements (in terms of clay content and plasticity), application rates, and method and performance claims are similar to those advocated by the suppliers of electrochemical/sulfonated oils. Enzyme-treated roads can be maintained with conventional unpaved road techniques.
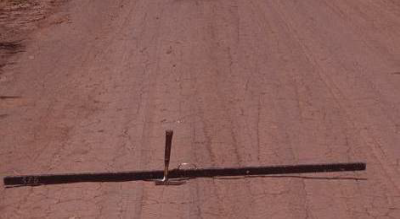
Figure 54. Photo. Enzyme.
Additive Selection
After optimizing the aggregate material, a suitable chemical treatment can be considered to further prevent the loss of fines, reduce dust levels, improve all-weather passability, and extend intervals between maintenance. Dust palliatives and stabilizers are usually developed to address specific problems, and contrary to some undocumented claims, there is no one chemical treatment that addresses all unpaved road problems. The recommended procedure for selecting the most appropriate additive for a given situation is as follows:
- Using the chart in Table 3, select the additive category that will work best in terms of the specific traffic (numbers of cars and trucks per day), road geometry (presence of steep grades and/or sharp curves with super-elevation), climate (humidity levels and storm intensity), and soil chemistry. More than one category may be suitable.
- Refine the selection to subcategories using the chart in Table 4, or the expanded version of the chart provided in Appendix E, both of which are based on the US Forest Service Dust Palliative Selection and Application Guide method. Choosing one additive category over another will depend on specific conditions and cost will require some engineering judgment, experience, and advice from experienced users, suppliers and vendors. Simple abrasion (mechanical brush [Figure 55]) and erosion tests can be considered to assess effectiveness of different additives under
specific conditions, to compare additives, and to refine application rates.
- Check material compatibility based on test result interpretation discussed earlier in this chapter and using the expanded performance predictor charts in Figure 56. Guidance on how various additives perform in terms of the material grading coefficient and shrinkage product is provided below.
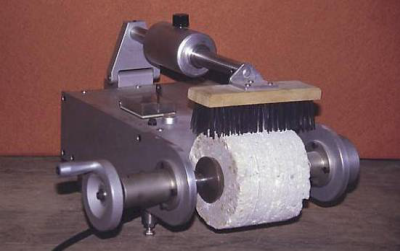
Figure 55. Photo. Abrasion resistance test.
Table 3. Category Selection Chart
Additive Category |
Traffic Limitations |
Road Geometry Limitations |
Climate Limitations |
Soil Chemistry Limitation s |
Cars |
Trucks |
Steep Grades |
Sharp Curves/ Super- elevation |
Humidity |
High Intensity Rain |
Water absorbing |
A |
B1,2 |
B3 |
B1,2 |
C |
B5 |
B6 |
Organic non- petroleum |
A |
B1,2 |
B4 |
C1,2 |
A |
C4 |
A |
Organic petroleum
Petroleum resins
Mineral oils |
A
A
A |
B1,2
B1,2 B1,2 |
A
A
A |
B1,2
B1,2
B1,2 |
A
A
A |
A
A
B4 |
B7 |
Synthetic polymer |
A |
B1,2 |
A |
B1,2 |
A |
A |
A |
Synthetic fluids |
A |
B1,2 |
A |
B1,2 |
A |
A |
A |
Electrochemical |
A |
B1,2 |
A |
B1,2 |
A |
A |
C8 |
Enzyme |
A |
B1,2 |
A |
B1,2 |
A |
A |
C8 |
A = No significant influence of performance B = Some influence on performance C = Significant influence on performance |
1 Empty trucks and trailers at high speed may break crust and accelerate washboarding and raveling
2 CBR must be increased with increasing number of trucks to ensure all-weather passability
3 May be slippery when wet
4 Likely to leach out or down into lower layers with heavy rainfall
5 May leach down into layer, but dry-back plus light rejuvenation will return it to surface
6 Can react with some elements if abundant in soil to form non-hygroscopic compounds (e.g., iron chloride in soils with very high iron content)
7 Choice of anionic or cationic emulsion may influence performance on certain soils
8 Requires specific clay minerals for satisfactory reaction |
Table 4. Chart for Refining Additive Selection
Additive Category |
Traffic |
Surface Material |
Climate During Traffic |
Vehicles per Day |
Plasticity Index/ Shrinkage Product |
Fines (% passing No.200 Sieve [75 µm]) |
|
Dust Palliative |
<100 |
100-
250 |
>2501 |
<5 |
5-15 |
>15 |
<5 |
5-10 |
10-20 |
20-30 |
>30 |
Wet |
Damp to Dry |
Dry2 |
<50 |
50-365 |
>365 |
Water absorbing |
Calcium Chloride |
A |
A |
B |
C |
A3 |
C3 |
C |
B |
A |
B3 |
C3 |
C3,4 |
A |
C |
Mag Chloride |
A |
A |
B |
C |
A |
B3 |
C |
B |
A |
B3 |
C3 |
C3,4 |
A |
B |
Organic petroleum/Mineral oils |
Asphalt emulsion |
B |
B5 |
B5 |
A |
B |
C |
B6 |
B |
B5 |
C |
C |
B |
A |
A |
Petroleum resin |
A |
B5 |
B5 |
A |
B |
C |
B5 |
B |
A |
C |
C |
B |
A |
A |
Mineral oil |
A |
B |
B |
B |
A |
C |
C |
B |
A |
B |
C |
B |
A |
A |
Organic non-petroleum |
Lignin |
A |
A |
B5 |
C |
A |
B3,5 |
C |
B |
A |
B3,5 |
B3,5 |
C4 |
A |
A |
Tall oil |
A |
B |
C5 |
A |
B |
C |
C |
B |
A5 |
B5 |
C |
B |
A |
A |
Vegetable oil |
A |
C |
C |
B |
A |
C |
C |
B |
A |
C |
C |
C |
A |
B |
Bio-Fluids |
A |
A |
B5 |
C |
B |
A |
C |
C |
A |
A |
C3 |
C3,4 |
A |
C |
Synthetic polymer emulsion |
Synthetic polymer5 |
A |
B5 |
C5 |
A |
A |
C |
C |
A |
A5 |
C |
C |
A |
A |
A |
Synthetic fluids |
Synthetic Fluid7 |
A |
A |
B5 |
B |
A |
B |
C |
A |
A |
A |
B |
B |
A |
A |
Electrochemical/Enzyme |
Electro-Chemical5,8 |
A |
A |
B |
C |
B |
A |
C |
C |
A |
A |
A |
B |
A |
A |
Enzyme5,8 |
A |
A |
B |
C |
B |
A |
C |
C |
A |
A |
A |
B |
A |
A |
Other (mechanical) |
Clay Additives5 |
A |
B |
C |
A |
B3 |
C |
A |
B |
B |
C |
C |
C3 |
A |
A |
Performance relative to unpaved road with no chemical treatment: A = Good B = Fair C = Poor |
1 Higher application rates/more frequent rejuvenation required for high truck traffic
3 May become slippery in wet weather if shrinkage product >250
5 Mix-in treatment usually required
7 EPA Definition |
2 >20 days with less than 40% relative humidity
4 May leach out in heavy rain
6 SS-1 or CSS-1 with only clean, open-graded aggregate
8 Requires reactive (usually expansive) clay minerals to react with |
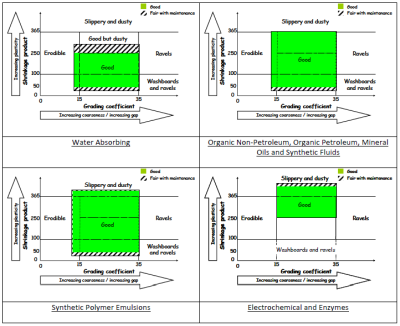
View larger version of Figure 56
Figure 56. Chart. Additive selection guide linked to material performance.
(Adapted from Jones, 1999)
- Erodible materials: The problem with erodible materials is usually grading and/or drainage related, and consequently it is difficult to overcome with a chemical treatment. Non-water- soluble polymer emulsions or bituminous-based products can be tried on gentle to moderate slopes in combination with drainage improvements. Water-soluble products (for example, chlorides and plant-based polymers such as lignosulfonate) will reduce dust, but will not prevent erosion. Neither will sulfonated oils/ionic stabilizers or enzymes, as the clay content is usually insufficient for a reaction that will bind the particles satisfactorily to prevent the shear action of flowing water.
- Materials that corrugate and ravel: These materials lack fines and plasticity. Chemical treatments are generally ineffective if the shrinkage product is less than 50 because uneconomically high application rates are required to fill the voids between the particles. Wind- and tire-shear forces usually also exceed the binding ability of the treatments used under these circumstances, leading to continued problems. If the shrinkage product is above 50, a variety of chemical treatments can be used to improve the materials by enhancing binding, leading to significant reductions in dust and washboarding. Chlorides, plant-based polymers, synthetic fluids, synthetic polymer emulsions, mineral oils, resins, and combinations of these products can all be considered. Sulfonated oils/ionic stabilizers and enzymes are generally unsuitable as there is insufficient clay to support a reaction.
Incorporating fines, often readily available from adjacent land owners or waste piles at quarries, can be considered to raise the shrinkage product to 50, before applying an appropriate chemical.
- Materials that ravel: Chemical treatments are generally ineffective on these materials because of the coarse or gap grading. They will keep the dust down initially, but won't prevent the raveling. Some success may be achieved at very high application rates (that is, using the chemical to fill the voids before a satisfactory bond is obtained). Alternatively, the addition of the gap material can be considered to adjust the grading coefficient before treatment. Dust levels will increase as the material gets displaced to the side of the road.
- Slippery or impassable materials: Additives used on these materials need to either chemically alter the clay minerals to reduce the plasticity or "waterproof" the clay particles to prevent them from expanding/shearing when wet. Synthetic polymer emulsions, mineral oils, resins, sulfonated oils/ionic stabilizers and enzymes can be considered. Atterberg Limits and soaked CBR tests should be carried out to check that a suitable reduction in plasticity and sufficient increase in shear strength is achieved with the selected product before it is applied on the road. Chlorides and other water soluble products should not be considered to treat these materials.
- Good and good but dusty materials: Chemical treatments can be effectively used on roads with these materials to minimize dust and limit fines loss, reduce the rate of gravel loss, and increase the intervals between grader maintenance. Chlorides, plant-based polymers, synthetic fluids, synthetic polymer emulsions, mineral oils, resins, and combinations of these products can all be considered. Clay contents are typically too low for sulfonated oils and enzymes to work effectively.
EVALUATING NEW PRODUCTS
New dust palliatives and unpaved road stabilizers are continuously being introduced to the market. Some of these are combinations of existing additives that have been engineered to meet specific project requirements or to counter undesirable properties of certain additives. Examples include mixing magnesium chloride with lignosulfonates to reduce the chloride content of applications or mixing petroleum products with lignosulfonates to reduce leaching. New products are also being developed to meet specific soil stabilization or environmental requirements. Examples include specific synthetic polymer emulsions, mineral oils, and synthetic fluids. New industrial processes can also lead to the production of by-products that may have an application in unpaved road maintenance. Examples include the growing ethanol production in certain states, which produces organic non-petroleum by-products. Finally, existing additives are often "repackaged" under a new name to elicit renewed interest, or to counter the effects of bad publicity from unsuccessful applications.
A cooperative but restrained relationship should be maintained with product vendors and their product track records should be evaluated independently (for example, by searching the Internet for reviews and experiences). Vendors should be quizzed on product attributes (both existing products and new ones) and asked to provide evidence of scientific research (laboratory tests and monitored field experiments [Figure 57]) to support their claims. Example questions to ask the vendor include, but are not limited to:
- About the product in general:
- Are construction specifications available? Are they generic, or targeted specifically to one vendor's product?
- Why has the product been developed and what makes it better than other currently available additives? Is it new, or is it a repackaged currently available additive? Is it a blend of currently available products, and if yes, which product, if any, dominates?
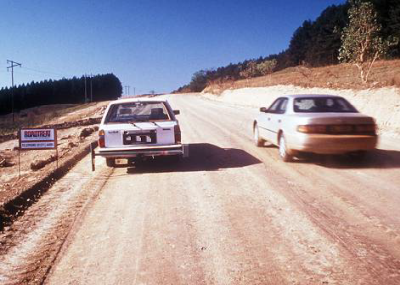
Figure 57. Photo. Additive experiment.
- How long has the product been available, how much has been sold and who uses it? How long have individual users been applying it? Phone other users to get an independent opinion about the product, performance limitations, and cost-effectiveness.
- What is the target use of the product? Is it aimed at improving all-weather passability (that is, strength improvement and aggregate binding) or simply as a surface treatment to bind surface fines together and reduce dust?
- Is a guideline document (not a glossy brochure) available to guide the user on how to make an informed decision about where to use the product, how to justify its use in terms of life-cycle cost, how to apply it, how to maintain it, and how to determine optimum rejuvenation intervals and rates?
- What technical support is provided to road owners and managers?
- About environmental compatibility/impact:
- What is the product composition and what are its properties? What generic category does it fit into? Check these in the MSDS and other technical guidelines that the supplier must provide.
- What is the product's impact on the environment? Has independent environmental testing been carried out? Are there any environments where the additive should not be used? Ask for a copy of the environmental testing report.
- What is the product's regulatory impact? Are there special storage, handling or reporting requirements if stored on site? Ask for any requirements needed to conform with the US EPA Spill Prevention, Control and Countermeasure Rule. Check that product distributors are aware of these requirements.
- About the economics:
- How will this product help save time, money and resources? More specifically, what is the initial cost per mile, predicted longevity, number of applications per year? What can be expected regarding road life-cycle maintenance and regravelling costs? Ask for back- up data from experiments, not just an opinion.
- About performance:
- Are warranties, performance guarantees, and/or "fit-for-service" certifications provided?
- How are performance and effectiveness measured? What defines a success or a failure? What remedies are provided for failures?
- Is the product expected to perform better than current products? For example, does it resist moisture, is it less slick, is it easier to maintain, does it give measurable improvement in strength (California Bearing Ratio), abrasion resistance, or rate of gravel loss? Does it have any limitations in terms of traffic, climate or soil chemistry? Again, ask for back-up data and check whether reasonable comparative testing has been carried out.
- What type of aggregate properties does it work best on? How does it match up in terms of the discussion above on materials and what simple tests can be done to get an idea of how well it will work? Where does the product fit on the performance predictor chart (discussed earlier in this chapter) and what impact will the product have on washboarding, raveling, rutting, gravel loss, erosion and slipperiness? Check field performance data to verify this and never trust anyone who says their product will prevent potholes (because that's a road/shape drainage issue that no chemical treatment can solve!).
- About application:
- How is the product applied for best performance? Should it be sprayed on as a topical application, or does it require to be mixed in? What are the implications of applying it as a spray-on treatment if a mix-in application is recommended?
- What can be expected when the road needs to be bladed? Is there residual performance after blading or is a full or partial reapplication necessary? Is it easy or difficult to rework? Does the road require watering before blading? Check the duration of field trial evaluations and whether maintenance procedures are documented.
- What changes in current practices are recommended for best performance with the new product?
- About the stage of development of the product:
- Is the product still considered to be experimental? If yes at what stage of the development cycle is it and when will it no longer be considered experimental?
- Is independent scientific testing focusing on quantifying performance in terms of reduced dust, reduced rate of gravel loss, improved passability, cost-benefit, etc?
- Are applications in the foreseeable future part of this research and if yes, is there a benefit to the road owner?
- If the test fails, will the vendor be willing to re-treat at no cost or provide an alternative product?
- Who else has tested/is testing the material? Can testimonials from other customers be provided? What volumes of the product have been used?
- Will there be vendor representation at the test application and will assistance be provided to monitor performance throughout the application life of the product?
Previous Chapter « Table of Contents » Next Chapter